Making holes and cracks around oil and gas wells
Posted by Heading Out on November 22, 2009 - 4:42pm
This is a continuation of the tech talks, discussing technical topics, that I write on Sundays. For the past few weeks I have been writing about some of the techniques used in producing the gas from shales, and that will likely continue for another week or two. Because of the need to condense the topic into a relatively short post I would ask those familiar with the topics to understand that I have had to shorten the description and gloss over some details in order to keep the main theme clear. But further comments to help readers understand the techniques better (or questions when it isn't) are appreciated.
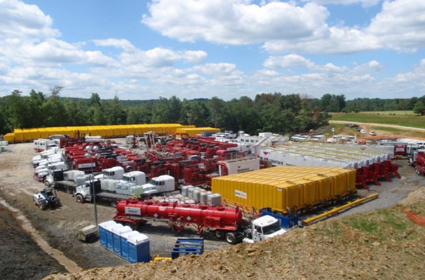
There is a simple test that I use in one of my introductory classes, where I give the students a rectangle of paper and ask them to pull it apart, then I give them a rectangle with a cut half way through it perpendicular to the length, and half-way down, and ask them to pull that apart. It tears apart much more easily, and it is how I start a lecture on the role of cracks in causing materials to fail. You apply that principle about every time you pull open a package with a serrated top. The deeper cuts focus the force you are pulling with over a small area, making it easier to part the package and extract the candy, nuts or whatever without having to pull so hard that, when the package tears, you throw the contents around the neighborhood.
Today I want to talk a little more about perforating the wall of a well, and a bit more about hydrofracing. They are not necessarily used together, but both are ways of getting cracks out from the immediate wall of the wellbore so that the valuable fluid on the other side can have an easier path into the well.
To begin with the topic of perforating a well, I have written about this earlier, but more from the point of the tools used to do the job. What I’d like to do here is to talk a little more about it from the rock point of view. As I mentioned last time the rock right around the well can be subject to a high enough pressure that it will partially fail, or crush, and this can lower the amount of fluid that can get through, or alternately it might have been damaged in some other way. By bringing in a tool with a set of shaped charges in it, and then firing these at the appropriate place this problem can be overcome.
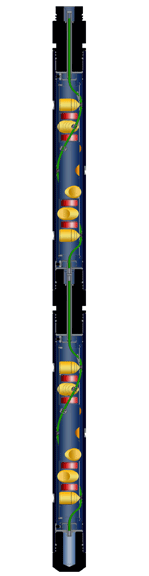
The charges aren’t all necessarily fired at one time or place, even though, for the illustration below, they appear to be.
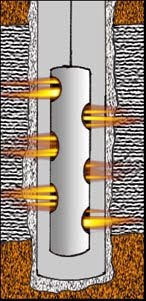
The jet of metal that shoots out of the cone will travel into the rock roughly 10 cone diameters, as a rough rule of thumb, and this carries a channel, or tunnel, out through the damaged rock into the surrounding reservoir. The collapse and creation of the channel happens very fast:
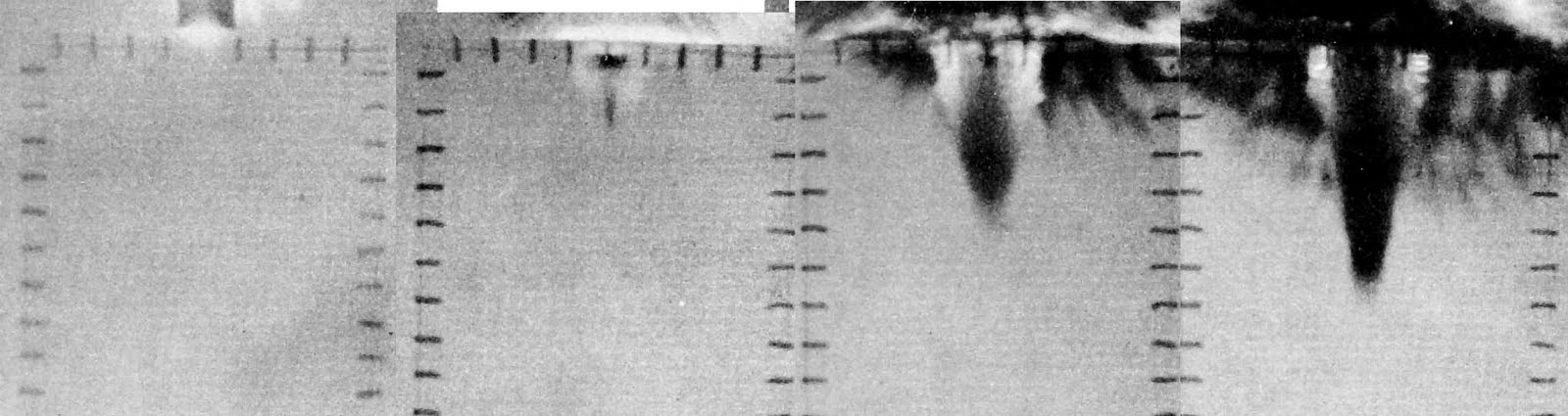
The channel is initially hollow, and drives a set of small and large cracks out into the rock around the line of the charge.
