Tech Talk - American Stripper Well Production
Posted by Heading Out on May 22, 2011 - 6:04am
The Total (oil company) discussion on Enhanced Oil Recovery has an illustrative graph to explain why there is a growing need to get as much of the oil in a reservoir as can be economically recovered.
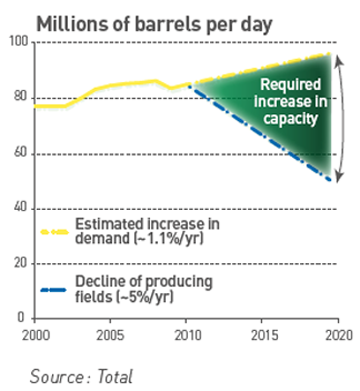
When the large flows of oil that I have written about previously stopped flowing from the major production fields in the on-shore United States, that did not mean that the wells from which they issued were immediately shut-in. Rather, in many cases, although the driving pressure to move the oil to the ground surface had largely disappeared, there was still a sufficient imbalance within the reservoir that oil would flow to the well. And so, before moving on to discuss other fields, I thought I would spend this space covering the pump jacks or “nodding donkeys” that dot the landscape over many of the older oilfields of the United States (and elsewhere).
These “stripper” wells that remove the final volumes of oil from a reservoir make up by far the largest number of wells, by category, that produce within the USA. The EIA reported that there were 363,459 producing oil wells in the USA in 2009. Of these, 35.1% produced 1 bbl/day (bd) or less, and 78.7% (a total of 286,109) produced less than 10 bd. For Texas alone, the EIA reports that there are 141,582 wells, and 79.4% of these produce less than 10 bd. (H/t Joules Burn).
So when oil production gets this low, and intermittent, how does the owner get the oil out? The short and simple answer is that the oil is pumped out. And if the well is running slowly, then the pump won’t run all the time, but rather intermittently depending on how fast the pump fills. The original pumpjack design was put together in 1925 by Walter C. Trout, and provided the basic design for the units still dotting the American landscape.

That basic design has largely remained the same, but the instrumentation and controls have grown more sophisticated over the years. A baseline estimate of the power requirement is that it needs around 0.2 kwh/bbl/1000 ft to lift the oil to the surface. (Which is quoted as being about a 66% efficiency). Deeper wells are reported to require from 0.27 to 0.81 kwh/bbl/1000 ft. And if the wells are 4,500 ft deep, that can create an electricity bill of up to $2,000. (H/t to Joulesburn for raising the topic). Part of the problem and loss in efficiency comes from the need to start and stop the pump because of the low flow of oil into the well.
The Web site dealing with Stripper wells (those defined as producing below 10 bd) notes:
In the United States of America, one out of every six barrels of crude oil produced comes from a marginal oil well, and over 78% of the total number of U.S. oil wells are now classified as such. There are over 400,000 of these wells in the United States, and together they produce nearly 900 thousand barrels of oil per day, 15 percent of U.S. production.
The average stripper produces around 2.2 bd (ibid). (The 25-minute movie “Independent Oil: Rediscovering America's Forgotten Wells” can be obtained from Amazon, or by dropping a note to the Stripper Well Consortium.
Further, it points out the economic factors that inhibit re-starting these wells once they are abandoned.
When marginal wells are abandoned, significant quantities of oil remain behind-- sometimes as much as 1/2 to 2/3 of the total oil. In many instances, the remaining reserves are not easily accessible when oil prices subsequently rise again: when marginal fields are abandoned, the surface infrastructure - the pumps, piping, storage vessels, and other processing equipment - is removed and the lease forfeited. Since much of this equipment was probably installed over many years, replacing it over a short period should oil prices jump upward, is enormously cost prohibitive.
The site notes that between 1994 and 2003 some 142,000 wells were plugged and abandoned, losing the remaining oil that they might have produced. This oil is sufficiently important (since it makes up about 10 - 20% of the domestic oil production, depending on what is counted) that DOE has a program dealing with Stripper Well Revitalization (covered on CNN here) and funds the stripper well consortium that investigates ways of improving the technology.
Many of the advances have focused on improving the pumping systems used in these old wells, since the old conventional plunger systems are not that efficient, relative to the new units. The large number of wells means that even where these improvements are significant, it will take some period of time to get enough new units into the field to have a significant impact on overall production.
The Gas Operated Automatic Lift (GOAL) PetroPump developed by Brandywine Energy & Development Company. The pump removes fluid from the wellbore more consistently than currently available plunger lift systems. Test results on wells in New York showed a 1.5 to 2.3-time increase in gas yield using the GOAL PetroPump over other casing plunger- type tools. The tool is inexpensive to operate because it requires no external energy source and limited manpower.
One area that they have just started work on involves the use of high-pressure jetting for drilling laterals, with the work being developed by Buckman Jet Drilling Inc. Since I jet drilled my first lateral of this type back some 30-odd years ago and have some considerable familiarity with both the promises of the technology, and some of the problems and other issues that have arisen, I suspect that I will be following this in a bit more detail than I usually allow. But that too will come in a future post; for the moment I will note that, after having watched the promotional video I do have some significant concerns that arose out of an earlier incident where a somewhat similar technology was claimed to be able to achieve considerable improvements in well production. In that case my concerns were expressed in Federal Court.
One other recent breakthrough that they have highlighted involves the conversion of the significant amounts of water than come from these stripper wells, but which is often brackish, and thus difficult to dispose of into water of potable quality (i.e. you can drink it). In a slide presentation by Texas A&M, who developed the membrane technology used, the resulting water is compared with Evian, Perrier, and similar commercial products. Given the problems that Texas is currently facing with drought this could well solve two problems at one time. Further by lowering the cost of water disposal it, like other SWC developments, can encourage the economies of these small producers and sustain their production further into the future.
Each well may not contribute much, but in the aggregate even small changes can add up, when the totality of the wells affected runs into the hundreds of thousands. This improvement in the tail of well production, sadly, is only likely to be viable in the relatively small on-shore wells and close off-shore where the costs of maintaining the infrastructure above the well is minimal. Once those costs become significant it becomes more difficult to make the economics of the process work.
I’ll talk about some of the other ideas for stimulating these wells in a post somewhat later in the series. But this, from Total, is one I have written about before.
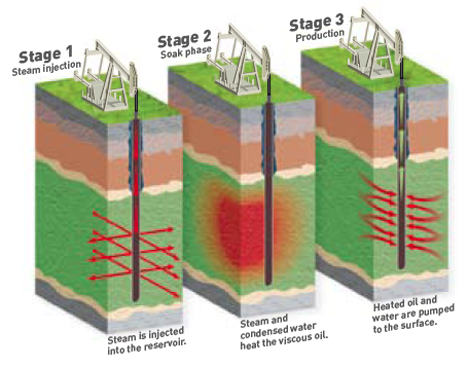
HO – Another nice coherent presentation…thanks. I’ve just had an experience with a new hydraulic pumping system. Unfortunately I don’t have a picture but it’s easy to describe: it’s a vertical cylinder about 3’ in diameter and 25’ tall. And unlike a pump jack that requires a steel reinforced concrete pad it attaches directly to the top of the wellhead. A small diesel pump sitting on the ground powers the hydraulics. An electric system is available if you have service on your lease. The system drives a rod in a max vertical movement of 20’ which in turns drives the down hole pump. In addition to eliminating the pad it’s less than 20% of the mass of a conventional pump jack. It’s also controlled by simple computer program.
