Back to Basics: Direct Hydropower
Posted by Rembrandt on August 26, 2013 - 1:20am
This is a final guest post of Kris de Decker, founder and writer at Low-tech Magazine, an internet publication highlighting the need for elegant yet simple sustainable energy technologies. We published a number of most interesting in-depth energy articles before from Kris about a-typical energy topics including 1) Endless Rope Drives, 2) Small urban wind turbine performance, 3) Heating and Cooling cities without fossil fuels, 4) Fossil Fuel Use in pre-industrial times, 5) solar powered factories for industrial production, 6) Trolley Canal Boats, and 7) The extensive history of windmills. Kris has been sad to hear that The Oil Drum will end its journey, and provides his final contribution on hydropower as a mechanical form of energy, as opposed to hydro-power as a conversion from kinetic to electrical energy, which shapes our conception today when discussing this energy source.
All hydropower plants today produce electricity. Transforming energy to electricity seems to be the only way to harness water power, but it is not. For almost two thousand years, water wheels powered machines directly via mechanical transmission.
Some small direct hydro powered systems in South America present a strong case for combining the use of modern materials with old fashioned methods of water power mechanization.
The higher efficiency of this approach means that less water is needed to produce a given amount of energy. This lowers the cost of hydropower and enables power to be produced by the use of very small streams.

Throughout the course of history, the efficiency of water powered prime movers has steadily increased. Wooden water wheels, which appeared more than 2,000 years ago, converted a relatively small amount of water energy into mechanical power: The efficiency was 5 to 15% for an horizontal water wheel, 20 to 30% for a vertical undershot water wheel, and 50 to 60% for a vertical overshot water wheel. [1]
Iron water wheels, which appeared in the late 18th century, had improved the efficiency rating of the vertical overshot wheel to 65 to 85%. [1] Water turbines, which were developed in the 19th century, and which are the water-powered prime movers that we still use today, generally convert over 85% of the kinetic energy inherent to the water source into mechanical power at the shaft of the turbine. [2] Water turbines are ten to twenty times more compact than water wheels for the same power output, an advantage that led to much cheaper and much more powerful prime movers. Turbines are more widely applicable than water wheels, because water wheels could not make efficient use of any head of water (the vertical distance travelled by the water) much greater than their own diameter. [1]
Why Modern Hydro Power is Less Efficient
In spite of these significant improvements, hydropower installations today are actually less efficient than those from earlier centuries. The culprit is electricity. Not long after the introduction of the water turbine, another change occured: Instead of using water-powered prime movers to run machinery directly (as had been the case for centuries), water turbines were (and still are) used to generate electricity. This modern approach has introduced an energy deficit that has nullified any progress behind hydropower design efficiency.
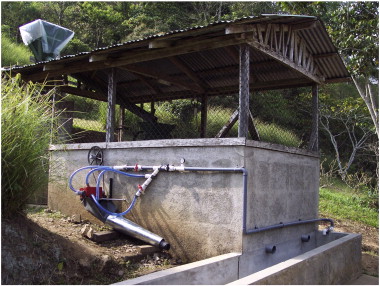
In a modern hydropower installation, a water turbine converts the energy in the moving water into rotational energy at its shaft, which is then converted into electrical energy by the generator that is coupled to the turbine. Next, the electrical energy is converted back into rotational energy by the electric motor of the machine that is being powered. Every energy conversion introduces energy loss. This loss of energy occurs due to friction, which is observable as heat, vibration and noise. Friction occurs at all levels of electrical transmission: In the turbine, the generator, and the motor. Additional components such as batteries, drive systems and inverters can further increase efficiency losses.
It is possible to calculate the efficiency rating for each modern hydropower unit by measuring the difference between turbine input and electric generator output. A home-sized hydropower plant generating AC electric power has a "water-to-wire" energy transfer of at best 60 to 70 percent. [3] Smaller DC electric systems, which require inverters and generally have battery banks, have lower efficiencies of 40 to 60 percent. [3]
Energy loss in the electric motors of the devices being powered is not included but should also be considered ("water-to-motor" efficiency). The efficacy of an electric motor can vary wildly - from less than 60% for small motors to more than 95% for large motors. On average, a hydro-electric power installation only converts about half of the energy available in water into useful work.
This means that a small, modern hydropower plant has a similar efficiency rating to a centuries old configuration using a wooden vertical overshot water wheel (50-60%), and that this modern counterpart is considerably less efficient than the iron water wheels of the 18th century (65-85%). In an old fashioned hydropower installation, there was only one conversion of energy; A water wheel converted the energy inherent to the water source into rotational energy at its shaft. The same shaft also moved the machinery, so that the only source of significant energy loss occured in the water wheel itself. [4]
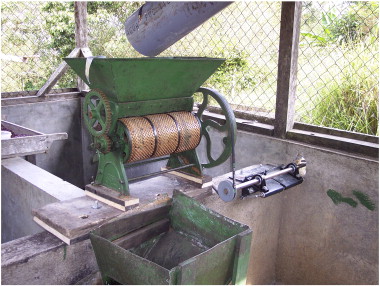
Note that this is not the total efficiency of the hydropower installation: friction also occurs in the pipeline that feeds the water to the turbine. Most small hydropower systems don't use dams. Instead, they divert a fraction of the water of a stream downhill through a pipe. The energy losses in the pipeline are the same for hydroelectric and direct hydropower installations. Therefore, for the purposes of our comparison, these power losses can be overlooked.