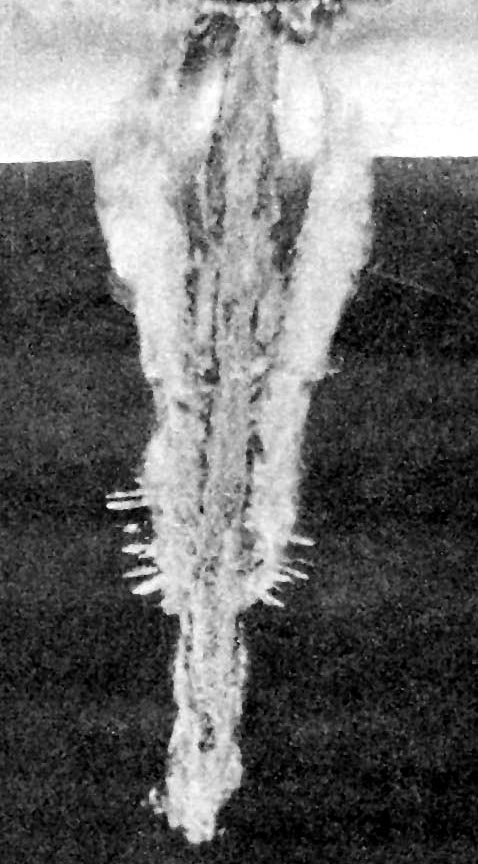
However, while it is easier to show the damage that the jet does by showing how it penetrates Plexiglas, this is not rock, but it does show some of the events that occur. When, for example, (vide the discussion on jointed shale last week) the jet shoots into rock where there are clear joint planes defined, then these act to stop the crack growth (perhaps in the way that those who used to remember stopping cracks growing in old cars by drilling a hole at the end of the crack. It distributes the stress that was causing the crack to grow when focused on the tip, over a larger area so that it drops below the critical level). Or the stress is high enough to cause cracks to form and be reflected back at the jet.
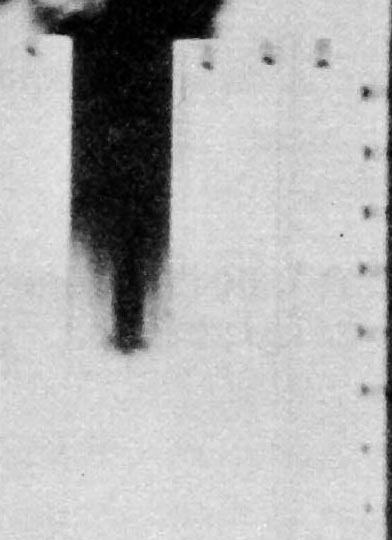
If the charge is not carefully designed and used, therefore, it might not be as effective as initially hoped, and this becomes even more true if the pieces of metal that are formed when the cone collapses are carried into the channel and partially block it. There are different strategies, depending on the well and the surrounding rock and it is one of those things in life where, if you got it right the results are almost immediately obvious – as is the converse.
Creating cracks that go out into the surrounding rock has become a vital part of the economic production of gas from the shales around the country, as we have discussed, and having a starting crack in the right direction, whether it is a natural joint in the rock, or a crack that has been deliberately created helps control where the crack starts and how it grows.
In the above picture you can see that when the hole was pressurized, a crack grew, and ink flowed into the crack, as it formed, but, when the pressure came off, the crack closed and most of the ink was forced back out of the crack. (We created the pressure by firing an air rifle pellet into the hole).
So if we are going to have a useful crack we need to have it open after we take the pressure back off – after all we need to get the fluid back out of the well, so that the gas can pass up the well for collection.