Unfortunately I don’t have values for efficiency but it’s clearly an improvement. It could represent a significant increase in the economic life of thousands of strippers. Or not. Here’s the good news/bad news. The company that developed this system recently sold out to Lufkin, the major supplier of pump jacks. We might hope they’ll use their position to expand distribution but they may just sit on it. A large percentage of pump jacks are leased to the operating company, just like I had leased my hydraulic system. Nearly all the many thousands of existing Lufkin pump jacks have recovered their cost long ago so the lease fees are almost all profit. Swapping out to the new system will require someone to invest a lot of capex…operators or Lufkin. Time will tell.
Like this?
Lufkin Long Stroke Hydraulic Unit. Bigger picture here: Antique Pumpjacks, Old Pump Jacks.
Lufkin Industries | Well Servicing Magazine
That's it. Good job. I heard they paid the developer $X millions for the rights and a $250,000/year retainer for 5 years as part of a non-compete trade. Nice guy...met him in the field a couple of times. First time was when he came out to yank them off my two wells. The previous operator didn't pay him. Signed a new contract and wrote him a check. Easy to keep on friendly terms that way. LOL
Seems so simplistic I wonder why no one thought of it before. I'm not a mechanical enginer but I suspect most, if not all the parts came of the self.
Any use of solar or wind to power these wells? It seems that intermittancy wouldn't be a problem. Also, offshore strippers could be powered by wave/tidal action, though I don't know where the oil would be stored. Large, submerged tanks perhaps, to be emptied only occasionally. Likely not profitable (enough).
I tried to explain to a buddy once how this is one of the differences with onshore and offshore wells. Onshore wells can be 'stripped' for years, sometimes decades; offshore, due to the economics, are generally capped when the flow drops to a certain level, leaving alot of oil behind. It didn't quite compute that this oil wasn't worth going after, whatever the cost. Such is (much of) the public's perception of oil.
An "off grid" stripper well would seem to be a good candidate for solar and wind power, but then, you can always run the pump with an engine powered by the wellhead gas or even the crude oil produced!
A video here of an old horizontal oilfield engine chugging away - has probably been running for decades. Wouldn't want it within earshot of my house though..
http://www.theinfomine.com/2010/05/08/photo-of-continental-emsco-falk-11...
Those numbers for kWh/bbl are interesting, allows an easy calculation of the marginal EROEI. A barrel of crude is about 1600kWh, and if we said the well is 5000' deep and use mid range number of 0,5kWh/bbl/1000', we need 2.5kWh per barrel produced - a raw EROEI of 640:1
If we use some of the oil to run the engine for the pumpjack, and say the engine is at 30% efficiency, then we use 8.3kWh, for an EROEI of 192.
So, if the wells are already there, getting the oil out, even at 1bbl/day, is a very high EROEI.
If the well is grid connected, it may make a good place for a grid connected wind/solar system - all the infrastructure is there - land, access road, grid. Watching the pumpjacks on the windy prairies in Alberta I always thought they would be good spots for wind turbines.
A question for HO/Rockman - if you have an old stripper well, you could set it up to only pump at night, on off peak power. But that means doubling the pumping rate at night, and shutting down during the day - is there any problem with the well in doing this?
Paul - Your pump timing and rate are determined by the reservoir. But they can be set to fit as most economical with the surface situation. On very marginal wells they might only pump a few hours each day. The well needs the down time to allow the oil to flow back into the well. The pumping doesn't pull the oil out of the reseroir...it just lifts it up out of the tubing. Taking the back pressure off allows the oil to flow in. But there are better wells that pump 24/7/365 and produce 100's of bbls of fluid per day.
Good example Paul:
How about another idea? Along the same vein...
Think oil sands. Unlimited supply. No need to look for it.
Say you have a small lease north of Ft MacMurray. It has about a billion barrels underneath...a 30m payzone more or less.
By way of new technology, you heat this ground with wind or other intermittent resources (not typical grid power which is 80% Coal/gas thermal FF in Alberta).
The Capex for installing this technology to extract the 1 Billion barrels over say...25 years @ 110,000 bpd or so is $15,000 per flowing barrel per day (bpd).
That is $1.6 Billion Capex to get that production up to 110,00 barrels per day.
Now you need the wind (we have lots of stranded wind in BC and to a lessor extent in Alberta also...
We require about 65 KWh to get one barrel up to the surface. If wind costs $100/MWh, then we need about $6.50/barrel to extract the bitumen.
No tailings Ponds, no added water, no Nat gas, no Emissions.
The wind farm CAPEX to allow this production rate will cost about $2Million/MW to install or about $1.6 Billion for the 1000 MW wind farm to supply the energy over a year (not capacity) to the bitumen payzone below.
We require $1.6 plus $1.6 = $3.2 Billion to extract the 1 Billion barrels (plus other O&M costs)
1 Billion barrles x $65 per barrel of bitumen (65% of WTI Price) is worth $65 BILLION undiscounted and does not include Renewable energy credits for all the GHG's we don't produce...
It is the ideal Utility or Grid system load as it is entirely interruptable with no consequence to grid operations. It is, in fact, exactly what the Bonneville Power Authority (BPA) is crying out for....a Marketplace load or sink to prevent them from spilling water and killing fish..right about this time of year...
The point is: It is doable, scalable and has an EROEI as follows:
Bitumen energy content is less than 1600 KWh per barrel of crude. For sake of argument , let's call bitumen @ 1400 KWh.
It takes 65 KWh to get it to the surface. 1400/65 = 21 for an EROEI
this markedly better than SAGD and BAU Surface Mining.
We still need to adjust for other energy inputs such as the EROI of wind turbines. The latest I have seen for the new very large scale Vestas units at 5 MW and up are in the range of 25 to 30 for an EROEI.
Paul ..can you help me with integrating the wind EROI and the simple energy to bitumen extracted equation?
Thx....
PS: We can discuss the next step...upgrading and refining the bitumen without nat gas and no GHG's...
Then the next step, railway to tidewater without emissions.
Tidewater to market in very slow supertankers powered by sail kites.
i saw a great heat windmill in canada. blades made out of automobile hoods. big steel tank full of steel and iron chunks bought at the scrap yard. copper tubing ran about the tank with glycol running in it. windmill ground the steel
down to dust, friction heated the house and barn. metal dust sold for twice what he paid for the scrap. a little noisy, but it was down wind, and behind a bank of earth from the farmhouse
How fine were the particles that the metal was ground into ?