Why Direct Hydropower Makes Sense
There is one possible hydropower configuration in particular that deserves considerable attention: a water turbine directly powering machinery, without the intermediate step of generating electricity. Depending on the type of turbine used in such a system, the value that corresponds to the "water-to-motor" efficiency is roughly 80 to 95%. The implementation of this form of direct hydropower doubles the effectiveness of a small scale electric hydropower installation. [4]
The higher efficiency of direct hydropower brings important advantages. If the intermediate step of generating electricity is bypassed, considerably more power can be gathered and utilized from a given head (the vertical distance travelled by the water) and water flow rate (the amount of water that runs down a stream). This advantage can be used to increase the energy production of an existing water power site. It also means that more potential water power sites become available, and that relatively small streams and rivers can be shared by several hydropower units.
Because of its higher efficiency a direct hydropower system is also cheaper than a hydroelectric power system. Less water is needed to produce a given amount of power, which means that all components of the installation are reduced in size, cost, and other resources. For instance, less civil engineering is required. Water can be carried to the turbine by low cost, low pressure, easily transportable, flexible, plastic tubes that are small in diameter as opposed to the rigid, large diameter penstocks common to electric hydropower plants. The flexible connections between the pressure pipe and turbine also simplify installation.
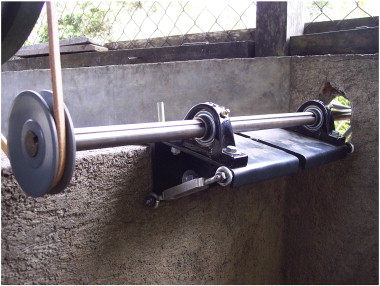
Last but not least, the higher efficiency of direct hydropower limits the ecological impact of a water power site. Maintaining enough water in the power source for aquatic life to thrive is a cornerstone of environmentally sound microhydropower production. This type of ecological sustainability is easier to achieve with direct hydropower because less water is required.
Old-School Approach, Modern Materials
Many NGO's are introducing small hydropower systems in the developing world. Almost all of them are aimed at the production of electricity. However, there are a few exceptions to this standard practice. In 2007, a team from the Appalachian University in the US designed, built and installed a direct hydropowered coffee depulper in Nicaragua. According to a recent study in Energy for sustainable development, it has "performed flawlessly through five harvests". [5]
Much of the necessary energy for coffee harvesting and processing is provided by manual labour. One of the most tedious, labour intensive steps of coffee bean processing is depulping. In the past, the depulping process was restricted to a hand cranked machine, and would take all night to complete. Now, with the help of direct hydropower technologies, the depulping can be completed in two or three hours.
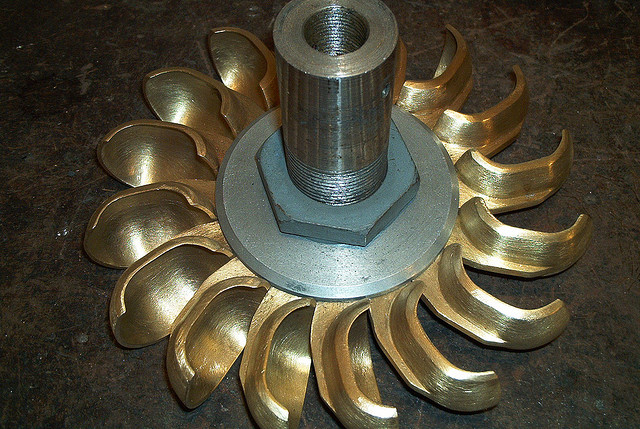
The installation can deliver a maximum of 800 watt mechanical power with a head of 35 m and a water flow of 300 liters per minute. The material costs amounted to just $1900. For comparison, Practical Action states that, when using appropriate technologies, a small scale hydroelectric installation costs $1,800 to $6,000 per installed kilowatt. It takes about two kilowatts of mechanical power to produce one kilowatt of electric power, so that direct hydropower is at least twice as economically viable as a hydroelectric operation with the same rate of energy production.
Precise Control
The turbine used by the direct hydropowered coffee depulper is a commercially available Water Motor model 90 from Campo Nuevo in Bolivia. According to the manufacturer, the compact machine (16 x 16 x 32 cm) is "the only modern turbine designed to drive common machines directly with water power". The turbine uses a 9 cm diameter Turgo type runner, which converts water power into mechanical power at 80 to 85% efficiency. It is suited for moderate to high head systems. The larger model 150 has a 15 cm diameter runner and produces about three times as much power.