Now it is not quite as easy to grow the crack, or prop it open as I may have suggested earlier, and to explain some of the issues in a little more detail I am going to use an example and some details from the Modern Shale Gas Primer.
When you decide to frac the well, and each well is different, as is just about every location, so there is a significant amount of preparation and knowledge required to work out the procedure required at that particular point. Bear in mind that the crack that you are going to have to grow needs to stay in the shale layer, and not go out beyond it into the surrounding rock. One of the reasons for this is, apart from giving the gas a path to the well, if it goes outside the reservoir rock then the gas can escape, or, alternately, other fluids can gain access to the well. This is particularly true of the Barnett where the rock immediately below it, the Ellenberger limestones, can hold a lot of water that can muck up the gas recovery if it gets into the fractures. (Given this degree of control and the large distance below the ground to the reservoir rock, this is why a lot of the fears that the frac job will damage the ground water tend to be dramatically overstated).
In the example cited, which is from the Marcellus shale, the treatment of the frac takes a total of 18 steps, and because some of these are fairly similar I am going to go through them in groups. First the hole is treated with an acid, to clean away any remaining debris and mud from the drilling operation and to clean any fractures around the hole, so that they can be used to help the frac grow. After the acid the hole is filled with an initial polymeric fluid, largely water, but containing the “Banana Water” that I referred to in an earlier post. This is a friction reducing agent and will help carry the particles used to hold the crack open into the crack in the first place. The problem with that polymer is that some of the choices available, while good at reducing the friction to help move the particles, aren’t that good at holding the particles in suspension, and the last thing we need is for them to settle out in the bottom of the well, and so in the subsequent steps in the process as the particles (or proppants) are added, there is usually a second polymer in the mix to hold them in suspension.
Once the hole is full of the slickwater (the official term for the first polymer solution) the initial frac is made with a fine sand suspended in the fluid. To keep the crack open all along its length we need sand along the path and the crack gets narrower as it grows deeper. So for the first several stages of the crack growth the fluid is filled with successively greater concentrations of the fine sand, so that, in this way, it can penetrate to the deepest part of the fracture.
In the example cited there are some seven of these sub-stages with the fluid being pumped into the well at some 3,000 gpm but varying the fluid:proppant density to carry more and more of the particles into the fracture. Once these stages have been completed, then the job is finished by pumping an additional eight sub-stages of fluid, with this second set containing a larger size of proppant particles. In this way the area closest to the mouth of the fracture will be held wider apart to make it easier for the gas to escape. As with the first set of sub-stages, the concentration of proppant in the fluid increases as the stages progress. In total, in the example given, some 450,000 lb of proppant was used to make the fracture, together with some 578,000 gallons of water.
Once the fracture is created, then the well is flushed to clean out the different fluids, and make it easier for the gas to get out out of the rock and into the well. (It also removes any loose and ineffective proppant so that it doesn’t later become a nuisance). If you think that this would need a lot of equipment you are right!
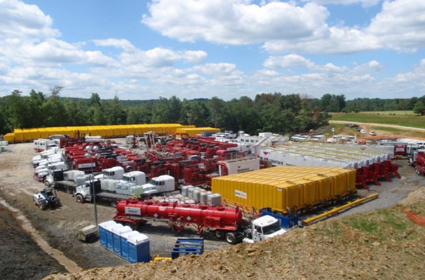
Since there is some discussion of the effects of the different constituents of the fracing fluid on local waters I thought I would end with the listing of common chemicals used in that liquid, which is provided in the Primer.
As usual this has had to be a very brief review of the technology and may have oversimplified to the point of not being clear, so all technical comments and questions are appreciated.
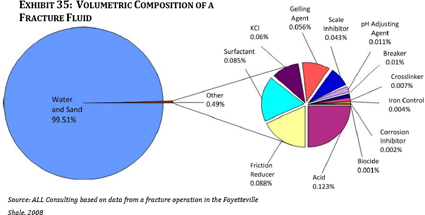
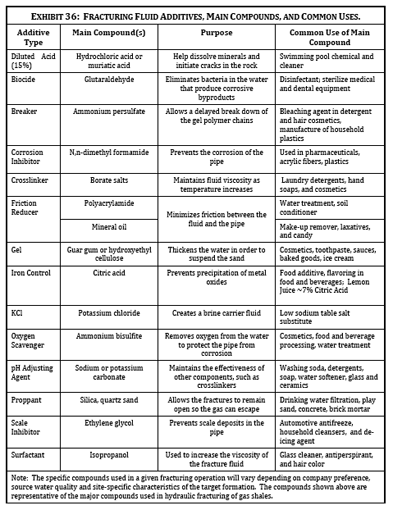
* The initial photos in this post were taken as part of the dissertation of Dr Konya, "The use of Shaped Explosive Charges to Investigate Permeability, Penetration and Fracture Formation in Coal, Dolomite and Plexiglas" Missouri S&T, 1972.
