Medieval Smokestacks: Fossil Fuels in Pre-industrial Times
Posted by Rembrandt on October 12, 2011 - 10:00am
This is a guest post by Kris De Decker. Kris is the editor of Low-tech Magazine, where this post first appeared.
The history of energy use in human civilisation is generally summarised as follows: from Antiquity until the start of the Industrial Revolution, people made use of the manual labour of both animals and humans, as well as biomass, sun, water and wind.
Next, all these renewable energy sources were replaced by fossil fuels: first coal, and later oil and gas. Uranium completed the picture in the second half of the twentieth century.
While this historical summary is basically correct, there were some - rather important - exceptions. Almost all of the Western European economies during the last millenium relied on a large-scale use of fossil fuels such as peat and coal.
Before we delve into the pre-industrial history of fossil fuels, it is important to note the difference between thermal energy (heat) and kinetic energy (motion). For the greater part of history, wind, water, and muscle power could provide only kinetic energy. This was the kind of energy required to grind grain, saw wood, or set sailboats in motion. For centuries, wood (and charcoal made of wood) was the only source of thermal energy in Europe, apart from the use of direct solar energy for low-temperature processes like the drying of mud bricks and food crops. Wood or charcoal were required for activities such as heating buildings, cooking food, producing building materials (such as bricks, tile, cement, lime and plaster), manufacturing glass and paper, forging iron or producing dyes and soaps. At the same time, wood was the main construction material for buildings, ships, bridges, mills, piers, wharves, cranes, winches, mine shafts, vehicles, barrels, furniture and tools.
The invention of the steam engine in the 18th century meant that thermal energy could be converted into kinetic energy: the heat generated by the burning of coal was used to power machines and vehicles. Likewise, the arrival of electricity in the 19th century allowed kinetic energy to be converted into thermal energy: a windmill, for instance, could be used to drive a generator that delivers energy to an electric oven, or heater. (Kinetic energy could produce heat by friction, for example in windmill gears, but this was mostly wasted).
These days, it is self-evident that both types of energy can be converted to one another (with considerable efficiency losses), but for most of human history kinetic energy and heat energy were entirely different and were treated separately. Then, just as now, thermal energy was much more important than kinetic energy.
Urban revival
The Romans - who fuelled practically all their mechanical activities with slave labour - deforested large parts of Europe in their hunger for thermal energy and construction materials. When their empire collapsed, forests recovered during the half millenium that is termed the Dark Ages. But at the beginning of the second millenium AD, Europe became the setting of an urban revival. Between 500 and 1000 AD, some important agricultural innovations occured, including improved ploughs, the triennal rotation of crops, the horse collar, and the horse shoe.
These technologies enabled a larger population and higher food surplus: more food could be supplied with less labour, which further aided the growth of cities in which people could do things other than working the land. The invention of the printing press, for example, further increased the demand for wood. Similarly, building gothic cathedrals required tonnes of materials, raising thermal energy use.
Urbanisation thus went hand in hand with increased industrial acitivity. Also, medieval industrial processes were less efficient than similar processes today. Up to 20 kg of charcoal (with an energy content of 600 MJ) was used to produce 1 kg of iron (compared to 20-25 MJ/kg today). Urbanisation and industrialisation increased rapidly between 1100 and 1300, which again resulted in widespread deforestation.
Windmills are only half of the story
Our romantic image of the Middle Ages and Renaissance as a paradise of renewable technologies results largely because of our failure to distinguish between thermal and kinetic energy. The Dutch and the Flemish, who dominated the Western European economy from about 1100 to 1700, are famous for their impressive use of wind technology, which took off in the 1100s.
The most spectacular use of windmills appeared in Holland from the late 1500s (16th century) onwards. There, the Dutch applied wind power to a wide range of industrial processes, including paper production, wood sawing, glass polishing and cement production. (See the article: "Wind powered factories: the history and future of the industrial windmill").
The industrial windmill was a marvel of pre-industrial technology, but it explains only partly why Holland became the most important economic power in the world during the 17th century. While sustainable providers of power, windmills could only deliver kinetic energy. To give just one example: you can use wind power to polish glass, but you can't make glass using a windmill. For that, you need thermal energy. And in pre-industrial times, as the history books tell us, the only way to reach high temperatures was to burn wood.
One problem, though: virtually all forests in the region had long vanished by the 1600s. Yet, during the Golden Age of the Netherlands, the Dutch not only made glass, they also produced bricks, tiles, ceramics and clay pipes, they refined salt and sugar, bleached linen, boiled soap, brewed beer, distilled spirits and baked bread. All these processes were based on a massive input of thermal energy.
Moreover, the Dutch produced much more than needed for domestic consumption. They became the largest European exporters of many of the above-mentioned industrially manufactured products. On a more modest scale, a similar production boom had happened in Flanders a few centuries earlier, in which an energy-intensive industry appeared in the near total absence of wood reserves. So how did the Dutch and the Flemish achieve this? By mining peat on a truly massive scale.
What is peat?
An intermediate step in the formation of coal, peat forms when plant material, usually in marshy areas, does not decay fully because of a lack of oxygen. This semicarbonised fuel can be found near the earth's surface in layers of up to 5 metres thick.
The energy density of dried and pressed peat - known as "turf" - is about 15 to 17 MJ per kg, which is similar to the energy density of dried wood (15 to 18 MJ/kg) but lower than that of coal (24 MJ/kg) or charcoal (up to 29 MJ/kg). However, it is a bulkier fuel than wood: 1m3 of coal provides 6 times as much heat as 1m3 of turf, for instance.
Turf is still used today in some countries, notably in Ireland, Finland and Russia, where it is burned in power plants and used for domestic heating. While peat is classified by the IPCC as a renewable fuel, this is highly debatable. Peat is renewed at a rate of about 1 mm per year at most, and so it takes at least 3000 years for a peat layer of 3 m to return to its original size - and only if the land is not disturbed in that time. In addition, the mining of peat has a very large impact on the landscape, as we shall see, while the burning of turf produces slightly more CO2-emissions than coal for the same energy content. The only advantage it has over coal is that it produces less smoke and has a lower sulfur content, and thus produces less air pollution than coal.
How to dig peat
In pre-industrial times, peat was dug out using very simple tools. Before being cut,the peat was often partially dehydrated by digging drainage trenches on its surface. Next, the land was stripped of its vegetation and the peat sods were cut up vertically to the required size.
