BP's Deepwater Oil Spill - The New Plan: Shears, Working on the Riser, and Wed. Open Thread 3
Posted by Heading Out on June 2, 2010 - 8:09pm
This is a repeat of earlier threads, but see that updates have been added throughout the day both on top and under the fold--we kept the same post/information in one place since we are running through three comment threads or so a day.
There has been a lot of activity at the bottom of the Gulf, not all of it immediately successful, but all working toward the current aim of being able to field the Lower Marine Riser package. That installation requires that the broken existing riser that connects to the Blowout Preventer (BOP) has to be removed. The bent riser has been exerting some lateral pressure on the BOP, and this might be relieved when it is cut off. To minimize the damage, the first cut is therefore going to be further down the riser, provided that they get the saw "unstuck," which it seems like they might have done, but no word yet on when cutting is to resume.
UPDATE: 5 pm Wednesday: I have added new material explaining how the diamond wire blunted, and how they might have fixed it, but now won't. They are going back to the Shear.)
(My post continues after the video. Please click, "There's more".)
UPDATE: 1 am Thursday: New plan. They are going to go with the big shears instead of the diamond saw for the cut. I have been intermittently watching for the past couple of hours, while doing something else - they were prepping the Shear, and I think reconnecting the power lines from the Shear to the power pack. Now, I believe that they are lowering the ensemble to the riser on CNN.
VIDEO BELOW FOLD
http://www.cnn.com/video/flashLive/live.html?stream=stream/3&hpt=T1
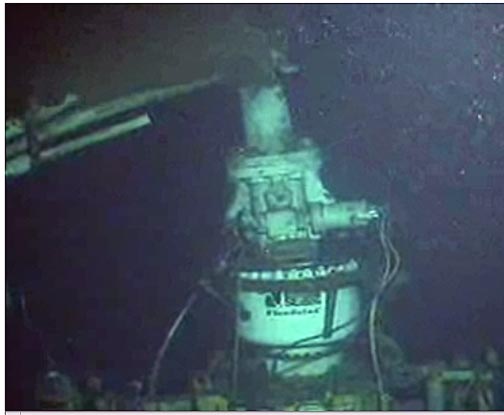
I described the plan of attack in an earlier post, and what has happened, over the course of today has tried to follow that script. I say tried, because there have been a couple of glitches that developed over the course of the day. The large shearing machine (apparently owned by BTI) appeared on the scene, and in preparation for its use some of the pipes surrounding the main riser (the choke and kill lines) were first cut away using a diamond saw.
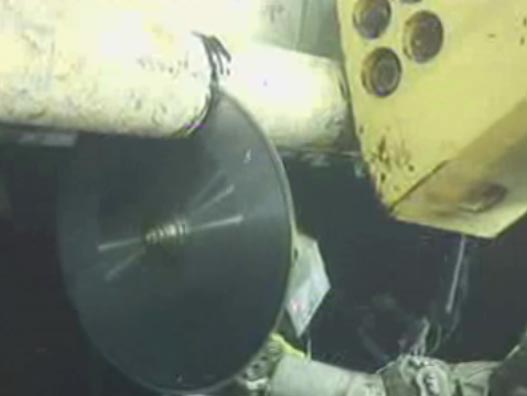
At the same time that this was going on, the wire saw that would make the final cut on the riser had been brought down to the site. The riser assembly has been cleaned of extraneous pipes already, and the wire saw would fit about the flange and below the bend.
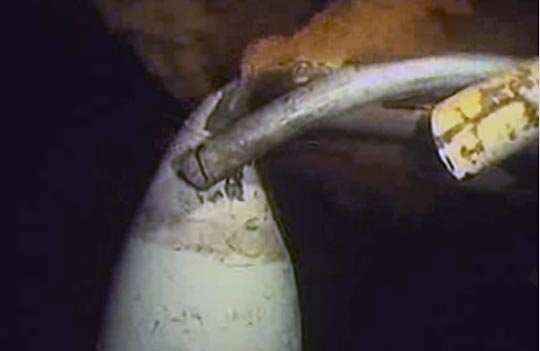
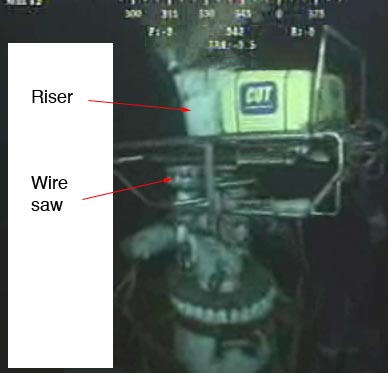
It was now time for the shearing machine (which I’m going to call a Shear from now on) to fit around the riser and to make the first cut through the pipe.
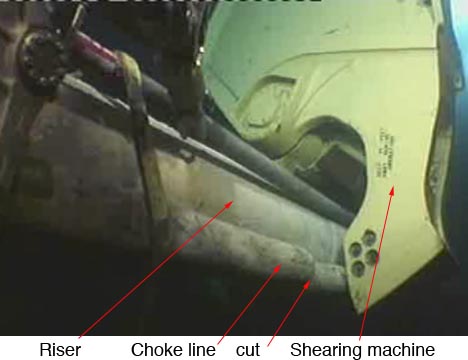
Unfortunately the first cut did not appear successful, although there was a cloud of oil and gas released, indicating that the riser was at least breached. There was a pause, and the Shear moved to a new location closer to the riser. Again it tried to shear through the nest of pipes, that now included choke and kill lines. It was not successful, and returned to the surface where it was fixed, and returned to the site. UPDATE 1: Having written this post and not seeing much happening I went off for a couple of hours. On my return (and before Gail posted it), I did not check again and as the notes below show, the Shear worked at 7 pm. At 10:15 pm the wire saw was cutting through the riser. I apologize for the errors.
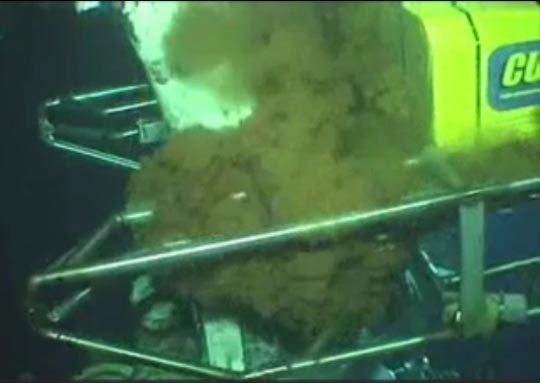
END of UPDATE 1 UPDATE 2 below> In the meanwhile, a little calculation, based on reports that the White House has announced that the removal of the riser and drill pipe that are protruding from the Blowout Preventer (BOP) of the Deepwater Horizon well in the Gulf may increase the amount of the petroleum leak by 20% when the riser section is removed. There are two immediately obvious reasons why this might be the case.
The first of these is that there is a small amount of oil that was leaking up through the drill pipe that extended beyond the broken riser. That flow was one of the first things capped in the remedial effort. It did not have much impact on the overall flow volume, since the flow merely backed up and increased the flow through the main crack in the riser, but there may be a small increment of flow when this channel is re-opened with the cut below the fold in the riser.
The greater change in the flow, however, will likely come because the riser and DP, while not providing much increased resistance, did raise the pressure on the downstream side of the BOP by about 500 psi. We know that though the pressure down at the formation was at around 12,000 psi, up on the upstream side of the BOP it fluctuates in the 8,000 to 9,000 psi range. The higher resistance on the downstream side, reduces the pressure drop across the BOP by that 500 psi, and the flow rate will be reduced accordingly (the gap size through the BOP is assumed not to change).
However, if the pressure drop across the nozzle was at 6,000 psi in the current condition, (which with an orifice size of 0.6 inches, would give a flow rate of 512 gpm), then raising the pressure drop by 500 psi would only increase the flow rate to 532 gpm, or a difference of 4%--which might suggest that there is something about the drill-pipe flow that was initially capped which we don’t know yet. Alternately it may be that they think that removing the bend in the riser might ease the forces on the BOP, relaxing the metal a little and increasing the orifice size. After all it has only to open up by another 0.05 inches to give the increase in flow that the White House are predicting.
UPDATE 2: Sometime about midnight it appears that the cutting wire stopped moving and may be jammed in the cut, roughly half-way through.
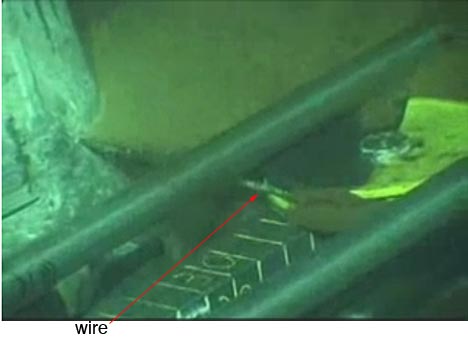
UPDATE 4: On other feeds they are showing that a second cut is now being made by the wire saw, but the camera is further away. BP is predicting that the cut will be completed today and the LMRP installed. But it doesn't look good that they are still working with the Shear, because they can't use that for a final cut, and it implies that they may be having problems with the second cut also.
UPDATE 5: Part of the problem was apparently according to a BP spokesman that the cut through the first half had dulled the blade, so that when they got it restarted it would not cut. (What we do in those circumstances, which are not uncommon with diamond blades, is to run the blade through firebrick, and this erodes the material into which the diamonds have been pushed, and sharpen it. Then we drop the cutting pressure a little.) However, BP's current answer is going to be
The technician said that rather than trying again with the saw, the plan now was to use a large shear to cut the riser. The shear, which is about 20 feet long and nearly 10 feet high, was used to make an earlier cut in the riser about 50 feet from the wellhead. Because the shear will not make as clean a cut as the wire saw, modifications would have to be made to the containment cap that is to be lowered over the cut pipe. But the technician said that even with the switch to the shear and the modifications, he expected the containment cap could be in place by Thursday.
Oh, and I mentioned earlier that an ASJ system had cut through casing and pipes at the bottom of the North Sea. I had the orientation of that cut wrong (at least for the picture below) since in this case it was from the outside in, but I am aware of it being successful the other way. And so here is the picture of casing and cement cut by an ASJ. Sadly it was so long ago - around 23 years, that I can no longer remember exactly the pressure it was cut at, but I believe it was 5,000 psi. And to answer a comment because the nozzle is non-contact, the surfaces it is cutting don't have to be cylindrical.
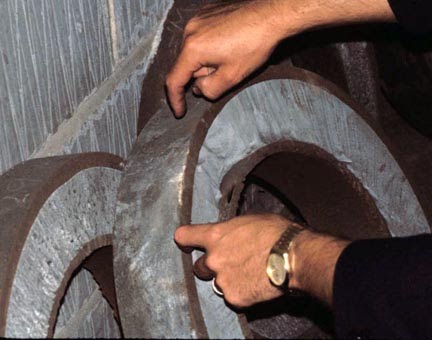
A continued sincere thank you to all who have donated thus far. It will help with the increased costs we are facing (see point 3 below).
1. The Oil Drum is a pretty special place. We strive to maintain a high signal to noise ratio in our comment threads. Short, unengaging comments, or comments that are off topic, are likely to be deleted without notice. (to be clear--engaging, on point humor and levity, more than welcome.)
We are trying to perform a service to the public here to coordinate smart people who know their stuff with other people who want to learn about what's going on. Promotion of that ideal will be the criteria by which we make our decisions about what stays and what goes.
Flame wars, polemic exchanges, and other content deleterious to the community will be removed, either by an editor or by the community through its moderation process.
2. If you see a problematic comment USE THE COMMENT MODERATION SYSTEM--see the "Flag as inappropriate" and (?) beside it? Learn more there. If you see comments that are questionable after you've done that (that aren't being removed), let us know at the eds email address.
It is up to this community to enforce the norms we have established here (a high signal to noise ratio), keep. it. up.
Our guide to commenting at TOD can be found here: http://www.theoildrum.com/special/guidelines . Please check it out if you are unfamiliar with it, but it is essentially 1) citations welcome (if not necessary), 2) be kind to others, and 3) be nice to the furniture.
3. We have gotten a lot of queries whether this bump in traffic is adding costs to keep the site functioning. Truth is, yes, we are incurring added expenses from these events. It is also true that we try not to beg from you very often as we are not the types to bother you with constant queries.
That being said, if you are inclined to help out, your support is always welcome and very much appreciated. To those who have already given, thank you very much.
You can find the donate button in the top left hand corner of the main page.
4. If you have come here to vet your plan to kill the well, understand that you will be queried on whether or not you have read the other 10 previous comment threads and all the myriad plans that have already been run by the kind folks in this room; if you have actually read all 10 comment threads and still think your plan has legs, well, then maybe yours really is the one that will save the Gulf of Mexico.
This is not to say that well considered questions about current attempts and modifications to those attempts are not welcome; they are. But try to place them in context and in what's actually going on, as opposed to your MacGyver dream solution where you have a 10 megaton bomb, an ice pick, and Commander Spock at your side.
5. Also, if you're looking for live chat to talk about the ROV/LMRP video, etc., and are IRC capable, go to freenode, the channel is #theoildrum
(google MIRC and download it; Hit the lightening bolt and fill in your info; select the server as "freenode" (it is in the server list), hit connect; when connected type /join #theoildrum)
or you can get there just via a browser: http://webchat.freenode.net / Just enter a nickname and #theoildrum in the boxes.
6. Do not be afraid to go back and read the last couple of open threads yesterday and today before you start on this thread. They are really good, and will likely catch you up if you have been out of the loop for a while. We shut down threads when we get to 300-400 comments, as it's really unmanageable. Lots of good stuff in there though.
as an unimportant aside: Xchat is also available as an IRC client and it is free, mIRC will only work for i believe a 30 day eval before you must purchase. if you're like me (read: poor and/or cheap) you may wanna try XChat, i also feel it is a superior IRC client.
FYI - My Discussion Forum uses parachat - http://chat.parachat.com . It is registration optional if you want to make it a private chat (keeps undesirables out). It is free, quick to setup, and easy to use. See their basics overview page for details - http://www.parachat.com/basic/
Not trying to endorse one client over another, I'll just add this for those who might be looking for options. I use Pidgin, which is free and open source, and handles all or nearly all IM protocols as well as IRC. It's available for Windows, OS X and several flavors of Linux.
I've tried several times to get on the webchat.freenode link. However, all it does is show me my nickname and nothing else. Do I need to do something else? I know it is a waste of your space to chat while looking at the video. Thanks.
once you're connected you will notice that if you type anything i.e. "Hello World" it will say Not Connected. you will need to type the follonwing:
/join #theoildrum [enter]
thanks.
Can someone clarify whether "8,000-9,000 psi" is an absolute pressure or relative to seawater pressure at the bottom. My notion is that it has to be absolute.
A pressure of 9,000 psi ABOVE the seawater pressure would create an incredible flow, far more than we see in the videos.
Thanks,
DAW
Water is roughly 1 psi per 2 foot of water, 5000"=2500psi
[Carrying on from conversation started in last thread where I proposed wiggling remaining riser up and down until it breaks, leaving an easier job for saw or spanner.
And in reply to newdood who warned that this might weaken the BOP, which is a valid fear.]
Thanks newdood.
Yeah I thought that too. That's why I said GENTLY. I also think it should be carefully monitored and stopped if the BOP looked like breaking. (I don't suppose there'd be any way of stabilising the BOP first? For example pushing on its opposite side with the ROVs to oppose the force being applied.) But when you consider what a lot of stress the whole assembly has survived so far...just a teeny bit more.
Also, the kinked area could be weakened further beforehand by e.g. "nibbling" at each of the squashed sides with the end of the shear tool.
I just want to point out that the riser is mounted to a flexjoint. I'm not sure how much resistance there is in that joint, but to put any stress on the bend one might have to move the riser enough that it hit the hard limits of the flexjoint (minimum of +/- 10 degrees).
The flexjoint apparently was strong enough to survive the leverage applied by a mile of riser which came crashing down. The thick steel wall of the riser by contrast is quite clearly fractured at that point.
Is anyone watching the video from http://mfile.akamai.com/97892/live/reflector:46245.asx I think it has the best quality. It appears they are currently showing the release of dispersant underwater. I came up with that conclusion by the screen that says "Dispersant Ops." First time I've noticed that.
http://www.mms.gov/tarprojects/377/DeepSpill%20Final%20Report.pdf
Link cited by NYT(http://green.blogs.nytimes.com/2010/06/02/evidence-of-undersea-oil-plume...)
159 pages so it takes a while to read, but excellent study of deep blowouts and underwater plumes in which MMS and BP(allegedly) participated.
MMS certainly had a number of studies warning of the hazards of deepwater drilling.
At some point an expose will come out showing how much the MMS and USGS do not get along. Kind of like the firewall between the FBI and CIA. I and another long-time oil depletion analyst have received some insider accounts of what is going on there. I have always wondered about this bit of parenthetical info I received from a guy who works at MMS:
I guess this means that they collect all the lease fees. No wonder they have no time to do any work on real oil depletion analysis
Less than 1000 people and all they probably do is keep track of permits and leases. It makes sense why all the real oil depletion analysis is posted by dedicated amateurs on TOD.
Thanks for that Deep Spill Report.
One of the regular questions, okay, complaints, is BP should be telling us more about what is going on. Especially with regard to the ROV work at the BOP. The problem is simply it is illegal for them to do that. All public corporations are required by law to disclose information, that might affect their share price, in a manner which allows everyone access to that information in a format that is easily accessible and widely distributed. Typically a news conference or press release covered by the major media outlets.
The information also has to be understandable to those who might want to buy or sell BP stock. As many of you have seen, what is going on at the BOP is anything but easily understandable. That's why there is no running commentary coupled with the ROV video. It would be illegal. Instead, you get one or two press conferences a day that are general updates, and they don't go into a lot of detail about the odds.
At least that's how I understand it. We have several good lawyers who contribute to TOD. They can expand on this if they like or correct me where I'm wrong.
Plus, it would blow the whole Capricorn One feel to the live feed and operation in general. Why else would James Cameron want to get involved?
Actually, I prefer the after-action commentary here at TOD to any kind of BP pablum. The insights here are unfiltered and explained in small words for dopes like me.
I'm not a lawyer, but that seems to be a law that's only followed when convenient, just as the law that says that a corporation's only interest is to serve its shareholders.
funny how BP gets all concerned over the law now
I know this: BP, and in particular Tony H,. have had the piss scared out of them by the lawyers whispering "Plea Bargain."
yeah, and seeing their stock price drop $50BN doesnt help them much either. i've been hearing industry analysts saying that if BP drops another 20% or so their competitors will start buying them up because at that point their assets will be so undervalued that they'll be a bargain even with the risk associated with them.
i cant imagine a world w/o BP though, i think they're more entangled in this system than anyone realizes. i also seriously question if a world without BP would be better off. i cant say... i just dont know, to me its a scary precipice we're standing on. if BP is thrown over i think it could spell some rapid and massive changes in the way we use energy (perhaps thats good) but i'd bet the other Big Oil Co's will all be reassessing the risks they're taking and probably charge accordingly.
I have read on this site that the DoD is heavily contacted with BP to provide oil for the military. If true, and I think it is, BP owns the DoD. Foreign wars and the doctrine of unforseen consequences. And so it goes....
Indeed! One really good way to save fuel is not to try and maintain multiple occupying forces on the other side of the planet.
There's a bill that seems to have made it no further than being referred to committee which would bar corporate felons from receiving federal government contracts (and grants and...). Somehow this isn't already the law.
Again, this is why BP should be taken off the case and another major put on it (with access to all of BP's privy data) and told: cost is not object because BP is paying. We might likely be done by now. Maybe not, given the challenges, but a much better chance of success without half-ass measures.
I have to disagree. BP have a strong incentive to reduce damages now. Every minute this drags on, every gallon of oil that goes into the see, adds to corporate liability and loss of goodwill. Their ass in on the line. You bring in an outisder, without risk to them, and BP paying: they will have every incentive to drag it as much as possible, without risk to themselves. Selfish interest is the best guarantee that something will get done. That is human nature.
Sometimes a cool, financially disinterested hand is a plus, though. I've been musing about the wisdom of turning over all BPs gulf ops to Exxon (I hear they run a tight ship now, pardon the pun) or another safety-conscious major.
I see claims that BP has the lion's share of infractions across the board. Would be interesting to see their share of political contributions too.
I see claims that BP has the lion's share of infractions across the board.
OSHA was not satisfied with the amount of auditing that BP did at Texas City, which accounts for something like 90% of the "Egrarious willful violations". BP is currently contesting OSHA's charges.
True enough. But I don't think Exxon faced quite the same threat to its existence that BP is facing. And I'm not really saying to handover the cleaning operations to BP (there is too much chance trying to hide stuff under the carpet). Although I would definitely not trust a private business to control that either.
