Tech Talk: Supporting Underground Tunnels
Posted by Heading Out on September 5, 2010 - 10:38am
With thoughts of the miners in Chile, and suggestions that a rescue tunnel will also be started to try and drive down through the broken rock, I thought I would write a little today about holding rock together. For those of a slightly cynical nature, I recently used the example of the Forth Road Bridge, in comparison with one of the bridges that the Romans built in France. The latter is over 2,000 years old and still standing, the former was built in 1964 and is now being scheduled for replacement, since the cables in the old one are corroding and snapping. The point of the comparison being that if you know what you are doing with rock, you can build a structure that can carry load for a long time. (And if you think about it, the rock that the Romans built with is bits of broken rock, rather than the solid structure that a tunnel starts out drilling through).
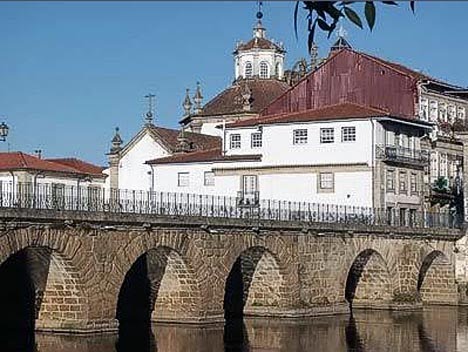
When man first started digging into rock, whether to get flints, create shelter or extract some coal that would burn, it was a relatively slow process. The miner relatively slowly dug out the rock, giving the loads around the hole some time to redistribute, and small holes could be made that would be stable for a long time. That is only a generalized statement and not always true, there are several factors that limit its validity. The first is water. Of the underground hazards water is one of the worst. In its most visible form it can fill the hole, and drown all those in it. There have been many disasters where water has invaded a mine, either from the surface, or from nearby underground workings. (For example Quecreek).
But water has a more insidious role underground, travelling into the mine with the air that the miners must breathe. Underground the ground temperature stays quite constant, and for many mines nearer the surface, the temperature can be quite cool (one I was in recently was at 58 F). So in the days of high humidity of the summer, the moist air moves into the mine, meets the cooler rock, and the moisture condenses onto the rock. It soaks into the rock, and usually weakens it – some shales (the more common rock in coal mine roof) will lose 60% of their strength when they get wet. And it is often why there are more accidents from roof falls in the summer – while in the winter it is more the time for gas explosions – another story).
The second problem that affects the rock relates to the number of cracks in it. If you drive along a road and pass through a road cut where you can see the cracks that develop around individual lumps of rock. Some, the bedding planes, are formed when the rock was first laid down as a sediment, some were formed as the rock was twisted and distorted over geologic time, or during the time that it changed from the sediment into the rock structure encountered today. And some cracks are made as the opening in the tunnel is made. We want to break the rock in the tunnel face into small pieces that we can pick up and carry away, and so we place explosive in known patterns of drilled holes in the face that will break the rock into bits, when the explosive is set off. Generally the charged holes are set off in a sequence, so that after breaking out the middle of the face, successive rounds (they are set off with timed detonators) will blast successive layers of rock into the opening until the desired shape has been removed. In the process some cracks from the outer ring of blast holes will extend out beyond the intended wall of the tunnel and into the final wall. (Seems to happen more on Mondays and Fridays for different reasons).
So there are several concerns that face an engineer that is going to try and drill a tunnel through rock, whether it is solid or already broken into boulders and smaller pieces. The first is to get some idea of the general strength of the rock – designs that work in something like a granite won’t work in a very weak shale, for example. Once the rock strength is known, then the amount of cracking, either natural or man induced needs to be found. There is a very simple way of doing this that a group at Urbana/Champaign developed called the Rock Quality Designation (RQD), under Don Deere to simplify how it is measured, you drill a core through the rock layers that you want to drive the tunnel under. You recover the core and measure the core lengths that are more than 4-inches long. That total value, divided as a percentage over the length of core recovered gives you the RQD. Over time (it is now 40-years old) it has been shown to give a very good first estimate as to how badly broken the rock is, and it is used in many design programs to decide how best to hold the roof up.
When working out how to hold the roof of the tunnel up, the engineer knows that he is not trying to hold the weight of all the rock between the tunnel and the surface. The work that most of us used to refer to as the basis for the support of the tunnel was written by Karl Terzaghi. Again, to simplify a relatively complex subject, he came up with a simple method of classifying rocks so that, the designer of the support would know how much rock load from above the tunnel, the supports would have to carry. And very often it was only a small additional amount above the height equaling the width of the tunnel. (The presence and actions of water being the main factor that would make it a lot worse).