The following step was to cut out the peat sods horizontally, after which they were loaded onto wheelbarrows and transported to a nearby field. There, they were laid out or stacked up vertically in a formation for drying. It took six to eight weeks for the peat sods to become dry enough to be used as fuel, after which they were beaten or trodden to make them more compact. During the drying process in the field, the peat sods were turned regularly. Finally, the peat (now called turf) was loaded in baskets and carried to the farm or the market.
Mining peat was a seasonal activity that took about 3 months per year, from late spring to early summer. Starting production earlier than April was risky because frost could damage the drying peat. Digging peat in summer was equally risky because there was a chance that it would not be dry enough following a cold and wet season. Likewise, a very hot summer could make the peat useless if it was not taken away from the drying field quickly enough - it would then be dispersed by the wind.
You could thus argue that peat has the disadvantages of both a fossil fuel and a renewable fuel, without any of the benefits. Like other better known fossil fuels, it is a non-renewable energy source that produces large amounts of CO2, yet it has an energy density that is much lower than other fossil fuels. On the other hand, peat digging is a seasonal activity with a "harvest" that may fail because of the weather. And yet, because they had no other choice, the Dutch and the Flemish built their entire economy around it.
The evolution of peat production
The evolution of peat production was eerily similar to the mining of fossil fuels today. When the easiest accessible reserves were exhausted, the peat diggers developed new technologies and methods to mine harder-to-reach resources at an ever increasing financial and environmental cost. We do not have much detailed knowledge about peat production in Flanders and Brabant, because few written records from the late Middle Ages remain. However, the history of peat production in the present-day Netherlands is relatively well documented.
Bruges, Antwerp, Amsterdam
The urban revival of the late Middle Ages started in Northern Italy, where the dominating merchant cities were Venice, Milan, Genoa and Florence. However, around 1100 a second urban core developed east of the North Sea, a region that would become known as the "Low Countries" from the 15th century onwards. This region would soon rival the economic power of the Italian cities, and become the leading economic and industrial centre in Europe from about 1500 to 1700.
The cities of Bruges, Ghent and Ypres in the province of Flanders (today a portion of Belgium) were the first to develop. Bruges, in particular, became an economic powerhouse due to its position in international trade, finance and cloth production. In 1350, Bruges and Ghent boasted a population of 90,000 and 57,000 inhabitants respectively (compared to 1,000 in Amsterdam, for instance). The picture shows the Bruges town hall, built in 1376. (Picture by Pantchoa).
Around 1500, economic power shifted to the cities of Antwerp, Brussels and Leuven (today all in Belgium) in the province of Brabant. Antwerp became the economic centre of the Western world, a position it would maintain until the end of the 1500s (16th century). By 1550, Antwerp had 90,000 inhabitants, up from 40,000 in 1500, which made it the second largest city in Europe, North of the Alps, after Paris.
In 1580, the Low Countries, then under Spanish rule, were divided into two. The seven provinces in the South revolted against the Spanish and formed a new state, the Dutch Republic (the present-day Netherlands). As a result of the subsequent chaos in the Southern provinces (present-day Belgium), the city of Antwerp lost its leading role and power shifted rapidly to the Dutch province of Holland, where the capital of Amsterdam now became the European centre of economic and industrial activity. It would remain so until the end of the 17th century.
Large-scale peat digging started in the coastal area of Flanders and northeast of Antwerp in the 1100s and 1200s respectively. The activity was largely aimed at supplying the fuel for the fast-growing cities of Bruges, Ghent and Ypres. The reserves in the coastal peat bogs of Flanders were exhausted by the end of the 1300s or 1400s, while peat production in Brabant diminished sharply during the course of the fifteenth century.
By the time Antwerp came to dominate the world economy, its peat reserves had already been dug out to satisfy the energy needs of Flanders in the course of the preceding two centuries. As a result, peat digging shifted to the neighbouring province of Holland, from where the turf was exported to Antwerp. At the time, Holland was still largely an agrarian region with relatively few energy needs. During this period, it is estimated that between 220 and 440 hectares of peat bogs were mined every year in Holland and Utrecht. Around 1530, the then accessible reserves in both provinces became exhausted, while demand continued to grow. As a result, peat prices skyrocketed.
Peat mining intensifies: peat mining below the water table
In response to this, peat diggers developed a new tool, the "baggerbeugel" (a dredging net on a long pole, there seems to be no English translation for the term). Standing on a small boat or at the waterside, this tool allowed them to cut peat below water level and haul it up. This technique, called "slagturven" (again, no English translation available), greatly enlarged mineable peat reserves.
The peat bogs in Holland and Utrecht were up to 4.5 metres thick, but because of the high water table in the region (why we call these the "Low Countries"), only the top layer could be stripped away using conventional techniques. Digging deeper would have flooded the land and made the fuel inaccessible.
However, now that it was possible to cut peat far below the water level, the complete peat bogs could be mined. There is evidence that the "baggerbeugel" was already in use in Flanders two centuries earlier, and that the knowledge of the technique was transferred to the North.
The intensification of peat production came at a cost, though. To start, mining peat from below the water table introduced extra steps in the processing of the fuel. Due to its increased water content, the muddy peat had to be spread out on narrow and elongated strips of land which were not stripped of their peat. There, the water was pressed out by people trodding on it with boards tied beneath their clogs. Only when this was done, could the peat be cut up in blocks and stacked to dry.
Environmental costs: land turned into water
Worse, however, was the destruction of the landscape and the loss of agricultural land. Wherever the peat was mined below the water table, land disappeared into the waves. This was a rather ironic consequence for a country that spent so much effort reclaiming land on the sea elsewhere on its territory through the use of windmills. Every year, about 115 to 230 hectares of land was lost as a result of peat production below the water table. The exhausted peat bogs formed lakes that expanded to cover vast areas throughout Holland and Utrecht.
Only the elongated strips of land used to dehydrate the muddy peat remained. Historian Jan de Vries (see references) notes that the area between Amsterdam, Rotterdam and Utrecht "took on the appearance of a veritable Swiss cheese, with dozens of water-filled, exhausted peat bogs often separated from each other by nothing more than narrow, vulnerable strips of land on which were scattered the structures of what once had been farms".