You will need an awful lot of nodding donkeys. Conduction is a slow way to heat soak a reservoir. According to the back of my envelope, you would get about 5m of soak in 25 years, so you would need wells on a 10m pitch. If you want to get a reasonable rate of heat soak, you need to convect the heat source through the reservoir, and that means either a condensing vapour (effectively SAGD) or a fuel (effectively THAI).
You could theoretically use windpower to run the THAI air compressors or to boil the SAGD steam, but I don't think you can directly soak the reservoir with it on anything close to a reasonable timescale.
Solar Powered Pump Jacks are already in use on some gas wells with low water rates (< 10 bbls/d). The key is fiberglass rods....the lighter weight allows for a smaller motor....and saves on workovers from holes in TBG due to rod wear.
Well, there we go, the oil industry and solar together at last!
Must be a lower power and/or low duty cycle pump/motor - looks like about an 800W array. But, that's obviously enough to do the job, so great!
HO,
I'm told that pumpjacks are an unusual site on offshore platforms. Can you tell me why? Here is a photo I took of those on Emmy off our coast.
Huntington Beach is a textbook example of your discussion. Here is a nice visual for the capped and active wells in my neighborhood (solid black active). I don't know the going rate for capping a well but a decade ago it was well over $100,000 in our area.
And here is our production data.
Debbie:
Thanks for the pix, and the plots of the wells, it makes the point about making sure that you get what is yours, rather than letting the neighbor's well grab it.
The reason that the offshore wells aren't stripped as long most often will come down to cost. There is more maintenance involved offshore, and it is often a more hostile environment than a corn field in Illinois. Thus where there were small production wells offshore Louisiana before the Hurricanes of 2005, many of these were never re-started because of the cost:benefit numbers. In other cases as production falls the investment to maintain production is not offset by what can be recovered. (See Rockman's comment below).
Great map, Debbie. I have a copy of Early California Oil: A Photographic History, 1865-1940, oil production in the midst of urban development is fascinating to me for some reason. It's amazing, the solutions they've come up with for dealing with hiding the machinery in the LA area.
Here's Google Books's link for Oil and gas production in nontechnical language. This should link to the excerpt that answers your question, if not, go to Page 172. Beam pumps take up too much room for offshore, are limited as regards depth, can't handle deviated wellbores, can't handle high volumes, and use too much energy to lift oil at these depths.
Thank you for the info.
Regarding electricity to lift oil, I took a tour of the Wilmington oil field (Long Beach) several years ago and the guide said that their energy bill exceeds $80 million a year.
Debbie - $100,000 to P&A a well? Maybe in CA but in Texas today I can do it for $10,000 - $20,000. And sometimes for a zero net cost if I can sell enough salvaged equiment, like seperators and oil tanks, off the well. Offshore wells will obviously cost a lot more.
Debbie, That map sparked my memories. I remember jogging down Goldenwest on the way to the pier a few years ago and noticing those rigs in the lower right part of your map.
It was memorable seeing them still pumping away and also the fact that few people jog on the streets in Huntington Beach :)
The production profile is also interesting because it demonstrates how a spread in development effort from onshore to offshore tends to broaden the peak curve. I think it is a classic example of dispersion of effort -- lots of early fast effort at depleting resources followed by slowly accelerating progress exploiting the other more difficult-to-reach areas.
This is part of the magic of liquid fuel. If we had to extract a solid from a depth, the energy would need to be balanced by the removal of the head of material (plus the material itself) lying on top of it.
Think about it in terms of a buried explosive; how much energy in the explosive would be be needed to lift off the amount of earthen material that is covering it. If this is a thin seam, realize how thick the seam would have to be to make it energy positive, i.e. that there is some energy left over to use elsewhere.
With liquid, the one time charge of excavating a bore-hole is balanced by the drainage of a much larger volume.
That is essentially what we are dealing with everyday, in terms of coal, oil sands, shale, etc -- a really significantly reduced Potential Energy Returned on Work Invested = PEROWI; something you can derive from freshman physics.
The ever present issue is that the way that humans are able to operate so efficiently, in terms of extracting thin profit margins in just about any line of business, that even narrow PEROWI will get taken advantage of, even though it adds huge amounts of entropy to our environment.
Are there currently subsidies for stripper well production. If not, when was the last time that stripper subsides existed? Below is a link to a planned 1944 subsidy. Has there ever been a situation where subsidies made it possible to profit financially in spite of a negative EROI?
http://www.time.com/time/magazine/article/0,9171,803261,00.html
No source and before my time, but I believe in the 1970s when a differentiation was made between "new" oil and "old" oil for purposes of a Windfall Profits Tax, stripper production regardless of discovery date was classified as "new" oil. Not a direct subsidy, but a small recognition that marginal production is marginal.
HO - Advances to make the poduced water potable. Shouldn't pressure maintenence dictate that the best use is reinjection (presumably on the edges of the field)?
Like Ghung, I suspect that intermittent power ought to be a good match with pumping needs. As the penetration of renewables increases, grid operators should be looking for more and more intermittent users who could be offered rate discounts in return for participation in demand management programs.
eos et al - Not all reservoirs require pressure maintenance. Many have a strong natural water drive. In fact, these tend to be the fields with the most water to dispose. If a well is making a small amount of water we’ll pay to have it hauled to a disposal well. But if there’s a lot of water an infield disposal well is required to make the operation economic. I’ve seen many wells abandoned because hauling water wasn’t economic and the capex for a disposal well couldn’t be justified. Sometimes you have to burn up horsepower to pump the water down but if you’re lucky the injected formation will take it on gravity drainage. Injection wells are expensive…often twice the cost of a producer. They aren’t maintenance free either. And pump jacks can take a personal toll on occasion: every year a number of production hands are injured/killed by pump jacks. They may look like tinker toys but they are a massive piece of unforgiving steel. A couple of years ago the father of my daughter’s best friend died when his head was crushed by the horse head. The timer turned it on while he was working on it. There was a kill switch that would have prevented it from doing so but he didn’t use it. Carelessness can be deadly. He stopped at the well on the way to church and left his wife and daughter in the pickup when he jumped a fence to check on the well. Wife found him when he didn’t come back. Sometimes the effort costs a good bit more then sweat. I’ll think of him every now and then when I’m putting gas in the car.
Solar power: I’ve seen a number of applications where small panels were used to power various electronics but never a pump jack/injection well. Not my area but I suspect the capex for a sufficient collection system isn’t economic. Typically by the time a well starts to reach a marginal level it belongs to a small operator that is usually capex poor. Stripper wells usually survive on a lot of sweat equity: instead of an auto lube system he’ll cruise the field very morning with a grease gun in hand. If the timer on his pump jack burns out he swing by and flip the switch by hand. If he has to shut a well in for a mechanical problem he might wait a couple of months to set aside the money for the work over.