But as far as "plugging the damned hole", BP really do have the most incentive in doing that as fast as possible. And that is saying quite a lot, considering how viscerally I, and I'm sure most of the people following this thing, want it plugged.
Somewhere near the end of the last thread someone posted what seemed to me to be a really good solution to the current problem of not being able to get a 'clean cut' on the riser pipe. This is important for the cap to seal against. His suggestion had to do with mating to the flange OD rather than unbolt the flange (which we've all heard those ideas and the reasons why it wouldn't be a good idea)... it went on to talk about square pegs which lost me but I thought it was such a good thought I fired up the CAD station and came up with this...
http://picasaweb.google.com/KWoodME/OilCap#5478339901873726402
Its like the second cap BP plans to use after they bring down a new manifold to process the oil captured up to the suface, the one that will slip OVER the riser pipe rather than seal on top of it. The thought is for those who don't venture to the link of the image is shear the riser pipe at the kink, slip cap over riser AND flanges the cap will seal at the OD of the flanges and could seal against the remaining riser pipe, similar to the second cap. Use a split flange to mate the flange on bottom of the cap which should create a pretty good seal, seamingly as good or better than what is currently being attempted?
In previous thread Raptor had responded with...
http://www.bp.com/liveassets/bp_internet/globalbp/globalbp_uk_english/in...
It does appear that they plan to go over the flange & riser stub with the cap. See above link.
---I agree but that graphic seems to be using the flange as a means to apply downward pressure on the topcap to create a seal on top of the riser pipe. So you are right they do appear to be going over the flange but its clear they are not trying to seal at the flange, think the same thing as they show but seal AT the flange rather than the top or sides of the riser pipe. Lets hope the ROV show starts up again, now is one of those times we wish there was more info coming from BP. These feeds have been invaluable to KNOW whats going on and not have to wait till the following morning to get some garbled report like the blade is stuck when we all knew that when it happened. Thanks TOD and all those who are contributing. Sorry to throw in yet another idea but sealing at the flange makes a lot of sense.
from my totally armature perspective, that looks like an outstanding and simple solution. the only concern i'd have (which is minor) is the ability to a) position the pipe over the riser while its flowing, hopefully the pressure wouldnt be enough to divert it and b) once the top is on, i'm guessing you're using two "C" shaped pieces to form the bottom seal? would that be able to contain the necessary pressure?
EDIT: also the riser appears to be warped from the initial incident where the kink is, i think you may have trouble getting a snug fit unless you use a larger diameter "top hat", then you run into questions about the stability of the seal.
Yes you are correct that is what is called a split flange. As far as sustaining the pressures, I have no clue they are dealing with pressures I never do in the water engineering field that I am in but I would think so, it seems the top cap they have planned is going to attach to the back side of this existing flange to create the seal on the top of the riser pipe.
Are the BP engineers considering inflatable seals to mate ther LMRP to the riser? These can seal around very irregular shapes. There is a company in Kent, OH that specializes in these seals: http://www.sealmaster.com/; though these seals are normally designed for low pressure, I'm sure they could go up to several hundred psi in the seal...
Yea, that was me on the other thread. Your drawing is much what I was thinking about when I wrote it. Except that I was assuming that the new flange bolts would be to difficult to work from the ROV's. On the other hand, I guess they used them set up the BOP in the first place? If they can that would be the most straightforward way to finish this part of the job.
One thing, you'd be tightening against the existing flange bolts with the split flange. You'd want an thick extra squishy gasket there. and a port somewhere to monitor the pressure differential. Honestly, I doubt you'd need to pump it hard to reduce the differential at the coupling to nearly zero.
I work in the Water Well industry, so Im used to having to fix downhole things for next to nothing.
One point to be aware of is that the riser is deformed, so instead of a round profile down to the flanges, you have an oval wider than the flanges. The CRAW could be used to clamp it back into a rounder shape, clearing access to the flanges.
Also, how about some camming clamps to wedge the assy down into firm contact with the flanges by locking up underneath them. They would be flush with the outside diameter, then swing in and cram the top-hat down. Seems there is room where the auxiliary hoses and pipes were cut out leaving stubs that would need to be removed.
They have got to get this under control!
Not that it matters, but it might have been my post that mentioned concerns for having a clean surface on which the first mechanism would fit - it just seems to require too much machining, and I have been thinking of an overshoe sort of device - your drawings are great.
IMHO I think they spent too much time on the top kill rather than going after a 'divert the flow' using the pressure differences as a driver.
I think Shleburn and others speak to this - I am not sure if the overshoot device has to seal completely, or if a bit of seawater can get sucked in and have it still work.
UPDATE 5 : "The technician said bla bla bla ..."
What? you mean "The engineer said bla bla bla ..."
Is it suppose to be reassuring that a tech (no offense) is in charge of this whole operation ? It sounds like my corner garage mech talking about changing my brake lines.
No wonder that all attempts to fix it failed.
Comment was cutoff during the thread change.
Take 50 toolpushers min requirement 25 years drilling experience and put them in a room. You will get a solution.
In the mean time put an old fashion rotating head (big rubber balloon) on the riser with a swedge to the drill pipe and call it good. Or you could use a sleeve with a packers similar to a DST packer. Set weight on the riser, the packer expands.
The top does need to be partially open to act like a choke. Drill holes or use the old fashion glass charges (they hardly penetrate 5 1/2" casing anyway).
There's certainly nothing wrong or lacking with being a good technician, but even top-notch, world-class technicians don't call the shots strategically in a major operation of this kind. The person in question really must have been an engineer, or really, the chief engineer of crisis team.
What's really scary about the original remarks here is that they must have been made by someone who patently DOESN'T KNOW THE DIFFERENCE between the job of engineer and technician -- someone who must think they're all basically similar and interchangeable pieces of furniture. Someone like, well, a "top-level manager" or a corporate PR flack (i.e. basically the same thing). Now that's really scary.
What if we couldn't see anything with our own eyes (via the live video stream) -- then all we'd have is this PR crap. Sort of like --- the Soviet Union.
Near the bottom of the last thread there was an important post:
"Stvrob_63 on June 3, 2010 - 12:02am
I have an idea There is a halfway decent mating surface for the collector device that we have been staring at for hours. The OD of the flanges just below the saw cut. A coupling could be made uop that slightly exceeds this OD and be attached to the fitted to the base of the riser they were going to use. Then use the "claw" to cut the riser off just below the crinp.
If you made this couple device with six or eight square windows cut around its base, then have the rovers hammer in large square tapered pegs to catch the bottom edge of the flange to keep it halway secure. A lip on the inside with a big squishy gasket would help make a halfway decent seal with the top flange
If they overpumped this riser from the drillship and monitored the pressure inside the couple they could try to find the pumping rate that more or less exactly neutralizes the pressure differential until they get these square tapered pegs hammered in place. Then when they stopped pumpimg the higher pressure inside the riser, plus the bouyancey of the new riser, would keep it pretty secure.
It will leak some, but you can control the differential pressure (and hence the leakage) by pumping the riser at the surface."
---
stvrob_63's idea is a good engineering alternative if (as now seems likely) a clean saw cut of the riser pipe cannot be achieved. It's fairly similar to a garden hose connector. I think it could be done in three stages:
Stage 1: Cut riser pipe a few feet above the BOP using the Shears, leaving a rough cut end
Stage 2: Lower a new module over the whole thing (broken rise pipe + flange) and clamp it on to the flange. The top of the module would be open, for now
Stage 3: Connect LMRP to top of the new module as per existing BP plans
The 'module' is basically a cylinder with sufficient diameter to fit over the flange (I guess 30" approx) and sufficient height (I guess 8' approx) that when in place, the top of it will not be fouled by any remaining part of the riser pipe. Inside the base of it there is a gasket or O-ring designed to make a good seal either with the top surface of the flange (if there is space enough on the outer side of all those bolts) or with the circumference of the flange. The base of the module has a simple clamping system so that it can be clamped onto the underside of the flange once in position, so as to compress the gasket - it could be tapreed pegs that can be tapped in horizontally, or if the height of the flange is known precisely, it could be pivoting, gravity driven latches, initially held "open" with a rope which can easily be cut by a ROV, these latches would have a simple lever mechanism so they can be opened up again if the first attempt to put the module in place is not successful. The top of the cylinder will have a hole with the same dimensions as the riser pipe, such that the existing LMRP can make a perfect coupling to it.
Hopefully, because of the small height and the large diameter hole in the top, this cylinder will not add any significant resistance and so it will not have the hydrate formation problem while it is being manoeuvred into position - if there might be hydrates, then the same solution can be used as for the LMRP itself, i.e. methanol lines.
Note that the existing design of the LMRP seems to incorporate some of these design elements already, at least there is a cylindrical base designed to fit over the flange and possibly also therefore a clamping system which is not drawn on BP's slide:
http://www.bp.com/liveassets/bp_internet/globalbp/globalbp_uk_english/in...
The essence of stvrob_63's idea is to put the gasket against the flange and not against the riser pipe, therefore there is no requirement for a clean-cut surface of the riser pipe to put it against. A simple but good idea - even obvious with hindsight. BP should have thought of this!
It would be wonderful if some skilled person who likes the idea could make a drawing - a picture speaks 1000 words...
I see that wood27 beat me to it, so apologies.
Wood27's development of the idea involves a more sophisticated shape, with a lower mating flange (split flange) - and he's even graced us with a drawing. I'm not sure a lower mating flange would be possible as the underside of the existing flange (at the top of the BOP) has many obstructions, but if it is possible then it would make the best seal. It's also not clear to me why Wood27 wants to pinch in the cylinder half-way up so that it makes contact with the outer diameter of the riser pipe - that seems unnecessary, and it would be easier to fabricate and position a plain cylinder. (Also note that the remaining stub of the riser pipe is unlikely to be perfectly cylindrical after the shears have cut it.)
What about a RIT-type interface with a conical probe ringed by an inflatable rubber grommet? The idea being to insert it into the cut riser and pump up the grommet, letting the Bernoulli effect do it's thing to assist with the seal.
Disclaimer: I am not an engineer nor did I stay at a Holiday Inn Express last night.
Thanks eggtimer for bringing this back to the forefront, I suspect we are going to see something like this in the second cap, as Shelburn pointed out. I would guess if they can't get that pipe cut clean we will see it sooner than later. As far as pinching it half-way up I think u probably are right, it would likely make puting it in place more difficult. I also presumed some of those obstructions could be removed? One is a level bubble I think someone said is called the bullseye. Its mounted near what looks to be some sort of valve acctuator to me. Again all I really was trying to do was present the idea of sealing at the OD of the existing flange that Stvrob_63 posted that we thought was a good idea.
First - I think this is very similar to the second LMRP cap that BP already has sitting in a basket on the bottom. It is supposed to overshot the riser stub and seal to? around? the flange.
Second - For safety you cannot have anything that clamps directly to the BOP or riser unless it can be remotely quick released. In case of a problem - drive off, hurricane, etc, - the rig must be able to detach from the well head and leave.
i dont see how wood27's approach would make that impossible. a quick release should be able to be made within a few hours. there are ROVs down there now, no reason they have to leave until a RW is done.
Not a few hours, the normal time is measured in seconds. If you have a drive-off (exceedingly uncommon these days) you don't have more than a few minutes or less to react. And you can not depend on having an ROV there, it must be operated from the surface.
I don't know for sure but I believe this is an MMS and USCG regulation.
Edit - The captain of the rig is not going to agree to anything that could tie him to the wellhead.
The BP engineers are not going to want to have any thing attached to the BOP that could possibly pull it around and create additional stress.
It won't take a lot of weight to hold the cap in position once it is stabbed on. And once it starts flowing they will probably be throttling the flow at the surface to keep from sucking in seawater. If they were to allow it to run open the gas lift would probably create a substantial suction.
An overshot to the flange makes sense and has already been constructed.
well i think this situation has enough fallout factored into it that we should be a little more tolerant of that risk in the face of the actual occurances as they stand now. just like that whole hold up with the oil boats from the N. Sea, its just asinine to say that covering 95% of the parameters is not good enough in this situation.
also the situation as it stands right now is not an "instant leave scenario" either, theres too many tools in the water to just sail off. if a Tropical Storm came through in the next few days, you can bet it would be Tropical Storm "Feces hitting the fan" regardless of the naming convention.
I'm curious now that I've had a chance to read more of your feedback. I am not sure I proposed anything to tie the rig to the well head or BOP but rather just a means to attach to form a seal, any mechanism that would normally be employed to detach the rig from the well in an emergency I would presume would be at the top of the topcap (since top hat has already been used, or not I guess its still sitting in the mud down there). Not being that knowledgeable about the oil industry is the LMR that I'm proposing wrapping around usually the point where the rig would detach from the well in an emergency? and presumably slam the bop closed?
are the flange bolts for the split flange to much to ask of the rovers? If so, my idea was to machine seveal square windows aroung the circumference of the lip of the coupling. Then with weight on the whole thing you could hammer in several square tapered wedges into the square holes to catch the lower edge of the lower flange and keep it from moving up and to keep a thick gasket (on the upper side of the flange) squashed down. Then when bouyancy is returned to the riser assembly (filled with oil and gas) the wedges should be very tight.
If the ROV's can handle threaded bolts, your idea is better though.
As far as the ship being tied to the riser during a storm? What would they have done before? Maybe use flex pipe for the uppermost 300 feet or so and then just tie a bouy to it and let it ride? Couldnt be any worse than it already is.
How far is the nearest production pipeline? Maybe tie in to it and make some money to start paying off claims?
The flange where you would clamp is at the top of the LMRP which is in turn attached to the BOP (which it wouldn't have been if the Emergency Disconnect had worked) and the BOP is attached to the wellhead which in some photos appears to be bent.
All of that took terrific forces as for over a day it was the anchor holding the Deepwater Horizon in place until it sank.
If things had worked properly the BOP would have slammed shut and the LMRP detached from the BOP allowing the rig to float off. Of course those were the last in a long list of errors and failures.
When it is all said and done I think part of the blame may lie in the reluctance to operate the BOP until either the drill pipe was blowing through it so that it damaged the rams or it didn't even operate because the hydraulic and communication lines were severed by the explosions or fire.
There seems to be some confusion, especially to us the general public, about what happened when the ROVs tried to operate the rams. Whether they had already been operated or if the ROVs actually operated them but couldn't get full closure due to internal damage or other problems.
Well I hesitated to even post an 'idea' since I have found some of the 'noise' to take away from the value of the site. But I really only wanted to follow-up on the idea others have voiced of using the flanges in someway to mate a seal. I am happy to see that the idea has been gained some legs and even commented on by Shelburn, one whom I have newly found great respect for. I realize you are speaking from experience but from what I see is the future plans they intend to just leave the riser pipe floating at the surface in case of a huricane, it will just be left to spill. This was posted in thread 1 I think the last post..
http://www.nola.com/news/gulf-oil-spill/index.ssf/2010/06/post_8.html
The blow up of the graphic...
http://media.nola.com/2010_gulf_oil_spill/photo/bp60210jpg-0287b162a5f1e...
I would agree looking at this crude drawing that the second cap very well may be more or less just what I had drawn and perhaps if they can't get that riser clean cut they will move to that cap sooner rather than later.
I haven't been able to come up with any scheme that prevent oil from spilling during a hurricane until the RW is completed. The well is going to flow. The idea of a connection at -300 feet has merit in that it might save a few hours to a couple days leaving the site for a hurricane and probably save several days on return.
But when the rig has to leave site there is nowhere to put the oil. Inflatable balloons and sunken barges all sound great but the physics of the situation make them non-starters.
Shelburn: I am going to respond here to your comment concerning my 64 billion dollar question about the defective riser (first twenty feet) on the prior thread which has been closed.
The fact that this is the first BOP failure out of 30,000 wells is a bit like saying this is the first type of catastrophic failure on an plane with 30,000 flights.
That excuse does not cut it any more than it would cut it for the airline industry.
In fact, in this situation 120 people could have died as well as creating the worst environmental disaster the country has ever seen. Planes don't cause this level of environmental and economic damage.
Nor is your tornado analogy appropriate. Tornadoes are not man made.
When the risk of damage is this great, basic mistakes can't be legally permissible no matter what safety redundancy is in place. (I am a tort lawyer, by the way, who has handled many products liability cases).
Moreover, I would have rather seen twenty good feet of pipe that could effect a repair, maybe even more than I would have seen many of the other safety measures you mention. This was a very simple design flaw that resulted in the additional spill of millions of gallons of oil.
If the reinforced pipe would have prevented the incident then I would agree with you, but it had nothing to do with the blowout, failure of the BOP or failure of the emergency disconnect.
In many decades in the underwater industry I have seen or studied the results of many underwater blowouts around the world - including in Norway which everyone puts forward as being much safer that the USA.
I think this is the only one I know of where a reinforcement on the bottom 20 feet of the riser would have made any difference.
A better application of the same concept would be reinforcement of the top 50 feet of the wellhead where the BOP attaches because that has often been an area of concern. In fact I think it may be of great concern to the BP engineers right now.
Actually I think reinforcement in both places would have been smart. The torque of a 5,000 foot riser would be huge.
That is what gets me. These are the two most vulnerable places in the whole string of pipe.
If you lose the riser for any reason, damn you want these two areas beefed up.
Agreed. There is a real design problem here, and I really doubt it's just this well. This is unacceptable.
What amazes me is they think this problem disappears at 500 feet. How does it disappear at 500 feet?
What problem disappears at 500 feet?
I think he's referring to the moratorium on drilling in water over 500 ft deep but no new restrictions on shallow water drilling.
Shelburn
Seems it would be easy enuf to add a quick release coupling to the new riser pipe a few feet above the BOP.
That might not have helped with drill pipe inside. What I think you really needed was about twenty feet of 36 inch pipe coming out of the BOP and then a reducer down to the 21 inch riser.
That way when the riser breaks or bends, it breaks or bends in the 21 inch section and you have twenty good feet of 36 inch pipe with which you can effect a repair.
The riser is generally under a bit of tension during operation. If they actually bend it somehow (which did happen in the early day of DW drilling) you bring it up and replace it after firing the responsible party.
Reinforcing it just in case the entire drilling rig sinks while attached to the well seems to be a bit of overkill.
If this leak goes on for about two or three months, the public is not going to think it would have been overkill. When your plane is going down because some engineer thought it was overkill to reinforce an aileron you are not likely to be too happy with his decision.
Reinforcing the riser was a very simple inexpensive thing to do.
There are two kinds of engineering disasters: the kinds that cause accidents and the kind that fail to easily mitigate one.
It is not overkill to inexpensively mitigate a national catastrophe.
Look at it this way. If you have any hope of ever drilling in the deep ocean again, you better find some reasonable way to mitigate a duel riser and BOP failure. This might be able to do that.
The national catastrophe is not the leak, the national catastrophe is that we can't stop it in an acceptable time frame.
Assume there was a 20 ft by 36 inch riser coming out of the BOP stack. How would that have changed the current situation?
On a small scale, the diamond saw would have dulled and quit sooner, because of having to cut through more steel. Not much of an improvement in my mind.
On a larger scale, the extra strong 20 ft of riser would have acted as a heck of a cheater bar as the rig sank and the riser collapsed to the seafloor, and instead of having a slightly tilted BOP stack, we might have had the BOP bent and broken, or yanked all the way over. That little safety device could have meant unrestrained flow from day one. Also not much of an improvement in my mind.
Again, it might require beefing up the casing beneath the seafloor, for fifty feet or so, as Sheldon has suggested, if you are worried about the additional leverage on the BOP.
As for how twenty feet of straight 36 inch riser pipe would have changed the situation. Assuming you can cut the riser off, (and there might need to be a special tool made to be able to cut it), twenty feet of straight pipe gives you numerous options to fix a leak.
You could slip thirty feet of 40 inch pipe over it easily with an open valve on the end. Oil pressure in the larger diameter pipe would drop, perhaps significantly reducing pressure at the valve opening, making repair easier. Then the bigger pipe could be clamped, or cinched to the smaller one and a good seal could be made. There may need to be pre-manufactured seals and fittings to ensure a good seal. Then you can kill the well with mud and cement once you have a closed system.
The real problem that is unacceptable to people who are not in the industry is that the only sure fire method of killing a leak is a kill bore. A kill bore takes an unacceptably long time frame. There needs to be another means of adequately killing the leak, even if it is only a temporary kill.
When Sheldon talks about overkill, all of the safety features he talks about address not having a leak in the first place. Nothing addresses a leak once you have one. A viable second leak killing option needs to emerge if the industry ever has any hope of expecting to drill in the near future.
I think I did and posted it already... check it out!
http://picasaweb.google.com/KWoodME/OilCap#5478339901873726402
Great diagram. I had assumed that BP was going to use the nice round outer edge of the flange to seal against, but your locking split flange underneath the riser's flange is well thought out.