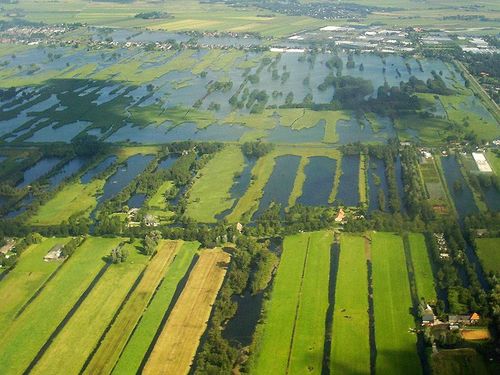
Some of these typical lakes still remain. The picture shows the "Nieuwkoopse Plassen" in Holland, today a nature reserve of 1,400 hectares. Other remaining examples are the "Loosdrechtse plassen" and "Vinkeveense plassen" in the province of Utrecht. Often, even the narrow ridges of land used for drying the peat were eventually mined or simply washed away by the waves during storms.
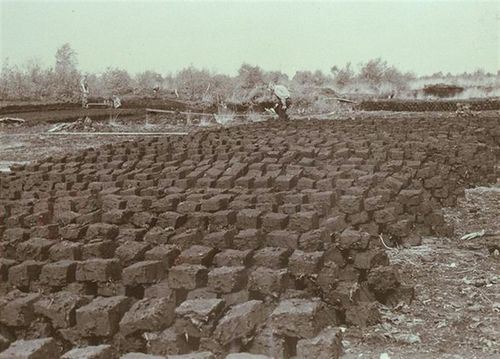
Things got out of hand when entire villages disappeared. Historian J.W. De Zeeuw (see references): "Around 1600, these lakes occupied most of the area between the rivers Oude Rijn, Gouwe and Hollandse Ijssel and threatened the villages of Zevenhuizen, Moerkapelle and Waddinxveen. In 1630, the church of Jacobswoude, North of the Oude Rijn, was pulled down because by then the rest of the village had been swallowed by the waves of encircling man-made lakes."
The authorities, horrified by the loss of agricultural land - and the associated tax income - tried to stop the peat diggers during the sixteenth century by placing export prohibitions and restrictions on peat mining below the water table, but they failed. Digging out peat was more lucrative than cultivating crops. In total, peat digging would turn more than 60,000 hectares (600 km2) of land into water in Holland and Utrecht - almost 10 percent of their total surface area.
Peat production moves to the North: canal digging
Again, energy demand rose significantly from the late 16th century onwards, when economic power shifted from Flanders and Brabant to Holland. In spite of the environmental damage, peat production in the low peat bogs of Holland and Utrecht continued on a casual basis during the 1600s, with an average production of 200 hectares per year. However, this was not enough to satisfy the growing demand for the fuel, and turf prices started rising again.
In response, from the 1580s onwards, attention shifted to the somewhat higher lying peat bogs in the northern provinces of Friesland, Groningen and Drenthe - 200 to 250 kilometres away (see the map on the left). There, total production during the seventeenth century would rise to an average of almost 400 hectares per year. Most of the turf was exported to Holland.
However, mining these reserves was a totally different matter because there were few waterways. Transporting the turf all the way to the Zuiderzee, from where it could be shipped to Holland and Utrecht, would have been inordinately expensive given the transport options of the day. In order to exploit the high peat bogs in the Northern provinces, ditches and canals had to be dug, which required a large capital investment.
Historian Jan de Vries: "The result was that, instead of the numerous individual peat diggers each working small parcels of 'laagveen' [low bogs], the peat in the 'hoogveen' [high bogs] was mined by consortia of investors (urban capitalists from the western cities) who judged market conditions sufficiently attractive to buy up vast tracts of uninhabited bog, dig lengthy canals into the bogs, and hire armies of laborers to dig the peat".
The maps shown here illustrate the extensive canal infrastructure that was built in the Northern provinces of the present-day Netherlands from the 1580s onwards. In the high peat regions of Groningen and Eastern Drenthe, canal building continued uninterrupted from 1580 to 1650, which opened up the main body of the peat deposit. This made some 30,000 hectares of peat available for shipping. In the high peat region of Western Drenthe, Friesland and Overijssel, canals were dug between 1600 and 1670 to reach some 30,000 hectares of peat. In total, it is estimated that some 700 km of canals were built in the northern provinces, specifically aimed at turf transport. A substantial amount of them remain, with sometimes surprising results, such as towns without roads.
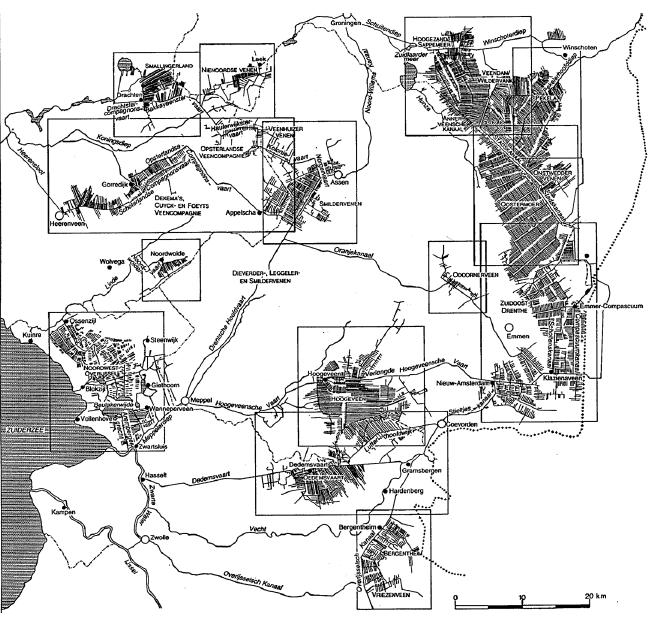
Canal building had happened before in Flanders and Brabant, where the monasteries seem to have been the driving force behind large-scale, organized peat production, buying up land and hiring peat diggers. In the peat bogs in Brabant, Northeast of Antwerp, from about 1300 onwards some 20 turf canals were dug up to 16 m above sea level, each reaching lengths of 10 to 20 km. The main canals, which connected the export harbours with the peat areas, attained a total length of more than 320 km. Aqueducts were built to help the canals cross the brooks. In the Northern provinces of the Netherlands, the total length of the canals reached at least 700 km.
