Other Methods of Breaking Rock
Posted by Heading Out on August 23, 2009 - 11:21am
I thought that this week we would expand the horizon of these talks a little, and talk about the general philosophy of breaking rock, since the extraction of fossil fuel requires more than just the drilling of holes. I’m going to give a couple of further examples of the benefits of breaking rock out into big bits, and then I’ll describe some of the more exotic methods that have been tried.
For those who are just passing through, on Sundays I post on some technical aspect of the extraction of fossil fuels, so that those of us that are concerned about their future declining production can understand some of the issues that are involved in extraction. One can find a list of recent posts by clicking on "Tech Talk" at the top of the Oil Drum entry screen, or by clicking on this link tech talk. The last post was on Energy Costs in Drilling, which was meant to leave you with the conclusion that the bigger (in general) you can break the rock out in pieces, then the more efficient it will be. So let me give a couple of examples of this. The first is in mining blocks of limestone in Indiana, and the second quarrying granite (perhaps for Paradise) in Sardinia.
In both cases there is a market for the large pieces that are produced, and thus the alternate advantages of just drilling lots of holes, partially filling them with explosive, and then breaking the rock out into a lot of small pieces is offset by the sales price of the end product. So say you wanted to mine these large pieces, you could take an extra-large chain saw, and cut a set of horizontal slices into the face of the rock at the end of the tunnel.
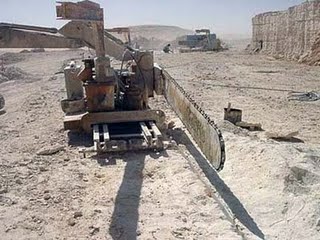
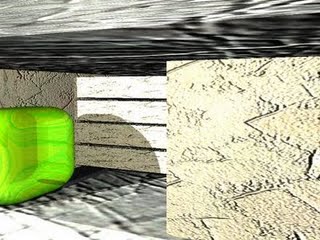
Once the slots are made then an air bag is placed in the top slot and inflated, it applies pressure over the full slab surface, so that the force on the top slab is enough to break it loose and it drops on the one below it. Under the shock load this also collapses down onto the one beneath, and so on, until all four slabs sit, one on the other. The can then be dragged out of the mine, and cut into shape, perhaps for replacement parts for Washington Cathedral.
An alternate approach that is used in surface granite quarrying is to drill a series of long vertical holes parallel to one another and perhaps 3 ft back from the face of the quarry wall. These are perhaps 4.5 ft apart, and might be drilled down some 30 ft. The holes are then filled with black powder (less powerful than conventional blasting dynamite) and simultaneously fired. The blast runs a crack along the back of the slab outlined by the drill holes, and then the powder has enough power to tilt that slab over so that it falls into the open quarry. There are two thoughts on what it falls on. Some quarries let it fall on the solid rock, on the idea that if there are weakness planes in the granite then it is good to know this early – others drop the slab onto a mound of dirt, in order not to break it into pieces, and thus get more useful rock out of the slab.
More often, however, when we are breaking rock we aren’t concerned so much with the condition of the rock after we remove it, we just want to get it out of the way, either so that we can take it somewhere else to process, or to leave the space so that it can be used for something else (such as a subway tunnel).
Some years ago the National Science Foundation funded a program that looked at a variety of possible new ways to drill through rock. They funded a number of different concepts through a trial, and this gave us some measurements of the relative energy cost and practicality. While I don’t have time to go through these in any detail, I thought I might put up a picture and a short comment about some of them. Essentially, as Bill Maurer showed some years ago rock can be broken either by thermal means, mechanical fracture or by applying a variety of chemicals. Starting therefore with thermal, there are three different ways to do this: spalling the rock, melting the rock, or vaporizing the rock. Thermal lances have been used to cut the initial trenches in granite quarries for decades.
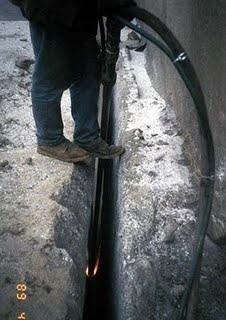
This technique is quite loud (over 140 db) since the flame at the end is the equivalent of a small jet engine burning kerosene and air to heat the rock to over 1400 deg C. The flame heats the rock to a temperature where the quartz changes phase, and rapidly expands, breaking off very small chips (as mentioned in the Energy Costs in Drilling post) which can also become airborne and thus a possible respirable hazard.
