Tech Talk: Working Thin Coal - the Coal Plow and Hydrominer
Posted by Heading Out on August 29, 2010 - 10:50am
In the last couple of years, there has been a growing concern about the amount of coal that remains in the productive reserve for the world. At the same time, the incoming British Government, which had been somewhat antagonistic to coal while in opposition, may be giving large coal-fired power plants a reprieve. Questions might therefore arise as to how long this fuel source is going to last, if use increases more than projected. While I am not going to answer that specific question today, I will address a part of the issue. Namely, what do you use to mine coal when the seams get too thin for modern equipment?
The lowest coal which I personally have mined was about 1 ft 8 inches high. The low coal was caused by a roll in the middle of the face (the floor got closer to the roof) which was normally about 3 ft high (the Beaumont seam at Seghill Colliery in the spring of 1962). In that height you lie on your back, put a pit prop under your shoulder to give you some leverage, and shovel across your chest. In more advanced mining countries it is unlikely that we will return to such manual labor, which is not very productive. So what do you use?
The most productive machine in most longwall operations is the shearer, which I described in the last tech post. The problem is that it most effectively runs on top of the armored face conveyor (AFC) and the power pack that drives the cutting head, and the haulage unit takes up quite a bit of space. One idea was to take the shearer off the conveyor and have it slide along the ground on special shoes, with the cutting head mounted ahead of it on the longwall. My father had rather strong opinions on this, since two of the mines he worked with had such machines. Remember that the coal conveyor must snake over behind the machine in order to allow the supports to also advance.
.jpg)
To hold the machine together, the gear boxes at each end and the power pack in the middle, there are through-bolts down the machine. Now it breaks down in low coal. The roof is say 2 ft 6 inches above the floor, the machine is 22 ft long, and the conveyor is 7 inches high. How are you going to take the machine apart to fix it? (The answer involves explosives, and is not a “quick fix.”)*
So if the shearer is not an ideal machine, what is? The answer is known as a coal plow (or Hobel in Germany where they were developed by a company then called Westfalia Lunen.) Very simply in some coal types, particularly those that are brittle, the coal at the front of the face is weakened and cracked by the pressure of the overlying ground. Thus if you take a narrow pick and drag it across the coal it will peel off some coal. Put a number of these picks together and the coal between them will also chip off – perhaps to a depth of a couple of inches. Make the machine move down the face rapidly, with the rams pushing through the AFC to keep the plow pressed against the coal, and you have a simple but effective mining machine.
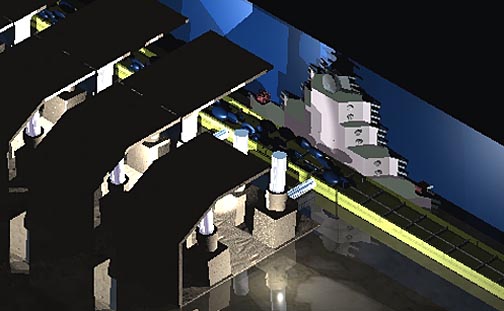
The coal in which this is most effective does not necessarily have to be mined over its full height, since often, when undercut, it will fall under its own weight. Depending on the coal strength, the depth of cut of the machine can be adjusted. As a result the coal produced can be quite large, sometimes bigger than the average size of the fragment coming from a longwall shearer face. It is, however, an "interesting" experience, to see one working under a sandstone roof, where the face rolls a bit.
There were a variety of plows built, depending on coal height, coal type, and the speed at which the plow could be moved down the face. It is a fast moving operation, but one that is not that popular at the moment, since, in most higher coal a shearer may be more effective and produce more coal. However in the years to come the plow may make a comeback.
By then, however, it is possible that the picks on the machine, that generate dust, will be replaced by high pressure (10,000 psi) water jets which cut into the coal perhaps a foot ahead of the machine, and allow mining without the generation of the dust and sparks that make current operations so dangerous. It has been done before, and is a relatively simple technology to adapt to future conditions.