Peat production versus agriculture
The exploitation of the high peat bogs in the North did not always result in the loss of agricultural land, as it did in the South. Firstly, because the peat mining companies converted some peat bogs into permanently agricultural land after the peat had been dug out.
J.W. De Vries: "Once the peat was stripped away, these enterprises had a further interest in making use of the newly exposed underlying soils. Since this soil lay above the water table, the cost of converting it into productive agricultural land consisted primarily of taking the trouble to conserve the surface soil (which was [in the case of high peat bogs] in any event poor quality peat) so that it could be re-spread over the land, and heavily manuring the new soil. This occurred most systematically in Groningen, where the capital city encouraged agricultural development of the hoogveen by subsidizing the distribution of night soil."
The new canal network created to move the turf to Holland's industry in the South also provided low-cost transport for agriculture which, by itself, could never have afforded such an investment. However, the efforts to reclaim agricultural land in some parts of the country did not make up for the much larger losses elsewhere on the territory.
Few peat bogs in Groningen were brought under cultivation during the Golden Age - it was only with the arrival of artificial fertilizers at the end of the nineteenth century that large-scale recultivation could begin. In the province of Friesland, the underlying soil was not suited for agriculture and peat digging resulted in large lakes which still exist today. And as we have seen, vast tracts of (potential) agricultural land disappeared in the waves in the Southern part of the country. The result is that the Dutch became, unlike other European countries at that time, highly dependent on food imports. They produced vegetables, meat and dairy products, but they had to import about half of their grain (the staple food) from the Baltic regions - a very costly affair.
Energy consumption per capita
Until the twentieth century, the Dutch stripped an estimated 283,500 hectares (2,835 square km) of peat, close to 10 percent of the total surface of the Netherlands. However, only two-thirds of this was mined in pre-industrial times. Peat digging in the Netherlands continued until 1950 using mechanical peat diggers powered by coal, as it happened in many other countries from the end of the nineteenth century.
If we take 1850 as the start of the "modern" peat mining era (the Netherlands were very late to enter the Industrial Revolution), the pre-industrial use of peat in the country amounts to just over 190,000 hectares from about 1300 to 1850. Of this, some 70,000 hectares were mined from 1600 to 1700, which roughly corresponds with the "Golden Age" of the Netherlands. All these figures are deduced from a 1978 paper by J.W. de Zeeuw, "Peat and the Dutch Golden Age" (see references). Other authors (like Jan de Vries) give higher estimates in more recent studies, with about 275,000 hectares of peat stripped after 1600. Either way, almost all peat that existed in the Netherlands has been mined.
De Zeeuw also calculated the heat content of the extracted peat, taking into account the average thickness of the mined peat layers after dehydration. He concluded that in an average year in the seventeenth century, the Dutch consumed 25,120,800 GJ of turf. With an average population of 1.5 million this amounts to 16.75 GJ per capita per year.
Other authors have come to similar figures, ranging from 13.4 to 19.3 GJ per capita per year. This is similar to dozens of poor countries today, some of which do not even reach 10 GJ per capita. Average energy consumption per capita worldwide was 76.6 GJ in 2008, only 4.5 times higher than in the seventeenth century Netherlands (though the Dutch themselves now consume much more, with 210 GJ/capita in 2003). It should be noted that the figure of 16.75 GJ/capita only includes turf consumption, not other energy sources like wind, animal labour, firewood, charcoal and coal (see further).
Urbanization and industrialisation in 17th century Holland
The high energy consumption of the Dutch was an anomaly in seventeenth century Europe. The same goes for their prosperity, and for the level of urbanization and industrialisation in the country.
More than 60 percent of Dutch people lived in cities, compared to about 10 percent in most other European countries at the end of the 17th century. The level of urbanisation in seventeenth century Netherlands was only attained in other European countries at the turn of the twentieth century. A similar development happened in Flanders and Brabant in the 1500s, where over 30 percent of the population lived in cities with more than 10,000 inhabitants. From about 1600 to 1720, the Dutch had the highest per capita income in the world - at least double that of neighbouring countries at the time and about five times higher than that of the poorest countries today.
The opening of the peat bogs in the northern provinces from the 1580s onwards meant that the Dutch had a cheap energy source that was widely available, while most other countries in Europe were entirely dependent on wood - which had become ever more expensive as deforestation advanced. The Netherlands' ample fuel reserves stimulated the development of various fuel-instensive and export-oriented industries.
In several cases, the presence of these industries was solely based on the abundant and cheap supply of thermal energy. This was the case for sugar refinement, for example, which is a purely thermal process. Sugar became the world's most important commodity in the seventeenth century, and Amsterdam was Europe's largest sugar refiner by 1650. In 1662, more than half of Europe's one hundred sugar refineries were located in the Netherlands, all of which processed imported sugar from South America and the Carribean.
Salt refinement too was based solely on a massive input of thermal energy. Salt was indispensable as a preserver of meat, fish and dairy products before electrical refrigeration was available. The Netherlands had 293 salt refineries in 1674, most of them concentrated in Holland and each consuming about 800 tonnes of turf per year. About sixty of these refineries were used for packing herring barrels, another important export. In addition, the city of Haarlem became the bleacher of German linen, another industrial process that was purely built on thermal energy. For all these industries, the iconic Dutch windmills did not offer any direct advantage.
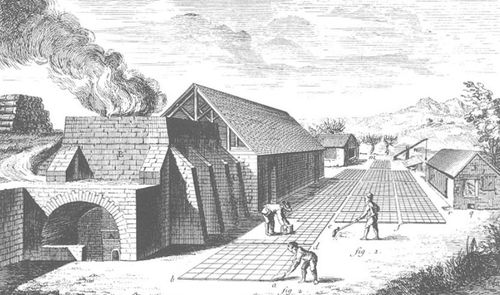
The success of other industries, however, was based on the combination of turf and wind power. The best example of this lies in the shipping industry. Holland became the leading builder of ships in Europe in the course of the seventeenth century. From 1625 to 1700, the Dutch shipyards produced as many as 500 seafaring vessels per year, many of them commissioned by foreign powers. The wood used to build the ships was sawn using sophisticated wind powered saw mills invented in 1596, while peat provided thermal energy for many shipbuilding processes, such as bending planks, melting tar and forging iron fittings.