Thanks very much, Heading Out, for the series of articles. They are very timely, and very useful.
All gas shale reservoir have different reservoir characteristics, WRT sedimentology, fracture patterns, TOC's, origin of the shales, etc. I recommend downloading the Shale Gas Primer to everybody who is remotely interested.
I have been called in to reorganise a shale gas project in the Horn River Basin which has totally lost all direction. The Engineer in charge wants to frac the shales at ~9,000 feet by running a nitrogen foam frac ... using local sands from aeolian dunes, mapped in the 1970's by yours truly for GSC.
I have consulted with some of my outside engineering contacts, who state that SOP in the Horn River Basin is running a slick water frac with sand propants.
What is SOP for fracing in the Barnett?
What is SOP in the Fayetteville?
When do you run a nitrogen foam frac? I'm told on low pressure reservoirs, like the Edmonton Fm., and at Jonah in the Green River Basin tight gas sands in Wyoming, where the pressure was low "because of depletion".
We also have a 12% CO2 content. Does anybody use CO2 foams? I've beaten that idea away for now.
This project would be a laugh, except incompetance and cognative dissonance aren't funny.
I am now being headhunted to repeat the process on an international shale gas project in a lacustrine basin.
Regards,
Harry Flashman, P.Geol, not P.Eng.
I get the impression that the amount of fracking has greatly been scaled up in recent years. Do you have any thoughts on how one might quantify this? Are there industry figures on gallons on fracture fluid, by year?
If there really are problems with fracking, would they have shown up in the last 30 years, in your view?
Gail -- rather difficult to quantify the improvements even for an operator analyzing their own results when hey have all the data at hand. Frac designs have changed significantly even over the last few years. A major change has been the lengths of the laterals and the number of fracs per lateral. Just a few years 2 or 3 fracs were common. Now it's not unusual to see 10 or more per lateral. To make it more difficult the geology can change significant over short distance so even when two wells are fracs identically the results could vary greatly. Also, as time goes by, we learn what areas have greater potential then others and a shift in focus makes comparisons more difficult. And if those aspects didn't make it difficult to quantify the results the actual pumping process is not always reproducible: human error and equipment malfunctions.
I've sat in more than one meeting and observed very "spirited" debates among engineers in the same company looking at the same data and arguing details of a proposed frac job. A lot of science behind the process for sure but, like many things we do, there' s still a lot of art involved.
Dear Mr. Heading Out. I love these posts. Abide some questions from the ignorant...please. 1. Is there a possibility of a subsurface explosion setting off a fire at depth of the charges??? Will the gas in its form at depth ignite or burn???
2. Is there some video or pictures of the downhole result??? like when discovery channel has picts in the womb of a fetus???
3. With regard to the propants.... do they really work??? or is there function largly assumed to work because we can't see them working???
4. Can Gas be drivin like oil.... from one area to the well for recovery as it were????
Regards TG80 sends
TG80:
Generally when the charges are set off the conditions in the well will protect against the ignition of any of the hydrocarbons around the charge. To ignite methane, for example, the amount of methane in the air has to be within a finite range, too much or too little and it doesn't happen.
That is not to say that there can't be fires in hydrocarbon deposits underground, though they are mainly in coal and coal mines such as, sadly, the disaster this week in China.
While I have seen the occasional picture taken from within an underground well I don't think that they are that common, and since the penetrating charge is going through the casing into the rock, the picture might not show a lot (though more if the hole was still open, i.e. had not been lined).
Yes proppants really work (at least the vast majority of the time) though there are some conditions to their use that I might get into in a later post. There has been a lot of lab work where tests were carried out at the same pressures as deep in these wells to validate that the results can be, to a degree, predicted, and then there are the actual practice in the fields where the production of natural gas/oil that would not have been obtained at that level without the proppants is an indication of the success of the tool.