However, I don't think it'll work as designed, because the area under the riser flange isn't a nice straight pipe as you've drawn it. There's a whole bunch of random mechanical crap under there, having to do with the flex coupling at the top of the BOP. A lot of that stuff comes to within an inch or two of the flange bolts, and would interfere with your split flange:
Here's a picture so you see what I mean.
You could work around this, but you'd have to design the split flange very carefully.
But I'm not sure you need a locking flange at all. As I've posted elsewhere on this forum, once you get some low-density oil and gas in the pipe leading to the surface, you're going to get a ferocious "chimney draft" effect, which will lower the pressure inside the pipe to below ambient seawater pressure. In layman's terms, the pipe will suck itself onto the BOP's flange like a vacuum hose.
And "drive off" capability is easy if you take the suction effect into account: you just close a valve at the top of the pipe, pressure at the bottom of the pipe builds up to ambient, and poomp! the mating gasket pops off the flange.
Exactly
Wow great feedback, and seconded by Shelburn. Thanks guys. Maybe the LMRP #2 is this design, maybe it will be the ticket. CNN update... Looks like for now they ARE going to shear off the riser with the claw and place the top HAT over the riser, perhaps that is sized to seal somewhat at the flange. I hope so!
I commented on your flange idea. The exact dimensions of the flange must be known to the millimeter from the CNC specs. You could use tapertip hex or Torx set screws around the perimeter just under the flange edge and the ROV could spin them in with a ball hex wrench of appropriate size. Easy to drill and tap all around, and easier to set underwater. Put some above the flange to act as adjustable stops. Setscrews are a wonderful thang.
I made some additions to my drawing to try to capture your ideas.
http://picasaweb.google.com/KWoodME/OilCap#5478378461884983010
I would say that the method to clamp or secure the cap to the flanges is not the key, I think they have that engineered, I don't think they are considereding sealing against the flanges. None the less I took a few minutes to try to illustrate your ideas since the ROVs seem to be just floating about now. I'm not sure if it was what you were thinking but the clamp idea seems like a good one in that it takes into account the capabilities of the ROVs. The peg idea seems to rely upon a more exact placement of the cap to allow for the peg placement, since the slot for the peg would have to line up btwn the bolts to allow for a peg to pass through. If anyone saw the trouble they had just getting the shear claw placed in the spot btwn the cut pipes you'd know they will have their work cut out for them to place any cap over the full flow of the well. Again I think whatever engineered clamp they have for the caps would work as it seems they are bearing upon the underside of the flange. The key still to the thought is stvrob_63 pointing out that the flanges may be the best point at which to apply a solid seal since they should be a 'perfect clean cut' already. I hope this IS the idea of the second cap and they just move on to that. I fear with the media making such a big deal of BP always moving past a failure and on to the next plan D, E, F.... may encourage them to stick with a plan as long as they can rather than moving on to what may eventually work.
I think they have already fabricated a cap that will seal at the flange area - but of course no details for us techno-nerds.
I think it was in one of BPs technical presentations and you can see a teasing glance of it here:
http://bp.concerts.com/gom/subsea_staging_area.htm
Its hiding in the background behind the riser seal cap.
Your pegs and clamps look good but for reasons already stated will never be used, but also they can get the seal with weight. The drill string has some very heavy pipe at the bottom and they can accurately measure exactly how much weight they are applying to the cap to seal it to the rise/flange.
Nice drawings.
My notion is that your adpter would have to have a greater diameter to accommodate the oval shape (Assuming the shear cut is accomplished) of the remaining riser.
DAW
When I saw where they were making the initial cut of the riser with the shears, I was concerned about the weight of the remaining pipe creating a situation where the wire saw would be pinched. As an analogy, when one cuts down a tree with a chain saw, one makes a wedge cut part way through the tree and then completes the cut from the other side, so that the chain won't get pinched by the weight of the tree (and the tree will fall the right way). Further, when felling a difficult tree under tension (not to be used for lumber), a tree guy will remove sections so as to reduce the weight on the final cut. It seems these guys didn't anticipate this senario well enough.
One of the main challenges of this latest attempt was to get a clean cut so that they could get as good a seal as possible. The shears will deform the top of the BOP and limit their ability to seal this thing. Why don't they resume cutting from another side with the wire saw or the rotary saw?
Whatever technical skills these people have seem to be exclusive of common sense.
"Whatever technical skills these people have seem to be exclusive of common sense."
Apollo 13 would not have made it home if NASA had been this inattentive to detail.
Apollo 13 was a cake walk compared to this situation. All they needed was some duct tape, cardboard and some vacuum cleaner hose, with people onsite to do the southern engineering.
I'll bet most of the people working this problem never even changed their own oil.
I'm sure some of them would have at least started the oil change, but to finish? Can't get the old oil filter off? Drive a screwdriver through it!
Oh sure, Apollo 13 was a real cakewalk compare to this blow-out thing. Just consider for a moment how you'd feel patching program code into your incredibly primitive Apollo guidance computer, by keying in a long string of byte codes (0x33, 0xa5, 0x97, 0x48, 0x31, ...), just as you're about to re-enter the Earth's atmosphere and burn up, with your life (and your crew's) depending on your getting every bit exactly right. That's a *piece of cake* compared to moving a joystick left and right, up and down, in a comfy air-conditioned control room somewhere, solidly planted on terra firma.
The computer was not primitive at the time. Sufficient if I remember correctly as they made it back.
What I was talking about was the atmosphere they had to work in, the stuff needed to make repairs and the fact the astronauts had to make fairly simple repairs. The obvious main task was to keep them alive and fortunately for them they had the lunar lander systems.
Here they are having to work in an entirely hostile environment where humans cannot work, with thousands of psi pressure with remote devices performing unfamiliar tasks. They have been dealt a hand with sub-sea failures that nobody could have calculated the odds for.
Murphy was camped out on the rig waiting for his opportunity. He took it and everything that could go wrong did. From the initial mistake on the rig all the way to the bottom of the well was nothing but failure after failure.
The art of placing humans in space does not have a very good safety record relating to deaths (deaths per person successfully launched and retreived) but lets take aviation for instance. With all of todays safety systems and backups, we still have mechanical failures but most accidents are the result of pilot error. Usually it is a cascading of events the lead up to catastrophe, just as the Deepwater Horizon accident.
Earlier I posted the following:
To those who wonder why it might not be prudent to try to shut in the well (like by crimping the riser pipe), it's not an issue with the BOP integrity or wellhead, but because of the likelihood that isolation between the 9-5/8' x 13-5/8" casing annulus has been compromised, either because of a wellhead seal failure or because of a collapse. The problem is that the 13-5/8" casing (and of course all of the larger strings) were not designed for the same burst pressure as the 9-5/8" x 7" production string.
If you could shut-in the well now at the BOP, there would be a mixed oil/gas column from the reservoir up to the seabed. I'm guessing that BP is esimating that the resulting shut-in pressure is greater than the burst pressure of the 13-5/8". If you look at http://www.ussteel.com/corp/tubular/documents/USS%202010%20Casing%20Prod... you can see that the burst pressure of 13-5/8 casing having a drift larger than the 12-1/4" bit needed for the next hole section is in the 5,000 - 8,000 psi range (w/o any safety factor).
Because of drill pipe wear when you drill the next hole section below the 13-3/8" shoe, it's likely to have thin spots up near the seafloor, so I'd guess that nobody feels good about subjecting it to differential shut-in pressures that could exceed 8,000 psi.
I think that BP expects that the delta p at the seabed would be dangerous to the integrity of the 13-5/8' casing. If that rupured, then all of the remaining outer stings would then rupture, which means that it's game over until a relief well could be drilled. Containment would no longer be an option.
Then again, I could be wrong :-)
The link to the initial finding document that someone posted later (thanks BTW), indicates that the next casing string inside the wellhead is 16", not 13-5/8' (that was a liner, not a full string). However, my point is the same.
I am posting this because things are a bit slow right now & this is totally ot.
I know that there are quite a few on here involved in the industry, so my comment is directed to them.
My father was a diver from the late 50s until the early 80s. He was also a shutter-bug. I have a huge collection of 35mm slides of 'job pictures'. Most of these I have no idea what I am looking at, but I know from the hours Dad and an uncle ,who was an oil field engineer, spent looking at them and talking about them, that they might be of interest to some here.
If anyone is interested, please let me know.
ExArco,
This is what all the daft wannbees are missing. THE WELL IS NOT SUITABLE TO KILL VIA TOP END STATIC HEAD PRESSURE FROM MUD OR BLOCK VALVES. The original problem with this well is down hole and not the wellhead mechanisms. If we took an old battleship (I'm putting on my "layman's" pants now) and attached a giant screw to its stern and then sank it stern first directly over the well after fashioning a nuclear explosives array to spin it sufficiently to insert the giant spinning screw into the well casing beyond the BOP, to block the hydrocarbon flow where ROV cameras can transmit images to the whole wide world,this well would not be tamed! Well beyond the sea "floor" we are seeing, this well has problems. If we block the well head, this singular point of escape for the hydrocarbons the well is producing, will take the next least path of resistance which is into the geological strata available outside the compromised well casing system, and the disaster will become manifold. We will see multiple mini volcanos of crude and gas spouting up in unpredictable and uncontrollable locations all around the locus of this well. The current effort is about placing a mechanism on the well head assembly that provides a means to capture the effluent hydrocarbons without further constraining them and increasing the downhole pressure so as to avoid forcing these same environmental contaminants out side the well casing and into the reatively weak gological structure beneath the gulf of mexico. Please, all you "I tried this on my toilet pipe once and it worked types" need to crack open a physics book and get a grasp of the basics of reality before you come storming out blasting the studied approach of some of the best engineers on the planet.
Scathing and Ranting I know, but I can only tolerate imbeciles singularly, this place is begining to be over run with them!
BW
I might be missing someting major here as a layman, but weren't the "best engineers on the planet" just trying a top kill with mud right before this pipe-shearing venture..?
Top kill is always the first emergency response to a runaway well, in deep water and with a well that had not reached completion, insufficient information was available to determine the condition of the down hole systems. Upon subsequent analysis of the chain of events and the data discernable form the top kill attemp the facts became clear that constraining the productin at the sea floor was not worth the risk of sending the hydrocarbon production into the surrounding geological strata. Given a functional BOP and proper a downhole cement job, equipment could have been deployed to circulate heavy mud to near the bottom of the well versus trying to force the produced pressures back while simultaneoulsy overcoming all the topside leaks. Even if the drill stem had been deep, someone I am sure would have thought of attempting to access it and using it to circulate mud to the bottom; but from what I gather, unfortunately it was only in about three thousand feet.
I think if BP was convinced they could have completely diverted the flow to another formation, an underground blowout - they would have done it - and the MMS and government would have probably gone along with it.
As bad as that would be what we have is worse.
Honestly not trying to be difficult here, but wasn't top kill the *third* or so response after The Big Metal Box and the Smaller Metal Box? And did this not carry the potential risk of a bigger blowout downpipe assuming there wasn't mud loss?
And now after thanking goodness for weeks that the kink in the riser was holding back some flow, we've decided to chop BELOW that kink, and now may have (pending breaking news reports) abandoned the leading reason for making that cut (not well at that it appears) in favor of another Metal Box!
At this point I'm wondering which of the Howard Bros. co-stars in this one, Curly or Shemp?
All pales in comparison that apparently no one thought it was particularly important to have any plan in place for when this eventuality occurred. This is the work of the best engineering minds on the planet?
I'm impressed, genuinely, by the ability of the oil industry to extract this stuff. I'm increasingly equally sure that these are not the best people to stop the flow or collect the slop, other than via the relief wells (even those they seem to want to go cheap on!).
The beginning of your post should be included in the boilerplate of all new threads here on TOD.
When the junk shot effort "failed," I think it proved that the casing integrity is crap, so the capital P for PLAN B is to suck all the gas/oil up until the relief wells are drilled.
Dan
ExArco this is the most significant thing coming down right now. I've been looking at the casing design from Halliburton at http://www.theoildrum.com/files/20%20Deepwater%20casing%20Halliburton2.jpg and it shows that the 13 5/8 casing is part of the string just prior to penetrating the reservoir. They knew before the well even started that the week point for well control was 8000 psi. The casing on this well was designed to get to TD past the lost circulation zones and sloughing formations; it was not designed for well control. The 9 7/8 string set at 17168 ft, just above the reservoir, should have extended all the way to the wellhead and not been hung off the previous string. I can't see an engineer making that call, but more likely a last minute decision to save a bunch of money by using a liner hanger.
This is an important lesson for the relief well to learn from. I think it also justifies reviewing the BP casing plan for the relief well.
The casing design must allow a total shut in with pressures of 14,000 psi. It looks like BP was already shaving the casing weight to accommodate drill bit size. Maybe they should have started bigger straight from the top.
The relief well may encounter high pressure formations caused by an underground blowout across the production cement inerval. Flow is probably coming from the annulus between the production casing and the 9 7/8 shoe. Flow could also be from annulus to formation through any of the liner hanger seals or weak spots in the casing, and thus charging up higher formations. Point being, a blow out needs to be anticipating all the way down rather than hoping they don't get one. The relief well can not hope that they won't take more than an 8 K kick like the Horizon hope, now less.
Plus we don't know if the flow is coming up the production casing, or the annulus, or both. All they know is the flow is coming out the top of the BOP. Is the production casing landed in the wellhead, or still in a state of semi-install? If there is no pressure at the PC then this might be the best avenue to perforate and cement off the flow; and an avenue that is not limited by formation fracture pressure. Drilling the relief well into and disrupting this could be a setback. Milling through will be difficult because there is a pipe within a pipe problem that could be bigger than what we got going on now at the riser. From a well kill perspective of the relief well it would be better if the production casing had not been run and the bottom of the 9 7/8 simply plugged and cemented off.
I can't understand why they hadn't run the 9 7/8 all the way to sea floor. If they would have done that they could have totally shut the well in. As it stands all this hoop do doo about shear rams not being good enough, or not remote control on the shut off valve, etc are all irrelevant when the weak point is 8 K psi, and they knew this before they even spudded. If this is according to license and regulation then it indicates that there are serious flaws in the regulatory mechanism.
Bottom line is that BP needs to do a review of their casing design for the relief well.
I'm at the BP page and all I can see is a sleeping robot.
Where are you guys getting your live feed action.
jal
Sorry! I just refreshed the page and action came up.
jal
I am at BP.com; click on the watch the live stream link.
try this link to another site that has multiple feeds
A different view:
http://a662.l9789246661.c97892.g.lm.akamaistream.net/D/662/97892/v0001/r...
thanks for the link. great view.
This page:
http://www.bp.com/genericarticle.do?categoryId=9033572&contentId=7062605
...has a menu of video feeds from two ROVs attached to each of six vessels:
Ocean Intervention III
Viking Poseiden
Boa Deep C
Skandi
Enterprise
Q4000
The only one working right now is Viking Poseidon – ROV 1, which is also what CNN are relaying.
Perfect, thanks.
It looks like they are on the sea bed now. Is it possible they are pumping dispersant up the damaged riser?
At 21:11 on 2/6 it appears the ROV is disassembling and rebuilding some kind of fluid control manifold. Any experts recognize this?
Ideas on how to stop the spill are still being offered by posters on TOD. I'd like to let those with suggestions know there is a formal way to get them to the Deepwater Horizon Response Team.
Deepwater Horizon Reponse Suggestions
If you feel your idea has real merit, it is up to you to forward it to the response team. It won't see the light of day here. Even if your idea got little support here, you still might send it off anyway. Problem solving sometimes gets inspiration from just a small piece of an impossible idea.
Just a reminder, this is a place to discuss your ideas only if you have taken the time to think it through and searched through the previous weeks' posts for similar ideas. Almost all the good ones have been already taken ;-) For example, if your idea has to do with a balloon, just open up the post and do a command F search on a Mac or a control F search on a PC to find all the comments with the word balloon.
And please, if you are replying to a comment that contains a suggestion, I don't care how poor you feel the suggestion is, a courteous response is the only acceptable response, IMHO.
Thanks!
excellent work on that post! of all the iodeas i've seen to me it looks like wood27's appears most plausible. if any industry professionals could look into it further for critique i'd suggest it bevetted and sent.
PriorityX:
Thanks for your insights.
If my idea is noob-thought, so be it but here goes:
Can't they consider trimming the riser by using an underwater ganged plasma arc cutter?
As I understand it, the riser would need to have an electric current generated and running through it
as it cannot be neutrally charged.
http://media.iupac.org/publications/pac/1992/pdf/6405x0665.pdf
http://www.synergyoilgas.com/oilfield-equipments-supply/welding-cutting-...
is there any person here who has an idea how the spill is going to be affected by hurricanes......someone knowledgeable in these things
1- far as i understand ....the temperature of the water has a big effect on hurricane intensity so I'm guessing oil s black it might absorb more heat .....or when we talk in terms of hurricanes the spill and whatever little heating effect is negligible.....
2- if the hurricane picks up water are we likely to see any oily rain or is the hurriace liable to pick up the oil and spray it onland ??? --this might be stupid but reason i'm asking is ....i've seen water spouts (i dunno if its the technical term..cud be just a rig-hand term) over in Timbalier Bay, LA pick up many fishes 50 ft and move them along fair distances [i heard an old wireline guy working for Wood Group, Houma, LA say he seen small porpoise pickup up by big water spouts ; but then wireline guys are wireline guys :) ]
any body knowledgable here about this stuff
@aliilaali
Here's a start: http://www.nhc.noaa.gov/pdf/hurricanes_oil_factsheet.pdf
I have read at the link, and the official line is that the oil cannot be picked up and rain down inland. For some strange reason I am skeptical of the official line these days. ;)
I hope we have some input from those with some knowledge.
water has a lower boiling point than most of the hydrocarbons in crude so it stands to reason that the oil would not evaporate and condense in that way. i suppose it would be conceivable that something resembling pentane may waft up as vapor, but i dont think it would condensate like rain.
i also cant really see a 'cane picking up too much oil, i cant put my finger on why at the moment but it just doesnt seem plausible.
Of course we get the odd "fish falls" and "raining tadpoles" and so forth which pepper the collected work of Charles Fort, so I wouldn't rule that out, although those are pretty rare, small-scale events. I should think the bigger worry would just be storms pushing contaminated water inland, and into groundwater.
Oil can be picked up in a hurricane the same way that salt water can be picked up by a hurricane. It's blown off the top of waves and suspended in the air as droplets. The droplets can then land tens of miles inland.
I have tasted salt in the rain from tropical storms & hurricanes in New Orleans. But the concentration is not high enough to damage even salt sensitive plants.
Alan
Central - appreciate the link, but its just like any typical govt sheet, heavy on the BBQ sauce an light on the info.
I found some good information at Jeff Masters' blog.
Notable points:
...a hurricane moving through the Gulf of Mexico spill will very likely make the disaster much worse, spreading out the oil over a larger region, and bringing the oil to shores that otherwise might not have seen oil.
...a hurricane passing over the oil spill will be able to hurl oil and toxic dispersants many miles inland during landfall. In regions where little rain falls, the concentrations of the oil and dispersants may be a problem. Again, we have no experience with this sort of situation, so the potential risks are unknown.
In general, we do not need to worry about oil dissolving into the rain, since the oil and water don't mix. Furthermore, about 50-70% of the oil that is going to evaporate from the spill does so in the first 12 hours that the oil reaches the surface, so the volatile oil compounds that could potentially get dissolved into rain water won't be around.
Dr. Masters also states that hurricanes mix the ocean water only to a depth of about 200 meters (650 feet); therefore, oil would have to be present within that depth to be carried ashore by a hurricane.
News reporting that BP will not use diamond saw..per Allen
Some questions: It appears that the LMRP has no pressure relief other than up the riser. Would this mean that the entire pressure of the well would be directed to the drill ship the moment the LMRP is sealed to the BOP? Would this cause any backpressure on the well that could risk well integrity? Does the drill ship have the capacity to receive the entire unrestricted flow from the well? Will attachment of the LMRP cause a rapid and extreme increase in pressure in surface equipment that could endanger the equipment and, more importantly, the crew of the drill ship?
I've been keeping up with prior posts as best I can and have read some of the previous LMRP discussions, but can't say I've read it all so regret if these questions have already been asked and answered.
Back when they were talking about the containment dome I did a rough calculation and came up with the fact that the drill pipe could probably handle about 20,000 bpd if it was 100% oil, maybe more, just due to the buoyancy of the oil. When you add a gas lift (even super-critical gas) it will increase that substantially.
The problem is controlling the flow at the surface to regulate the flow rate so as not to suck in seawater and to safety separate and flare the gas.
I'm sure they learned a lot from operating the RITT.