Apart from that, peat offered an important indirect advantage. While a large-scale use of peat did not prevent the Dutch from importing large amounts of wood, peat catered to their thermal energy needs, and so all imported wood was almost exclusively used as a construction material. This generated a much higher return on investment than its use as firewood, and made the Dutch less vulnerable to high wood prices. Turf was also the fuel of choice for heating homes and public buildings, and for cooking. Only the very rich used firewood, which was much more expensive but produced less pollution.
Why was peat only used in the Low Countries?
The Low Countries were not the only region that suffered from a severe shortage of wood reserves between 1100 and 1700. In addition, peat was found over large parts of Europe, most notably north of the Alps. Why, then, did other countries not resolve their energy shortages by mining peat?
For these pre-industrial countries, the value of energy deposits depended on the cost of transportation rather than the cost of gathering the fuel itself. There exists no period in history when a global, continental or even national shortage of wood occured. The problem was always local, caused by deforestation around urban (and industrial) centers.
Land-based transport - which amounted to carts on bad roads - was extremely slow, labour-intensive and expensive, limiting the practical distance between energy deposits and consumption centres to 20 to 25 km at most. The only exception to this was transport on water, which, in pre-industrial times, was powered by wind or by animal or human labour on towpaths (this was much more efficient than land-based transportation because of low friction-resistance).
One look at the map of the Low Countries immediately reveals why the region could afford to transport turf over large distances: it is criss-crossed by lakes and rivers. From Groningen and Friesland in the outermost northern part of the present-day Netherlands, one can sail (almost literally) straight to Amsterdam, Utrecht, Rotterdam, and then Antwerp, Brussels, Ghent and Bruges in present-day Belgium. No other region in Europe has such a dense water transport network.
To boot, the region is windy and flat, offering great conditions for sailing - and deforestation only improved these conditions. Importantly, the Low Countries are located near the water table - as were their peat reserves. The digging of navigable canals in the peat areas, and the linking of these canals to the already existing, extensive network of natural waterways was relatively easy. Because these natural waterways gave access to all major cities, the turf could be transported by ship directly from the peat fields to the doorstep of the consumer. Hardly any land-based transportation was involved, and this kept costs low.
In most other countries, peat reserves were located too far above the water table, making the construction of canals much more expensive. Often, cities were too far from potential peat reserves or did not have access to navigable rivers. This explains why large-scale peat digging in other European countries and the US only started at the end of the nineteenth century, when peat could be hauled by steam trains or locally converted to electricity (which is easier to transport).
Coal and the end of the Dutch Golden Age
Peat was not the only fossil fuel used during the second millenium AD in Europe. Coal mining started in the thirteenth century in England, Wales and what is now the French speaking part of Belgium. All over Europe, coal quickly became a wanted fuel for specific industrial processes, particularly for blacksmithing and lime manufacturing.
Large-scale coal mining started in the 1400s. In 1430, between 1,600 and 2,000 people worked in the coal industry in Liège (present-day Belgium). From the 1500s onwards, coal was used on an ever increasing scale in London, which was then one of the most populated cities in Europe. There, coal was used industrially, but more often in households for heating and cooking.
At the beginning of the 1600s, when the Dutch Golden Age began, coal accounted for three quarters of fuel consumption in London, which caused extensive air pollution. Coal burns much dirtier than wood, which is the reason why it was previously forbidden in England. However, the acute shortage of firewood from the 1500s onwards left the English little other choice than to switch to the abundant fuel. Peat was not an option for the English for many of the reasons mentioned above.
The crucial role of iron production
Initially, coal offered significant drawbacks compared to peat, which meant that England's early use of fossil fuels did not provide a commercial advantage during the seventeenth century. In most production processes, coal could not be used because it came into direct contact with the product, which was then ruined by coal's impurities - notably sulfur. Only in processes where the product could be separated from the fuel did the substitution of coal for wood cause no problems.
Because of its lower sulfur content, peat did not have these limitations. The Dutch could use it for almost all thermal processes in their industries. Over time, however, the English managed to adapt their industrial processes for the use of coal instead of wood and charcoal. With every step they took, the English slowly caught up to the Dutch. A turning point came at the dawn of the eighteenth century when the last - and most important - industrial process was converted to coal: the production of iron.

This last step, made possible by the introduction of 'cokes' or purified coal, marked the start of the Industrial Revolution in the Western world. (It should be noted that the Chinese already developed this process in the 11th century). From then on, the use of iron as a construction material was no longer limited by the supply of wood.
Turf, on the other hand, could not deliver the intense heat produced by coal, and hence was not used in iron production, nor to power steam engines. (The Dutch never produced iron, they imported it). Moreover, the caloric value of coal is four times higher than that of turf for a given volume, making it much easier to transport and store than peat. The combination of steam power and iron brought the English the rail system, solving the problem of transporting their fuel supply. The railway also proved faster and more flexible than the canal system.
Exhaustion of the accessible peat reserves
Around the same time, the most accessible Dutch peat reserves became exhausted. In addition, there was a growing problem with the silting of the shallow harbours and waterways, increasing the costs of turf transport. More and more sandbanks appeared, over which vessels had to be dragged. A similar thing happened in Bruges a few centuries earlier. The unique geographical conditions of the Low Countries, which made the early large-scale use of fossil fuels possible, eventually became a disadvantage. The depletion of the peat reserves and the difficulties in turf transport led to rising turf prices, until the point at which imported coal became cheaper.
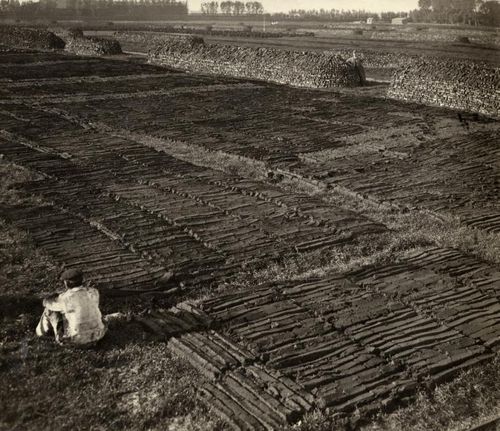
To combat this, Dutch industries switched from peat to coal, whenever they could adapt their production to use the cheaper fuel. English export of coal to Holland rose from 35,200 tonnes in 1700 to 117,900 tonnes in around 1750. The import of coal put Dutch industries at a disadvantage, because the English added tax duties. From the 1700s on, Dutch prosperity began to decline. The import of grain became too expensive, and de-urbanisation set in as more people returned to farming. By 1815, the level of urbanization had fallen back from 60 to 38 percent.