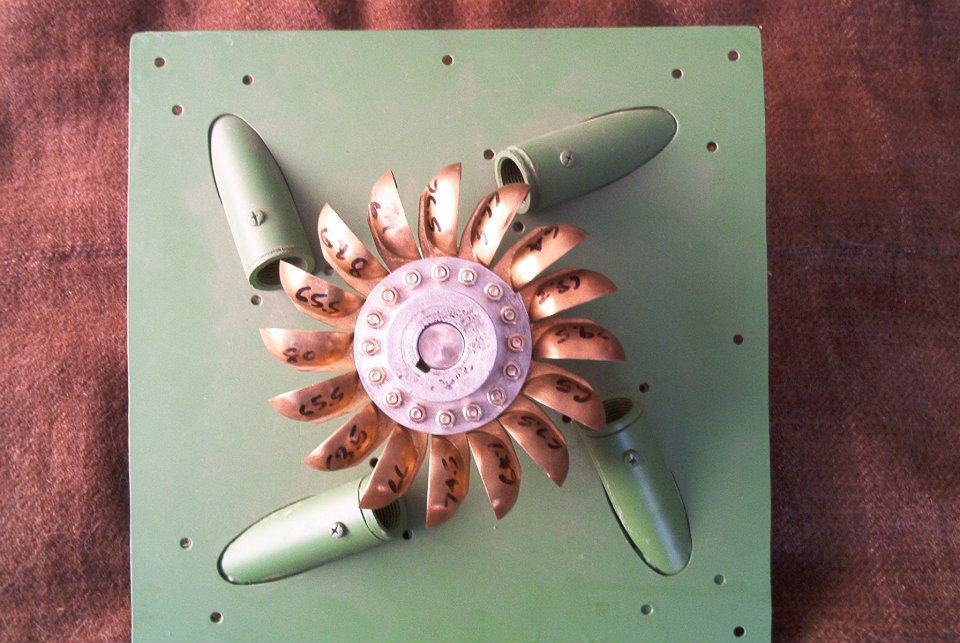
The water motor is as easy to control and adjust as an electric motor. It has a power switch that allows instant on/off control, which makes it practical to directly power machines which must be turned on and off many times during use. The mechanism works by deflection of the water from the runner, so that the force of the flow does not increase the pressure in the penstock.
The power output of the turbine can be precisely adjusted. Like any other turbine of the impulse type, a Turgo runner is driven by high velocity jets of water. A manifold separates the water flow into four smaller tubes, with each stream leading to one of the four jets driving the turbine wheel.
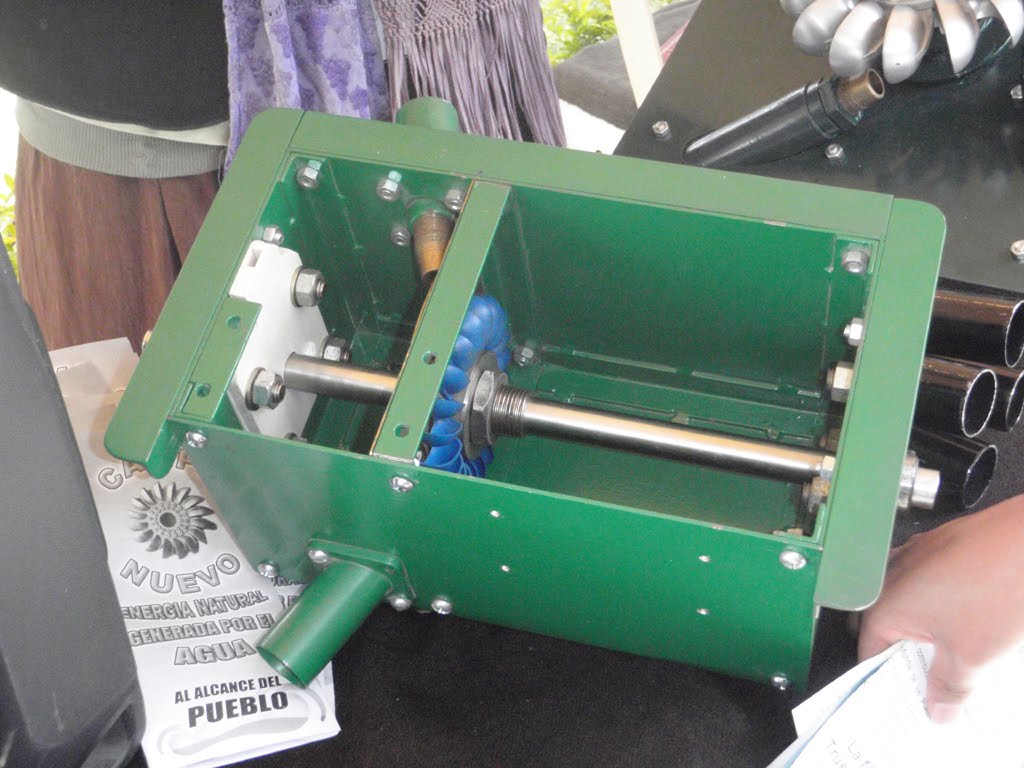
Each of the four nozzles has an individual valve to provide for a range of flows, so that the motor can be run on one to four jets at a time. Furthermore, the jets can be adjusted to various sizes. This mechanism makes it possible to precisely measure and adjust the power output of the motor and cater to seasonal variations in water flow.