TG -- No chance of explosions or fire...not enough oxygen down there to support such events. We actually do have a secondary oil recovery technique (in situ combustions aka "fire flood") that does burn oil in the reservoir but we have to pump oxygen down there to make it happen.
As far as imaging the frac results we do have a system similar to a seismograph survey. We actually can "hear" the rock cracking and place those sounds in 3 dimensions. It's a rather expensive effort and a tad complicated. But I've seen amazing results. One operator had fraced a zone and modeled that the frac propagated out in a certain direction. In reality the frac didn't even go into the target zone. It went into a completely different (and non-productive) formation. Imagine trying to analyze the results of fracing Reservoir A when you didn't know you had actually fraced reservoir B. It's a great system but expensive and often difficult to justify to management the need for it.
Propants: No Propants...no frac jobs. Cracking the rock open doesn't do much good if you can't keep the fracs open.
#4: Not exactly sure what you're asking but in general NG moves much more easily then oil through a rock or a fracture. A surface tension factor.
Just a hat tip to HO for taking time to provide this informative series. Lots of others must follow the series without commenting. Please be assured it is appreciated.
Bob
+1
Indeed. Doesn't take much time for me to pop in with a short answer now and then. But HO obviously spends a good bit of time and thought on the effort. A significant and much appreciated contribution.
My thanks also to HO and ROCKMAN for the 'from the trenches' perspective. It's wonderful to read about the art and science of petroleum and gas engineering and serves to remind us how much human creativity it takes to get these fluids out of the ground.
Kudos!
-- Jon
A question for Headingout or Rockman:
We generally hear about horizontal multistage fracs on very tight shales. In your opinion are there other tight reservoirs where the economics of these techniques should be better than shales?
There are a number of "tight" reservoirs, but it very much depends on the individual situation as to what will work best. As ROCKMAN says it is sometimes very hard to predict what is actually going to happen, but confidence grows with experience, and the techniques evolve as we see what works and what does not. The shale deposits have been known for some time, but the evolution of ways of getting the gas out have taken time to develop to the point that it can be recovered economically. Hard for me to think of other reservoirs with that potential at the moment.
As HO points out there are other low porosity reservoirs with oil/NG in them. The problem is universal: if you can't recover the hydrocarbons at a sufficient rate you can't develop such a reservoir regardless of how much production you might eventually produce. Fracing is not as uncommon in conventional reservoirs as perhaps many think. Just last month we drilled a well with specific plans to frac it. It was a conventional sandstone reservoir but the layers were rathe thin and discontinuous. In this situation the frac was designed to reach out to layers which didn't directly connect to our well. Additionally we can damage the rocks close to the well bore with the drilling fluids. So much damage that the oil/NG can't pass through that area to the well. Then we'll do a "clean up frac". Generally a single frac much smaller (say 5%) then the types of fracs they are doing in the shale gas reservoirs.
Much has been said in the press lately about huge amounts of shale gas in the US that has become available with very recent technological breakthroughs. However, it is not clear to me what part of this technology is so revolutionary.
Is it only "creating cracks that go out into the surrounding rock"?
Grin:
You need to read some more of the comments from the folks who are out in the field trying to make these ideas work. The latest parts to develop (that are widely discussed) are the changes in the polymer mixes to help get the proppant deeper into the fractures, and thus hold the cracks open further into the rock, and then the use of multiple fracturing techniques along the well, as ROCKMAN noted above.
Thanks for your replies HO and Rockman.
I should have been more specific in my question. I am interested to know if the economics of horizontal multistage fracs are would be more economic in tighter conventional reservoirs(conventional reservoirs that historically need to be frac'd to produce economic quantities of gas or oil) than in shale deposits. There seems to be a movement by smaller companies to using these techniques in tighter channel sands and smaller tight deposits. Do you believe the economics will hold up on plays that are not huge blanket sands?
Virgo -- Your questions are actually connected. Low porosity conventional reservoirs have been frac'd for decades. The economic value is spread across the board. Even in the same trend and over short distances the results can vary greatly. The value of a multistage hz frac program is the ability of one horizontal well bore to act like a series of vertical wells. Picture a 5000' lateral with fracs every 1000'. the result would be similar to 5 vert wells spaced 1000' apart. Much cheaper to drill one hz than 5 vert wells especially in deeper reservoirs.