The irony has been discussed before: companies with large capex have a difficult time keeping marginal fields productive due to their high over head…especially salaries. The small independents essentially pay themselves out of the net income: have a bad period of low oil prices and a lot of repairs and he might work some months for the equivalent of half minimum wage. But he is his own boss. I’ve dealt with many stripper operators and they tend to be very “independent”. This is what makes the US very unique in the world. Time will tell but IMHO we won’t see the life of marginal wells globally match that which we’ve seen during the last 40 years in the US.
HO probably plans to go into details on other “lift systems”. For now the two other common methods are ESP’s (electric submersible pumps) that are placed down hole at the end of electrical lines and GL (gas lift) where NG is injected down separated from the upward moving oil. The oil is essentially aerated by the NG and “flows” to the surface. And if there isn’t enough NG produced with the oil then “lift gas” will have to be purchased from a source. Of course, that would require laying a pipeline to the field. One more big capex expense. Additionally once the lift gas is separated from the oil it’s at low pressure and needs to be compressed in order to be re-injected…one more expense. When an offshore well requires lifting help a GL system is the typical choice. Space is always a premium in the offshore so pump jacks seldom fit the need very well.
from an article I wrote for Don Hart in February:
Interesting case history. Is any information on decline rate available for this field? And what was the cap-ex for this project?
With $100 per barrel oil price this field makes a good profit, even if the owners net $65/barrel ($230 mil/year). But if in two years the price drops to $60/barrel (maybe net of $35), will the field still make a profit after decline reduces production to maybe 6,000/day? Injection of CO2 is not cheap if the gas comes from a far away, and compression costs rise with price of nat. gas. Another reason oil price needs to be kept at $100/barrel level or higher, to encourage projects like this.
Joe sixpack does not understand that if the oil price stays high we will have much more supply than if the price drops to $35/barrel and gas is $1.50/gallon (like in early 2009) and remains there.
"The small independents essentially pay themselves out of the net income: have a bad period of low oil prices and a lot of repairs and he might work some months for the equivalent of half minimum wage. But he is his own boss. I’ve dealt with many stripper operators and they tend to be very “independent”. This is what makes the US very unique in the world."
Could this perhaps be seen as a future model for the middle east, once the existing feudal societies there finally break down, following a lack of income due to depletion and world chaos?
mo - Difficult to predict. The only significant asset of value in ME countries will be what oil can be produced from the dwidling fields. And the oil fields belong to the govt and not private citizens as in the US. Perhaps in a Mad Max world the remnants of local civilization might take over the fields (actually was such a Mad Max plot). Of course, in the movie it was esentially gang warfare to control those fields. But even if this did come to pass I doubt much would be heading to the export market. Another far fetched possibility is that the US might "export" the spirit of our independents to the ME much as we are "exporting" democracy over there now. Maybe like the Federation "exported" farming to distant planets by transporting tomato growers out there where no man has gone before. Just need to load a bunch of C-130's with a pack of E Texas rednecks, head them across the Big Pond and we'll have those strippers pumping "our" oil in no time. Don't even need to arm them...they come preloaded. LOL
Can any of the people with some expertise make a SWAG of what the production might be brought to if all possible wells were equipped with the best pumping/recovery technology? Could we get to maybe 3 Mb/d and keep it there for a couple of decades?
Murry – If you’re asking about potential gain in the US thanks for allowing me my first smart *ss answer of the day: almost no gain. LOL. This has been one of the more irritating aspects of some cornucopians’ projection of increasing US production. Almost all the current methods used to keep margin wells producing (water floods, pumping systems, etc.) have been applied to every well in this country where it made economic sense to do so for the last 50+ years. And in many cases applied when it actually didn’t work economically but did add to our production stream. That’s exactly why we have so much of our production coming from marginal wells. And all those tens of thousands of stripper wells abandoned when the then economic conditions required plugging? Almost all are lost forever even when conditions improve significantly. To comply with regs and protect the environment the plugging techniques effectively destroy the well. Typically it’s far too expensive to redrill such a well. I might be able to spend $50,000 to install a pump jack but not $2 million to redrill the well.
Bottom line: there is no huge cache of US conventional oil just waiting for EOR or some pump jacks to produce it. We’ve been doing it for over 60 years. And any wells that may have reached the stage of needing a pump jack in the last few years? High oil prices quickly took care of that potential: they are producing today.
You’re welcome. LOL
Rockman you're losing the flavor here, which is Cornucopian Licorice. It only comes in one flavor but its such a valuable one that holds the promise of infinite BAU.
Earl - I do chuckle sometimes when the cornies go on about all the reserves the oil patch has been too lazy/ignorant to produce. With repect to onshore oil exploration the oil patch was scraping the bottom of the bbl when I started in 1975 for Mobil Oil. They and all the other Big Oils had given up on US oil exploration for the most part. There was one last gasp in the offshore arena which was extended into the 21st century by the Deep Water GOM play. But even the majors didn't dominate this play. Many had already shifted their efforts overseas decades earlier.
I'm a development/production geologist and for the last 36 years almost of my oil projects have focused on squeezing the last few bbl out of old fields. This weekend I'm writing a proposal for my owner to target 100's of millions of bbls of residual oil in fields that were discovered ove 60 years ago. A bunch of pump jacks won't get it done. It will take some high end and expensive horizontal well bores to do it...hopfully. And if it does work I'll still just recover an extra 5% of the URR. But I need to do a couple of pilots projects to prove to him (and me) that the project will generate an adequate return. And if it works really well and other operators give it a try? The results won't even show up as a minor blip on the national oil productional curve. But me and my owner will make a lot of money and that is, after all, why we do this. It's not to save the public from PO.
Rockman,
CO2 seems to be the Holy Grail for EOR in the States, would an increased availability make a significance change to production?
The reason I ask is, Underground Coal Gasification (UCG)which as a by product produces large quantities CO2. At least two companies I know intend to use for EOR in Wyoming. The coal that is used is below normal economic depth for mining, and has no other use. As you are aware these deep coal beds commonly lie in currently producing oil fields.
What is your opinion, would this make much of a change?
pusher - In a particular field it would make a huge difference. But nationally such upticks hardly register...just too few applications. About 10 years ago there should have been a uptick in CO2 EOR in eastern Wyoming. ExxonMobil(?) finally had enough economic incentive to lay a very expensive pipeline from CO2 fields in the west. About 15 years ago Shell had plans to do the same for one of their fields in S La. But every field that had access to economical CO2 was undergoing this EOR...often for decades. New opportunities just didn't pop up to often. And with high oil prices these days there could be more possibilities out there but an operator will be cautious with respect to oil prices staying high enough long enough to get to a 3 or 4 year payout before the profit starts to kick in.
Rockman,
My thoughts about UCG being a bit of a game changer, or should I say game helper, is the fact that UCG would make CO2 available in many of the producing basin where today it does not exist (in required quantities), with no long distance pipelines required.
Not sure how much coal lies under Texas and La but if there is any, I am sure UCG and CO2 injection would be a very economic use, flammable Gas from the coal and increased Oil production from CO2 injection at the same time.
I wrote this a while back.