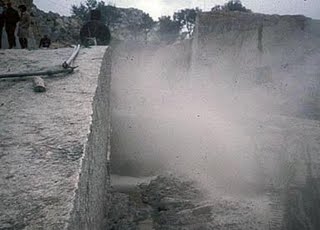
If you were using this to drive a tunnel then you would likely need to wear a substantial amount of protective equipment.
Now you can put more energy into the rock, so that it doesn’t spall (and some won’t any way) but putting more energy in does make a change. In the first case you have molten rock to deal with. A number of folk have looked at that, using different sources as a way of generating the heat. Techniques have included using electric arcs and a plasma.
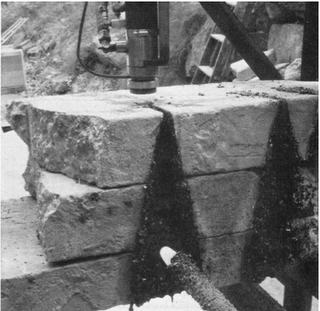
If that wasn’t powerful enough there were several further steps that were tried – the first was electron beams (this was a GE favorite)
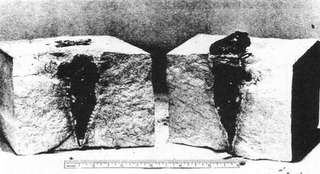
Of course electron beams also generate other things, and apart from dealing with molten rock, dealing with those other issues would have made a tunneling machine that was about 360 ft long. So while it got a glance it did not get an embrace.
Lasers were also tried – they have a little problem of access (although later we thought to use a waterjet as a wave guide) through the mud and while they could vaporize the water in a crack, thereby breaking off quite large chunks of rock, in what is more of a mechanical application, they were also tried to see if they could spall, melt or vaporize rock where they were less efficient.

Although this is still receiving some interest there is a problem with all the techniques that I have mentioned so far that require heat, and that is the amount of energy that they have to use to cut the rock.
We measure the energy that is put into the rock to make a hole in joules, and the volume of rock removed in cubic cm (cc) – If you give a skilled miner a pick and a coal face, he can pull off lumps of coal with a specific energy of around 4 joules/cc. (But they will be rather large). A conventional tri-cone type of rock drill can drill at somewhere around 120 joules/cc, so where do these fit?
Plasma jet – between 133,000 and 220,000 joules/cc
Electron beams – 2,980 to 15,700 joules/cc
Laser beams – from 1,600 to 4,820 joules/cc
Now it is true that all these tests were in harder rock (granites and basalts) than conventional drills normally penetrate, but I can still show you techniques that in even those rocks keep the numbers down by keeping the fragment size up. But before I get around to mechanical fragmentation let me add one more thermal tool, that has an advantage that might overcome the previous problems in such a way as to justify use.
This was the Subterrene, invented at Los Alamos, so naturally it was powered by a small nuclear reactor. The power from the reactor is fed to a ceramic tip on the drill, which melts the rock ahead of it, and then (this is the clever bit) the molten rock is squeezed into the surrounding rock by the thrust of the bit as it keeps moving forward.
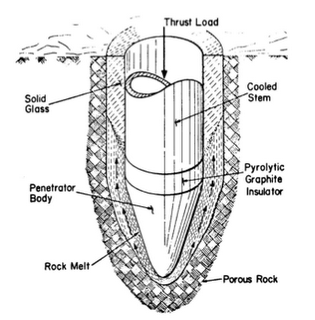
Now you might be a little cynical about this but a) here is a hole punched through a rock with the technique:
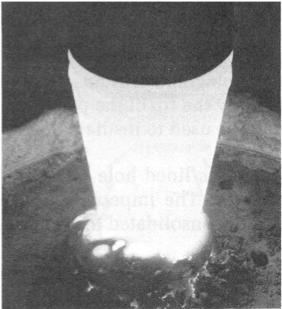
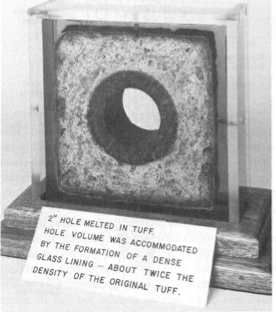
And b) the irritating thing is that I remember that the conventional tool was used to run some underground pipes for one of the local pueblos, with the refrozen rock providing the impermeable liner that was required for the pipe. I thought that it was written up in National Geographic – but alas I can’t find the references that I once had. Nor could other folk, because when we tried to get information about it for a possible use in drilling on Mars, a lot of the original information seemed to have been lost over the years.