Direct Hydropowered Woodworking Unit
At the Campo Nuevo demonstration site in the Andes, the water motor runs a large variety of machines, including a small woodworking unit (table saw, grinder, joiner, drill, abrasive disk), a cement mixer, and a grain mill. When mechanical power is not being used by any of these machines (for instance at night),the motor runs a generator which stores electric energy in batteries for lighting and other purposes. The water motor can also operate an air compressor to run air-powered tools. (In principle, it could also run a compressor from a refrigerator). [6]
The water motor on the demonstration site delivers power similar to a 0.75 horse power (560 watt) electric motor at 1,450 rpm using a stream with a vertical fall of 18 m and an average water flow of 310 liters per minute. These conditions are less than ideal for a hydroelectric power site, but for direct hydropower the situation is perfect.
A small storage tank attached to the direct hydropower unit even makes it possible to temporarily run more powerful machines. Since the operation of the table saw requires 500 liters of water per minute (which is often not available), the 6,000 liter storage tank was installed, measuring 2 x 2 x 1.5 m. It allows the table saw to run for 15 minutes continuously. This additional power output adds up over two hours of operating time over the course of a ten hour workday.
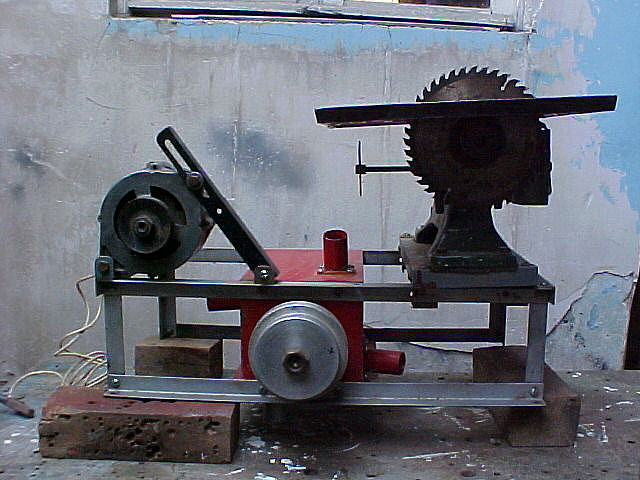
All machines (including the generator and air compressor) are placed directly on or beside the turbine housing. These tools are attachable to (and driven by) the same belt. The water motor can only operate one machine at a time, since there is no distribution of energy. This works well in a workshop, because many tools and machines are used intermittently.
The same configuration is used for the direct hydropowered coffee depulper in Nicaragua, which was described above. Coffee beans are harvested from December through February, and they must be depulped within 24 hours of picking. This processing constraint means that the depulper is only used at night for a small fraction of the year. Therefore, the direct hydropower installation is often available for other applications (such as running a saw, a drill, an air compressor, or an electric generator). Although the turbine that powers the coffee depulper can provide up to 800 watts of mechanical power, the coffee depulper itself uses only one fourth of that waterpower and one jet to deliver 200 watts for its operation.
Upgrading Medieval Water Mills
Will we see a rebirth of direct hydro power? Maybe, but the fact remains that this form of energy production has never disappeared. In some mountainous regions, there are still water wheels in operation that share similar design with the water mills so extensively used in medieval Europe. The rotating shaft directly drives machinery, most commonly found today as grain mills for flour production.
In remote villages in Nepal, many farmers use all wooden traditional water mills to grind grain. About 25,000 to 30,000 of these are still in operation today. In Nepal, the goal is not to reintroduce direct hydropower, but to make sure that it stays. That is why the national NGO Central for Rural Technology Nepal (CRT/N) runs a program to upgrade these mills. The improved water wheels can grind grain more efficiently and have longer lifespans, which allows them to compete better with diesel powered mills.
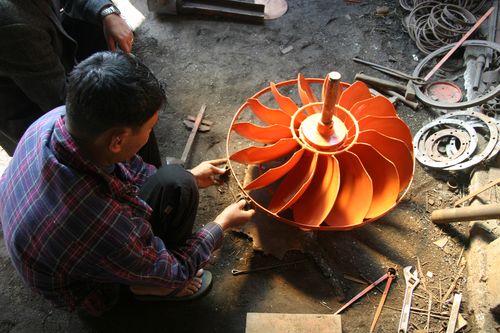
Basically, CRT/N upgrades medieval style water wheels to nineteenth-century style water wheels, by replacing key wooden parts such as the shaft and the runner with locally produced precision metal parts. The wooden penstock that delivers water to the mills is replaced by a high density polyethylene pipe which reduces leakage and other avoidable problems.
CRT/N calls its technology the Improved Water Mill (IWM). Estimates suggest that grinding capacity of the upgraded mills has doubled, which corresponds neatly with the efficiency figures we introduced at the beginning of this article. The higher efficiency makes that less water is needed and that the mills can operate for longer periods of the year.
Replacing Diesel Engines
The NGO has upgraded 5,700 water mills from 1990 to 2009. Some of these upgrades (237 to be precise) also involved adapting water mills so that they can run other machines as well, such as oil presses, rice de-huskers, sawing machines, or an electric generator. To achieve this variability, a longer shaft is installed which disconnects the runner from the millstones. Instead of connecting to the millstones, the grinding shaft operates from the long shaft using a belt drive, allowing other machines to be operated by direct hydropower.