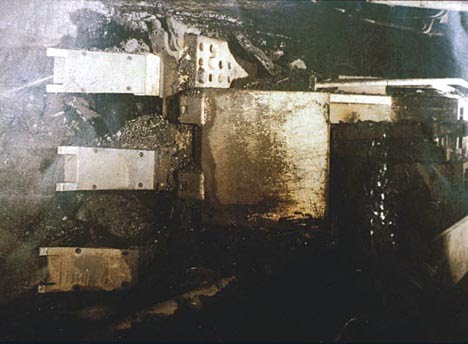
We called it the Hydrominer, and as I learn how, I’ll put up some video on Youtube of it operating. There are better ways of using the jets than those shown, so that the plow can actually mine coal to a web depth of over 3 ft 9 inches (we have) at shearer speeds.
Incidentally longwall mining was not a part of the Modern Marvels review of Coal Mining, though in Part 3 they do show the development of the continuous miner, and shuttle car. (H/t to Pasttense who gives a list of some Youtube films), though there are a number more than I had thought there would be.
* At least in those days they excavated a chamber ahead of the machine by blasting it out with explosive and removing the coal by hand. This allowed them space to pull off the head, remove the bolts, fix the machine, and put it back together again.
A dumb question--why not excavate a much larger depth around the coal seam, so the miners and equipment fit comfortably inside? It seems like you can make the inside depth the same as ever, even with a thin coal seam (although the amount of energy used, compared to the amount of coal extracted, would be quite high).
Of course, all of this is underground mining. The other approach seems to be to scrape off the soil down to the thin seam, then use some sort of heavy equipment to mine the seam from the top. It seems like unless the thin seam is very deep, this is the approach that would be used.
Knowing very little of coal mining, the physics of the problem you present would be similar mass. With gold, metals even oil you have water and chemical separation.Coal is cheap and so much like rock how would you separate the two without great expense?
Gail - If you excavated say 6 ft to get at a 2 ft coal seam this would require the handling of much more material and even getting much more rock out of the mine along with the coal -- not very profitable. You would also have to separate the rock from the coal adding still more expense.
Whatever method used to mine the coal it will be enevitable that some rock is taken from the roof and bottom and rock partings in the coal seam. The rock can be say 30% of the material transported out of the mine. Sometimes the product is sold as raw coal with the rock and all particularly if it is a mine mouth power plant. But this reduces the BTU per lb of the product and introduces difficulties at the power plant and increases shipping costs to transport useless rock by rail or barge to the power plant.
Thus, many mines have preparation plants to separate the rock from the coal. Most preparation processes rely on the difference in specific gravity (weight) between rock and coal. For instance, one method uses a heavy media bath when a water and powered magnatite (iron ore) bath is used to float the coal to the surface of the bath and the rock sinks to the bottom. All processes are not 100% efficient and some rock ends up in the "clean" coal and some coal ends up in the refuse pile with the rock.
Today, the value of the coal has made it economic to introduce more costly preparation methods to recover more coal and put less coal in the refuse pile. In the past this was not the case and old refuse piles have a lot of coal mixed in with the rock. In the coal fields there are lots of unsightly giant refuse piles. It is now economical to set up plants to recover the coal in these piles particularly after the federal govmt introduced tax incentives for this.
HO - perhaps a presentation on coal handling and preparation would be in order.
edited to add following paragraphs
Whenever it is more economic stripping the overburden over the coal seam is done rather than deep mining. The depth of the over burden vs the coal seam height is the main item in the economics. The price of coal in recent years has increased the depth of overburden that can be removed. In WVA nowadays whole mountaintops are removed and the soil and rock pushed into the valleys. As you can imagine this creates mucho environmental concerns and causes a lot of friction between the folks who live close by, the mining companies and the locals who are employed by the surface mines in relatively high paying jobs.
Recent court rulings and the federal govmt will make it more difficult or create an outright ban on this method of mountaintop removal. Like offshore oil drilling a conflict between our needs for energy and the environment.
In the Yorkshire and Nottinghamshire coalfields there was a lot of coal mixed into the 'pit tips'. I recall that some caught fire due to spontaneous combustion. There was 'burning tip' at Kiveton Colliery and Manton nr Worksop. Probably many others to. There was a nasty sulphurous tang in the air near them.
During the '84 miners strike the pit tips were worked over by the miners for coal during the bitterly cold winter (which also happened in the 1926 miners strike).
On a more general point - there seem to be many developments in coal bed methane extraction in the UK (I'm aware it's been done in the US and Australia), and UCG. This may be a better way of exploiting the many thin seams that were ignored when the miners were working the good quality, thick seams.