Going on to mechanical and chemical means, you can drill and drive tunnels using explosives but no conventional drilling – you use the explosive to drive small holes ahead of the face that are the location of the next round:
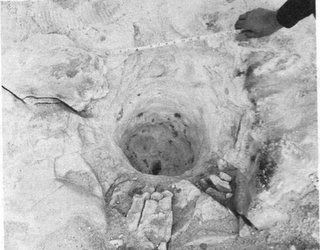
Dr George Clark actually drove one of our drifts at the Experimental Mine (that later became the WOMBAT hole) using this idea, and got the tunnel in about four rounds or so.
But the one that I want to finish with is this:

Yes! That is a portable howitzer firing a round to drive a tunnel (REAM after Lundquist)
And for all those who are amused – it did actually drive quite a deep tunnel, and quite efficiently (energy wise) – though there were some issues we don’t need to cover in regard to how best to use it. The tunnel was in granodiorite, and as you can see, was of quite a decent size.
Well those are some of the ideas that were tried in the past. Lasers haven’t gone away, nor have waterjet drills (of which I may write more in the future). But on a slow Sunday, perhaps this indicates that we really have tried to find other ways of drilling, and that it isn’t quite as easy to find something better than ol’ man Hughes bit (but there are some things that are!)
As usual this has, of necessity, been a simplified review of what was a rather complex series of tests by some highly intelligent folk. If I have been a little glib in the summary I trust they will either forgive me or comment.
Thanks for another educational post on something that most of us don't know much about.
I take it that when we get oil or natural gas or coal, drilling (or the equivalent) is a fairly significant part of the cost of extraction. And perhaps the reason that coal tends to be so much cheaper than other fuel is that it can often be obtained by surface blasting (and picking up the pieces), after removing a some overburden. Underground mining for coal would seem likely to require considerably more energy (or at least more expensive energy) than surface mining.
Thanks, Gail.
Coal is actually a special case since it quite easily can be broken to existing free faces - there are, for example, hydraulic mines in New Zealand where the coal is just washed out by a pressurized water stream. There used to be one in Canada also where two men mined, on average, about 3,000 tons of coal a day for about ten years. It was one of the safest mines in Canada, and the water also carried the coal out of the mine during the earlier years.
Thanks HO for another nice explanation of the state of the art...
The key to energy efficiency in breaking things is to concentrate the applied energy in space and time. Somewhere recently I read an article on femtosecond lasers, which can "vaporize" extremely small volumes of material. They can create, for example, 3D designs inside a diamond. The same energy applied over a longer time or larger volume would merely heat the material slightly without doing any damage.
Femto second lasers can control the energy input sufficiently that they can also cut into explosive charges, without setting them off. But they still require lots of energy because of the inherent demand from the target material for that level to achieve vaporization.
The same principle goes for other methods of cutting as well. Garden hose vs. ultrahigh-pressure jet for example. And of course, the energy calculation has to include the support hardware, so the femtosecond laser that puts out a microscopic pulse might need several kilowatts' worth of electronics to support it.
Wow, I didn't know that about cutting into explosive charges :-o I think I'd want to wear safety glasses for that experiment, though. And stand behind the barrier.
I've only ever seen the laser cut explosive on video - grin! (but we also washed out missiles from behind concrete walls).
Heading Out -
As to the subject of how much energy is consumed in drilling oil and gas wells, I realize that it mainly depends on i) the depth of the well, ii) the diameter of the well, and iii) the type of rock one is going through.
However, confining the subject to oil wells for now, can you pick a moderately deep well of typical diameter, and a formation that is somewhere between the easiest and most difficult and then come up with an estimate of the amount of energy that went into drilling that hole?
Being that these drill rigs are diesel powered (I would assume), what would be a typical size for such engines in terms of rated horsepower? I would think that once one has that in hand and a typical drilling rate in terms of feet per hour, then one can come up with the total number of horsepower-hours to drill that hole. And being that a diesel engine has a typical specific fuel consumption in terms of pounds of fuel per horsepower-hour, one should be able to back into the energy consumption per hole in that manner. (In doing this, I think a reasonable assumption might be that the actual average output of the engine is probably something like 80 - 85% of rated power, being that the engine is probably not run at full throttle at all times).
I think the above exercise would give a reasonable ball-park figure that one can either shrink or expand, depending on whether the formation is easier or more difficult.
Sound reasonable?