Can we power a prosperous society on renewable energy?
Pre-industrial use of coal and peat occured succesively in those parts of Europe that dominated industrial production from the 1100s to the start of the Industrial Revolution. The Flemish, the Dutch and the English, consecutively, became the most prosperous regions in Europe at the very moments when they used the largest amounts of fossil fuels. In other words, all economic success stories of the past millenium are based on an ample supply of fossil fuels - accompanied by serious ecological damage. Moreover, these regions produced many exports, so that countries that did not use fossil fuels also benefitted from their application.
All this does not mean that a prosperous society cannot be built on 100 percent renewables. We can now transport biomass over larger distances, due to good roads and cost-effective transport options. And I am not referring to motorways and diesel trucks, but to trains, strip roads, trolleytrucks, cargo bicycles and light electric vehicles in flat areas, and aerial ropeways and cable trains in mountainous regions.
Furthermore, we now have an additional renewable energy source that could deliver vast amounts of thermal energy: solar thermal power (see article "The bright future of solar powered factories"). The merits of solar thermal heat and concentrated solar power have been known for centuries, but the materials and industrial processes for large-scale deployment only became available at the end of the nineteenth century. The same applies to geothermal power, the potential use of which was previously limited because of a lack of materials and technology.
It is obvious that a prosperous future for seven billion people cannot be based on pre-industrial technology. The key to our success, however, lies in choosing the best of industrial technology and discarding the rest.
Kris De Decker (edited by Deva Lee & Shameez Joubert)
Sources:
- "Energiemarkten en energiehandel in Holland in de late middeleeuwen", Charles Cornelisse, 2008.
- "Peat and the Dutch golden age" (.pdf), J.W. de Zeeuw, 1978.
- "The First Modern Economy: Success, Failure, and Perseverance of the Dutch Economy, 1500-1815
", Jan de Vries, 1997.
- "The Economy of Europe in an Age of Crisis, 1600-1750", Jan De Vries, 1976
- "Verdwenen venen. Een onderzoek naar de ligging en exploitatie van thans verdwenen venen in het gebied tussen Antwerpen, Turnhout, Geertruidenberg en Willemstad. 1250-1750", K.A.H.W. Leenders, 1989 (English summary).
- "Peat and Canals" (.pdf), Michiel A.W. Gerding
- "Meeten, boren en besien: turfwinning in de buitenrijnse ambachten van het Hoogheemraadschap van Rijnland 1680-1800", A.J.J. van't Riet, 2005
- "Delfstoffen, machine- en scheepsbouw", in "Geschiedenis van de techniek in Nederland", H.W. Lintsen, 1993.
- "Het verloren technisch paradijs", in "Geschiedenis van de techniek in Nederland". H.W. Lintsen, 1993.
- "Vervening", "Turfsteken", "Veen", "Slagturven", "Baggerbeugel", Dutch Wikipedia.
- "Canals and energy. The relationship between canals and the extraction of peat in the Netherlands 1500-1950" (.pdf), Michiel A.W. Gerding, in "Peatlands", February 2010.
- "The Rise of Commercial Empires: England and the Netherlands in the Age of Mercantilism, 1650-1770
", David Ormrod, 2003
- "A Forest Journey: The Story of Wood and Civilization", second edition, John Perlin, 2005
- "The Making of Urban Europe, 1000-1994
", Paul M. Hohenberg & Lynn Hollen Lees, 1985
- "Urban World History: an Economic and Geographical Perspective.: An article from: Canadian Journal of Regional Science
", Luc-Normand Tellier, 2009
- "Peatlands and climate change" (pdf), International Peat Society, 2008
- "The Dutch Republic in the Seventeenth Century: The Golden Age
", Maarten Roy Prak, Diane Webb, 2005.
- "The Rise of the Amsterdam Market And Information Exchange: Merchants, Commercial Expansion And Change in the Spatial Economy of the Low Countries, C.1550-1630", Clé Lesger, 2006.
- "Turf fires -burning peat". Old and Interesting.
- "The Mother of All Trades: The Baltic Grain Trade in Amsterdam from the Late 16th to the Early 19th Century
", Milja van Tielhof, 2002.
- "Energy transitions: history, requirements, prospects", Vaclac Smil, 2010.
Hi Kris,
Thank you for a terrific post. Fascinating.
Dave
Seconded. Great post, Kris. Thank you!
John
Yes. A fascinating read. Most of us today only know peat as a soil conditioner. Fascinating in a manner similar to guns germs ans steel, why did region X dominate for a few hundred years, then go into relative decline.
Thanks for this terrific historical account.
Many thanks, Kris, for this absolutely brilliant article!
Despite a fascination with European history, this is the very first time that I have seen the Dutch Golden Age tied to their consumption of a fossil fuel.
I wonder how much the lessons from their peat experience have stayed with them. I have held the Dutch up as an example of enlightened management of natural gas resources in talks with the following slide:
The way I have told this story, it is their experience with dikes and "polder" mentality that led to a conservative management strategy for natural gas. But your article provides wonderful new insight into the Dutch and potential historical underpinnings for current policy decisions.
Fascinating!
Jon
Well not quite. Most of Dutch gas occurs in Permian sandstones (Rotliegendes) sourced from Carboniferous coal measures - it is largely dry nat gas. The Gas in UK, S North Sea is a similar play. But further north its completely different with a range of plays from oil associated wet gas, gas condensates, HPHT condensates, and post mature drier gas - most of this sourced from the Jurassic Kim Clay. And much of Dutch gas occurs in just one field - Groningen. But apart from that, I agree that Dutch policy has been very enlightened - and most of it is produced by NAM - a Shell / Exxon consortium.
¥
Just looked up Utrecht province, what happened over there is absolutely incredible. Great article.
The English mines started using coal seam outcrops. Eventually these were mined down to the water level, making pumping necessary. Some mines used as many as 500 horses for pumping water.