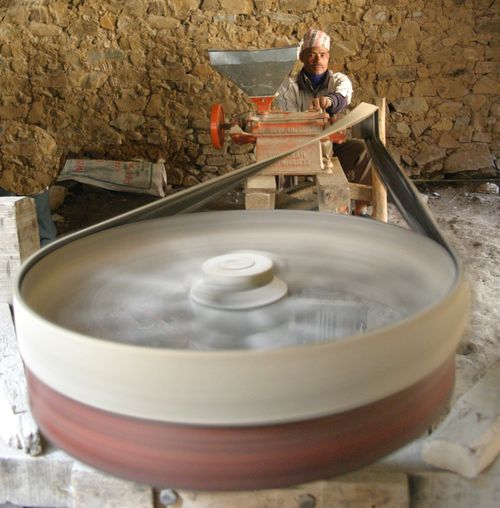
While these upgraded water wheels do not achieve the high efficiency of direct hydropower installations using turbines, they are less expensive. Basic upgrades of a water mill cost $350, whilst the option of running multiple machines brings the total cost at $900 to $1,200. Thus, upgrading a traditional water mill is at least two times cheaper than installing a complete new, turbine driven direct hydropower system. In Nepal, improved water mills have even replaced some diesel powered grain mills, because they are less expensive to run and produce better quality flour.
The water mill upgrade project is still ongoing. Similar but much smaller projects have been implemented by IT Power India, also in the Himalayas (70 upgraded mills at a cost of $200 each), and by SITMo in the Philippines (as part of a mostly electric hydro scheme).
The best of both worlds
This plea for direct hydro does not imply that we should stop using electricity. Some things cannot be powered by mechanical energy, most importantly lighting and electronic equipment. Furthermore, many people in the developing world do not have access to electricity at all, forcing them to use unhealthy kerosene lamps instead.
Rather, the examples described above show that it might be interesting to combine both methods. The best results would be obtained by a hydropower installation that produces mechanical power for operating machines, and stores electric power in batteries for lighting and other purposes when mechanical power is not required (for instance at night). Compared to a strictly mechanical system, it would offer important extra benefits. Compared to a merely electric system, it would deliver more power and be much more efficient.
Water motors can also be used if you don't have a mountain stream running next to your house, farm or factory. That's the topic of an upcoming post. Stay tuned and get updates by email, feed, facebook or twitter.
Kris De Decker (edited by Caylen Cole-Hazel)
Notes & Sources
[1] Stronger than a Hundred Men: A History of the Vertical Water Wheel (Johns Hopkins Studies in the History of Technology), Terry S. Reynolds, 1983. See pages 106, 306-307, and 342-349.
[2] The efficiency of a water turbine depends on the type of turbine used. There are many types of turbines available, and each one is aimed at specific combinations of head and water flow. For small-scale hydro applications, a minimum efficiency of 80-85% can be achieved in any situation. Pelton turbines are up to 90% efficient and large turbines can be over 95% efficient.
[3] Intro to Hydropower, Home Power Magazine, 2012. Another source is the Fact Sheet MicroHydro of Appalachian State University, which gives an average system efficiency of 53% (including energy loss in the pipeline). And a recent study states: "It is common to assume an overall system efficiency of 50–60%. However, in practice actual power output may be as low as 30% of gross input power for very small installations and as high as 70% for larger schemes."
[4] To this should be added the energy loss in the drive train, which is needed to match the rotational speed of the prime mover with that of the machine being powered. This loss has been included in the efficiency results of modern hydro power installations, where a drive system is used to match the rotative speeds of turbine and generator, but not in the results for the old-fashioned installations. The energy loss in the drive train can be quite large, for instance when you would use a slow-turning water wheel to operate an electric generator or a circular sawing machine, which require high rotational speeds and thus elaborate gearing to step up the speed. On the other hand, the energy loss in the drive train can be negligible when a water turbine is used to directly power fast-rotating machinery, because water turbines have much higher rotational velocity than water wheels. This also holds true for water wheels operating machines which do not require high rotational speeds. Turbines operating slow-rotating machines will need gearing to step down the speed. If the connection is made by a single gear, chain or belt, the drive train can be up to 99% efficient.
[5] Design and Construction of a Direct Hydro Powered Coffee Depulper, Energy for Sustainable Development 16 (2012) 401-405. Brian W. Raichle, Raymond S. Sinclair, Jeremy C. Ferrell.
[6] Water Power in the Andes. Yesterday's Solution for Today's Needs, Ron Davis, 1999
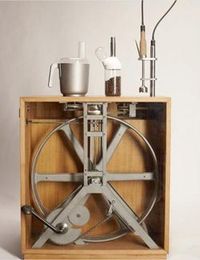
Related articles
The use of direct mechanical energy can also be useful for pedal power and wind power. The use of direct thermal energy can be useful for solar power:
- The bright future of solar thermal powered factories
- Pedal powered farms and factories: the forgotten future of the stationary bicycle
- Bike powered electricity generators are not sustainable
- Wind powered factories: history (and future) of industrial windmills
In some cases, the transmision of power could also be done more efficiently without electricity:
In a developed country there may be a minefield of problems associated with installing a microhydro. These include stream ecology, catchment diversion, rights of way and mains power alternating current issues. On the latter if you want to export 240v 50 Hz AC to the grid you'll need the co-operation of the network owner. They not only get to say whether they want to build the connector and buy the electricity but how much they will pay and their preferred form such as 22kv 3 phase.