Can I get there when I get up to the drill rig floor? There are a couple more posts that I want to put in on the way back up out of the hole that include where some of the energy goes and why it has to, before I get there. In doing it that way it makes it easier to show and explain the comprehensive picture.
I have used an expansive concrete, like Dexpan, to control crack rock. It is very effective. Cut out a granite doorway in Maine and trenched out blue stone in Hawaii. It is nice because it is slow, non explosive and does not require large tools. Just a relatively small drill and the product.
We tried using that when we were excavating the rock from what is now the OmniMax Theater under the Arch in St Louis. It is fine for small delicate work, but we had to remove 2,000 cubic yards of rock and it was way too slow, and for those quantities very expensive. It also didn't give us the breakout patterns that I wanted since I wanted to get the large pieces that I showed in the post last week.
We ended up pre-cracking the rock using a Darda Rock Splitter in holes about 18 inches in from the face, and about the same depth, and then growing the cracks to the free face using an impact hammer on a Bobcat. (Each of the three steps, drilling the hole, cracking the rock, and breaking out the lump(s) took about a minute so we could set up a little production team of four people).
Thx again HO - for widening my horizon on these topics and as you mention , I agree, Hughes drillbit (in conjunction with mud) is "the king of the pack" . Hughes should be embedded of our bedtime prayer.
Most of them other methods "look and seem" to costly and complicated 10 000 meters down into bedrock - from my rookie neck of the woods.
Those numbers are for the total volume of rock extracted or for the volume extracted by the heat. I mean, if those methods are used like the rock saw at the begining of the article, will the eficiency increase, or those numbers are already for rock saw like usage? By the way, what is the eficiency of that saw?
If I understand everything here correctly (I'm no expert on that), a saw may be useless for driling oil, but not for coal.
They are for the volume extracted by the heat. So if you were coring (and the Subterrene had a design that would) the central section of the rock could be extracted without much energy cost, and the overall cost of the excavation would drop accordingly.
This was the premise of the high pressure waterjet drills such as that developed by Flowdril where the jet cut the kerf of the hole, and this released the high confining stress on the central core so that it became easier to fracture into the outer free surface, and ROP increased by the factor of 2 - 4.
If you are using a saw to trench rock, for example, the slot may be 8 ft deep, 14 inches wide (single chain) and use 15 gal/hour of fuel -with the speed controlled by the hardness of the rock. They might, for example, go 1,500 ft in a shift, depending on the horsepower of the machine. That particular example was cutting a trench for a pipeline. Obviously a smaller saw used in a dimension stone quarry would use less power and you gain the reduced energy cost since the inflated air bag then breaks off the four slabs for very little additional energy cost.
Incidentally there is a rock quarry feasibility study available, which gives you some size of the dimension stone market, it is not huge in the United States.
I finally found the Web Page of the saw manufacturer I was looking for - they get 200 sq ft/hour with a machine that is 50 - 75 hp in size.
Hope this helps.
Thanks, that answer them all.
These techniques apply to dimension stone or ornamental stone not so much bulk ores. Incidentally a friend of mine is getting a 24" diamond circular saw to cut slabs out of petrified wood, fossil marble and the like.
This series will hit the nail on the head when it gets to reduced energy blasting. In open cut mining the preferred explosive is ANFO where ammonium nitrate is made from natural gas and fuel oil/diesel is made from crude oil. What will we use for explosives when there are no fossil fuels?
Well we could always go back to gunpowder (grin).
Being the sort of rolling stone for about thirty years that stopped here and there as circumstances and chance dictated,I drove a giant Catepillar truck on a "rock job" once -the construction of I77 off the crest of the Blue Ridge mountians.
If the truck broke down I had to help the "powder monkeys" dump the anfo into the holes bored on about a ten foot grid about twelve to fifteen feet deep over an acre or so at a time.Into the bottom of the hole first went a large armload of dynamite sticks about three inches in diameter and maybe 16 to 18 inches long,IIrc about six to eight sticks per hole.The last stick had a cap and wires attached ,the ends were placed under a shovel of dirt or a rock temporarily.
The holes were bored mostly with truck mounted drills very similar to the ones used to bore water wells and probably were eight inches to ten inches in diameter.If the ground was too rough for the trucks,a drill driven by compressed air supplied with a long hose was used,the drill being equipped with dozer style tracks and air motors to move itself around.The air came from a nearby truck mounted compressor of course.
Then the anfo went in out of a spout on the delivery truck similar to the spout on a concrete truck but much smaller of course.