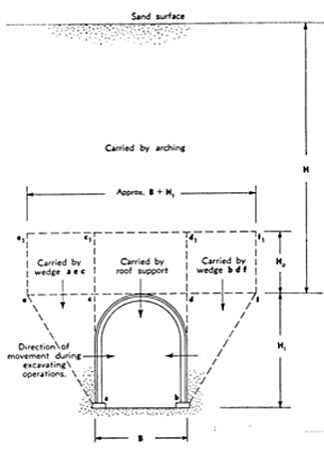
Karl was starting the knowledge base that now allows engineers to classify rock and thus design the tunnel supports before the tunnel gets started. It was only a start, however, because back in those days (beginning in 1925) most of the tunnels were supported with large steel arch girders. Because those had to be ordered and delivered before the tunnel was started, getting that size wrong could be very expensive, and there have been many lawsuits as to whose fault that was. (Very awkward, for example, if the tunnel is half-way under a harbor when you discover the steel beams aren’t big enough).
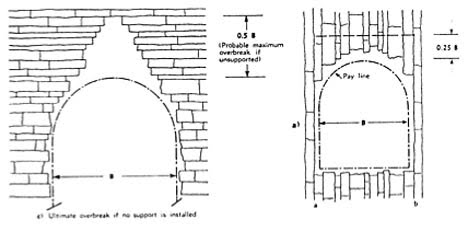
Since then a new method of support, which works more on helping the rock to support itself, along the lines of the Roman arch bridges, has been shown to often be more effective. Although it has been generally more effective, and more flexible, it has become more popular, but I will write about it, and the change from steel arches to sprayed on concrete (shotcrete) and rock bolts, next time.
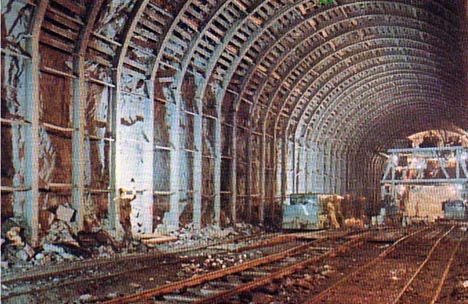
I thought I would write a little today about holding rock together.
I've read this gent's book:
http://www.romanconcrete.com/index.htm
Seems part of the secret sauce was the constant tamping and less water.
You could always try adding starch to your concrete.....
http://www.physorg.com/news194411869.html
Or you could try stacking the rocks with some sand, bacteria, Calicium and Urine.
http://creation.com/sand-to-rock
http://www.popsci.com/environment/article/2010-05/new-bio-manufactured-b...
(Perhaps Greer should be asked operative mason questions)
Thanks for the reference, I'll take a look.
The roman concrete book will be more useful than the other 2 references - I toss out the other 2 as 'outside the box' thinking.
It is named Christian Louboutin for the reason that man who create Christian Louboutin shoes. At the same time, it's helpful to reduce the risk of injury for the player. If you think your feet should be protected well during the strenuous exercise, the Christian Louboutin Pumps are the right choice for you.
There are many Cheap Christian Louboutin Heels from our shop. If you want to learn more informations of those Christian Louboutin Boots, please visite our website http://www.louboutinshopsale.com/. Are you looking for a comfortable shoes? We are ready for you to give you great discount Christian Louboutin Sandals and best service.
As I learned from "Life After People", yes I'm a proud Doomer and its one of my favorite shows:). The Romans used volcanic ash (very fine silicate powder) in the mix which made the concrete highly non-porous and thus kept out a lot of the moisture that breaks down concrete during freeze-thaw cycles.
The show also related that one of the major causes for breakdown of modern concretes is that the same metal re-enforcing that gives it its strength, corrodes when water gets in and helps to break down the concrete as well.
If one 'digs around' in the links I posted you'll note references to Bamboo being used to provide tensile strength to concrete.
Alas, the cell walls would expand and contract with H2O exposure over time I imagine. :-(
But parts of the Great Wall of China are did use such material and last I knew the wall was still a Great Wall.
Using aggregate and sand from beaches is also a problem - salt messes up the concrete's setting, and when it's mixed into the concrete, the concrete is weaker.
I was working with a Lithuainian whos father was also a bricky. He told me in the winter it was common to have minus C temps. In England they stop work if the temp drops below 4C because the cement becomes weak so I asked him to ask his father how they managed to work in the winter. The reply came back that they mixed salt into the cement!
Calcium chloride actually. Up to 2% can be added-- Two per cent defined as two pounds 77-80% flake material per 100 pounds of cement. Adding more CaCl2 as an anti-freeze is more than frowned upon but that doesn't mean it isn't done. Concrete strength will suffer. Too much water in the original mix also is detrimental to concrete strength. But we love building rocks and will keep fiddling with 'new and better' mixes. Some of those will actually be such.
We pour plenty of concrete in cold weather here in the subarctic. Heated plastic tents and insulated blankets are used extensively.