Ecology issues could include fish migration and aquatic mammals, in Australia the platypus but maybe beavers and otters in the northern hemisphere. The intake to the penstock should have a grill to exclude such critters, perhaps also with a leaf cleaning mechanism. Getting ecological approval could affect green loans and bonus payments such as renewable energy certificates. The catchment people may insist on a minimum stream flow so weirs or impoundments may be minimal at best.
The power formula is a litre of water falling one metre per second is 9.8 watts maximum. A cubic metre (1000L) of water falling one metre is 9.8 kw falling two metres is 19.6 kw and so on. A practical kinetic to electrical efficiency is about 70%. That needs a generous diameter penstock (ie not restrictive) with a head (vertical drop) of at least 10 metres connecting to an efficient generator. The generators I've seen near home are vertical axis 2 nozzle turgo style turbines driving a 3 pole induction generator at 1500 rpm with the water flow controlled by needle valve.
What do I think of micro hydro? It's cute but it will never make a dent in coal fired generation.
Almost all hydro projects are ecosystem killers.
One needs to really look at the feedback loops, and not get too anthropocentric.
Compared to coal, oil-n-gas or (Gen I-III) nuclear, it's practically zero impact. Nothing is perfect, but if intelligent ecological compromises are made in the design (salmon runs, etc.), hydro can be very low impact ideed. I'd rather take 10 dams before 1 coal plant near my city.
I agree - in principle.
But in the "real world" defined by anthropocentrism, the choice is between bad- as in hydropower- and MUCH WORSE - as in burning that much more coal that much faster and the destruction that will come from stripping the land of trees, etc, to replace electricity with wood for cooking and heating.
When there is less irrigation water, the local people who would otherwise depend on it will necessarily clear that much more of any remaining unfarmed land of whatever natural cover remains in a desperate effort to eat.
It appears we are in a damned if we do situation down the road in respect to expanded hydro, and a damned right now situation if we don't go with more of it.
It's heartbreaking, but it is extremely likely that most of the world's remaining free river will dammed unless overshoot outruns the availability of big biz and big govt to raise the necessary capital.
I'm afraid the bitter truth is such that the damming of the remaining large, free rivers which have considerable hydro and irrigation potential is a foregone conclusion.
Given the hard , hard choices available, in terms of the truly big picture, it might be making the best of a bad situation to face up to this reality, and instead of trying to stop hydro , try to extract as many concessions from govt and developers as possible- concessions structured to preserve some smaller watersheds with the greatest potential as biological preserves and to lock in the best possible water management practices where the rivers are dammed.
A well managed river used for hydro is not a total loss from an ecological pov- there can still be a lot of value remaining, depending on the choices made.
Probably the greatest stroke of luck we could have, as a species, would be for Mother Nature's genetic random event generator to crank out a highly contagious virus with a long incubation period (so it would have spread everywhere by the time the alarm is raised) which would permanently sterilize a very high percentage of us.
She cranks out lots of them- ask any farmer .
I wouldn't be very surprised to live long enough to see a pandemic disaster comparable to the plague that wiped out half of the people in some towns during the middle ages.
We know how to stop the spread of such a disease, but the world is now so interconnected it might prove impossible to contain it if a highly communicable plague ever once got a good start .
Even if the usual control measure- containment thru quarantine- works, there are enough people around eager to make trouble - and technically sophisticated enough to m to do it- to spread it deliberately.
It would be very easy for instance to deliberately infect a person cleared for travel to this country at the last possible minute- on the ride to the airport.
Thanks for all the interesting and thought-provoking articles over the years, Kris.
While direct hydro has its place, I think you are underestimating the efficiency of hydroelectric. One of the main advantages is indirect; electricity can be efficiently moved large distances, while stuff to be processed, like coffee, is harder to move, so you waste a lot of energy in transportation.
The choice between direct and electric will likely be determined by the amount of power available in the stream/river. For small amounts of power, the cost of the electricity connections will likely be too high. For high amounts of available power, it is not practical to use it all directly on site.
Here is my Micro-hydro experiment;
http://imgur.com/oGFaL0e
Best I can get in the currents that I am able to navigate in is around 150 watts.
Thats because the system is optimized for powering not generating.
I really like the the idea of direct mechanical powering. Maybe I will install a mill in the cabin of the boat.
Cheers!
If one should like to use energy efficiently and economically, it is best to take the shape of that energy into account. Thermal energy is most efficient at heating stuff up; transforming it into movement or electricity incurs a loss. Kinetic energy, on the other hand is most efficient when used to directly move things, which is why pedal power is feasible for lathes and stitching machines.
Electricity shines at providing light and running electronics, does ok at running motors, but it is really bad at heating stuff.
A complete and efficient energy system, which would still allow a 'modern' lifestyle, should concentrate on using kinetic energy to do kinetic stuff, thermal energy to do thermal stuff, and have enough left to generate electricity for lighting an electronics and the occasional motor.
So the sun should be used for heating, the wind for milling and sailing, and pedals for moving stuff, and any surplus energy should be used to generate electricity for storage in batteries.
This may seem bleak, but I think Spock would approve.
"Electricity shines at providing light and running electronics, does ok at running motors, but it is really bad at heating stuff."
Actually, electric resistance heating is near 100% efficient; virtually all of the electrical energy gets converted to heat. How that electricity is produced is a different matter, and there are many other high value uses for electricity, most of which can't be easily substituted for.