Then you had to shovel the hole full of small rocks and gravel.
And THEN you got a break on Vecellio and Grogans time,all equipment was driven at least a quarter of a mile away and the powder crew tied all the wires together and set off the "shot."
It didn't make much noise-a really big suprise to newcomers- at all but you could really feel the earth move.If the shot went well the largest pieces of stone were small enough to load and haul ,probably about fifteen tons or so.The trucks normally hauled fifty tons but were customarily overloaded and we usually hauled sixty or sixty five tons.About the only way you can hurt a Catepillar truck is to drive it over a cliff or ignore the routine maintainence.
Production minded supervisors LIKE to see then go airborne on rough roads but the safety men in more recent times fail to see the beauty and excitement of the Cat versus Volvo versus Terex dump truck motocross.
You definitely got your butt out of the truck when such a boulder was dropped into it ,or you would suffer some bruises from bouncing around in the cab.
I wish had kept a diary sometimes.
The slowest dozer operator was named -what else-"Lightning"- and the best operator "Lady Fingers " because he refused to run a Cat dozer when his International broke down-said the controls of the Cats were too crude and caused him to grow calluses on his hands.He got away with it both because his brother was the super and he had many years of seniority.
Thanks for the informative article, HO. I've got a question you might be able to help with on the topic of energy cost of rock excavation.
I've heard that one of the hazards of deep mining operations is "rock showers". At least I think that's the term I recall. At great depths, the rock all around the excavation is under tremendous compressive stress. Apparently, when miners start to drill the rock face for placing explosives, sometimes rock sprays out from the face on its own, driven by the compressive strain that it's under.
Has there been any work that you know of on trying to exploit that effect in a controlled manner? It seems like it has the potential to achieve very rapid excavation in deep tunnels. Can you think of any reason why it wouldn't be feasible?
Obvious application: deep reservoirs for pumped hydroelectric energy storage.
Generally it is called a rock burst when it occurs in most rock, but a coal "bump" when it occurs with coal.
It is a generally a very dangerous thing, since it can happen without a lot of warning and can be very violent - a rock burst in Merkers Germany was recorded in Constantinople on one occasion.
It generally occurs when the stress in the rock exceeds its strength, and can involve large volumes of rock, since as one bit fails it transfers load to the adjacent rock. Generally miners try to ameliorate the situation since it is so dangerous - but when they fire a round in some of the deeper mines in South Africa it can trigger bursts that bring down additional rock - its just that it isn't usually in the vein.
When it occurs with coal - often anthracite - the coal can fragment and flow some distance and this can be fatal to anyone close.
The subject of energy costs in mining and indirect CO2 is coming to the boil with the Olympic Dam expansion in Australia. A green tinged criticism is here
http://www.onlineopinion.com.au/view.asp?article=9332
Note they will throw away 8,000 tonnes a year of truck tyres. The whole dig is reckoned to use 15 billion litres of diesel. Since it is arguably driven more by uranium demand than the associated copper and gold it gives credence to claims of major CO2 in the nuclear fuel cycle. I don't see how the company (BHP Billiton) can claim it can use 60% low carbon energy unless it employs the offset scam.
Heading Out
I have been reading these posts with a grin as I have been dismantaling an internal 1930's chimney in my house.
Lots of old, really good and set up, concrete and some even older recycled bricks. Taking that chimney apart without destroying my equally old plaster walls has been an interesting challenge.
The best approach by far is an old steel chisel and a rock hammer. Careful placement of the chisel and the right tap "wedges" apart the chimney better than anything else. Knowing where to hit and at what angle is more important than the amount of energy used.
Granted it isn't the fastest approach but from an energy standpoint it takes very litlle energy to make a pile of rubble.
I think sometimes that it is our need for speed that sometimes discounts the most energy efficient way to do things.
Keeps the posts going - they are great fun to read.
Thanks! The hammer and chisel and the right amount of force through the hammer, and then the right amount of twist on each impact are why older miners can often out-perform the young "football player" types of student who hits the chisel several times with much greater force, before trying to turn it.
I did an energy calculation once on the old hand-won longwalls and the energy of 15 miners loading off that coal was much less than the machines that replaced them. But they weren't nearly as fast.
I like your style dude,
Its completely my pleasure for comment this post.
The Sports HQ - Golf source for golf clubs and golf equipment. Also get golf sets complete package.
I like your style dude,
Its completely my pleasure for comment this post.
The Sports HQ - Golf source for golf clubs and golf equipment. Also get golf sets complete package.