The steam engine seems like an invention way ahead of its time(1712). I am amazed that Newcomen was able to build one that actually worked. The world had no machinist because there were no machines as we know them. Machine tools, such as the slide rest lathe, milling machine and metal planer, would take another 100 years to be invented. There were no interchangeable parts until precision metal working was perfected ca. 1840s, and then it was just for guns and clocks. Steps toward interchangeable parts for steam engines began taking place in the 1860s.
The blast furnace was another sophisticated invention. Unlike the bloomery, the blast furnace operated continuously and was a countercurrent exchange operation, very efficient in using the carbon (as monoxide) for reducing the ore and also being energy efficient. But the product was pig iron rather than wrought iron produced by the bloomery. Pig iron required additional refining and hammering to be converted to wrought iron.
Charcoal for iron smelting took far more labor than running a blast furnace, perhaps 8 or 10 times as much. The ability to use coke for iron smelting saved a lot of labor because coke took a fraction of the labor as charcoal.
Steel use and production in the U.S. peaked 1973, both in absolute and especially per capita terms. Part of the reason we use less is because the weight of cars has declined, highway construction is way down, and high rise building has also declined. Pig iron production is down because we recycle more steel, and cars last longer. Car sales have probably peaked and are in long term decline, just like steel since 1973.
This is a fascinating article, but the author is evidently not a plant ecologist, forester or botanist. I get tired of pointing out that deforestation is due more to agriculture than to urbanisation or industrialisation. (TOD readers may also be tired of me pointing this out...)
More seriously, the categorisation of peat as a pure "fossil fuel" is far too extreme, as is the statement "Peat is renewed at a rate of about 1 mm per year at most". Actually, 1mm/year is generally accepted as the average value for the main circumboreal peat bog zone. And in milder maritime climates like Britain, Ireland, and of course the Netherlands, the accumulation rate is much higher. I estimated about 5mm/year at 100m elevation in Aberdeenshire. 28mm/year has been measured in Western Norway. A (lengthy!) discussion can be found at http://www.uel.ac.uk/erg/documents/Peatbogsandcarbon-Part2-Peatandcarbon....
Peat growth tends to be self-limiting, as erosion and decomposition counterbalance the renewal process - hence it is easy to underestimate the latter. Peat will never be a major renewable energy source, but the story of the Dutch peat industry shows it shouldn't be ignored completely.
Peat is still heavily exploited in Ireland. In Scotland there is still some hand-cutting. And the reason that peat was not an option for England after 1500 is only because the main deposits were exhausted by that time - for example see http://www.visitnorfolk.co.uk/explore-norfolk/norfolk-broads-history.aspx.
I get tired of pointing out that deforestation is due more to agriculture than to urbanisation or industrialisation.
Aren't they all tied together some as urbanization gives higher population densities that require more agriculture. The value added products of urban industry make food cheaper per man hour work so a higher population can support itself requiring even more agricultural land...and on and on until some resource gives out.
Kris's fine article throws 'fossil fuel' (or a very close relative to it anyway) into the mix as the great accelerant to the whole process which then deforests even more land so more agriculture can support more city people...
until we get to modern times and modern fossil fuel derived fetilizer...lots of opinions on where that goes next.
There is quite a lot of farming land that have been planted with trees in Sweden since modern fertilizers started to be used. The country side is actually full of abandoned barns. There is also a lot of unused houses, some are simply abandoned others have disappeared and some are used only on holidays-
If we made the decision to "mine" and sequester peat -as an atmospheric carbon removal process, what sort of annual tonnages of CO2 removal is possible? I can imagine the world getting to that point before much longer. What sort of price of carbon would it take?
IPA map: Distribution of permafrost and ground ice in the Northern Hemisphere, based on the EASE-Grid version of the International Permafrost Association map. "High," "Med," and "Low" refer to ice content, and "T" and "t" refer to thick and thin overburden, respectively. Image courtesy International Permafrost Association, supplied by Tingjun Zhang, National Snow and Ice Data Center, University of Colorado, Boulder.
Considering frozen saturated peat (or material working its way to becoming peat) is a not so very inaccurate a description of a huge bulk of permafrost soils and considering the area of the northern hemisphere that is permafrost...well the only sequestering mechanism I can envision is freezing it...
Where a person lives certainly affects the way they see scale. In my case (with discontinuous permafrost soils maybe not actually under my property but certainly underlying a big part of what can be seen from it) I can see about 270 square miles out my front window--that corresponds to the area mined for peat during Netherland's 'golden age,' about 70,000 hectares. That didn't seem like all that big as chunk of land in my mind's eye. I'm exaggerating slightly, near hills block some of the view. Other wise "I can see Russia from my house" well I could if Big Diomede was maybe an 80,000 to 100,000 foot tall mountain and the weather was really, really clear
?- )
[edit add on]
and again great read Kris, always have fun learning from your posts. So peat powered the strain of mercantilism/captilism that the Netherlands exported to England that was evnetually spun off to make the USA... interesting
I am surprised that there is no mention of water mills. A lot of British industry was originally powered this way, which is why the cotton and wool industries were located in the north, along the Penines
The low countries used wind power because they were so flat they had few water mill sites.
A count for mills in England ca. 1086 was given in the Domesday book. http://en.wikipedia.org/wiki/Domesday_Book
There were several thousand mills listed, but as I recall, there was no distinction between wind and water; however, they were assumed to be water mills.
Water mills are shown powering mining equipment, such as mine hoists and stamp mills, in De Re Metallica (1555).
http://en.wikipedia.org/wiki/De_re_metallica The book contains over 200 woodblock illustrations and descriptions of locating ores, mining, ore processing and smelting.
Any comments about peat in the United States? I personally have only heard about discussion of peat in reference to the British Isles (until this post about the Netherlands).
Try this: http://minerals.usgs.gov/minerals/pubs/commodity/peat/dir-2008-peat.pdf
Terriric story. I've long been interested in the beginnings of the industrial revolution but have always focused on England. This was a new insight.
Two things struck me as particularly relevant for today. First, men are willing to put up with incredible damage to the environment to fill their pockets. That hasn't changed. Second, deindustrial-ization, at least on a local level, has even happened in Europe and not that long ago. So a repeat of that is certainly possible. I suppose if there had been more peat in the area there would have been no farmland to go back to when it was gone.