Many micro-hydro generators use electric resistance heaters as dump loads for regulating output, either heating water for other uses or dumping heat into the outlet stream. I dump surplus PV into a hot water tank for our domestic use (I just heard the relay click, meaning our batteries are near full capacity). If I had enough hydro potential, I certainly would be using it to charge batteries and heat our water.
One direct use of hydro power is to pump a lesser portion of water up hill or over distances. The simplest device for this is probably the "tramp", but I saw a system that uses a small belt-driven pump powered by a pelton wheel turbine to move clear spring water over a ridge for domestic use and irrigation. Much simpler/cheaper than using an electric pump powered by an alternator.
Not sure what a tramp is, we use one of these for stock water
http://en.wikipedia.org/wiki/Water_ram
WATER RAM COLLECTOR
You know these things much better than I do, I'm sure. I'm no engineer.
My experience is this : I used to have a 10 ampère limiter on my meter. Great for lights, 2 computers and the fridge. But the washing machine trying to heat water to 30% celsius tripped the security within seconds. Spinning the drum at high speed was no problem, heating water asked for too much. I had to shut down an electric water heater, it would trip the security at each use of warm water. And the drip drip coffee machine was impossible to use.
I'm sure you're right in stating that electricity to heat is very efficient, but I know for a fact that a little bit of heating takes a lot more juice than turning a washing machine drum. Which is why I try to avoid using electricity for heating.
Ask someone with a ground-source heat pump (GSHP) if electricity is really bad at heating stuff. Typical COP for a GSHP is 5, which means it creates 5 kW-hrs of heat for 1 kW-hr of electrical input. That's not just 100% efficient, that's 500% efficient. Even air-source heat pumps are now getting COP's of 2.5-3 down to 17 degrees F and COP 2.0 down to zero deg. F.
Ground source blows away other conventional heating/cooling systems. But you are not using electricity to heat or cool your using it to run pumps and fans, your stealing the heat or putting the heat into the ground, as a bonus the excess heat is usually used to make hot water as well.
Lukitas,
I agree that oftentimes, like might best go with like, but I would also offer the extreme usefulness of the way we can use many of these energy inputs and convert them to a complementary need.. such as using the Sun's heat to refrigerate or create Ice.
Many's the time during a windy winter night that I so wanted to have a wind turbine for nothing more than to take that frigid power and turn it right into heat for the house that's huddled under that tough weather, using Jack Frost's power to directly defy him!
Finally, and I'm just shocked, Shocked that Ghung didn't bring it up.. but electricity is even MORE efficient with Heat Pumps which can now achieve a coefficient of Performance of 3 or 4 times the Heating or Cooling *(lower COP) power that is available through resistance heat.
In the spirit of the Post by Kris, I have been eager to see the use of wind or water power to directly drive the compressor of one of the many types of heat pump that we can use, and get rid of the Middlemen that rob from it's performance.. and the Heating or Cooling that is created thus can be pretty easily stored, making it convenient to use these power sources when available, and enjoy their fruits when needed.
All the Best,
Bob
Since Kris is "highlighting the need for elegant yet simple sustainable energy technologies", I didn't consider the level of complexity that heat pumps represent, though the idea of running a compressor directly from a water wheel or windmill is intriguing. Pumping/compressing refrigerant isn't very different than pumping water or air. Using water to turn a compressor to store energy as compressed air is also an option; run a pneumatic chainsaw or something.
I guess grinding grain or coffee beans is too mundane for 21st century gadget gurus. Anyway, I think Kris is suggesting more simple and resilient uses of water power than heat pumps. I do wish I had a big stream with plenty of fall, just to play with; what fun that would be. Alas, I'm the top of the watershed. At least no one is messing up our water (except TVA).
Ah, then my shocks have been grounded..
Don't get me wrong.. I'm very much in favor of using the power for simple direct work, but similar to your dumped loads, I would be eager to switch over to a compressor or equiv., whenever the shoptools or the coffee hulling was done for the day.
I did also feel it's worth remembering at that point to also keep an eye on not simply looking at something 'extractable' as something we should extract ALL of, either. To be willing to moderate our own taking is, IMHO, an important aspect to being in a better relationship with the source and nature, and in a better mode of thinking around our own need.
It's worth putting some thought to the old words Gluttony and Avarice, I think.
Another factor to consider is if you're using direct hydro, you need to maximize the amount of power you use to keep those efficiency levels up. For instance, if the river provides 1600W of power, you'd be wasting energy if your saw only used 800W. So even though conversion to electricity may suffer an efficiency penalty, there may be less waste overall if you're able to store excess energy or distribute it to other uses.
A lot of the original industrial development in the US occurred where there was the potential to set up direct drive mills, and a number of Eastern cities got their start this way. The problem is that the potential for direct drive mills generally occurs in hilly country with difficult transportation and insufficient farmland to support the population. Most industries like to locate where the land is perfectly flat and their is easy access to transportation.
I found the references to Nepal interesting. Trekking around and looking at the country from a Canadian perspective (60% of Canada's electricity is hydro) it was obvious there was huge hydroelectric potential - there were numerous huge rivers falling from the height of the Himalayas almost to sea level. If they were to put dams on those rivers, they could have almost as much hydro power as Canada does.