A friend directed my attention to an article by Luke Burgess at Energy and Capital that gushed with optimism about exciting new carbon dioxide injection technology for enhanced oil recovery, capable of sweeping an extra 89 billion barrels of crude from old, sticky domestic US reservoirs.
Unfortunately, Burgess copy-pasted his so-called 'news' verbatim from a Dept Of Energy website that fudged the numbers and materially misrepresents reality.
Carbon dioxide injection is not new technology
The oil and gas industry has over 35 years of continuously developing experience in transporting and injecting CO2 for enhanced oil recovery (EOR). While constantly evolving, the technology operating experience and regulatory requirements that have been developed for EOR are extensive. In the United States alone, the oil and gas industry operates over 13,000 CO2 EOR wells, over 3,500 miles of high pressure CO2 pipelines, has injected over 600 million tons of CO2 (11 trillion standard cubic feet) and produces about 245,000 barrels of oil per day from CO2 EOR projects. [American Petroleum Institute, 2007]
The technologies and practices associated with geological CO2 sequestration are all in current commercial operation, and have been so for several decades. Such commercial operations include: enhanced oil recovery, CO2 injection, natural gas storage and CO2 pipeline transportation. [Heinrich J. et al, MIT, 2004]
Close reading of DOE technical assessments reveals that only half of the headline 89 billion barrels deemed "technically recoverable" are conceptually "available" by implementing costly and complicated acid gas injection.
In the Base Case, 45 billion barrels of incremental oil become economically recoverable from applying CO2-EOR using an oil price of $70 per barrel (constant, real) and a CO2 cost of $45 per metric ton ($2.38 per Mcf)... Higher oil prices, by themselves, will not unlock much more of the large 84.8 billion barrel technically recoverable oil resource available from state-of-the-art CO2-EOR [Kuuskraa et al, DOE, 2008]
Let's Back Up A Bit
Primary oil flow in a new well (a gusher) depends on reservoir pressure. Thousands of feet of rock create a hot, heavy overburden. Trapped oil, water, and dissolved gases flow up the wellbore to the surface naturally, sometimes too easily and too fast to control. That's why blow out preventers are standard equipment.
Primary flows decline rapidly as oil, water, and gas are produced and pressure in the reservoir is reduced. Most operators plan upfront to inject water in flanking wells "downdip" under the oil column to maintain reservoir pressure and keep producing wells flowing. This is secondary recovery (water flood).
It's important to note that oil wells produce oil mixed with water and dissolved gas, along with sulphur, CO2, sand, radioactive minerals, and drilling mud that invaded the formation while drilling. Gas wells produce gas, liquids, and sticky tar. Topside separators are standard equipment. Salty, sour formation water is hauled away for treatment and disposal or reinjected to maintain reservoir pressure.
Natural pressure and water flood will produce about 30% of the original oil-in-place (OOIP). Heavy oil fields recover less. Oil flow is impeded by tightly packed granular structure of the rock and surface tension around each grain. That's where "tertiary" enhanced recovery comes in, to flush more of the oil from the surrounding formation rocks to the producing wells.
Before we discuss CO2 injection which has been used in Texas since 1972, please note that CO2 is not appropriate or economic in every field. Injection of heated water and steam (thermal EOR) delivers 50% of all enhanced oil recovery in the United States. Capital and energy input cost of thermal injection (pumps, topside separation, etc) is only one-fifth of equivalent CO2 enhanced recovery.
Here's a typical CO2 injection system.
In general it is acknowledged that using CO2 for tertiary EOR may add an additional 5 - 12% of OOIP to the anticipated total production. An essential feature of using CO2 for EOR is that the CO2 will mix and remerge with the produced oil and gas. [Kinder Morgan]
Does CO2 make sense?
The short answer is yes sometimes. The Permian Basin carbonate formations in Texas and New Mexico are particularly suited to alternating CO2-water flood "huff-n-puff" stimulation. It has been tried elsewhere in light oil and gas reservoirs. But CO2 injection is not cheap and won't work in all fields or rock formations.
DOE's glowing endorsement of CO2 injection and geologic sequestration is driven by politics more than science. Their fantasy scenario of someday recovering 100 billion barrels from the "transition zone" where oil is hopelessly mixed with formation water and mineral contaminants is a bad joke. Absent government subsidies and tax holidays, no one can afford the front-end cost of CO2 infrastructure plus added cost of separating, treating and disposing of a 95% water cut.
Given the significant front-end investment in wells, recycle equipment and purchase of CO2 equivalent to $20 to $25 per barrel and the time delay in reaching peak oil production, pre-tax economic margins on the order of the front-end investment will be required to achieve economically favorable rates of return. Oil reservoirs with higher capital cost requirements and less favorable CO2 to oil ratios would not achieve an economically justifiable return on investment. [Kuuskraa et al, 2008]
The supposed 400 billion barrel "technically recoverable" domestic US oil reserve is highly misleading. Most of that mythical resource is tar sands, super heavy, oil mixed 1:20 with water, or as yet undiscovered and purely conjectural.
DOE bureaucrats are in plain denial about carbon capture and sequestration as a practical aspect of enhanced oil recovery. CO2 used in EOR has to be clean and dry, with 2.5% hydrogen sulfide gas, no more, no less. Flue gas (10% CO2 80% nitrogen gas) could be forced into a reservoir to add pressure, but it won't scrub oil as efficiently as miscable supercritical CO2. The chemistry is well understood.
The DOE website that Mr. Burgess quoted so enthusiastically pointed in partcular to a CO2 injection "success story" at Encana's Weyburn Field in Saskatchewan. Let's look at exactly what happened and judge for yourself whether carbon dioxide is the grooviest thing since cheese in a tube. [Screen shots from Encana CO2 Enhanced Oil Recovery Initiative Session, Calgary, March 6, 2009]
Disclosure: no position in energy or industrial gases when this article was written Jan 2010 or since then. Crossposted at http://oilgeology.blogspot.com
Avon,
I, personally, thank you for this post - well written on a technical aspect that some people equate to the second coming for oil. this would be worthy of a key post in itself in HO's "tech talk" series.
I might suggest that you get in touch with Robert Rapier of the R-Squared Energy Blog, as I think this might make a good key post on his blog.
His blog is hosted at Consumer Energy Report, and click the link "write for us" , give the permalink for your post, and se where it takes you.
Weyburn has been the poster child for CCS/EOR, but the fact that it has not been replicated in Canada suggests it is not worth the trouble in most cases.
Alan:
Going past the question of economics (at some point, cost precludes recovery of oil... and that is clearly a moving target. I expect one day we will be extracting negative EROEI oils for use in pharmaceutical and industrial applications, rather than as an energy source for transportation) would you be able to educate me on one aspect that bothers me (or not) about CO2 injection EOR. My question is predicated on the prominence of CO2 in the media as a negative. That is to say, we do not want to add any unnecessary co2 to the atmosphere. So, my question: is the CO2 we are talking about presently existing CO2, and being injected in such a way as to sequester it far beneath the surface, or is it 'new' CO2, that will escape and add to the global mix of greenhouse gases?