I'm glad to see a post from Low-tech and I encourage others to read his blog. I think he has some of the most well researched articles I have read to date.
I believe we are at or past 'peak' and to me his articles are a "must" read to get knowledgeable ideas of what actually works.
I for one am very glad to see this posted here on TOD.
I am also glad to see another of Low-Tech's articles posted here. I found that site several years ago and have always found the articles well researched and interesting and thought provoking.
Actually, I believe it may have been the seven provinces in the North (not the South) that revolted against the Spanish...
Overall, I thought this was a superb article. This topic of peat as a vital (then declining) factor in the early economic power of the Low Countries seems highly relevant to our current world energy situation, yet this is the first time I've ever read a thoughtful analysis of the subject.
There are probably deposits of peat in many many places where it is not recognized as such. There is a name for it as a soil type, but I can't remember it right off the bat.
I have seen it in areas where construction work was being done on low lying wet ground.Nobody to my knowledge has ever made a practice of burning it around here, as wood has always been plentiful.
My great grand parents who are of course long since gone used to talk about it, but only as something they heard themselves from their own old folks who came over from the "old country".
I have seen it burn,where construction work was underway, when a piece of formerly wet ground was ditched and drained, and a long hard drought followed, and a fire was accidentally started.It is hard to put out as it burns like a large pile of sawdust.The fire burns low and slow and enough air filters in to keep it burning, but water poured on it mostly runs off without penetrating enough to put it out without actually flooding the area.
The first such fire I have seen occurred near home.
The land owner piled waste wood from clearing the surrounding land there with a bulldozer and lit it deliberately to get rid of it during a dry spell.This was the perfect spot to get rid of it since hardly anything would grow there.There was nothing else nearby to burn, after clearing the land, so it was safe enough to do so.
The fire lasted a couple of days longer than usual, and afterwords there was a quite noticeable depression at the site.The heat from the primary fire dried the already drought dry peaty soil enough for it to burn itself, once it was lit by the logs and stumps burning.
There are probably huge deposits of peat in many areas in the southeast.It may be that in a few more generations, people will be burning it for winter heat and maybe even for industrial purposes.The local forests won't last very long at all once the coal and natural gas play out.
Low Tech is one of my favorite sites.
Hats off to Kris!
but water poured on it mostly runs off without penetrating enough to put it out without actually flooding the area.
Peat fires in the wild are notoriously tenacious. It's not all that unusual in these parts for the first forest fire of the season to be peat fire that overwintered under the snow and took off as soon as it melted off.
It is tough stuff. Years back I made the mistake of buying ten yds of peat instead of a 50/50 sand/peat mix from one of the local gravel operations-they strip the peat off the old river bottom gravel deposits. Well long story short winter was coming and the load of peat was still in my parking place so I packed it tight in some quick made log enclosed raised beds. Barely a weed took hold in that stuff for several years. To water flowers we have since planted in it I jam the hose nozzle in the ground and blast repeatedly. That stuff is really hard to get wet.
There may be one more important angle to this peat story. As I understand it, peat plays an essential role in producing traditional scotch whiskey. Peat is not a direct ingredient in scotch, but it is known to impart the characteristic smokey flavors to scotch whiskey, when the malted barley ingredient is dried over burning peat fires. This is especially true with the currently popular single malt scotch whiskeys.
Hopefully someone will think to reserve a healthy supply of peat for this purpose, should the overall peat supply ever be at risk. In fact, Scotland and other nations may want to consider establishing a Strategic Peat Reserve...
Scotland has > 2 million hectares of peatland, average depth 2.4m, so our Strategic Peat Reserve currently holds some 50 billion cubic metres - for those who prefer to think in barrels, that's 300 Gb. The USA's SPR is tiny in comparison.
So I can assure you that Peak Whisky is not an imminent danger.
Nonetheless, it may be worth setting up an Association for the Study of Peak Whisky and I shall be happy to organise an inaugural meeting at a suitable Highland hostelry, if there is sufficient interest. Serious threats to civilised existence do require careful study.
Dont forget why scandinavian and alpine regions became rich: the development of hydro energy on the right moment in the industrialisation period and subsequent building of industry. So after the low countries paved the way with peat and coal.
As a single malt aficionado for over 40 years I agree that a strategic reserve of peat is most important:-) The water used is also peat seeped for flavour.
There is one NA single malt that legally can't be called Scotch but sure tastes like Scotch --- http://www.glenoradistillery.com/glenbreton.htm
Very interesting to read about the conflict between peat mining and agriculture as production methods went deeper and deeper.
Today, we have the same problem with coal seam gas clashing with agriculture in Australia
http://www.abc.net.au/rural/coalseamgas/default.htm
Look at how the landscape is disturbed:
http://www.abc.net.au/news/2011-08-30/aerial-photo-of-coal-seam-wells/28...
And compare the energy: 1 CSG well produces around 0.7 TJ per day or 255 TJ pa
The image above has about 90 wells, that is 23 PJ pa which is similar to the figure of 25 million GJ for the Dutch consumption in the 17th century
Truly excellent article. So what conditions would cause existing peat to decay?
I'm not experienced with peat soils, but I'll hazard a guess;peat simply won't decay unless it drys out enough for it to be colonized by the fauna and flora indigenous to the local area.
This would involve a substantial lowering the water table, over a very long period of time-many many years probably.Such a change could probably only be expected to come about as the result of significant climate change , either natural or forced.
If conditions remain stable, the deposit will likely grow rather than decay.
Very interesting. Truly amazing considering that all of this peat accumulated since the last ice age.
A great article.
I wouldn't dismiss windpower as a heat-source quite so quickly. The use of heat pumps; heat recycling; and high efficiency facilitated by the convenience of electricity mean that it would probably be preferred over solar heat for most industrial and commercial applications. Residential applications, of course, fit elegantly with solar heat.
The key to our success, however, lies in choosing the best of industrial technology and discarding the rest.
And who will make this decision?
If I were to ask Apple, they'd say the iPhone is the best phone. Google - Android. Kyoceria - a locked down android. HTC - their rootable phones.
Where are these people with the Wisdom of Solomon to be found who will find this best tech?
Missed one
If I were to ask Apple, they'd say the iPhone is the best phone. Google - Android. Kyoceria - a locked down android. HTC - their rootable phones, Microsoft - anyone else's.
NAOM