FOR ALL NEWBIES
05 (question from previous thread) – For your benefit and that of other newbies showing up daily I’ll offer you my very biased conclusion of the primary cause of the blow out. The regulars can skip the rest of the story…they’ve heard already. I’ll make just one qualification and it’s a big one: IF THE INITIAL REPORTS ARE CORRECT. It will likely be at least 6 months but more likely a year before there’s official confirmation. The following are just my suppositions. But suppositions gleamed from 35 years as a petroleum geologist with a strong background in well site operations. That experience includes working on site on DW GOM wells as a pore pressure analyst. As a PPA I assisted the drillers in determining the magnitude of the rock pressure they had to deal with.
BP drilled thru an oil reservoir at about 13,000’ below the sea floor. The pressure in the reservoir was around 14,000 psi (an educated guess). They ran steel pipe (casing) from the bottom of the hole back up to the wellhead at the sea floor. They then ran the drill pipe to the bottom of this csg string and pumped wet cement up between the csg and the rock. The purpose of the cement isn’t to hold the csg in place…it isn’t going anywhere. The purpose is to isolate the oil reservoir and keep it from flowing along the outside of the csg in either direction…up or down. It appears the cmt job failed to provide this isolation. Opinions vary but IMHO this is not the BIG SMOKING GUN. Cmt jobs fail all the time. You assume that during the course of drilling a well that you’ll have get a bad cmt job or two. That’s why you routinely test the cmt after a period of 18 to 36 hours. The primary and best cmt test is to apply pressure to it. The cmt has to hold a pressure greater than the reservoir pressure. If it doesn’t then you do a “squeeze job”: pump more cmt behind the csg and then test again. There is some question regarding the validity of the pressure tests BP conducted. Opinions vary but the cmt did fail…that’s why the well blew out.
After BP decided the cmt job was sufficient they had to set cmt plugs inside the csg string as required by MMS regs. But before setting the upper cmt plug they began removing the heavy drilling mud (14.5 pounds per gallon) from the csg and the riser (the 20” tube that connected the wellhead to the drill rig 5,000’ above. They did this by going down into the csg with drill pipe and pumping seawater down. The seawater pushed the drill mud back up to the rig. The seawater weighs about 7.5 pounds per gallons. That means the pressure exerted at the bottom of the well was reduced considerably. So low this pressure wasn’t sufficient to keep the oil reservoir from flowing up. This is a normal procedure. Had the cmt job held all would have been fine. The bad cmt job allowed the oil reservoir to flow up the csg. Had they set the top cmt plug first the well would not have blown out when they displace the mud. Even with a bad cmt job a proper upper plug would have held the flow back.
There are any number of circumstances when there’s a valid concern that some reservoir is flowing into a well that’s cased or still drilling. There’s a very basic protocol for checking to see if the well is “kicking (flowing upwards): you turn the mud pumps off and determine if there’s any drilling mud still flowing out of the well. There are some exceptions but in general a reservoir can’t flow up the well unless it pushes the mud out ahead of it. No flow returns and the well is static. Mud flowing out of the well when the mud pumps are off = something pushing it out. This is not an uncommon event. The drill crew has practiced “killing” the flow (stopping it) many times. First all the return lines are closed (shut the well in). Even if this doesn’t prevent the oil/NG from flowing all the way up to the rig it does prevent it from breaching the drill floor (this is the definition of a blow out). Once the well is shut in they can pump a “kill pill” (heavy drilling mud) down the well and put enough back pressure to stop the well flow. I could be wrong but the evidence seems to indicate that the hands on the rig weren’t monitoring the mud returns when they were displacing the mud. They didn’t see the well coming in (flowing) until it was too late and the oil/NG breached the drill floor and exploded. Why weren’t they closely watching the mud returns? I’ll skip that part of my already long store.
When the well blew out every hand on the drill floor knew exactly what was happening at that point. They knew what was likely to happen. Every hand on the rig knows. The hands had two simple choices. Run and give up any chance of killing the well. Or stay in there and try to execute the kill procedure. The 11 hands that died took the second option. They were obviously “top hands”. That’s the highest title you can earn on a drill rig. Doesn’t seem like a very impressive title to most but in the oil patch it says everything you need to know about the guy working next to you.
I’ll pass on the BOP failure. That’s a critical but separate issue. Just as the efforts to stop the flow since the rig sunk. Lot’s of folks on TOD better qualified to handle those discussions. Likewise other knowledgeable TOD folks have other interpretations of what caused the blow out. Listen to them all and you can come up with your own conclusions
I watched the testimony of Mark Haflay today and one thing stuck with me. He believed a CBL would not have produced any useful results that could have prevented the blowout. He was under the impression it was needed before perforation of the casing, but not before. From your reports ROCKMAN, that struck me as completely against your beliefs about what CBL is used for in wrapping up drilling operations. Do you have any idea why he would believe that a CBL wasn't warranted until the completions crew came in?
Actually Greg I don't consider a CBL a substitute for a leak off test. A CBL is more important from a completion stand point IMHO. I've seen bad cmt jobs with good CBL's and good cmt jobs with bad CBL's. I consider their interpretation as much art as science.
Much of the discussion around BP's negligence has centered around not doing a CBL, therefore I just wanted to clarify if it really was negligence or if their other tests (let's assume they were successful) were enough for industry in general.
Anyway, I think I may have asked you the wrong question. Let's assume the cement was no good. What the leak path you would expect into the wellbore. Is it up the outside of the casing to the string overlap section?
Greg – could have gone up the annulus or up the production string. Without a caliper log we can’t calc cmt height. But it seems a little short to me. But that’s mostly a WAG on my part. OTOH it seemed to me it came in so fast and hard coming up the production string sounds like a good bet too.
If it went into the production string (we're talking the 7" right), wouldn't it have encountered the plug first to leak around?
I'm a newbie not in your industry. Lowly aerospace navigation systems engineer. Do you really think Schlumberger's crew high tailed it off of the rig, requesting their own chopper in a hurry, because they were miffed that they didn't get to do the CBL job? My impression as a casual observer is that it wasn't a matter of art or science, to do a cable log, but that they were truly frightened for their lives--or at least the media seemed to hipe it up that way. It it reasonable for Schlumberger people to claim such (now after the fact) or was their ego just hurt by being overruled by BP management? How is it that a vast list of failures can be adding up like this?
Drilling really is a very rough job. I know it is probably more art than science and now that an accident has happened, all the science and technology for safety is being referenced when none of the newbies really understand the difficulty and art of doing the job. However, that vast (55 item) list that ndyer1 published is quite revealing on the state of current industry practices and that this accident pushed way past normal boundaries of operating between art and science.
Thanks again, and I appreciate all the education from this place.
oe
Mark is right technically.
A CBL is really needed in completion job ...as when running a completion job all you need to know is zonal isolation exists...so long as it was run before the perf gun is would have been fine...
Also a CBL does not detect micro annulus which really is the problem with nirtified cmt delivery so would not have been useful much in this case
A decent 60,000ft elevation review of events. Well done. However, I suspect you "fat-fingered" the density of seawater. Fresh water is 8.33 ppg (0.433psi/ft) and seawater is north of that. I typically used 0.455 psi/ft in the GOM.
Thanks Rockman for that explanation, and also for mentioning the 11 rig workers who perished that night. I never understood why not much was said about those 11 men in the media. But then again, it is the media...and they answer to their corporate masters. But anyways, i appreciate your knowledge and helping me understand a little bit more about the disaster that is unfolding each and every day. But i have seen enough...BP has no idea how to solve this problem...that should be obvious to anyone who has been following this for 7 weeks now. So thanks for all the info, and one word of advice to anyone living in the Gulf area...Get the hell out! You people are living on the edge of ground zero, and just like the 11 rig workers whose lives were dispensible by BP, so will the lives of everyone living near the Gulf. God Bless!
212 – I don’t think many of us are bothered by lack of attention from the MSM. Such events happen and will happen again. You just put it behind you and carry on. I doubt that attitude is very different the folks in other risky jobs. One of my production hands lost his nephew in the blow out. Less than two weeks earlier he lost his adult son in an auto accident. I saw him on one my drill sites the day after the blow out. I expressed my feelings and we haven’t talked of it since. He doesn’t bring it up. If he wanted to talk about it or get drunk and curse God I would go along with him. But he doesn’t. And the rest of us are thankful for that.
I have thought a lot about those men who were killed. Maybe it's a mom thing - I have two sons very close in age to one of those fellows. Maybe it's because so many were Misssissipians and Louisianians. My heart goes out to their families.
I know it isn't accurate but it seems like the same old thing: management makes a blundering error and the man out on the shop floor is the one pays for it with his life. :/
Thanks Rockman for your explanation.
"Or stay in there and try to execute the kill procedure. The 11 hands that died took the second option. They were obviously 'top hands'."
To that I would add they were heroes of the first order. Their failure to kill the well does not make them any less heroic or deserving of the highest honors.
Thank you for that explanation, Rockman. I've bookmarked your permalink for that comment. So I can direct people there in future when similar questions are asked.
I think each of us can do a little to bookmark a few important explanations and that will save time if people ask questions or if we ourselves need to go back.
I just want to thank all those here who are offering so much so patiently to those of us who know next to nothing.
EDIT: Here's an article from a few day ago that dovetails with Rockman's explanation, but is a news report and offers further info as well, based on internal bp documents and their testimony:
http://www.nytimes.com/2010/05/30/us/30rig.html?ref=science
Thanks Rockman. Some time ago I downloaded a free app called Evernote. It allows you to highlight and permanently save Web pages (and create notes) to the app database on your computer and also in the clouds. I keep schedules, etc on it so I can use any computer to access info. I can also email the copied text or whatever directly from Evevrnote. (What will they think of next, Mable? Underwater contraptions that fix things?) I just sent Rockman's explanation to 4 friends and told then they must donate to theoildrum.com. Maybe one will. [I have no connection to Evernote. I just use it a lot.]
I have a question. Im an engineer water well projects, typically 600 to 1,200 feet deep. We always cement the entire annulus, and we only have a few feet of head between zones. How come in the oil wells they use such short intervals of cement?
63 -- you can often push cmt higher. I usually recommend getting full returns as you do. Put trying pumping too high can cause bad lost circ. I think that was one reason they went with the N2 cmt.
INMHO ROCKMAN is the only cat with a grasp of reality on this forum. Blame is meaningless, hollow. Evey major oil company is drilling wells, and it just happens that BP's number came up first. Who lives their life totally devoid of petroleum consumption? It is not a matter of how many GPM your anemic can't get off the entrance ramp shoe box of a car gets, you use oil!
I disagree.
First, BP had a reputation for cutting corners that predates April 20th. The well was below industry standards is several areas. It was not just a matter of random bad luck that a BP well blew out.
Second, if the average American used as much oil as I do, and the transportation initiatives I push were realized, the US could be self sufficient in oil with no DW drilling.
Alan
The well was below industry standards is several areas.
Except that you don't know that at all Alan. I know you think BP is the worst company ever, but could you please try and refrain from continuing to make unsubstantiated conclusions. I expect very little from alot of these new posters, but do expect better from you.
greg, i know you think BP is the best company ever, but could you please try to refrain from continuing to make fact-free statements and unsubstantiated conclusions.
greg - got any facts to support your position that alan's statement "The well was below industry standards is several areas." is incorrect?
otherwise, please refrain from shilling for bp.
The questioning in the inquiry in Kenner was quite critical of the well design.
When the use of nitrogen cement at this depth was questioned, no one on TOD (admittedly not the entire industry) had ever known of a case.
Did not set top cement plug, used below standard grade steel, the whole BOP issue (apparently BP was paying for upgrades and maintenance for this BOP), etc. just off the top of my head.
Alan
1. Nitrogen cement is not substandard. That it had not been used at this depth does not indicate that it was the wrong cement for the job. It has been used in many other wells quite successfully
2. The top cement plug was not set because the well had a blowout.
3. I'm not sure I've ever seen a comment that below standard steel was used or that the casing had any metallurgical issues whatsoever.
4. You want desperately to link the BOP solely to BP, but it is not clear what failed on the BOP yet and whether that had anything to do with any requests made by BP or even if it had to do with a deficiency in the BOP. The MMS qualified the BOP for use less than 2 weeks before the accident (I can't remember the date, but they have to test it every 2 weeks from what I understand)
You're grasping at straws Alan.
N2 cement is @ 7% air (nitrogen) which compresses with pressure. Higher pressures will change the characteristics of the cement. That is a given.
Using N2 cement without understanding in detail the changes in characteristics is irresponsible.
There was criticism of the very tight clearances to inject cement into per the design.
and
http://www.theoildrum.com/node/6551#comment-638599
And no CBL run.
Alan
tuna -- I appreciate your kind words. But I do harbor some very harsh feelings. In fact I had to back off of TOD for a few days in the beginning. Started when the BP head man started pointing the finger at the drilling hands even before the memorial service. It took a while before I could contribute on a more balanced level.
The BP man definitely should not have done that. I haven't been in the oil field very long, but even I know the office never ever should go off on the field like that.
Rockman, you've done an excellent job all along on this site and I applaud you for it. 30 years ago I was a roughneck, but a world of change has happened since then and I was just happy to get away from it. Per your note about a "top hand". I worked with a driller from Texas and there was a problem with the mud pump in a huge mud pit. He was standing next to me and handed me his hard hat and proceeded to DIVE into the pit! One of the other hands rushed up to me and asked where he went and I said, "I think he just committed suicide"! About a minute later, we see the submersible pump jump around a bit and it starts working again. Then we see the driller follow the power cable / guy wire assembly holding the pump hand over hand as he worked his way out of the pit. Astonished doesn't begin to describe what I was feeling. When he got back, looking like a creature from the brown lagoon, with slimy bentonite dripping off him I said, "What the hell were you thinking?" He replied that he'd never ask a hand to do something he wouldn't be willing to do himself, and he didn't think asking any of us to do what he'd just done would have even worked, we'd have probably died. THAT was just to keep circulation!
What people lurking here don't realize is just how slick drilling mud is. He essentially dived into quicksand and his only hope of survival was to find the pump and use it to get back to land. He may not have been the brightest bulb, but he had more heart than I could ever muster in that profession. He knew how to be a "top hand". If he'd been on that DW rig, I don't doubt for a second he'd have tried to "get er done" no matter what.
I too suspect BP cut one too many corners, but for all these folks beating them down, remember that BP acquired multiple companies along the way, including the so-called merger with Amoco. Amoco should have been the dominant company but BP has whittled them down over the years in political in-fighting. There are still a lot of Amoco hands left who are dismayed at what has become of their once proud heritage. I know one who is resigning over this, I'm sure there are more, they weren't involved at all but are ashamed of what has happened. Remember, fish rots starting at the head.
I've really appreciated ROCKMAN's insights, but I have to add that he's not the only cat with the hands-on experience and ability to write about it that I've read on this forum. There's such a thing as a "Ring of Truth"*. He's got it and others do too. Pay attention to your gut as you read.
* Hmmm. I think that phrase refers to the ring of a hammer hitting wrought iron on an anvil. I'm pretty sure it doesn't refer to Mordor and the One Ring. At least I hope to hell not.
PS OMG. Definitely not all the stuff that comes up on a Google search of the phrase!!
PPS This appears to be what I'm talking about.
http://www.amazon.com/Ring-Truth-Inquiry-into-Know/dp/0394556631
There was testimony that indicated they were offloading mud to a supply boat simultaneously with circulating the mud out of the well. Due to this they were not able to accurately measure the net influx of mud from the well. I think nobody was watching because they knew they could not measure it.One note about the "Top Hands" on the rig floor. It appears that some of them took too much precious time trying to run the chain of command for approval to kill the well. Everyone needs to know they have the authority to "stop the job" at any time if they think it's unsafe.
True 3...it can be very difficult to keep up with mud tank volume changes even when you're not offloading. OTOH you can periodicly turn the mud pumps off and check for flow directly. Takes only about 10 minutes. I have my hands check for flow with every connction when we're drilling deep. But they had such confidence in the cmt job they didn't think they needed to check for flow...just my assumpton.
Esa, unless you have heard or seen something I have not there is absolutely no indication that those who died were waiting for anyone to give them permission for anything. They knew exactly what was happening and were doing everything they could to shut in the well, they just didn't have time. The assistant driller called the off duty Sr. toolpusher and told him the well was coming in and he needed help. That man did his best to join them but before he could leave his room the gas exploded and blew the living quarters apart and killed everyone on the rig floor. The subsea engineer hightailed it to the bridge and tried to activate the EDS to unlatch from the well (the captain said to wait but the command was ignored) but as the rig had lost all power in the explosion there was no hydraulic pressure to activate the rams in the BOP and unlatch the rig.
The two explosions occurred seconds apart and power was lost at that time. Because the BOP backup system was non-functional once rig power was lost the rig was fixed to the blowing well with no way to escape.
For those interested watch the testimony of Miles Ezell and Chris Pleasant before the MMS inquiry.
There is a bit of a writeup here:
http://www.nola.com/news/gulf-oil-spill/index.ssf/2010/05/oil_spill_hear...
Chris Pleasant, assistant mechanic: "Ah am the authority."
Do you understand the BOP logic? "I don't understand the question."
Inspected the stack. Grease and oil. Checked cables for kinks.
Doesn't know the regs. Doesn't know anything about BOP assurance.
Never saw the Transocean maintenance document.
Never involved in a well control problem.
"Mr. Jason [Anderson] was convinced we didn't lose no mud."
"Company man wanted negative test done the way BP does it."
Pleasant lowered the annular pressure to 1500 psi.
Typed and took paperwork to Mr. Jimmy [OIM Harrel] at 9:30 pm.
Saw mud and water blowout on TV in his office.
No company man in office, no one answered the telephone.
Explosion.
Ran to bridge, captain said 'Don't panic, don't hit EDS.'
Company man Vidrine said they had the well shut in.
Pleasant fired the EDS [emergency disconnect]
There was no hydraulic flow to the BOP stack pods.
Marine riser should have detached on Emergency Disconnect.
Miles Ezell, Sr Toolpusher
6:30 am daily telecon with shore asset managers, OIM, capt
busy all day with OIM Harrell conducting VIP tour
5:30 pm handover - BP not happy with negative test
Harrell insisted on negative test, argued with BP drillsite leader
Don Vidrine BP in charge of well, Jason Anderson toolpusher
Ezell ordered increased pressure in annular
BP ordered open kill line test
Jason was confident, Ezell went to dinner
met with dignitaries 7pm - 9 pm, 2010 budget
9:20 called rig floor, talked to Jason, still confident
telephone rang at 9:50 asst driller Steve Curtis
"well is coming in, mud to the crown"
Joseph Keith should have been monitoring returns
BP execs were aware of negative test problem
refused to say what he thinks caused blowout
lawyer blocks him from expressing opinion
Chris Pleasant knew it was time to get off the well, and so did the OIM who was with him.
Ezell was headed to help with the problem and likely would have died had he made it before the explosion.
Key people were not waiting on authority to do what they could to shut in the well and then to get the rig away. That is one issue.
Now as to what led up to the accident and actions taken in its aftermath - were the actions taken by the crew prior to the accident prudent and following best practice? were they overconfident to the point of carelessness? was the equipment properly maintained? safety systems checked? was the well design adequate? was there a clear chain of command in an emergency? did all hands know what to do in an emergency? was the crew under undue pressure to finish the job? did the presence of the VIPs distract from the task at hand? etc, etc - those are other issues.
Thank you, ROCKMAN.
Sobering, indeed.
Thanks, Rockman - A remarkably compact, informative summary. Very helpful to those of us (like me) who are trying to learn what happened.
Thanks for the great writeup on the initial cause of the event. It is very good to remind people that wells have kicks all the time when being drilled and they are safely handled. When I read reports of "BP knew this was a problem well because they had kicks when drilling it and so . . .", I'm a bit disappointed.
With the bad cement job going undetected it would seem that the problem would have only been delayed until the completion rig was moved onto the job. I'm still amazed that they did not run the CBL on that last job at the bottom. Particularly since they had already had the SLB crew on standby and were going to get a ticket for that without gaining anything from the bill.
It appears the cmt job failed to provide this isolation.
if the annulus is not isolated from the casing, is it possible that continued pressure and flow will weaken the cement which may have previously tested good?
if the wsj article is correct, (there is a casing breach at 1,000'), doesn't that mean that any attempt to stop the leak at the bop would not succeed?
thank you for the generous gift of your time and words.
kimyo -- the annulus is that area between the csg and the rock. The cmt is there to isolate the oil reservoir from other reserves above and below it so the oil doesn't flow thru the annulus to those other zones. And yes, once there a cmt failure a lot of other complications can ensue. That could include making the top kill very difficult if not impossible.
Had they set the top cmt plug first the well would not have blown out
I've seen this statement many times, and I've examined many diagrams of the well structure (from BOP down to the reservoir) but somehow the "top cement plug" never appears in these diagrams. Maybe that's because it was never "set", so it wouldn't seem to matter. But, just for the record, it would be nice to know where it *would have been* placed, had BP decided to set it. Would it have been up at the top of the well, at the mud layer? Or at some intermediate location down the hole? Somewhere else?