Thanks.
Craig
And even if you could increase production by a factor 2 or 3, you would only decrese depletion time. Better to let go of it slowly than cold turkey...
This explains why so many pump jacks are stationary. They are waiting for the well bore to refill with oil, then start again. However, if you look closely at a pump jack and see no rod going into the well, its probably out production and waiting to be removed and well sealed.
A friend has a company that owns a few dozen of these wells in southern Illinois. Many only pump 1- 2 bbl per day. If the well/pump has a failure requiring $50,000 or more investment, the well will be abandoned.
Remember that most of these producers are getting far less than the NYMEX spot price for oil, maybe only $65 per barrel if NYMEX is $100, due to operating cost of well, transport cost to get oil to a refinery, mineral lease of the well, and extraction taxes paid to the state.
So, if the well produces 1.5 bbl per day, the net to the operator may not be even $100. Any major failure of the extraction system and production is over. This will happen to every "stripper well" sooner or later, adding to overall US oil production decline. And remember, many new onshore wells are being drilled with horizontal legs and fracturing (like Bakken formation of North Dakota/Montana) which precludes using pumpjacks effectively.
nb - Your story reminds me of a very low capex way to pump oil from strippers. When the economics can't justify the expense of a pump jack a small operator can go to a portable pump jack. The well had is fitted with a quich latch connector. A tractor has an arm swung over the cab to the front. Tractor pulls up to the well head and latches on to the sucker rods. The line from the power take off on the rear on the tractor powers the stroke. And you don't even need an oil tank: the tractor can also pull an oil cart behind with the production dumping right into it. It might not sound like much of a business but a one-man op might make 6 bopd net. But that's a little over $200,000/year these days. Not bad for sitting on a tractor for 10 hours a day listening to satelite radio. Especially for a guy with a high school degree and a small cattle operation on the side.
Not sure if they are still in business but there was enough demand for this system for someone to start a company up in OK to manufacture it. So much for the oil patch not going after every last bbl of oil.
That's a great story, Rockman. I think when you combine two of the most innovative types of people there are - independent oilmen, and farmers, chances are that there will be some very creative ways to solve problems that the "experts" would never think of. Often because they will simply abandon the issue as not being worth solving.
If I had a well on my property, I'd be looking for a simple way to get the oil out of it too, and if it can be done with equipment I already have, so much the better.
There is no way there would be the same level of innovation (if any) in KSA, Russia, etc. Canada and Australia, yes, but any country where the industry is nationalised and there are no independents, no.
Paul - About 10 years ago I tried to buy a piece of a field SE of San Antonio from a couple that had operated their wells for 23 years at that time. Made about 20 bopd and no water. It was a pure gravity drainage field. As long as the casing didn't rust away these wells would produce for another 100+ years. Tiny pump jacks...less than 2' tall. The husband would run the wells each morning with a grease gun in hand. Sold their oil once a month with about a 20% H2S deduct. Occasionally a down hole pump would break down. Asked him how much to replace. His answer...$812.83. These folks watched the pennies close.
I obvius had no chance of buying their wells. If I paid them a 5 year payout the field would still be worth the same in 5 years thanks to NPV calculations. As long as he could run the wells each morning it made no sense to sell. At a price of $80/bbl they should be netting over $400,000/yr before taxes. And they did run a small heard on their lease on which they lived in a very nice ranch home that was paid off decades ago. Needless to say it was very easy to be jealous of their situation.
I am about as small and about as fiercely independent as they come; thank you Mr. Nash. I spoke to some engineers years ago, including some KSA and Kuwaiti guys and after the presentation I tried to explain to them how it was that I could make money at $25.00 crude oil prices moving 250 bbls. of water per day to make 2.5 BOPD. They had a very difficult time understanding. When I asked the KSA fella what the least amount of oil per day from a well he managed from his field was, he said 2500 BOPD and 25 BW.
One of the ways I can make all that work is by wearing all the necessary hats of operating myself. Short of the same 3 employees I have had for 40 years, as my buddy says it... its a one man operation and I am the man. I say that very humbly, however. I learned structural geology from several good friends of mine and prepare my own prospect maps, confidently enough to spend my own money to drill the prospect. I go knock on the front door of the mineral owner and do my own leasing, occassionally even my own title work. I build locations, hire the drilling contractor, sit the well, log and core and/or test the well, engineer the casing and cementing, do the cased hole logging and perforating, remedial cementing, testing, sometimes participate in the labor to dig ditches, set pumping units and nipple up tank batteries. I learned that by working my entire life in the oilfield and by paying attention. I have made a lot of mistakes, that I paid for, but learned from them and did what I could to not make the same ones again. If the well is OK I do all my own regulatory filings, set up most of my own accounting proceedures, etc. and otherwise operate the well from its inception in my little pea brain to birth and thru its meager life. I don't do many things well but I do all things pretty well. I had an amazing banker that trusted me and most of the money came from borrowing and then lying awake at night worrying about it. I am a lucky man and I do not know of any other country in the world where I could be afforded the privilege of operating my own little junky oil wells. It makes me very proud.
And proud you should be Mikey. And as far as all the different hats you wear folks probably understand you couldn't afford to hire full time employees to handle those tasks because you don't have enough ops to keep them busy full time. But there's a world of consultants out there who would be glad to help Mikey...for $800 to $1500 per day. That's a lot of money for some part time help. Don't know what type of wells Mikey drills but each one of those hats he wears could save him $15,000 - $30,000 per well per hat. It do add up fast.
You can add independent power producers to that list also....
They are trying to come up with alternatives to flooding valleys (Site C Dam project).
and extracting bitumen with zero GHG emissions and a reasonable EROEI.
It is hard to "Connect the Dots" though for the TOD crowd....
Maybe I am on the wrong forum for this complicated innovation ?
Site C (very expensive energy and capacity, ratepayer risk - not needed)
Site C and 83 km of Valley Flooding (not needed)
Load or Market Sink for excess wind and freshet hydro (needed)
Huge Stranded Wind resource in BC (has no market in BC)
Massive interruptable, grid-stabilizing energy load market available in Oilsands next door in Alberta-Saskatchewan (will be needed) if....
There is a market for the end result output.
The Worlds Friendliest Upgraded/Refined Oilsands product..... ULS Diesel that meets and beats Low Carbon Fuel Standards in California.
This is a far better use of our renewable energy, rather than building a powerline down to the California system, instead sell them the GHG offsets and Green attributes now imbedded in the ULS diesel fuel due to best practice, new technology, zero emission extraction methods.
So, to Bring this back to the topic thread - Stripper Wells and what Ghung mentioned above...
Ghung has the right idea. but maybe it should be applied to another resource up north of 49th Parallel (pun intended)
That way, the person filling up their own gas tank can both:
Make a Difference in the oilsands (no more tarsands are evil)
and
This person would then be closer to 100% responsible for the GHG emissions from burning fossil fuels.