Unfortunately, while there were lots of micro-hydro projects sponsored by NGO's, almost none of their major potential was developed. We took a tour of the second biggest hydro project in Nepal (the Nepalese were not allowed in, but we were), and it was smaller than the two hydro plants within a short walking distance of me here in the town I live in (Canmore, Alberta). Their second largest plant was about 100 MW, our two plants are 200 MW in total. And our two plants are almost nothing in the overall scheme of Canadian hydropower. They are automated and run completely unstaffed.
Nepal has almost as many people as Canada (30 million vs. 33 million). The capital city of Kathmandu now has 2.5 million people in its urban area - as many as Vancouver - and suffers from horrible air and water pollution. Unlike Canada, Nepal is severely overpopulated in relation to its resources and is no longer the mystical Himalayan kingdom it was 50 years ago. When I was in Kathmandu, they had power outages of 8 hours per day, and now I hear they are up to 14 hours per day of blackouts. Outside of the capital, 60% of the Nepalese population has no electricity at all, and is going to completely deforest the country in about 20 years burning wood for heat. It is a typical 3rd world disaster. I'm never going back again.
This is from the Interdependent Power Producers Association of Nepal (ippan dot org dot np):
Hydropower in Nepal
OTOH, I flew from Kathmandu, Nepal, to Paro, Bhutan, with spectacular close-up views of Mount Everest in passing, and it was like leaving from India and landing in Switzerland:
Bhutan banks on ‘white gold’ hydropower
So this is a comparison of two countries - Nepal with 30 million people and 600 MW of hydro capacity, and Bhutan with 750,000 people and 1,500 MW of hydro capacity - almost all of it paid for by nearby and energy-short India. Which one would you prefer to live in?
Interesting fact that a lot of people don't know: The 4 largest power plants in the world are all hydropower plants. A nuclear power plant is the 5th largest.
One key advantage of hydro-electric generation over direct hydro is that it can be put to productive use even when the normal beneficiary of this power has shut down its operations for the day. A manufacturing facility that operates ten hours a day, five days a week, say, would only utilise 30 per cent of the hydro potential that is available to them in the case of a run-of-the-river facility; the remaining 70 per cent is effectively lost.
Electricity generated outside normal business hours could be sold to the local utility for profit (where this option exists), used for space heating and cooling purposes, to heat DHW, recharge fork lifts and other battery operated equipment, and so on. In isolated communities that lack grid power, it could also be donated for communal purposes, e.g., street lighting, recharging mobile devices, powering a community centre, refrigeration of vaccines and other perishables, etc.
Think not only of what you want to do, but also what you could do.
Cheers,
Paul
Great post, thanks a lot. There are a lot of pioneers in miniature hydro in India.
About 60 years ago I visited Hardy's Mill, near Tumbarumba, NSW, Australia. It was a sawmill village completely powered by water. Water was collected by a contour channel around the mountain above the village, into a small reservoir (less than one acre, if my memory serves me right). The only platypus I've ever seen in the wild lived there. Water was delivered to the mill by two concrete pipes about 50cm in diameter, giving a head of about 200m. The largest user of the water was the head saw, a circular saw about 2m diameter, used for the initial shaping of the logs, and for cutting them into flitches. This was driven by a large pelton wheel. Other saws, winches, etc., were also powered directly by smaller pelton wheels.
But the high pressure water was also used throughout the village for both water supply and for power. The house we stayed in had a 32 volt DC power supply, based on lead-acid batteries, but instead of these being recharged by a dynamo driven by a small gasoline engine (which was common in remote parts of Australia in those days) it had the dynamo driven by a small pelton wheel.
A mechanic's workshop I visited there had the usual collection of power tools -- saws, drills, a lathe, a battery charger, etc. -- but instead of electric motors they all had small pelton wheels driving them.
The largest maintenance cost, we were told, was repairing leaks in the contour channel, usually holes dug by wombats.
I was no more than about ten years old at the time, but I was very interested in technology even then.
Hi Kris,
Thank you for your web sites. They really give me hope and a great appreciation of the ingenuity of our ancestors! Here is the US there is so little "old" that it is hard to imagine a life without lots of oil, gas, and coal.
Your direct hydropower article is an example of something very interesting: A small amount of high embodied energy equipment, upgraded water wheels, can harvest and use efficiently a much larger renewable energy source.
This makes me wonder if renewable energy will lead to a new increase in cottage industry? In the past, distributed renewable building materials (wood, reeds, cloth) were processed using renewable energy (grain, pasture raised meat, milk) into goods.
The central factory, using coal, could replace that work much more cheaply. The coal powered rail system could concentrate raw material and distribute manufactured goods more cheaply than renewable powered workers could compete.
What will happen as the cost of coal and oil rise? Will quality of life just fall? Or will investment shift to using factories to make devices that capture local energy? And then use that local energy to process local raw materials into local goods?
I don't know. I can imagine a large hydroelectric dam that is used to manufacture solar cells, or water wheels, and power tools. Those solar cells and power tools create local goods and services, some of which are traded back in return for the solar cells, etc. I can imagine this may work if the transport energy cost is reduced by more than the captured energy. Meaning the total energy in society is larger than without. I don't know.