If it had the important function of preventing a blow-out, why would it *ever* be skipped?
If I am not mistaken the drill pipe was 3'000' down the well ready to do this operation when the displacement was finished, and the Haliburtan man was on call to get the cement ready. - so, just over 3,000' down the well.
Okay, it does seem the drill pipe was set at 3000 feet at the time of the blow-out, and maybe that is where they intended to put the "top plug", but why there? I don't see anything special about that location -- there's no casing or liner boundary there, or near there. Just a good "rule of thumb" to maybe pump a couple of hundred feet of cement into the production liner at somewhere around that point?
This is good stuff Rockman.
So, do they replace the drilling mud with seawater prior to placing the top plug because it makes it easier to get back into the well for production? Why replace the mud at all?
Robert -- it is a major pain to clean OBM out of csg especially if it's been sitting there for a year or two. Last January I spent 2 weeks and $500,000 doing just that on a well. I had expected it to take 8 hours. The mud has to be replaced with a clear fluid before you complete the well.
Prior to suspension of operations and retreival of the BOP stack and riser the well is displaced with seawater. The purpose of this operation is to recover the drilling fluid inside the riser, in this case synthetic base oil mud (roughly 1,600 bbl riser volume). SBM is quite expensive (>$200/bbl). The MMS would frown if the operator dumped this volume of SBM into the gulf. In addition to an economic reason there is a technical reason regarding riser dynamics. The displacment to the lighter fluid (ie: seawater) actually reduces the tensile load on the riser. Enviromental loads cause the riser to bend at depth and heavier fluids induce a downward load component on the riser increasing tension. Overall, it simply makes the recovery operation more sanitary.
I watched earlier today as they took the saw and shear topside. I see how the video feeds read "Dispersant Ops". I say they are done.
I think they're done too. In fact I don't think they know exactly what they're going to do next. It seems like the LMRP plan is kaput, though.
After watching the ROVs with their circular saws make quick work of the smaller pipes I had hoped to see them at work where the wire saw failed. Looking at this other video feed the wire did not get far. http://a662.l9789246661.c97892.g.lm.akamaistream.net/D/662/97892/v0001/r...
Couldn't they just use a thick rubber bladder and shove it ,deflated, into the pipe, then fill the bladder with water making it expand against the sides? I know they use this process for creating pressure inside a sewer pipe to de-clog. When the bladder is filled nothing can get passed it.
Pressure down well in this reservoir is estimated at 13,000 psi. A column of oil 13,000' (depth of well) exerts pressure of about 5000 psi. So estimated pressure of oil/gas when flow is stopped at top of well will be 13,000 psi minus 5000 psi or about 8000 psi. Flowing oil will have much less pressure as velocity of the oil/gas has converted the potential energy of pressure into kinetic energy of flow, per Bernoulli's equation. Obstructions that create friction in flow (turbulent flow) will reduce the pressure further.
So, as you stop the flow at the top the pressure builds and any restriction, like your bladder in the pipe, must withstand a static pressure up to 8000 psi. but maybe less like 7000 psi. Because pipe ID is around 20" the total force on the bladder would be R*R x PI x static psi. or 2.2 million pounds (1,100 tons).
Try a little research, there is no benefit in just plugging off the top of the well casing!
I'm pretty sure that most of the knowledgeable, thoughtful and/or experienced folks here know that perfectly well. And snarky comments aren't going to help educate the ones who don't.
Can someone please comment (every so often) about what is going on in the video stream? (BTW, the "drivers" of the ROVs are amazing. They control the arms and move the vehicles with fantastic precision.)
Oh, if there is some other site that is giving a better play-by-play, please post a link. Thanks.
See item number 5 re freenode in the very first comment (above).
I've got a question about the oily water that the skimmers are working on. Is there information/estimates/guesses on the percentage of oil in various parts of the slick? I understand that there's lots of variability, but in the center of the slick is it 3% oil, 1% oil, 0.1% oil or 0.01% oil for example? Is there information on the vertical gradient - does the percentage oil decline rapidly below 1 cm, 10 cm, 1 m? I ask because the size of skimmers that would be needed to handle to 3000 or so tonnes/day of oil presumably depends on the percentage of oil.
The measurement is not the percentage of oil, but the thickness of the oil layer or film.
Oil film thickness:
.0000015 inches(15 gallons/SqMile)barely visable
to .0008(1332 gallons/SqMile) much darker
http://en.wikipedia.org/wiki/Oil_spill
There's some interesting data on estimated thickness (in turn at the time being used to try and calculate and rough estimate of total spill size) over at SkyTruth. Link: Dr. Ian MacDonald's calculations
The answer to your question is that burning fossil fuels contributes to the CO2 concentration in the atmosphere. Since CO2 has a long residence time in the atmosphere, with fat-tails extending 100 years and more, and is a potent greenhouse gas, it has a significant influence on climate change, likely to cause large scaling warming in the future. And all this with a concentration measured in the parts-per-million.
I apologize for the occasional minor typos that climate scientists make in performing their research.
Well our friends at BP are giving us the "Dispersant Ops" feed. Apparently, the comments about the mistake of starting the diamond saw on the side of the riser instead of opposite to the bend which many of us here recognize as being the wise choice may have caused BP to give us the cartoon channel.
Lord only knows what goofy things they are up to now.
I get the impression that they are activating a fan.
jal
There seems to be a lot of confusion about how the diamond wire operates. It feeds from the area of the buoyancy block towards the riser so it is cutting from the opposite side from the hanging portion of the riser. So the weight of the hanging riser will open up the kerf.
It does not wrap around the riser and cut from the backside.
Here's a good shot of the wire saw in action to demonstrate Shelburn's point: you can clearly see the cut edge jetting oil toward the yellow buoyancy block on the right, and the direction the riser is hanging is clear too (away from the camera and to the left)
IMO they're not coming at it from exactly the *wrong* direction, but it's not exactly the *right* direction to open the kerf either. The side of the blade farthest from the camera is definitely cutting through metal in compression. If what my daddy taught me about chainsawing is any guide, ideally the saw would be rotated about 45 degrees toward the camera to avoid a blade pinch.
There could be lots of reasons why they didn't do that (direction of ocean currents, nearby obstacles and obstructions, etc), but it's also possible they didn't think it through. From where we couch potatoes stand, there's no way to know.
Shelburn,
No confusion here about how the wire saw cuts.
But what is your conclusion?
Did the diamonds wear out (as one spokesman explained)?
Did the drill pipe (inside the riser) wiggle and jam the wire?
Might it have helped to undercut on other side first (that is what I always do with steel pipe/iron unless I am horizontal in a miter saw)?
Why not reload the saw and continue?
Expertise appreciated.
My own MO suggestion: a section of the outside riser should be cut away with circular saws (with 2 vertical cuts + 2 circumferential cuts), thereby exposing clear access to the drill pipe, THEN cut the drill pipe, finally use the wire saw to make a clean cut of the riser with no leverage or wiggly double cutting.
And if it is no longer considered critical to have a clean smooth cut of the riser, then this last cut could be made with circular saws instead.
I realize the riser is 1" thick, but surely the circular saws are capable of cutting it eventually.
I would take a wild guess - and I do mean wild - as follows.
My theory is that the drill pipe is probably pushed over to the side where the cut was started. I think the drill pipe might well have had some torque stress in it and that they cut almost all the way through the drill pipe and it twisted on the wire and stopped it.
If that was the case and most or all of the twist was taken out of the drill pipe then another attempt might well have been successful. I'm sorry they gave up so quickly, that's not how you accomplish anything underwater - never give up.
They also seemed to be running the wire very slowly. It could have been the video and the wire might have been running 2, 3 or 4 times as fast as it seemed to be. Slow would seem safe but probably fast is better with diamond wire.
One of the great advantages of diamond wire is, because it cuts on all sides of the wire, that it can often cut itself out of trouble. If it can keep running when it starts to bind it will cut top and bottom and the piece can close completely down on the kerf behind the wire but it will continue the cut. Of course if that happens and you have to reverse you have to cut your way back out.
I don't think the diamonds wore out, it hadn't cut enough but I have heard of them clogging up with material and having to be cleaned. Of course I'm not sure of the material specs for the riser except it is certainly high strength.
I heard (saw a comment!) that when they pulled the saw from the riser, it was covered with ice - what would that do to the rest of the pathways and components? It could have jammed one or more of the idlers, slowing or misaligning the cut, no?
I'm no oilfield hand but I've cut through a lot of stuff over the years - I was watching the Dsaw cut very closely last night. When they came to a screeching halt the camera moved in for an extreme closeup of the wire in the riser kerf.
After a few minutes it was clear they were trying to back the saw out, and the wire retreated back out of the kerf in the riser by quite a bit -you could clearly sea oil increasingly spurting out of the kerf in *front* of the wire as the wire retreated.
At some point they couldn't move it any more.
I think there's real chance it was hung on the DP inside the riser, or something inside the riser; if the wire had been in a hard pinch in the kerf in the actual riser wall itself I don't think they could have got that much withdrawal movement.
Makes sense to me to think that cutting through a pipe inside of a pipe, with no way to control or steady the inside pipe, or even monitor it, is going to be tough duty. It would not need much movement on the DP or whatever to get a bad chatter in that element, which would get worse as penetration increased. No way to know if the DP has any wiggle to it inside the riser - no reason occurs to me to assume it can't jiggle a little.
Wouldn't take much movement at all to put a wire saw in a bind in there.
How about bring the CRAW down and mash the riser flat against the DP. Then us DSAW to cut it across the short dimension. If needed, use CRAW to mash riser the other direction to make it more round to fit inside collection tube.
Seems like the riser should be snipped off the top of the BOP flange, and then cutting the riser off by working the cutter around the riser, once that is removed, they can cut the DP in a separate cut, with something clamping it to prevent chatter.
If manipulated by the ROVs eventually describes it, but I'd probably put my money on the RW to win that race. If mounted on a clamp with a feed mechanism it would be faster but still most likely a number of days and even more subject to binding than the wire - and still a problem to cut the drill pipe.
I'm sure time is a major consideration on all BP decisions and this time it may have bit them, I think they should have tried the diamond wire again.
Thanks, shelburn, and for all your other good posts, too.
I want to add a little in the way of trying to figure out why they are doing THAT, as opposed to just calling all the folks working on this dummies.
If you're sawing pipe on a jobsite, and you don't support the fall-off, it breaks just before you finish the cut, leaving a jagged edge. On this particular monster pipe, the fall-off (the bent over riser stub) is more or less supported by straps running up to a float tank or a crane or something. But it's a thick pipe a mile down and you can't predict exactly how much upward force will exactly support it at the end of the cut, it might tip down quickly and tear the last few inches.
By cutting at an angle to the long axis of the riser stub you end the cut in an area of the pipe that is more in the neutral zone between compression and tension, and less likely to rip and leave you with a bad edge.
Could easily be one of the other things goodmanj lists as well.
I would guess that might be why it appeared they were about 120 degrees, not 180 degrees, across from the hanging riser. Or maybe they thought that was where the drill pipe might be tight against the riser.
Lord Browne? [Sorry. I couldn't resist. I'll go to my room now.]
The previous now closed thread talked about a rupture disk. I was going to paste a picture of a casing rupture disk here, but not sure how to do that. Yes, rupture disks are used in casing (I think BP were the the ones who first started using them). I also heard the comment that a rupture disk in the 16" casing may have blown. The purpose for these disks are to prevent casing failure when temperature expansion in a trapped annulus occurs. For shallow On subsea wells or liners there is now ay to bleed or monitor the annulus. As the well is drilled and especially when producing the upper casings and the fluid in thier annuli heat up and try to expand. However, they can't since the annuli are sealed at the bottom by cement and at the top by a liner hanger packer or wellhead seal assembly. One mitigation is to install a burst disk in a specific location such that it will rupture and releave the trapped pressure before one of the casings fail in an undesirable way.
There are other mitigations for trapped annulus pressure and this is just one. Maybe it's use is someting that will have to be looked at closely in the future.
BennachieConsultant
Interested to see your comments, I have not heard of these burst discs before, and I had my doubts that this well was going to be a producer or BP was just coming back for a production test, based on the reasoning of no monitoring of annulus pressures.
The wording in the report was a burst disc at 1000ft below the seabed. It did not mention what casing / liner string it was in.
So you are saying the burst disc relieves pressure from an outer annulus into the inner casing?
I gather it does not reset being a burst disc?
If so, once it bursts how do they "repair " the breech?
Look forward to comments
PS Do you have a link to a web page? Who makes them? Halibuton / Weatherford?
OK, from an FMEA standpoint that's a bit strange - generally, I would think you'd design failure modes that result in end-states that are BETTER than what would happen if you don't mitigate the failure. Having a casing rupture disk (in this particular context) that mimics the consequence of a casing failure is not something that I am picturing as an improvement. (Although the casing failure isn't particularly good either for that matter.)
If you have any insights into the motivation for such a design in deep water?
I agree with PeterHug, what is the point of introducing an intentional weak point (defect) in your downhole containment system?
I probably got that confusion going, so help me out. This is a graphic of the Macondo well design:
http://media.nola.com/2010_gulf_oil_spill/photo/oil-halliburton-cement-0...
BP thinks during Top Kill they were losing a lot of heavy mud at 1000 feet. If so, how? There is a liner hanger well above that point and one well below that point. Where is it going and how is it escaping? There is a 16" casing there.
Woods27 and Eggtimer1
My thoughts have been moving in a similar direction to yours regarding the potential use of the Big Flange as an anchor point. My concept centered around a design similiar to a Prop Puller, which as you may know is 3 arms that swing in to seize the base of a boat propeller as it is tightened against the shaft. Seemed to me that up to eight adustable arms could be attached to a cap with feet that would swing in and extend under the big flange and tighten the cap against the top of the existing flange. It is this ability to easily and instantly anchor the cap and then to tighten at will as required to seal that is so important, and with the proper adjust able arms could be made to instantly release if required.
This idea seemed to address the concerns regarding the uncontrolled release of pressure if the existing riser is cut and would only need to contain the existing release pressure and regarding the holding down of the drill pipe if the riser is cut since the riser could be sheared or crimped beyond its existing leaks and contained within the cap. It also offered a larger mateing surface to spread the internal pressure and the ability to fit the cap over the existing structure and contain it rather than cutting off the existing structure in order to fit (thread the needle) within the pipe.
Your similar ideas and drawings have given this concept life and I have submitted this thread on an Alternative Technology Response form as referenced above. Hopefully it will rceive a reasoned response.
Just back from the air, there are rivers of oil moving through the Gulf. moving east to west from the site........its hard to tell how heavy the oil is, but it is relatively easy to spot the flows.
East to west? So-- can expect to see oil on Galveston Isle/Bolivar Penisula soon?
Perhaps. I can only tell you what I am seeing and hearing, that the outflow from the Mississippi River isthe prevailing current in the area right now. The oil is 12 miles off Grand Isle as of today......that could change as the river goes down, but the current is the main player right now. There is a lot of oil out there....
The last bit from the Nashville rains I think is keeping river flow and stages a bit higher than normal. Was quite a bit higher a few weeks ago.
Alan
Thanks jhb50… I agree, if the pipe is sheared rather than clean cut it is likely that the full flow of the well will not be burst upon us, although I think from pressure measurements posted that most of the bottleneck is within the bop not really the kinked riser, but none the less. I also think your analogy to the prop puller is a good one. The dimensions should be well known since flanges are machined to specific specs, therefore the clamp devices should be able to be made to clamp tight. Perhaps the clamps could be tapered (like the peg idea) and a locking ring could be dropped over the set in place clamps and driven down to tighten the seal further.
NOTE: the following are not personal beliefs or images that i created or whatever. i just wanted to share some things ive been seeing about public perception towards BP. as i understand the sitaution, cost estimates range up to 20 Bn and their stock value has already dropped 50 Bn. this is before legal proceedings and does not factor in US perception of BP is now dismal. for example:
This is not a photoshop, but rather what someone DID to a BP station in NYC

there are literally hundreds of these sorts of things popping up everywhere. from my limited understanding of the refining proccess all the major players share the same pipelines so it really doesnt matter whose name is on the sign you're getting something pumped by an oil company that may not be the "brand" you're looking at. that in mind, does this public outlash at BP have any potential for signifigant impact on their business? i mean, boycotting BP stations for example wouldnt keep them from selling fuel.
But banning them from ever again drilling in US waters would have an impact. IMO, BP is to the US oil & gas industry as a malignant cancer is to a human body.
i also have heard that BP provides something like 80% of the fuel for the armed forces... i cant imagine them being banned from drilling in the US.
Before this is over, it may be hard to imagine them not being banned from drilling in US waters.
NO WAY that BP provides 80% of the Departemnt of Defenses fuels. Defense Logistics Agency buys for DoD from qualified bidders and insures multiple contracs with different companies are in place. DLA is not that dumb!
You're right. But it sure sounds good tho don't it?
How about we ban them from drilling in the US take all their cash and pay off the national debt, give each kid a laptop and a tuna sandwich a day forever.
And yes, like noted down thread, we should carefully select the new Admiral Bing for ritual punishment.
The BP Plc has fallen quit a bit now, what is your thoughts about if PetroChina would buy BP and make the company to a Chinese company. Would that make the oil that BP produces not available to the world market, and what would that mean to the price and quantity.
Another thing to keep in mind: it may be a good idea to crucify BP by banning them from US waters not just for environmental justice, not for negligence, but to convince the other oil companies to take safety more seriously.
"In this country we find it pays to kill an admiral from time to time to encourage the others." -- Voltaire
Yes. And, to increase the chances of full recovery of costs, general & special compensatory damages, future damages, punitive damages, regulatory sanctions, etc., it might be a good idea to proactively seize/freeze adequate BP assets to cover such liabilities, right now. The sometimes rather extremist folks at http://seizebp.org are circulating petitions and organizing nationwide right now. They often want to go a few steps further than I think is reasonable, but, in this case, the idea may be perfectly sensible.
But really? I know how everyone feels about them. But what do they do that's different from other oil companies? I work for a major US firm, and it's not clear that we do anything different. Most of our folks, if they're honest, are saying "it could have been us". Apart from being British, what marks BP out? And yes, I know about Texas City etc., but I can only talk about Upstream. I'm not trying to be inflammatory, just genuinely interested.
I can see your point, but in a year when BP had more than 740 US safety infractions of some sort, ExxonMobil, the Valdez ogre of the past, had 1 (one) in the US. And most of the other majors had similarly low numbers.
Admitting guilt to two felonies (RARELY are corporations charged with felonies), reckless disregard for safety (see one of the felonies, 97% of all "Egregious willful" safety violations went to BP refineries, 3% for everybody else combined ! (More recent data posted here had 600+ Egregious willful safety violations for BP, *ONE* for the rest of the industry).
BP is a different sort of oil company.
Alan
Do you know how they compare for E&P operations? Where would this information be found?
Alan: I am of two minds abut what I hope happens to BP. If they do well, they may be able to pay for a whole lot of damages and could make a number of people in your area financially, if not emotionally, whole or close to it. In contrast, Chapter 7 dismemberment satisfies the retribution instinct of people and that's not to be treated lightly. Retribution by legitimate authority keeps the mobs off the streets. I guess I am really getting to the endless debate in the criminal justice system between rehabilitation (I think Exxon Valdez did that for Exxon) and retribution, two concepts that are frequently in unresolvable conflict. Perhaps, the solution is rehabilitation for BP as a corporation and retribution against its officers and other responsible parties. As the British would say: "I want to see them in the dock." Tony Hayward would understand what I mean.
Well I think its a slam dunk case. Its pretty clear that the era of cheap oil is over I don't think thats and issue. Whatever we get from now on out is going to be hard to get and expensive period. We need to ensure that companies go the extra mile. Draconian punishment will do this.
Treat it like nuclear war you have zero chances to make a mistake. Some how by the grace of god if you read some of the stories we managed to avoid this. In the end the fact it was a zero mistake game seems to have kept us from crossing the line.
If this means deep water is too expensive now well so be it sooner or later the price will make it profitable even with extensive safety matters.
Or not deep water is not going to solve our oil problem in any case cheap, expensive or simply not done at all.
In the end its a place we really don't have to go too and probably should not. Regardless let people paying for 200-300 dollar or more oil sometime in the future make that call now is not the time. Let them have it they will be glad we left it or have decided to change and don't need it. Dismembering BP is the solution and pushes the decision out where it should be made.
How soon till people stop pumping gas at bp stations - perhaps feeling embarrassed that anyone might see them patronizing bp? I thought of all the people who own those stations, how their livelihoods may suffer next. I wondered if bp stations will try and start price wars as the only way to bring in customers.
I have no idea if my thoughts will come to pass. But this affects so many people. And many of them who will be affected are people who in all honesty bought a gas station. Or leased it. I'm not sure how it works with such franchises.