That would put the onus for Change on the real culprit in this equation - The Consumer.
Not Industry which is just selling a legal product with huge demand for it.
sw - Interesting but far from my background. I will repeat that the biggest problem striper operators have is applying large capex to their wells even when it makes sense on paper. Many might be able to increase producion X% if they just had $Y. But they don't and the bankers ain't much into lending such money. And the deals tend to be too smal to bring in serious investors.
Stripper well contribution (<10 barrels/day) to the fat-tail of reservoir production rates.

This formula is pretty accurate all the way down the tail.
I have been in the rod pump business for 30 years both domestically and internationally, one thing for sure they differ greatly from region to region in the USA, mostly due to lack of education or understanding. The cheapest piece of the well service bill is the pump, put a better pump in the hole and keep the most expensive piece of the bill off the hole, the rig.
Rockman, the hydraulic units sure look good on paper, Lufkin, Weatherford and Dynapump all have them but the truth is they are fragile when compared to the mechanical nature of a conventional pumping unit, some Lufkin units are still in operation after 25 years, a complex hydraulic unit will never match that without considerable maintenance. The most promising one I have been around is the rack and pinion, linear unit made by Unico.
What kills a low volume stripper wells production is the off/on pumping cycle, during down time formation pressure raises the fluid level in the casing so when the unit is started there is fluid for the pump to lift to surface, but during the down time fluid is not being lifted limiting productivity. The state of the art now is the Lufkin automation system that uses a variable speed drive on the electric motor to control the Strokes Per Minute of the pumping unit based on pump fillage, exactly matching the inflow rate of the well while minimizing damaging fluid pound. A rod pump is the only form of artificial lift that can remove the fluid out of the well bore to its lowest levels allowing the fluid to enter the well bore with what remains of formation pressure and can keep it that way, “pumped off”, and not fail due to lack of lubrication or heat. All the other forms artificial lift (ESP, PC) namely must have fluid over the pump to cool and lubricate them.
Name of the game in the stripper well world as chronicled above is controlling costs and the service rig is the largest portion of that cost
I do not work for Lufkin or any of the companies mentioned above, I do however work for a large rod pump manufacture.
True OFT. For the short time I had that hydraulic unit I had to shut in 3 times due to hydr. fluid leaks. Didn't cost me anything for the fixes but lost 60 bopd while I was shut down. As you say it's the run time that makes you the money. Can't ever make up lost production.
You have much experience with rods in progressive cavity pumps? Good/bad life? I'm thinking the PCP may be the way to go with my horizontal redrills: very viscouse oil, lots of water, and very abrasive sand.
I have some Lufkin 57's that short of some bearing replacements are nearing 50 years old but all are in high volume wells not subject to fluid pounding or gas locking, etc. We monitor our producing fluid levels with acoustic shots all the time, regulate casing pressure and test the units with dynamometers for consistency in rates and fluid levels above the SN. Lufkin is the best.
Mr. Rock, I have two dozen PCP pumps, numerous that have had stators in the hole that are 20 years old or more, one 2000 BTFPD well that has never had the rotor or the stator pulled, not in 27 years, thats a fact. They move clays and some fines, the one inch rods will twist in two occassionally, a drive head will urp now and then and we'll rub holes in the tubing every 6 months but I intend to put mine in a museum when it is all done. Again however, these are sweet, low gravity wells with no parrafin issues. Imagine 20 years without pulling a pump? Gotta love it. Sorry OFT.
Mikey, you got your self a water drive and I totally understand what your saying, that long of a run with a PC has got to be a record, well done!!!
Rockman, rod pump applications is what I do for a living and there are more questions I will have about your application than you will want to air here, I will want to send you a well data sheet for you to fill out so I can do some predictive modeling.
I will be the first to admit that the PCP pump can flat move heavy oil and sand but there are temperature limits with the rubber stators in steam floods (unless you want to trial a metal to metal) and no mater of the material construction or bottom hole temperature they cannot take being pumped off, they will need fluid over them and any fluid level left in the hole will limit inflow and we are capitalist, we want it all! The company I work for has a patented adaptation of a standard rod pump that is performing miracles in those old unconsolidated sand formation steam floods in the San Joaquin valley on the left coast moving 30% sand and pumping the zillion pounds of flow back frac sand in deeper shale plays in the Bakken, Cotton Valley and Barnett.
From my experience with horizontal wells the key to maintenance free long term production has more to do with well bore geometry than anything. If you build the curve to sharply you are going to have rod/tubing issues regardless of lift type that are going to kill anything you do around long runtimes. I have help set up wells that run for 24 months without a problem and other that will fail in 6 weeks due to rod/tubing failure. There are things on the horizon that could change all this.
Bottom line is either PCP or SRP will work but the devil is in the details and the biggest devil is well bore geometry. Case and point is the hundreds of Barnett wells here that could have a long life using conventional well understood production techniques if they could just move 10 BPD fluid but can’t due to outrageous well bore geometry.
OFT -Actually my project is very simple. No pump off: powerful water drive will make 2,000 bfpd ...could pull 10,000 bfpd if I ran 5 1/2" tubing. The PCP would be in the vertical section. No temp problem: reservoir is at 5,000' with fluid levels usually standing above 2,000'. What killed previous attemps was the plugging of the screens in these open hole hz completions. In between 95% water cut stripper wells an operator completed 6 hz wells and tested 175-225 bopd with vavrious water cuts. But all the screens plugged immediately with fines. But I have a proven method to prevent that now. One operator in the trend replaced his ESP's with PCP's and increased his run time from 60% to 95%...the sand really chews up the ESP's. Gas lift is always prefered but not always an option.
What I need to prove is production decline rate that makes a good return. The hz won't stop the coning. You actually need the water flow to carry the oil out of the reservoir. The goal is rate. As water cut increases I would just keep upping production. Even at 90% water cut if I can still produce 200 bopd. So I can start at 200 bopd and end up with 200 bopd at the high w/c. The question is the time time span: will it take 3 months or 18 months to run that span. Can knock out models all day but as a production hand you know a paper model doesn't mean anything...the gauger reports will tell all. And obviously SW disposal is going to be the big LOE factor: have to be able to justify SWD wells to make it work...more capex. If the pilot project proves the idea I have a couple of hundred proven locations that can be leased for next to nothing. And that could generate 30 million bo recoverable. What dreams are made of, eh? And that would still only an increase in URR of less than 5% (a 54% RF up from a 50% RF).
Rockman, sorry I have been traveling, just got to my destination and now if I could just get the body clock to reset 10 hours… At that depth, fluid volume and no pump off you would be better off with a high rate PC if particulates are a concern. A SRP system would be at the largest the industry makes and a lot of CAPEX, I ran it through my predictive software and it is possible but my experience tells me for this application PC would be the better option. In my experience any particulate exclusion devise on the pump intake usually tends to plug off and starve the pump, if a PC is in mind I would not put anything on it and deal with the sand on surface. I sure would like to know more about your screen on the pump intake.