I have wondered just what the long term effect of 2% CaCl2 might be. We add all kinds of stuff to concrete these days-plasticizers, superplasticizers and on and on. Just how well can a lab predict what those substances will do to concrete strength a century or two down the road? I'm guessing that time frame is beyond the engineer's consideration, but it would seem there must be some trade offs.
Article below describes a "new" flexible concrete which is supposed to be very durable and is made with very fine silica sand but it is 3 times as expensive as regular concrete.
http://discovermagazine.com/2005/aug/concrete-gets-flexible
To slow the corrosion of concrete due to rebar corrosion now rebar in roads and bridges use epoxy coated rebar. Care is needed when handling to avoid nicking the epoxy and creating a focus of corrosion.
My driveway has concrete reinforced with tiny fibreglass shreds (but I still called for the usual welded wire mesh just to be safe).
500 times more flexible than regular concrete--interesting
deleted
Regarding the epoxy rebar, how do they handle the coefficient of thermal expansion?
Off the top of my head, CTE for rocks runs around single digit ppm, for metals around double digit ppm, and plastics around low three digit ppm.
So very superficially, I'd expect hot cold cycles to first crack the epoxy, then as the steel corrodes the rust will crack the concrete.
It sounds possible that the rebar steel, concrete, and epoxy are all specially designed to match each other, or perhaps building codes only allow that kind of stuff in coastie areas where the temperature never varies too much?
I'm just idly curious.
I've worked with epoxy bar in bridges and there are issues with it. Some rebar has to be pulled through some very tight spots so some epoxy get scraped off. In theory this probably is supposed to get recoated in the field-sometimes that would not be possible regardless how conscientious the workers might be. My guess is there is enough real world data out there by now to show how much epoxy coated rebar reduces the corrosion problem. We are still using it so it must justify the extra cost and inconvenience of working with it--the epoxy coated tie wire is a bit on the slippery side as well. The epoxy coating on the bar is pretty soft and flexible feeling so expansion differentials might not be too big an issue. And the coating is a rather pretty color of green ?- )
Roman bridges were admirable to be sure, but can they be reasonably compared to modern bridges on an interstate highway that must withstand millions of tons per day rumbling over them, especially in tractor-trailer trucks? The old Roman bridges I saw in Italy were only carrying foot traffic, bicycle traffic and the occasional tiny Fiat car.
And may well again...
Many of the, often very tall, stone railroad bridges built in France in late 19th century still stand. Plenty of load and vibration there as train traffic is heavy.
Comparing a suspension bridge with a stone bridge is inherently unfair.
If one is inclined to find things that can easily be brought down, just look around for metal in tension. Structures which are suspended or guyed with wire rope are always in peril.
Of course, if the metal in tension is corrosion resistant, like stainless steel, and if it is installed at a relatively low loading, to mitigate fatigue and cracking, then it will last for a long time.
The missing drill pipe below the BOP at the well site with the big blowout seems to be an example of what can happen to metal. Apparently it became very fragile under the conditions to which it was subjected.
or it was never there, because it was cutoff during the initial operation of the BOP, at the time of the blowout, and fell to the bottom even before the DWH sunk.
Most suspension bridge cable wire as I recall is (non-stainless) steel. Why of course is that its cheaper... I'm not sure about a structural comparison in tensile strength, but as in most things it boils down to how to do it the cheapest.
Paint seems to be the corrosion preventative most used, and without constant maintenance, the paint will begin to crack and fail relatively quickly which lets moisture in with a predictable result.
The Golden Gate Bridge is galvanized steel wire. Main Cable Recoating Project
Engineering is the the discipline that gets things done. Specify the performance and engineers can calculate the cost. "Stainless" steel isn't completely free of corrosion, it's expensive, and its mechanical properties make it harder to use than galvanized mild steel. For an engineer the right question is not "Will this wire ever rust?" It's "Will this wire do the job I've designed for it, for the design lifetime of the structure?" The original galvanized wire cables have been supporting the Brooklyn Bridge for 127 years.
Pictures of the mine in Chile seem not to show arch-work bracing.
1. Is this true? (I'm working from memory and could be simply mistaken.)
2. If true, what is it about that geologic formation that allows them to avoid the expense of arch-work?
Igneous rock.
That's next week's topic.
I read in the news this morning that they are now considering a third path to rescue the miners, using a pipeline boring rig. I would think this could work well even in this hard rock, AND the cuttings would be removed upward. Another path of tunneling toward the miners indicates a saving of 100 meters of drilling by inclining the borehole path. I hope the best and safest-possible alternative path reaches them sooner than the original 4 months estimate.
As soon as it reaches them and they get out the sooner than can resume a job where they will get paid.
(my way of mentioning that, according to reports, the mining company isn't paying the trapped miners.)
deleted