In any case if people are defacing stations or simply making their own protest signs, this is a huge swing in public opinion. And the next step will be boycotts of bp stations... or fear of pumping gas there. I can totally understand it all. Yet I also feel sad for the owners and workers there.
EDIT: Well, here it is already - all over the world!
Protesters Gather at BP Gas Stations
http://www.nytimes.com/2010/06/03/us/03boycott.html?hp
thats whats been going through my mind right now. part of me is glad to see the public outrage, but its being vented toward regular people just trying to make a living off of razor thin profit margins. i've heard so often about some of these owners actually losing money on the fuel and only really making anything off the convenience store end.
gotta feel bad for the owners. Like the poor frenchmen that owned the mcdonalds in the france that got destroyed. People are such animals.
Just to be clear: people who have no way of knowing what % of pump sales go straight to BP, and are attempting to merely boycott the corporation who have the worst track record in their industry in this country on safety, who have just initiated an economy-wrecking eco-catastrophe, who pump large sums of money into the political system as an apparent quid pro quo for less regulation than they get operating other places, who just killed 11 of their own workers, whose most visible executive just expressed a wish that HE could "get his life back"... these people are "animals"?
They appear to be concerned citizens, if a bit misguided in tactic. We need concerned citizens. Tony the H I could live without.
As one who does contract work for small oil company I know that gas stations all get the gas from the same refinery for a given area. Some metro areas have two or three refineries so the gas may come from any one of them.
Here in the St. Louis area are two refineries, one owned by Shell, one owned by an independent refinery company (used to be Clark Oil Co.). The gas station owner gets prices from the local refinery and thus posts his pump prices based on that wholesale price, plus the cost of additives (like ethanol) that the different brands may add to the tank load of gasoline. The additives are shipped from the ethanol refinery or chemical refinery in RR tank cars that are positioned at the refinery loading sites, which allow tanker trucks to make a trip to just one location to fill up with gas and additives (depends on the brand being sold). The raw gas is the same for every station, but the additives are slightly different.
Gas at BP stations probably did not come from a refinery owned by BP, nor did the oil likely come from a BP well. Boycotting a BP station is like refusing to eat any fish because a few fishing boats use nets that can trap sea turtles.
People that boycott, no, people that destroy other people's property, yes. I apologize for not making that distinction. I was thinking about my example where the rioters vandalized the McDonalds.
The price for regular at the BP across from our shop was down to $2.51 this morning, 21 cents cheaper than the guy up the road. No idea if this cheaper price is related to the oil spill and BP. There was a line for gas when I left work this afternoon. The owner is a great guy; he sells off-road (untaxed) diesel to farmers for 2 cents over his cost. I buy my tractor fuel there.
BTW, most stations get their fuel deliveries at market price regardless of what brand it is. It's all the same stuff. The proprietary additives are added when the tanker gets his order for a specific customer. Chevron regular is the same stuff as BP regular exept for the "Techron" and "Invigorate" additives. The only exception is dealers/brands that specify no ethanol.
BP with "Invigorate"..... sounds like they're putting Viagra in my fuel.
Yeah, unfortunately we can expect people to get mad and respond in those ways. But, I believe that response will be quickly replaced by... BP is not at fault... their number just came up. Instead, we're each at fault for being oil consumers and acting blind to the risks.
Nope, sorry thats not gonna happen. There's a strong possibility many, many people are going to be wiped out financially (job losses) over this. Could be a LOT of people having to move from the beach areas, property values destroyed, etc. Lots of hatred now building up at BP, but also with gov't response (its perceived failure, right or wrong).
a brand new BP station just opened in my neighborhood. I'm not sure why I should punish the family that just built the station because they are somehow connected to this disaster. I know a lot of others will boycott their station. Part of me wants to boycott, but another voice, which seems to be louder, is telling me to help these poor people by buying their gas.
part of my confusion is related to not knowing exactly what sort of business relationship these franchises have with the parent company. Maybe some of you corporate people can explain....
Or maybe you could ask them, i.e. initiate a discussion and see what they think and then make your decision.
The only thing BP about the fuel is the additives added to the premium grades. In theory BP can be very slightly hurt by boycotting of the premiums, but most of the rest of the fuels are just bulk blends. In general, boycotting the BP stations just hurts the value of the franchise, which is not very much to BP in general.
The Sponge Bob image is much more true than most -including probably the author- know; the sponge beds and Greek divers of Tarpon Springs, FL are most likely about to be completely wiped out, since this has reached the big bend area.
No offense to the 11 dead workers, but it was just as likely they were trying to escape and were blown away by the explosion.
Well, it is offensive to the dead.
"Up in the crane, Mr. Sandell saw another worker on the deck, assistant driller Donald Clark, a 48-year-old former soybean farmer from Newellton, La., bolt for a set of stairs leading for the area where workers were fighting to control the well."
http://online.wsj.com/article/SB1000142405274870411350457526472110198502...
And Dale Burkeen died after lowering one of the lifeboats.
"Dale Burkeen was a crane operator on the massive oil rig that exploded in the Gulf of Mexico last Tuesday night and was trained to lower crew members to boats in such an emergency."
http://www.neshobademocrat.com/main.asp?SectionID=58&SubsectionID=466&Ar...
king - they all might have been running from the rig floor those last few moments. And I wouldn't fault them for it. But there was opportunty to run earlier. I've been on the drill floor twice when you could hear it "winding up" but fortunately neither blew out. Varies with the rig design but you can get pretty far away in 30 seconds. You don't have to work on a rig very long before you run thru potential escapes routes in your mind 1,000 times. But your comment makes me address an issue I haven't seen brought up: why didn't more hands rush to the rig floor to help with the kill? Very simple answer: the last thing you want on the drill floor when a well is winding up are hands that aren't part of the kill team. The other hands did the safest thing for the floor hands...they stayed the hell out of the way.
I take no offense to your statement.
What ever you may think was likely, they were, if fact, trying to shut in the well, and others were headed into the danger zone to try and help - headed there knowing exactly what was going down.
Initial Exploration Plan Mississippi Canyon Block 252 OSS-G 32306
http://www.gomr.mms.gov/PI/PDFImages/PLANS/29/29977.pdf
On 03122009 some one wrote "noted Schexnaldre". One year to the day, permission to cap was requested.
For those who want graphics of the bathymetrics, this is a good document.
Page 2-1:
2.7 Blowout Scenario
A scenario for a potential blowout of the well from which BP would expect to have the highest volume of liquid hydrocarbons is not required for the operations proposed in this EP.
Yesterday, I posted a question
about the first well in MC252,
which PB capped and abandoned,
as I recall.
The reply was a question, where
did I hear of the 'first' well?
This is not where I first heard
of the existence of another BP well
near the wild well, but look at
the pdf cited above ... 29977.pdf,
pages 9 and 10. The latitude and
longitude of each of the wells
is listed there. They are near
each other. The first well was to
be finished in July of 2009, according
to the pdf. Is the well completion
report to MMS public information?
Is it possible to find out if all the
testing was done for that well?
So, as in my earlier question,
how well (good) was the first well (hole) capped?
Is that one safe? Was there a pressure
test done after the cementing?
Thanks, if someone finds out more
about the first well.
Now up to six different feeds on same page (Flash and Windows Media)
link
That link should be http://www.deepwaterbp.com/
Thanks for this link! I wish BP offered it on their Home Page.
BP is now offering all twelve ROV camera views ...
Live feeds from remotely operated vehicles (ROV)
A couple don't seem to be active at the moment.
I think what we are seeing with the 'Dispersant Cam' is actually them trying to gauge the flow rate,and is NOT dispersant.
I don't know .. I vote dispersant.
No, I think it's dispersant. I saw a small wand spraying a "clear" fluid into the flows near the kinked riser, just a little while ago.
CNN reporting the LMRP is being dropped for the tophat instead due to the ditching of the diamond saw which in turn will lead to less of a seal and more of a flow. CNN is the only agency I see reporting this, does it have factual basis?
Edit Link: http://www.cnn.com/2010/US/06/02/oil.spill.cut/
They are lowering "CRAW" in a horizontal arrangement so I think that confirms they are cutting the vertical part of the riser. So I think yes, I am scared...
That new slit seems to have greatly increased the flow rate, at least to these untrained eyes.
1) Nibble away at bend area of riser to find DP, bent or fractured?
2) If DP is bent cut it, if fractured/severed continue with DSAW around circumference base of riser
3) Riser comes off… cut job complete !
Or… we can all just sit around and watch our planet be destroyed… which by watching current live feed, is exactly what BP is doing.
Some things i learned from the BP “leak”?
1. mud should never come up out of the well without being gaged and alarmed for imbalance.
2. the method of setting plugs may not strong enough, not reliable enough
3. the current test procedures are not long lasting enough nor rigorous enough to detect pending failures
4. backup plugs are not being put at bottom such that a failure of the first will be caught by the second
5. the kill and choke lines are not large enough in diameter to beat a blow out with pill
6. the BOP is not protected structurally from a riser collapse.
7. the shear in the BOP is not strong enough and not reliable enough to cut a drill string joint
8. the rig detachment system, LMRP, totally failed to do its job (and it isn't even in deep water)
9. the platforms need safety chutes to get personnel down to the water and life boats in less than 10sec
10. doors were exploding off and crushing people. Alter the layouts to prevent this.
11. only certain rooms were explosion-proof (non-spark). Looks like ALL rooms must be spark-proof.
13. hot surfaces (engine exhaust manifolds) need to be water cooled to prevent gaseous ignition.
14. engine governors failed when natural gas got into the intakes. Must have auto intake close-offs.
15. BOP test and rebuild procedures got to be way sloppy. Leaky fittings and test jaws were left in.
16. management was allowed to over-ride safety. Always a really stupid temptation to fall into.
17. the BOP is not easily replaceable. Provide tracks below and above, so a second BOP could slide in, (needs sq flanges).
18. provisions for drill string section to be sheared out and dropped into side pocket to allow clear space for valve shut downs.
19. provisions for dealing with high velocity drill strings in blow out ejections. Need brakes before shear engages.
20. annular rubber was chewed apart, yet management said “So what!” Really a criminal act.
21. violation of safe procedure by filling with seawater rather than balancing mud. Criminal act.
22. totally missing: containment funnel from seabed to surface. 100' diameter at bottom. 1000' at top.
23. totally missing Stainless Steel floating ring (pool wall) at surface. Jointed, with positioner/tentionlines to 6 ships outside circle.
24. failed to take into account sand erosion of metal containment tubes (use AR plate abrasion resistant, or keep blow outs short)
25. no velocity detectors in BOP for auto-kill function when ever oil or gas moves through it too fast.
26. no gas-lift detection, which would be a huge indicator of pending blowout. (use tiny doppler LEDs)
27. no pause in capping procedure to measure stability of all components. (Hurry perturbs system and masks the small stuff.)
28. no permanent downhole sensors that would detect motion, pressure bumps, slipping plugs?
29. no containment corral for floating oil that actually works in calm weather, let alone storms.
30. no reserve of tankers and centrifuge ships for cleanup, adequate to the well production rates
31. no safe way of navigating fuel-laden, explosive risk, fire risk, waters. Need un-manned ships.
32. no certification process to guarantee the BOP was up to the task across new materials & pressures
33. both in and out mud crews should have flow meters and a kill switch in their grasp at all times.
34. improved gas kick detection and venting systems are needed.
35. emergency crimps, like the big claw shear, but to crush the riser flat , hold press to stop the flow.
36. A structural tripod to 20' over the BOP can protect it from bending, leaning, collapsing risers.
37. cement structural integrity tests and monitors that distinguish between plug and liner fails
39. improved pontoon protection to avoid sinkings via penetrations by fire or falling objects.
40. the riser did not fail gracefully. It needs breakaways, floatation, and reuse plans.
41. replacement riser with valves needs to be deployable within 24 hours, not one month!
42. the BOP must be designed so that a proper junk shot really does a “stop leak”.
43. the junk shot needs some scientific development until it relly works, else quit it all together.
43. need emergency water spray at the deck to quench any explosive atmosphere there, spray to lift blowout flame up another 100'.
44. eventually the 11 man deck crew will be replaced by robots
45. to keep generators running in a methane atmosphere might require cutover to oxygen bottles. Else just go to batteries.
46. need to have more life boats because people will not always wait to fill the boat when panicked
47. if the ocean is going to catch on fire, then life boats need to be submarines, 3' under with O2 tanks.
48. BOP must have better external access to forced completion of the shears. Allow direct mechanical squeeze.
49. need new ideas on velocity limiters near well bottom. Velocity must be kept below erosion speeds.
50. may need to allow ballistic ejection of the drill string just to let all the valves close tight.
51. need sufficient sensors and safety computer to choose the best lock down procedure, to take ~2 sec
52. killing off large swaths of flora and fauna at some point must be treated as equivalent to murder
53. damaging other people's livelihood is a civil matter, but deserves an escrow account for instant use, like unemployment insurance.
54. putting a cap on economic damage is like putting a cap on how much a bank robber must return
54. it must be made a felony to kidnap employees (so as to force them to sign claims waivers)
55. methane is a very bad green house gas. Every cubic foot of gas released must somehow be recovered! How?
That's a great list.
Great list; hope most of the mechanical details get instituted in future hardware. Thanks.
Nice list. Maybe you should be on that Presidential Commission. No, wait, they've got James Cameron. Never mind.
A Masterpiece!!!
ndyer1, dear sir or madam, what discipline has the privilege of your employ?
whatturn
ndyer1 -- really a lot of thought went into preparation of this list. Truly the President's commission should be evaluating your points for incorporation of new safety features into rig design.
Not to detract from your list, but to add a few more lessons learned:
A. six casing spacers were used instead of the prescribed 21 spacers
B. "o-ring" like seal never used for final 7" string
C. one BOP ram never was functional--kludged up for pressure testing.
D. 51 bbl cement not enough, N2 - no good
E. thin casing used in high pressure, lied to MMS about risk.
F. Management failure: shouldn't have the ability to distract mud flow experts and CBL experts. Shouldn't celebrate safety on rig, ever.
oe
Hi Ndyer1,
It would be really great if you posted an explantion of each of these items and where it came from
Pragmatic -
It seems that the ONLY way they can now capture the oil flow is with a tight, high pressure seal to the BOP collet connector top flange. Since they are not doing it, having decided to mangle the pipe above it with their claw, this approach will shortly become another failure - that's the best scenario. And, by the way, since they thoughtfully started then abandoned a cut right above the flange, they will always have a nice leak path right there, which will not be addressed by the "cap".
Since they are now going to claw real close to the BOP, unless the claw is balanced during the cutting just so, they risk putting all manner of uncontrolled loads into the BOP and upper wellhead pipe. Though I have written previously that the BOP external structure seems to have survived fine the total plastic hinging of the riser pipe with the drill pipe inside, I am much less sure of its integrity from the clawing maneuver. I am pretty sure the riser collapse is a BOP load case for the design team, while the claw loads is probably not. The worst scenario is structural failure of the BOP and or upper wellhead.
CUT the BOLTS! CUT the BOLTS! CUT the BOLTS!
Dimitry, if you mean grind the nuts off..? Grinding high tensile works because of the high temp at the abrasive face [in air]. Can you get that underwater? Too much lubrication? You want to grind fast, not just wear out cutters?
Lots of punters on here have said that, but what (and where) exactly do you cut? The head of the bolt? The nut on the bolt? Both? Neither? None of those approaches actually achieve much - in terms of releasing the screw thread holding the two flanges together (if there is such a thing) ... and there are LOTS of bolts around the flange - lots of tedious work for the ROV operator to get to each one. Cutting the bolts just seems wrong to me. But I was an architect, so engineers will be scathing of me anyway ...
Rockman I read your posting about how the well was drilled. Right on. I worked in the oilfields for over 50 years helped drill a well at Pt Sulphur La in 1954 to 22570. Deepest well in world at that time Old inland barge steam power. Same plan then as now. Pressure Test bottom of casing or liner. If liner pressure test top of liner. The more things change---The company I worked for believed that if the BOPs were to be tested to 5000 lbs for 30 minutes that did not mean 4900 for 29 minutes. Took bad kicks but never had to leave rig with shirt tail on fire Worked on some of the early day “OffShore rigs” 1950 vintage Some of ODECO’s very first. Worked in 30feet WOW Old jackups and platforms with Converted LST as tenders. Worked for years for a wire line service company and did pioneer work on running conductor lines under pressure. The old original “Injector, Grease seal lubricator.” CBL? I have seen CBLs interpreted as “Possible partial cement bond”. What does that mean? Had to work with several “Company men” on Hi Pressure jobs that didn’t want to follow all my companies safety rules. My company all ways backed me up when I told Company man “Sorry but it our way or rig down” I understand from one report on this job that Stumberger told them that and even called in their own helicopter “When told none were available” to bring their hands in. Insult to memory of hands killed in explosion to say “Might have been running” Old time Tool Pusher saying “Wells don’t blow out. “People let wells blow out”
I'm going let this idea go RE: The dispersant spraying into the plume. Could BP add regular or some special marine dye that is detectible in UV. Install a UV spotlight on skimmers and they could work at night when it isn't so hot. I heard it is absolute misery out there. RH close to 100% and temps in the 90's. I use UV headlamps for geology purposes, some things are easier to find in the dark when they fluoresce.
WAY outside my area of expertise but that sounds like something that might be really worthwhile. I don't know about UV materials but we used to use dyes to find pipeline leaks (before sonar) that you could see in ppm.
A tracking fluid - dye, radioactive, etc - that could easily identify any dispersant/oil from the well could go along way to identifying what underwater plumes come from the well and maybe even give a quick estimate of the density.
Good luck getting BP to agree to that.
As for the "absolute misery" I guess I don't have a lot of sympathy, that's what all offshore hands (except in the A/C office) go through every day.
Thanks Shelburn, Lots of questions about bonding to hydrocarbons, sure works well will glycol. I'm going to throw it to a chemist friend and a former NOAA corps officer bud who I used to climb with.
Way late in the game though.
The oil should flouresce in any event. As a mudlogger I got to use a "flouroscope" to check for oil shows. (The flouroscope was pretty much box with a black light and a viewport.) In fact the color of flourescence tells you something about the quality of the oil, the whiter the glow the lighter the oil. I'll never forget the first well I worked on, the oil show came in BIG and the shaker house smelled like diesel fuel and my sample of cuttings glowed the color of a radar screen in some old war movie!
I don't know oil and I don't know technology, but I'm of your era and just wanted to say thanks for this post. It reminds me of those days when integrity, honesty and taking pride in doing things the right way seemed to be a little more important than they sometimes are today.
Whoa.
BP has changed their former spillcam page and is now offering feeds from twelve -- 12 -- different ROVs attached to six different ships:
http://www.bp.com/genericarticle.do?categoryId=9033572&contentId=7062605
Thanks.
Why no attempts to use explosives yet ?
They could have tried a number of approaches up pipe if you will and determined what worked.
Also fairly easy to test some approaches on shore or elsewhere.
Also looking forward explosive bolts might be useful. None of these problems seem much harder than your typical large rocket engine. By that I mean it should be considered rocket science and treated as such. But we have solved engineering problems which have similar severe constraints. And judicious use of explosives are a common solution for similar classes of problems in aerospace.
I just don't see any hope until they get a reasonably clean cut made. A rough cut followed by a diamond say cleanup is fine etc. But get the dang riser cut.
Anyone know the diameter of the bolts on that flange? I’ve read elsewhere on TOD the pipe itself is ~ 22 inches (OD). If true, that would make those bolt diameters ~ several inches? http://a662.l9789246661.c97892.g.lm.akamaistream.net/D/662/97892/v0001/r...
1.5"-2.00" maybe. Previously someone posted a schematic from a catalog page for this collet connector - probably had bolt size in there.
was in thread 2 or 1 of this post I believe.
Torque is the issue.
n.b. BP main ROV feed is looking at the LMRP cap #2
(the one to seal over the flange).
torqued to 28500 ft-lb
going by memory so dont rmbr the size and thread specs
I don't know what the bolt size and torque specs are for the riser but consider this:
A 20" ANSI B16.5 600 class flange uses 1.625" bolts torqued to 2,044 ft-lb and is rated for about 740 psi working pressure under normal conditions. It weighs 590 pounds.
A similar 1500 class flange this size is rated for 1,850 psi working pressure and uses 3 inch bolts torqued to 13,320 ft-lb. It weighs 2,050 pounds, the bolts weigh over 60 pounds each.
Now ramp this up for the riser which is 10,000 psi working pressure plus has to take various axial and bending loads never seen by a standard flange. The BOP alone weighs 450 tons and this flange has to lift it.
You are WAY outside spud wrench and cheater pipe territory.
Then CUT the BOLTS!
Don't mangle the only pipe you got to seal to!