Coal bed methane extraction was originally developed to degas the coal seam ahead of mining to decrease the methane released in the mining process and so increase mining safety. At first the methane from degassing was flared to the atmosphere but later the gas collected, conditioned to remove water, oxygen etc and put in pipelines for sale.
There is a continuing problem in places in the US involving dispute over the royalities and proceeds from the sale of the gas where the owner of the coal rights is not the owner of the oil and gas rights and the laws are still evolving in some states in the US. Some folks consider the gas in the coal seam is just part of the gas in the strata around the coal and you have just an ordinary gas well even if you call it coal bed methane.
On exploiting thin seams in other ways see HEADING OUT's post from 2006 on burning coal in place to produce useful energy.
http://www.theoildrum.com/story/2006/3/5/010/09681
I would think the fundamental issue would be the cost. As in oil drilling, marginal deposits, or those which are in more geologically difficult terrain will inherently cost more to extract. In this scenario, extracting more unusable rock will inherently increase the cost to the point where coal ceases to be an economically viable energy source, as the extra effort expended on mining unmarketable rock, and then disposing of the tailings, would push the cost of coal to a point where more expensive options for generating electricity become economically viable and coal is phased-out.
Having said that, I'm not one of those who has a blind faith in the market to solve all things, but I do believe we're in a period where the economic pressures on our current fuel sources will start to manifest themselves in more private investment in renewables and nuclear technologies, as they already have in the expansion of the global wind energy industry (albeit with the aid of favorable tax climates) and an expansion of private R & D in solar technologies.
This doesn't imply that the rising costs of fossil fuel extraction won't spell economic calamity, but I think there will be a lot of carbon left in the ground by the time we reach a point where we can no longer economically sustain the consumption of fossil fuels.
It's fundamentally an economic problem, but in either way we're still looking at a future where energy is substantially more expensive than it has been in the past, but I think the economics behind fossil fuels will work against them and we'll see a market-driven transition take place at a pace faster than most of us can anticipate.
As the world becomes increases poor there simply
isn't the money available to invest in this
transition.
You must mean resources, since money can alway be created if it is the hold-up.
If the "world becomes poorer", that tends to suggest that unemployed labor and productive equipment will be available, so the bottleneck would be natural resources ...
... though a long term project to invest in an increased harvest of natural resources would seem to be the one thing that is not does not hit that bottleneck, as long as the EROI is at a gross 300% or higher.
I suppose that depends on what you define as being necessary and how you define poverty. We might have to make do with much less "stuff", but there's a lot of economic activity now that would just end up being redirected to other tasks. It really depends on your definition of prosperity. We can probably have a future where we all have more free time, enough food, shelter, clean water, and basic necessities. But you can't have a future where we can all have whatever we want, so long as we can pay for it. The world just can't support that level of consumption.
To use an analogy of mortal sins: There isn't enough to support Gluttony, but there's enough to support Sloth. Our current economic paradigm just doesn't allow for that.
The issue isn't whether or not we have the time, manpower, and savvy to make this transition, it's if our current economic order is compatible with a zero-growth world.
But that's just my two cents. When I said it's fundamentally an economic problem, you can interpret that to mean that there's a fundamental problem with economics.
HO: thanks for the post!
Many thanks yet again Heading Out for your Sunday essay on underground coal mining.
Myself, I would rather the coal be extracted from an underground pit than from tearing the surface apart in an open cast scheme. Is it not possible these days to mine underground using robotic machines rather than sending humans down the pit?
Heading Out,
I want to add my thanks to beagle's.I always read your posts but since I know almost nothing about mining coal , I rarely comment.
But today I have a question.It seems that the two biggest safety roblems in mining coal by far are cave ins and fires.
Is anybody working along the lines of flooding dangerous mines with co2 or oxygen depleted air or maybe nitrogen and either having the miners wear air packs similar to modern scuba gear or else use air lines and suits or suits and helmits similar to the ones once commonly used by underwater workers?
It would be easy to produce such gases or mixtures at or very near the mine by burning some coal in a small generating plant,perhaps even one that breaks down into truck transportable components , capturing the exhaust, while aloso also providing electric power for the mine itself.
Considering how fast other technologies have developed, it also seems that maybe mining machinery can be economically operated by a combination of wired and wireless remote control before too much longer-the wires extending close enough for wireless routers to be used to link to the machines.