OFT
Thanks OFT. I've been occupied too with a bad lost circ problem on a barge job. I used to be able to run 48 hrs with a few naps. No more...not at 60 yo with bad knees. LOL.
Hi All,
Nice to see a discussion about stripper wells and their economics.
My field in central Texas produces from about 300 to 700feet. Oil is 38 gravity, sweet, and the color of "British Racing Green" paint. Virtually no water is produced as we have a solution gas drive. Pumpjacks are small #6.4's or #10's. About 20 years ago we would frak the well with 4% KCL water, sand and no gel because there was not a gel available that would break around 70 degrees F. We could get about 4,000 lbs. of sand in before screen out. NOW there is a gel that breaks at 75F which allows you to get about 40,000 lbs. of big sand in. The wells come back at around 7-10 BBLs/day flush and settle down to around 2 BBLs/day after a year. I know this amounts to nothing on the "Big Oil" scene but you can drill and complete one of these for around $38,000.00 using a water well rig and air, so it's fun and at these prices economic to do.
To me it seems that a small refinery could produce enough diesel and lubricants to keep the county agriculture going and then some, There are many areas that have shallow oil and gas that I think something like this could work.
Best To All, TS
TS - that is a very sweet set up. Sounds like you pay out in less than a year. Any chance to expand to other reservoirs in the trend? I've got money burning a hole in my pocket. Could bring enough capex to the table to drill 500 wells the first year...if we can get the leases/rigs. If it's as good as it appears we could even build our own rig company. My owner is getting into the frac tanks biz because we can't find enough wells to spend all our capex. I've got over $100 million in my budget left for this year and I doubt I'll spend half out it. And another $150 million to spend next year.
Well...did that 2 X 4 get your attention? LOL
Hi Rockman,
WOW, that 2X4 is like the whole tree! We do pay out in about a year if you drill about 5 or 6 at a time. As I mentioned we use water well rigs 1000 to 1500 series using air compressors (its fast drilling that way). I will be buying a nice used rig next year, but for now we are starting to frak the old wells that came with the property. Another operator right across the river from me bought the land that has the discovery well on it drilled in the 20's. He cleaned it out - old tree stump or something- ran a new tubing string in with packer and did the "new" gel frak this spring. Last I heard he was doing around 5 BBL/d. and this well has sat idle for about 30 years!
I appreciate your offer, but I hope to have my sons join me some time down the road. I bought this lease a few years out of college - just in time for the oil crash of the 80's and had to build houses, fences, or clean up around dumpsters at shopping centers to make ends meet. It was so bad not all that long ago that I offered to give it to another operator just to get away from the damn thing. He turned me down saying the plugging obligation was more that it was worth, so to him it had negative value, and everything was paid for at that time !!! - Remember those days? I am NOT the person to complain to about high oil prices ;-). Now that the cash flow is building, I'm excited about developing the lease just to see what I can do with it. I hope you understand, but contact me through e-mail and maybe I can help you find something, but it sounds like you have the rod and tackle for larger fish.
Best Wishes, TS
TS - Yep...easily remember the bad ole days: started in 1975. Wasn't thinking about jumping you claim. LOL. Sounded like you wouldn't have trouble funding your ops. Was thinking there might be more fields on trend you don't own. I'm serious and will send you an email tomorrow. We can't mess with a half dozen of your wells...I need to drill 500...at least. And we're a low manpower shop...I would need all the boots on the ground you could dig up. Maybe even your boys if they're ready to break out. LOL.
TS What pumps style are you running? My guess would be a 20-125 RWAC 6-2 if it is a metal to metal or you are going old school with a cup and ring plunger. Either way I bet they last a long time in that sweet low water cut fluid.
OFT
Hello Rockman and OFT,
Sorry for the delayed response, was out in the field checking wells. Sorta in the middle of nowhere with limited internet, so I don't even take the laptop anymore.
OFT: Talk about "Old School" we use to use tubing pumps with 4 cups looking up but have since gone to 6 foot inserts rigged top hole down. We Have 2 cups looking down and 2 cups looking up with rag rings in between. Running a chrome lined barrel we can usually get a couple of years, but I have a couple sweethearts out there that are going on 7 years and will still go to 500+ psi. Rods lock in stuffing box at that pressure. I have not tried metal to metal but most of the time I hear the barrels chew up pretty fast. Our sand is like talcum powder and gets between the barrel and plunger, but some operators swear by them.
Rockman I look forward to visiting with you and will help you as I can.
Cheers, TS
Hello OFT,
I saw up thread where you were talking about some old Lufkin pumping units. I use to operate a lease in Sulfur Bluff around 20 years ago that had Lufkin 228's serial #'s 0001-0004. Number 5 was out there also I believe, but was out of service. They looked like - well, you know - pumping units, but I'd be willing to bet they are still on duty pumping away!
That was a crazy lease. We had two twenty thousand BBL SW tanks hooked up with 36" diameter crossover pipes, and 4 triplex disposal pumps using 5 1/2" casing as tubing. If the disposal pumps went down we had around 6 hours to bring them back online or start dumping to a huge open salt water pit, or shut things in. The lease made about $16,000.00 a month and the light bill to run the REDA's and disposal wells cost around $15,000.00.
A bank I was consulting for had foreclosed on this property and asked if they should sell it. They were owed something like $2,000,000.00. I told them Hell yes and I think they took $1,000.00 for it and quit foreclosing on oil properties.
Still those were some cool pumping units to see!
Take Care, TS
TX Sweet, I bet the boys from Lufkin would love to see those, I know some time back they were looking for the oldest pumping unit still active they made, if i'm not mistaken they found it near Kilgore and re-built it for free. I too love Lufkin units but as I mentioned above I sure like the looks of that Unico unit, it has some very advanced control features that are very rod/tubing/pump frendly
One thing most folks forget is that over 70% of artificially lifted oil/gas wells use a rod pump. Many types of lift methods have been invented, made a splash and faded away as their issues come to light mostly due to reliability, rod pumps are just rock solid simple but the key to a successful application is in the details,
OFT
TX Sweet, I expected an “old school” cup and ring set up with shallow wells like you have but two year runs can be improved on if you are pulling the wells for pump failures, if you are pulling for rod or tubing failures not the pump then no sense putting more money into the pump. A metal to metal pump with the proper materials will always out run a soft pack pump. For shallow sandy wells there are many options; 1st chrome ID barrels are in order due to the hardness, it will resist wear from the produced particulates, sand is silica and harder than most materials pumps are made from. A standard API pump can be improved by adding a wiper to the metal plunger to keep the sand out between the barrel / plunger interface. 2nd there are several specialty pumps like a “Texas Stripper” for low volume wells with periods of shut down, or a “Pampa” that has a long plunger and a short barrel that will out run an API pump but will suffer from gas interference if it is present at the pump intake. End of the day I bet I could double your run times all things being equal. I would be happy to look at your specific application if you would fill out a well data sheet for me.
Regards
OFT