I've read over and over again how we should be respectful 'cause the people doing this are the best of the best.
Well...I want to be respectful and all...
But they are doing it wrong. Clawing this close to the BOP risks finally compromising its structural integrity or that of the wellhead pipe. They will end up with a completely unsealable end. The "cap" will fail, like everything else they tried.
If they go with the mangler, I think it's over until the relief wells come in.
Someone posted some good reasons why you dont' want to try to mess with the bolts. I agree exposing a flange would be ideal mating surface for something to collect the oil. But think about how that is going to go down. As the bolts are cut and attempted to be removed (and note what shelburn pointed out about these bolts.. maybe 3" or more in diameter and made of who knows what) Cutting them all will be no easy job. But as you are cutting them you are going to create yet another leak point and how will you see to get to the remaining bolts? And even if one of the probably 20! bolts on that flange gives you trouble.. well what will you try to seal to than? I think this is one reason why they have attempted to do something as far from the BOP as possible and make it work, the more you cut or tamper with the fewer options remaining. I believe a chance exists that a seal can be made at the flange itself. This is a clean precision machined surface, or at least as close as we may get down there at this point. Go ahead and use the claw shear to cut off the riser just below the kink and put the LMRP cap no.2 over the riser pipe and seal around those flanges. Several have commented on the idea spawned from a post by Stvrob_63 and it seems to have passed the mustard test for the most part. I think the most encouraging was noted that goodmanj and seconded by shelburn and that is the need for a mechanism to tightly seal at the underside of the flanges may not be that necessary since once the oil starts to flow a chimney effect would seat the cap, or thats how I understood it. Nonetheless I submitted the idea for nothing else but to try to help in some way even if its comic relief only. A drawing of latest options based upon input from many, its not as detailed as it could be obviously but it trys to depict the idea that sealing at the flange could be a possiblity and could already be a plan waiting to be implemented. http://picasaweb.google.com/KWoodME/OilCap#5478427315003016306
Maybe, but one would need some form of O-Ring seal on the cylindrical surface of the flange and it is quite short and probably rough. You can't seal an O-ring on a rough surface, but you can seal a gasket.
Since there are only 6 bolts, cutting them and coming in axially with a bonded gasket on a new riser flange I think is easier to do, than coming in with a placement critical short dimension O-ring seal that is probably not going to work.
But all of this is academic, as they seem to be giving up and placing the old "hood" over the mangled up pipe.
So you cut the bolts, zip right through about 72 sq inches of hardened steel. Then what? You think they will drop out of the flange themselves? Corrosion, burrs from the cutting, torque from the bent riser, or a tight fit to begin with mean you'll need to drive them out. No guarantee it'll work.
And then you still have the darn drill pipe locking everything together, right? Gonna inject a hamster through the kill line and have him climb up and hacksaw the DP off?
After the bent riser and drill pipe are cut off lots of options open up, including unbolting the flange, although folks with more experience than I have said that is nearly or completely impossible at depth --these things are bolted together on the surface, then lowered, so we have heard. Besides, there is a latch connecting the LMRP to the BOP. That means while our imaginary crew is busy slicing the bolts, there will be a whole lot of snarking going on by the folks who know about the latch.
I know we all want this thing stopped, and we all have great ideas we'd love to try. But some of them just won't fly.
A small note:
The bolts go through the flange - cutting them will not make anything leak... until you get them ALL cut and the riser end pops off... if you get them all cut.
http://www.geoilandgas.com/businesses/ge_oilandgas/en/literature/en/down...
Bolt dia 3 7/8"
A respectable size. Cut them anyway.
Have they tried to operate collet hydraulics?
The feed from Skandi looks like they maybe clawed off the riser stub. It looks like a piece of DP has come out or perhaps a new pipe is in the way. The whole thing is swaying with the flow, which looks massive.
CUT the BOLTS!
Intuitively, from the Skandi view, it looks like the whole thing is about to blow.
ROV 2 from Ocean Intervention is working something, but I can't tell what yet.
right now:
Subsea 7 at 00:47:12
http://www.bp.com/liveassets/bp_internet/globalbp/globalbp_uk_english/in...
just looks like the old scene - just a view from slightly above.
The pipe in the foreground is one of the choke/kill/... likes they cut with the small circular saws. It is flopping around,
since the other end was cut to allow the shear to get on the riser.
The riser is visible in the left side of the frame, behind the red hose?
It is just that badly bent and kinked - more than 90 degrees.
Right now I can see the top of the kink pretty clearly, but it is usually hidden in backwashing plume.
Cool, a big burst of white snow-like stuff - hydrate? gas bubbles?
Off to the right of the riser one can see the flat fan of oil spewing from the wire saw cut.
bring on the CRAW!
Bedtime thought:
And we are here as on a darkling plain
Swept with confused alarms of struggle and flight,
Where ignorant armies clash by night.
— Matthew Arnold, Dover Beach
I cannot believe BP is giving up on the diamond saw after one feeble and poorly situated attempt. Surely they have a spare blade if that is the concern, but trying to use a bandsaw to cut into compressed pipe will pinch the saw every time.
Now that they should have a better appreciation of where to start the cut, I.E. at the point of minimal compression (opposite the bend in the riser) they might actually realize some success.
To throw in the towel so easily with so much at stake is beyond belief. I had given BP the benefit of doubt up to this point but now it appears that whoever is calling the shots needs to be replaced.
slymy,
I think they've gotten scared off by the powerful jet of oil/gas coming out of the slit they already cut. I don't know if it is an annulus issue, or if they've barely broken into the drill pipe itself. IF so, and it is that powerful (check out he videos and imagine the psi strength, this is not your dad's pressure washer overcoming 2270 psi pressure at the seabed. I think it is possible the CUT machine was damaged by the oil coming directly at it at something greater than 5000 psi through that small orifice. They probably realized going back down there and doing it again would end the same way. The definition of insanity is to do the same thing over and over expecting a different result.
Of course I'd be remiss if I didn't post this perfect depiction of what is going on, provided by XKCD.
widelyred,
I noticed the obviously higher velocity plume from the new cut. This is probably due to the smoothness of the cut creating laminar flow as opposed to the jagged, irregular openings from the ruptured kink which cause turbulence. Also, Since the new cut is the first encountered by the escaping oil, it will necessarily be at a significantly higher pressure than the downstream plumes. We really need to see from other angles.
Nonetheless, The riser must removed, otherwise the plan will not work. If necessary, the pipe can always be crimped later to reduce the flow if the LMRP plan fails.
Looks like a large leak below the flange ... what is that ?
Hard to say from the angle but I think thats the leak at the cut in the pipe made by the diamond saw.
I found this site while looking for information on BP's blowout in the GoM.
I am appreciative that there exists a site that espouses the desire to help break our western civilization of the hydrocarbon habit. If we as a society don't recognize the coming limitations, little effort will be placed on managing our current resource, nor developing suitable alternatives. I've found a few sites that don't venture to complete doomsaying, sites like this that promote sensible solutions and allow those with vision to plan for the future. This site has similarities to Whiskey and Gunpowder without the additional dark forecasting. Rather it brings a more focused realism.
That said, some background on me. I'm an accountant by day, shadetree mechanic on weekends with experience in mining, logging and pulp and paper (working across silos from management, engineering, accounting and operations).
I know from experience that large industrial companies get locked into bureaucratic niceties not afforded to smaller firms (tongue firmly planted in cheek). I also know that engineers are guided by management and corporate structure and that every task in crisis tends to be micro managed.
My thoughts on the topic at hand and the various attempts put forward for public consumption are from this perspective.
BP has every interest in seeing the well killed, however their various approaches and attempts are being put together 'on the fly' and that brings with it an inherent 'maverick' style that we, as outsiders can analyze second by second and second guess and suggest alternatives that may or may not prove workable. I can't imagine working under this pressure while live feeds broadcast every move to the world. I have to believe it must make working conditions that much more difficult.
And how it can it be otherwise? I've been involved in several crisis where teams are assembled to to rectify issues ranging from the extremely complex to the mundane. Rarely is there a perfect solution, nor is it accomplished quickly enough for management, shareholders, employees & other stakeholders. And occasionally there have been missteps that required stoppages, new analysis, novel approaches and implementation of unproven procedures.
Sitting on the outside is far different that being 'in the arena' with the lion ready to take your arm out of it's socket. We have the luxury of saying 'cut the riser here, cut the NUTS off the flange, do this. Guys like ROCKMAN, Gail, Heading Out, Prof Goose, et al. know this all too well. ROCKMAN is absolutely right that this blowout will be contained, the question that remains to be answered is when: 3 months? 6 months?
This problem in the Gulf won't be the last 'unintended hydrocarbon excursion' either, but my hope is through the efforts of those who belong to this site will help open the public's collective eye to the absolute need to cut our dependence on oil. Not foreign oil, but oil - ours and theirs.
Unfortunately, I don't see an easy transition. I can't see our North American population wanting to live more simply, advocating restraint in wants over needs.
This blown out well on block #252 Mississippi Canyon is a rude awakening for the masses, foreshadowing a microcosm of a future with dwindling, inexpensive hydrocarbons. Dirty, fouled and filled with failure.
Paul
Alan, the lowest stage of the river is usually late September, although it starts falling around now.....
I’ve worked in the ‘fishbowl’ most my life. This blowout was caused by shortcutting safe, time tested, proven procedures. I will not fall to lower my lifestyle for your ideology when good common sense should rule.
You will not WILLINGLY lower your lifestyle, but you will anyway. You are in the vast majority. Societies do not decide to collapse, it is the inevitable result of choosing not to adapt.
Well put Klondiker.
Welcome, Klondiker. There's a place in your profile where you can describe yourself. (That way you won't have to redescribe yourself on threads.) As a newbie from only last week I can report that you'll find this a hospitable community, interested in what you have to say (as long as it's "signal" - but there's forgiveness for mistakes made too).
would it be impossible to believe that all if not most of these ROVs are being driven by computers or a computer instead of human pilots ? I continuously read that people have never seen ROVs operated this well..
You're giving computers too much credit. The type of hi-fidelity control seen here almost certainly needs the cognitive abilities of a human operator.
Post from ROV driver on Fark
http://www.fark.com/cgi/comments.pl?IDLink=5358799&startid=60840602
Scroll down to kendelrio's post.
Thanks, I like his comment so much, here it is:
kendelrio [TotalFark] 2010-06-02 01:46:00 AM
queezyweezel: Watching the ROV work; they obviously don't have the right tools for the job, and the ROV operator is not exactly a carpenter....they're having a lot of trouble cutting the pipes. Trying to inserte the saw blade into the cut and then start the saw is never a good practice.
Ok, I am one of the operators of the ROVs. Let me explain to you what you are seeing. You are seeing a hydraulically controlled non-spatially correspondent 7-function rate controlled arm operating at 3,000psi. It is not coordinated like our arms. We also operate by looking at a TV screen. If you start the blade before you go in, you will be getting jagged edges and damaging more than you accomplish. You also fail to realize the pipe will not fall down and pinch the blade as a piece of wood would. (There is a crane on the surface rigged to hold it in place and lift it clear when the cut is complete.) Also, the arm is controlled by what amounts to a digital joystick (fap). It has only on/off functions in a rate controlled valve, not graduating degrees of control like you would get out of a proportionally controlled valve or servo.
As far as the tools go, that is a hydraulically operated 54" carbide tipped graphite blade designed to cut through hardened steel like the proverbial knife through butter. Guess who gets to tool up those "not the right tools for the job". Do you think we would go into a high profile situation like this just to make ourselves look like dumbasses?
Also, the pilot on the stick has over two thousand (that's 2,000 for you letter challenged types) hours of flight time. There isn't a man with less than that being allowed to even **look** at the pilot chair right now.
Understand working in water takes most of the rules you have learned on land and ass rapes them and sends them crying home to mama.
I am willing to let this go as simple ignorance, not malicious stupidity.
BTW, the article is absolutely crock.
What our control room looks like.
sphotos.ak.fbcdn.net
/hot like an ass raped rule
Access Denied
You don't have permission to access "http://sphotos.ak.fbcdn.net/" on this server.
Reference #18.146f1160.1275548780.3423de9
H. Rider Haggard:
Click on the original Fark link and see the photo embedded in the post.
http://www.fark.com/cgi/comments.pl?IDLink=5358799&startid=60840602
Scroll down to kendelrio's post.
Thank you!
It is definitely humans. Most of those pilot get 1,000 hours stick time a year and have many years experience. And for this only the best pilots will be on the boats.
Computers can help especially when just observing like auto hover, auto position etc but when they are working its a human hand on the stick.
So, the plan now (according to the CNN article referenced above) is to use the same top hat that's been "resting on the bottom" since May 12. But that was presumably designed for less of a flow (the number usually tossed around here for a while is a presumable 20% increase with the riser cut) than there is with chopping the riser - what kind of a problem does that present? They haven't been working on a different sized 'hat' for the greater flow while cutting..?! This was Plan B for post-riser-cut, and the capture structure for Plan B is the same one that you designed weeks ago..? This doesn't strike me as promising on the face of it... we've increased the flow 20% and we're going to use the same tool that captured 20% of the smaller flow to rein the larger amount in..?
The top hat weighs two tons (referencing same article) and has presumably a 4' diameter footprint, and has not apparently disappeared into the mud. I should think that gives some data that would be helpful in designing a larger capture structure that rests on the bottom, weighs about that per unit of footprint area, and doesn't rely on a tight seal over the equivalent of a jet engine to capture the muck. Couldn't a much, much larger dome than the top hat be put over the area to disperse pressure and heat of some sort be pumped in to help inhibit crystal formation? Not killing the well obviously but just something to keep most of it from spilling all over creation.
don't confuse the "top hat" with the "LMRP caps".
check out the Kent Wells technical briefing of May 31
http://bp.concerts.com/gom/kentwellstechupdatelong053110.htm
At about 03:00, he explains there are two versions.
Because the wire saw isn't working,
they'll used the 2nd version - the one WITHOUT the slots in the sides, that "will seal down on this flange".
This second version just made it to the sea floor at May 31
http://bp.concerts.com/gom/subsea_staging_area.htm
The slide pack and other relevant videos at:
http://www.bp.com/sectiongenericarticle.do?categoryId=9033572&contentId=...
According to said article:
"Because the rougher surface left by that cut will not accommodate the tight seal needed for installation of the lower-marine riser package, engineers will use the "top hat" instead, he said.
That 5-foot-tall, 4-foot-diameter structure had been considered before, but engineers opted instead for an insertion tube that wound up capturing only about 20 percent of the oil from the site of the leak to the surface."
An earlier version of the CNN article at that URL specifically said this top hat has been resting on the bottom since May 12. Of course CNN could just be confused. I did get something very wrong: it's the insertion tube that was only getting 20% to the surface. Apparently this top hat wasn't used at all.
That's why they should have cut the bolts and freed up a nice flat surface of the top flange to seal to.
That would have left the top riser flange as a loose collar rattling around on the mangled drill pipe jutting out of the BOP flange. Capiche?
Based on comments here, that isn't feasable. Looking at the situation, it's the most obvious thing to do. I'm sure it's been considered. One problem I see with cutting the bolts will be that once you are down to the last couple, the flange may come apart with explosive force becuause the remaining bolts may not be strong enough. That would ruin any sealing surface. They have probably figured it's easier to use the outside of the flange as the sealing surface.
not the first time the Main Stream Media is not exactly correct.
pictures of the LMRP caps (formerly also called top hats) at:
http://www.bp.com/genericarticle.do?categoryId=9033571&contentId=7062542
n.b. these are #8 and #9, like Kent Wells said in his briefing, they're constantly making new versions.
The first/old/never used "Top Hat" is at:
http://www.bp.com/genericarticle.do?categoryId=9033571&contentId=7062043
It has cutouts around the base.
Looks like they've standardized on a top connector,
but the bottom parts are all different.
It does appear that they have an ROV working on the original top-hat this evening. That would seem to indicate that the CNN report is correct.
I guess I should have written "could be correct".
The feed showing the ROV screwing around with original top hat (cut-outs at the bottom) seems to have stopped.
Enterprise ROV1?
Nope: this is LMRP Cap #2, side number 4.
In this pic of the original top hat, note it only has 2 feed-ins on top:
Note that both the LMRP caps have more inlets.
LMRP Cap #2 has about 6, #1 has at least 3.
LMRP Cap #2 has smooth sides, while the original top hat has some square members on it's side.
LMRP Cap #2 is painted yellow on the side, orig top hat is all white, except for the "Flow ^"

Also see the BP video of the landing of the LMRP Cap #2 on May 31,
way after the original top hat:
http://bp.concerts.com/gom/subsea_staging_area.htm
I believe the feed I was looking at was from an Ocean Intervention ROV (the big one with the beefy manipulator arms).
However, since they now appear to be hooking up one of the LMRP caps with the Enterprise ROV, then that may be what they plan to use. Perhaps the original top hat is being readied as a backup.
There were two LMRP caps. One designed to seal against the stub of riser pipe left after the diamond saw (#5), the other to seal against the flange (#4, the one they are using).
Never mind. I think I was mistaken.
I hope you are right, CNN did report using the old Tophat, but I think you are right they just misreported, happens all too often. I guess our idea of sealing against the flanges IS lmrp no. 2 LOL, well at least a lot us THINK that could work maybe it will finally succeed and stemming some of this horrific flow.
A bit more worrisome is they claim to have been getting this from the good Admiral himself. We can only hope that CNN was the weak link in whisper down the lane...
A ROV appears to be readying one of the caps/tophats. Glimpses of it are visible periodically via Enterprise-ROV1
Enterprise ROV 2 is a more reliable link to same scene.
http://www.troutbugs.com/rovs.html
Prepping to hoist #4 it seems, guess that would be LMRP cap #2
Thanks - maybe that's a methanol hose a little while ago.
On Skandi ROV1, I figured out what the white "particles" were - they're dispersant droplets.
Occassionally the middle thin tube backs out of the plume and one can see it's the thing making the cloud of white stuff.
Viking Poseiden ROV1 is still following the shears down,
but the time and depth displays are frozen as of 1:46.
man, this is like a 6 ring circus...
Its a feel good solution. RIP Gulf of Mexico.
Only one problem - not gonna make you feel good.
First… they should finish the job they started. Cut off the rest of the riser. It looks like some ‘hack’ has been working the site. These are professionals? I think not.
I thought the LMRP was a top hat it is marked TH5-LMRP thought th5 meant top hat 5
edit
at least one cam from each ship is working....except the q4000
.
I put all the links from the BP ROV feeds into a simple table. You can open the link below in a separate window (right click the link) and just make it small.
These links open directly in Windows Media Player so you can adjust size etc.
http://www.troutbugs.com/rovs.html
Note: Skandi ROV 1 and ROV 2 has the same link. BP screwup I guess.
I put all the links from the BP ROV feeds into a simple table.
VERY neat, thank you so much!
At about 0130 EDT, it appears that power supplies to the shear are set, and the shear is tested. You can see it on the ROV cams from Viking Poseidon, and they are now lowering it - the are at about 1000' depth. I am not sure how long it takes them to get it set in place for the cutting, but it could be early morning excitement for you in the Eastern time zone.
I am putting this up for information, I don't take a position for or against.
It is a letter issued by NOIA (National Ocean Industries Association today.
I'm not sure about the nomenclature as they refer to platforms and it was my impression that only deepwater drilling rigs were shut down, not any platforms.
Its arguable that this was a low probability event exacerbated by possibly poor safety management by BP.
You can bet your retirement savings that any other drilling done in the foreseeable future (at least in the Gulf) will have much better attention paid to all the details. Even though BP and the other Big Oil companies can afford to make a mistake like this its not like they want to. Saving a few millions here and there when the penalty is multiple billions just won't cut it. The culture change will be share holder driven and won't require government intervention.
At this point government intervention is most likely just to put even more people out of work.
With as many teams of so-called ‘professionals’ dealing with capturing/sealing this blowout, I’d think they would always be one step ahead of the game. That is NOT the case here.
Millions of gallons of raw crude continue spilling into one of our most valuable resources and the clock is ticking. What actions have I witnessed to counter this flow? Nothing I would be proud of here.
I’m beginning to think this whole event was intentional, being International Terrorism.
Preventing the spread of oil miles out at sea?
Hundreds of ships with booms placed near point of source should have been used to divert the oil and tankers stationed at apex to capture.
But no, they had better ideas. Booms were used ineffectively for containment along shoreline.
Brainless or intentional?
And look at the nice ‘unfinished hack job’ in picture below. Good job… NOT
Straight up question:
Why not crimp riser and top kill / junk shot together in tandem, in coordinated fashion?
I have yet to read why they won’t try this.
Instead they proceed to shear off top of riser and attach a hat they won’t contain.
Cut too close to flange, nothing left to crimp later.
August is a long time out.
Feedback appreciated.
no crimping tool for the riser.
trying to crimp something that big/non-ductile will probably crack it (just like it cracked when crimped by bending before).
I think the junk shot has been abandoned because they are worried the pipe below the BOP will rupture under the pressure of the rising oil & gas if successful. Only by trying the Top Kill could they figure this out for sure but we don't have their pressure readings.
One big problem with this well - maybe even the cause of it all - is that the pipes through the rock way below the BOP are not oil/gas tight. (they should be) So can go POP if there's a pressure surge.
Same problem if you crimp it. Can't close high-pressure fragile pipes at the top, have to close at the bottom. (=relief well)
At the moment, the BOP provides an attachment point of sorts. If you completely blow out the pipes below the sea floor
surface then you have just a huge subseabed leak that comes up anywhere and you can't collect any at all.
Ben (not an oil professional, but long-time TOD reader)
International terrorists penetrated the ranks of BP (and learned English accents)??
2010-06-02 11:51:58 CDT The Skandi Neptune Subsea 7 ROV is spraying dispersant onto the vertical portion of the riser above the BOP.
Hi Blue -
I think one of the hardest things to accept about an event like this is that
1. It was entirely preventable,
2. How to prevent it was well known, easy to do and comparatively inexpensive,
3. The folks who bring you disasters like this always plead that they did not know what their subordinated were up to, and,
4. Gross incompetence looks like a premeditated and deliberate action, but is not. After the fact, you can just never believe anyone would be so stupid.
If the whole story that's unfolding had been made up for a TV movie, all would have turned it off well before the mid-point because it would be unbelieveable.
Pragmatic
Mishaps are entirely preventable in an idealized world devoid of human failings and physical limitations. It was predictable from the answer to Bob Shaw's (aka totoneila's) question: Are humans smarter than yeast?
Napoleon once said: "Never attribute to malice that which can be adequately explained by incompetence." When considering the "really stupid" v. the "really mean" standard for awarding punitive damages, I've tried to keep this statement in mind.
Last thought:
Cut the bolts now! Don't mangle the pipe!
Don't worry: none of this is real.
They are filming it all in a secret studio somewhere just like the moon landing.
Forty years from now, certified experts of the future will expose the TRUTH.
Sweet dreams.
June 3, 2010
02:10 CDT Enterprise ROV 2 is manipulating straps on a yellow and white cylindrical device marked "4" that is dangling above the mud mats.
Is is me or are these BP cam links shutting down without warning or not even able to start? I can often get several seconds of video and I look back to black screen and it wont always restart?
I'm having the same problems. Only Viking 1 and Boa Deep 1 are reliable right now.
Inserting 'riser pipe' into a tophat #4? unsure which this is
the LMRP Cap #2, with "4" painted on its yellow side,
will be hooked to the bottom of the Discoverer Enterprise's riser - actually to a pipe inside the riser.
Looks like right now they were having trouble getting it untied from the carrier box it came down on. The ROV kept dropping the webbing cutter.
Now looks like trying to latch onto a stub of pipe that will fit beneath the riser. Having trouble getting a locking pin to fit into a plate.
(hard to see with the video jumping around and stopping and repeating - having to reload the page
LMRP description video:
http://bp.concerts.com/gom/kentwellstechupdatelong053110.htm
The slides from that video:
http://www.bp.com/liveassets/bp_internet/globalbp/globalbp_uk_english/in...
Is the LMRP2 the one shown in the bottom three images on this page:
http://www.bp.com/genericarticle.do?categoryId=9033571&contentId=7062043
If so, can anyone explain what we are seeing there? There is an internal view which appears to show an internal 'lip' which could compress a gasket, though the lip is not fully circular. It is not at all obvious how this will clamp on to the BOP, bearing in mind (a) the top surface of the BOP is canted at an angle of 5-10 degrees, so that the LMRP cannot be held in place by its own weight - there will be a moment; (b) once the new riser attached to the LMRP fills with oil and gas, it will become buoyant - the gas lift effect.
I still think they need some monster clamps around the base of the LMRP. Wood27's drawing have the right idea in terms of numbers of clamps, but Wood27 has them spring loaded - I suggest instead something simpler, operating by leverage and gravity.
4:04 am CST update
Shear hanging out around 4800 feet. Viking Poseidon 1
On Enterprise #1:
Discoverer Enterprise has hooked up to LMRP cap #2 (side #4),
but the locking plate was giving them trouble - the locking pin just would NOT go in.
The ROV dropped the locking pin, and after looking around for a bit, went up to its cage and looked in the side tool boxes. Found a piece of thin tubing about 6-8' long, stuck it in a hole in the box and bent it 90 degrees, and appears set to try to use that as the lock pin that keeps the LMRP cap on the pipe extending down from the riser.
They just lifted the LMRP cap off the sea-floor, then stabbed the tubing into the lock hole from underneath (there's a cross fitting on the cap's just above the lock plate - could have used a design with less interference).
Finally got this tube wrapped around the lock plate,
I guess next step is to hookup the methanol lines.
There are two input fittings, and 4 valves with T handles on top, I guess to vent things as needed.
Tired of the erratic video - g'nite.
how many skilled ROV operators are there available for this job?
what sort of shifts will they be pulling?
The claw is moving into position for cutting the riser LIVE
http://www.bp.com/liveassets/bp_internet/globalbp/globalbp_uk_english/in...
as you can see oil is billowing out from the 1/2 cut made earlier when the saw became stuck and vision is becoming a problem for the operators
Wouldn't it make more sense to use an explosive ring cutter and get a clean cut on the riser? The shear may cut and crimp the riser, but the stub will not be usable for any attachment that can contain and transport oil. With a clean cut, a Plidco sleave could be bolted on by the ROV and any attachment (flange?) could be used.
I'm just doing the PBP
They are very close at landing the sheers on the target the current walked it off and now they are re-centering.....
I hope Tony Hayward is paying this ROV Op a big bonus if he lands this. Seeing him fighting the flow is amazing. Respect!
Ex-- Could not agree more. Sorry to live chat here but I have not yet mastered the chat page -- I have missed the last 12 hours and so I am not sure what I am seeing -- is this the actual sheering of the riser or is he still positioning? TIA.
I have been following this since the first feed link I posted. I think what happened is they made an initial cut with the claw sheers (tons of oil plume came out) The screen actually blacked out off and on for several minutes. The cam backed away and semi-circled the top of the BOP at which point the Claw was moved into a different position and I believe is making another cut and/or dragging?? the remnants of the broken riser off the BOP.... all speculation at this point.
That, or make a jig with a centering Vee plate and clamp so the cutter would be located by the flange below the cut. A cutter that didn't cross the pipe could cut just the outside, working similar to a Mathey-Dearman 1SA pipe cutter/beveler (though built much stronger.
watching this happen now, I'm having a really bad feeling about their chances of getting the LMRP cap on against this flow.
Despite the incredible skill of the operator, the ROV is flying blind, with a total blackout of oil across the lens except for the occasional glimpse of the BOP
I do wonder if maybe the kink was holding back the pressure much more than we all thought . . .
Ben
Since the oil is a real PITA for the operators, I have some dumb questions:
Can't they just start another Top Kill session, this time using only water? Is the water not heavvy enough to work the same way? Or are there reasons not to pump water into the well? (But the drilling mud contains also water...)
I know a lot of people have been taking sh*t for second-guessing what BP/contractors are doing, but why the heck did they bring the shear in on the side where the saw perforated the riser? It seems pretty obvious to me that would cause problems with visibility. I really have no idea how they can tell what is going on in that cloud. It looked to me like that ended up placing one side of the shear on the flange instead of the riser.
Now it looks like they damaged the choke or kill connection (stab?) below the flange.
They had huge amounts of problems just moving it into a workable location, the rov robot arms had to keep moving cables and other obstructions around so the claw wouldn't get hung-up, plus they were in low visability with the oil plumes shifting and blowing out. Just landing it as they did was pretty darn impressive.
Now shifting to the viking Poseidon feed
http://www.bp.com/liveassets/bp_internet/globalbp/globalbp_uk_english/in...
I bet there are some people who wish they had tried the wire saw again. It doesn't look like they were able to separate the riser on the first? try. The shear is still clamped on just below the kink, so maybe they will get a second chance.
They are using this side for the shear for the same reason they used this side for the wire saw: The other side is blocked by the bent riser...
and that leaves one more quadrant - the side directly opposite the kink. Just where the shear is now positioned, but not where they started.
Thanks for being the place to get answers. As a long time member of TOD I've read much that was over my head. But as the blowout problem developed and I became more and more hooked on watching the disaster in progress, some practical questions came to mind. I've worked in heavy construction, as an Ironworker, and some things I've seen in the last couple of days don't make much sense.
When cutting the bent riser pipe below the bend, why did they start the cut from the under side, the side underneath the bend? AS the cut proceeded, it was bound to get more pressure from the weight of bent section bearing on the diamond wire. (Like cutting a tree limb from the underside.)
I presume the "yellow can" is the top hat. Why isn't this fitting an open cylinder with a closable valve at the top? It could be installed in the open position, letting the venting oil escape while installation is in progress, then closed once the fitting was in place.
Thanks for all your great work here.
BM
The quotation in the upper right hand corner of this page:
“Data always beats theories. 'Look at data three times and then come to a conclusion,' versus 'coming to a conclusion and searching for some data.' The former will win every time.”
—Matthew Simmons, ASPO-USA conference, Boston, MA, October 26, 2006
Not, I repeat NOT, in an election year.
It's always an election year, whether or not there's actually an election.
New York's got your problem solved:
http://www.nypost.com/p/news/national/leak_solution_Zw3RdLcmYcdsA4UAz6WM...
<Sarc>
if y'all weren't just a bunch of inbred redneck illiterate hicks, you would bow and scrape before her and sing her praises!
</SARC>
NB - I see that the HTML tags aren't working properly above. Maybe you could have Noo Jork come and fix that for y'all as well?
}:-]
OMG.
She just re-invented the packer.
Again speculation...
I think what everyone is watching now is the Claw lined up making a nice level clean-cut after the riser debris was cleared away. It's been hard following this event with all the oil cloud blowouts shifting this way and that. But for a few moments it appeared the BOP was cleared of the broken riser.....can anyone else verify this?
Sure doesn't look like it separated to me... Take a look at Viking Poseidon - ROV1 feed.
http://www.bp.com/liveassets/bp_internet/globalbp/globalbp_uk_english/in...
Nope, it's still there.
http://mfile.akamai.com/97892/live/reflector:46566.asx?bkup=54013
And if you want to see something scary, check out the wall of gas and oil you can see from Skandi ROV1.
http://www.bp.com/liveassets/bp_internet/globalbp/globalbp_uk_english/in...
I know much of this is coming out under high pressure causing the plume to spread, but this looks way worse than what we were seeing from the riser break two weeks ago.
Lot of dispersant in that plume.
I think the battleship just got displaced from the cover of that bad ideas book.
poseidon ROV 1 - getting shear in place
whoever posted the link to all the rovs --- thanks!!
http://mxl.fi/bpfeeds/
Excellent link, many thanks. Direct link for screens 1280px and smaller, http://mxl.fi/bpfeeds2/
did the claw just lose power? Ocean I ROV2 just found a mangled power (?) line - outer cover stripped off
Yeah, looked like Ocean I ROV2 suddenly started to search around for the reason why the claw didn't close when it should have done, and found a damaged line on the right hand side. If that's correct then it's going to be back up to the surface for repairs (assuming the claw can be opened enough to disengage) before anything significant now happens.
Meanwhile, Poseidon ROV1 giving great views of the flange at the top of the BOP, which makes it clear that there are plenty of obstructions to the underside of that flange.
It appears that the riser is cut and away from the top of the stack.
BP said you can watch all 12 ROV cams now, there site is here
http://www.bp.com/genericarticle.do?categoryId=9033572&contentId=7062605
riser is separated now
Are the following assumptions useful?
(1) the likelihood of getting clean cuts or a clean removal of fittings would seem to be small given the stresses on the fittings caused by the damage and the novelty of this situation, so any effort should plan for dealing with worse case removal, that is the top of the BOP being deformed and connected to jagged, twisted metal, meaning that none of the surfaces of the BOP or existing fittings are regularly shaped, precise, clean, or even to the point where they can serve to form part of a mechanical seal given the pressures involved.
(2) the force of the leaking oil combined with the likelihood of accidentally damaging fittings and/or changing stresses on fittings means that there is a likelihood of increased spill rates, new spill locations, and decreasing structural integrity.
(3) removal of the riser will likely result in increased flows that will increase the difficulty of operating the ROVs and other equipment due to turbulence and reduced visibility.
(4) any attachment to the top of the BOP should be made so that an attachment/seal can be made before any pressure is put on connections; once a new connection fitting is attached to the BOP, the next step is dealing with the pressure of the oil and gas, otherwise the connection will need to deal simultaneously with a connection to an irregular surface and pressue, which are difficult to address in combination.
(5) the situation will deteriorate such that solutions must anticipate worse conditions than currently exist. Therefore, solutions should anticipate continued deterioration of the fittings at the top of the BOP and the BOP itself.
Is BP engineering solutions behind the situational curve? Are the engineers using fabrication techniques that are appropriate for normal underwater operations but not well-suited to this situation? Are they trying to use only mechanical connections when instead they should be using a combination of glue (cement) and mechanical connections?
I think many of us want to opine about all of this because we feel powerless and frustrated in the face of a great tragedy and it is very difficult to just sit by and do nothing. No doubt some want everybody who isn't an expert to just shut up. Perhaps thoughts from nonexperts are a waste of time, but perhaps theoildrum is a place where nonexperts can learn how to engage more effectively and constructively in processes that have dramatic impacts on their lives.
While I understand that BP and the industry have very talented and smart experts, sometimes smart people make horrible mistakes. Also, sometimes those who are very good at dealing with normal challenges using normal responses are bad at dealing with abnormal situations that require innovative response. Not everybody is equally adaptive and creative. Some managers, experts and engineers have limited abilities to adapt to the abnormal. In thinking about BP's responses so far, as an institution it seems to be stuck in conventional thinking. Industry personnel might have much better ideas for how to respond, but this doesn't mean that the individuals at BP who are making response decisions are adopting them. I expect BP's command structure is full of conventional thinkers. Large corporations tend to drive away the unconventional.
This is not on the theme of the shear or the ROV operations.
I've read most of the threads on the blowout and do not recall anything on the cleanup microbes that are available. there is a pretty interesting video of the effectiveness of them on "normal" oil spills and wonder if they have been employed here. It could be pretty interesting if they could be added to the initial plume. I do not know if they are effective at the pressure and temperature environment but possibly they would travel with the small oil bubbles. The experiment and results are darned impressive. Maybe someone here has some real experience with these special bugs.
Oil Eating Microbes
http://www.youtube.com/watch?v=8VfypUzx1tI&feature=youtube_gdata
When I studied oil spill response in Alaska I was told that microbes are routinely used to clean oiled shorelines. But in this case the use of dispersants and natural causes will keep a big part of the oil in deep cold waters. As with any processes in living nature, they slow down when it gets cold. So the microbes would not be very efficient in deep water. I also believe that you would have to have different species in deep water and surface.
On the shoreline however using microbes might prove useful depending on the site. Luckily GOM is a warm area where the oil degrades much faster than e.g. Alaska.
Also adding other nutrients enhances microbial activity and may speed up the oil eating process.
Did anyone catch this? I just snapped an image from the Viking ROV1 feed that seems (to me at least) to show two pipes inside the riser.
Sure looked that way to me. Similar diameter, but possibly different wall thicknesses. Almost impossible to work out why. The ROV was certainly taking a lot of trouble to get a clear look at the severed end.
Cue the conspiracy theorists.
Edit:
On reflection, maybe. If the diamond saw had severed the DP, and the BOP shears had also severed the DP, the flow might have pushed the now free length of DP up into the region the shears were cutting. That would mean two pieces of DP in the cut. Would not explain why they appeared to have different wall thicknesses. Doesn't match the theory that the BOP shears stalled on a DP join.
The pipes are too mangled to tell if the walls have the same thickness. The one to the right of the image is crimped as you might expect. But, the left pipe is not, as if something "solid" in the pipe resisted the force of the shears to crimp it. You can also see that the riser is much more "squeezed" on the right side. I don;t subscribe to conspiracy theories. There is an explanation for everything, no?
Edit:
The riser was bent and the only other cut to the riser was several feet downstream. I can't see how the remaining length of DP could have "moved" towards the BOP top if the diamond saw had severed the DP before stalling. The "second pipe" (if what I see is a second pipe) must have fallen in while the riser was still straight.
Please post that image
gdtrfb just did. Mine is very similar.
To me also.
Seems that if there are two parallel pieces of pipe inside the riser, then the BOP could not work properly. All the info describing how a BOP works assumes that there is only one pipe inside the BOP and the rams close around this pipe (or shear this pipe). If there are two parallel pipes, the rams can't make a seal. And the shear ram could possibly get jammed.
Hmmm.... More questions, more questions....
Jim
In an article in the FT times this morning at http://tinyurl.com/2afrnnk the CEO of BP is quoted as follows:
Speaking in Houston at BP’s leak control base, Mr Hayward argued that the industry could cut the risk of serious accidents in deep-water drilling to “one in a billion or one in a trillion”, but it might mean changing the way the drilling industry works.
One in a Billion? One in a Trillion? I don't think so.
Listen up . . . I used to do this stuff for a living. There is NO FRICKING WAY they could drive the probabilities this low . . . the hazards from natural phenomena would overwhelm that.
Let's do a bit of a back of the envelope calculation - In a table was recently published by the EIA, they listed 463 production wells and 193 exploratory wells as being drilled between 2004 and 2008 in the GOM. So we have 463 + 193 = 656 wells drilled over the last 4 years, or 164 wells per year. We have had 1 major blowout (Deepwater Horizon) since the last major blowout (Ixtoc in 1979), so the industry experience is 1 blowout per 31 years, or approximately 1 in 31 * 164 wells, or 1 in 5084. Now Tony thinks we can drive this to 1 in a billion or 1 in a trillion?
Consider the hazards from meteorite impacts. From http://en.wikipedia.org/wiki/Impact_event
Small objects frequently collide with the Earth. There is an inverse relationship between the size of the object and the frequency that such objects hit the earth. Asteroids with a 1 km (0.62 mi) diameter strike the Earth every 500,000 years on average.[2] Large collisions – with 5 km (3 mi) objects – happen approximately once every ten million years. The last known impact of an object of 10 km (6 mi) or more in diameter was at the Cretaceous-Tertiary extinction event 65 million years ago.
Asteroids with diameters of 5 to 10 m (16 to 33 ft) enter the Earth's atmosphere approximately once per year, with as much energy as Little Boy, the atomic bomb dropped on Hiroshima, approximately 15 kilotonnes of TNT. These ordinarily explode in the upper atmosphere, and most or all of the solids are vaporized.[3] Objects with diameters over 50 m (164 ft) strike the Earth approximately once every thousand years, producing explosions comparable to the one known to have detonated above Tunguska in 1908.[4] At least one known asteroid with a diameter of over 1 km (0.62 mi), (29075) 1950 DA, has a possibility of colliding with Earth in March 2880, with a Torino Scale rating of two.
The hazard from natural phenomena of meteorite impacts would be greater than 1 in a billion . . . no way to get it down to 1 in a billion or trillion.
There are other hazards from natural events as well, including massive hurricanes, tsunamis, earthquakes, planes crashing into the rigs, and so on.
Probably an acceptable goal would be to drive down the frequency of a blowout of all drilling activity in the GOM to on the order of 1 in 1000 years which would mean that for drilling 164 wells a year, we would need to drive the frequency of an individual well from the current 1 in 5000 to 1 in 200,000. In other words, they need to be about 40 times safer. I think that is doable.
There is a well developed methodology methodology to evaluate risks associated with a complex engineered technological entity such as offshore drilling, nuclear power plants, or airliners -- probabilistic risk assessment. It isn't easy or cheap, but it will tell you how you can most cost-effectively lower your risk.
See http://en.wikipedia.org/wiki/Probabilistic_Safety_Assessment
Ultimately, however, the question of 'how safe is safe enough?' is a political question, and is very difficult to grapple with.
JRW: "Ultimately, however, the question of 'how safe is safe enough?' is a political question, and is very difficult to grapple with." Nicely understated. Thank you.
There are two aspects to this accident - the blowout and the response - and the response can be further subdivided into subsea/wellhead response (how to deal with the leak), and the surface response, or what to do with the oil after it leaks.
It seems to me that the first aspect is the easiest to deal with - use of best existing practice for well design and implementation, improvements in the BOP design, and drill rig safety. Plenty of information and technology available now.
Subsea response - woefully inadequate - a serious effort needs to be mounted to design better tools and improve procedures for dealing with problems.
Spill response - same as above.
Its also a little hard to design out the 'stupid' factor where humans are involved.