As far as blanket sands vs. limited areal extent the fact that you need to frac tells you there is a limited drainage capability. Thus even if the reservoir covers several thousand acres if a vert/hz frac only drains 100 acres the results would be the same as a 100 acre reservoir. The one thing about having thousands of acres of a suitable reservoir is that it becomes a "cookie cutter" operations (yes...that is the technical term we use). After you establish the value of fracing you just punch one hole after the other until you've completely patterned the reservoir.
Thanks Rockman - I guess what I am trying to figure out what is are economies of scale (ie. cookie cutter economics) more important to the value proposition of a play than reservoir quality. Asked another way, would applying multistage technology to a reservoir that has better drainage characteristic than shale yield better economic results than shale (on the surface it seems like it should). The caveat being that these wells may require scale (cookie cutter) to make them interesting. There are many small companies, that cannot compete for land and cannot commit the required drilling capital to the big shale plays, who are applying multistage fracs to more conventional types of reservoirs because they are close to infrastructure and they do not need as much land and capital. I am wondering if anyone has experience with this techologies in different play types and how the results compare? Could I compare results between vertical fractured shale wells and other vertical fractured other plays and then extrapolate the results to horizontal multistage wells in both shale and other play types?
Virgo – First, the cookie cutter aspect value isn’t so much scale economy as it is just the sheer number of prospects generated with little additional effort. Generating viable drilling projects is expensive and, more importantly, very time consuming. This the prime reason so many public companies jumped so hard into the SG plays. For Chesapeake to generate the drilling budget they’ve expended over the last few years would have taken many times the number of prospect generators they employ and perhaps as long as 5 to 10 years to produce the same reservoir increases. A Y-O-Y reserve increase is the key metric the stock market uses to value such companies. Thus time is a very big enemy for these companies.
As far as comparing economic gain from frac’ing shales vs. more conventional reservoirs there such a wide range of possibilities it’s difficult to offer a meaningful answer, There is a wide range of outcomes not just between different SG plays but even within the same play. Same is true for conventional plays. As far as small companies competing in the SG plays you’re exactly right. And not so much as the size of the capex resources but different goals. It may sound simplistic but the smaller independents (some of which are rather large) key on profit generation. Thus they’ll avoid paying those crazy high lease costs and ever escalating drilling costs seen in the SG plays. It’s not that the public companies don’t care about profit but it takes years for the profitability of their efforts to reveal themselves. But every year they publish their proved reserve increases. And that’s the number Wall Street hangs on. I once drilled 4 horizontal wells in a conventional gas reservoir offshore that added no profits to the company books (the same NG would have been produced from the existing wells but at a much slower rate. But these new wells increased the total company production rate by 400%. As a result the stock price went from $0.50 to $3.00 per share. Not bad: stock price increased seven fold and they weren’t going to a penny more profit.
As far as extrapolating vert and hz fracs in one type of a play to different plays one can make some very, very general comparisons. I’ve seen much effort expended trying to compare frac models between two wells not only in the same play but only 1200’ apart. So many variables. You might notice that most of the discussions around the different plays and frac technologies tend to talk in terms of the “big picture”. For good reason: it’s get so complicated and subjective when you start looking at individual wells you get lost in the details before the conversation even begins.
Thanks Rockman thats great info
Heading Out - great as always.
A comment and three questions:
In exhibit 36, it lists "isopropanol" as a "surfactant" to "increase the viscosity of the fracture fluid".
Isopropyl alcohol is not much less viscous than water, and .085% is not much added,
but it does (due to having both hydrophobic and hydrophilic parts to the molecule) have much greater "wetting" capability (i.e. lowers the surface tension), which is what surfactants are about - causing a change (usually lowering) in surface tension of liquids, a for example detergents.
Question 1: How much of that 450,000 lb (225 tons, 204 tonnes) of sand stays in the cracks you make?
If I guess (from some of what you and ROCKMAN have mentioned) for example this is say a 2 mile hole, 8 inches in diameter, and then calculate that sand is silica at 2.634 g/cc and granular sand is half that density, and get the volume of the hole, I get that filling that 2 mile x 8" volume takes 133 tonnes of sand. If none of the 225 tons of sand comes back out, you've put nearly two hole's worth of sand into the rock!. (I find this astounding). Even if my hole volume guess is off by 2x or 4x, that's a huge amount of sand that gets stuck into the rock!
The water is 21x my surmised hole volume, but I gather there are several flushes with the acid and such. How much of that water is pushed into the rock when actually frac-ing?
Question 2: How far do the cracks go away from the bore?
Question 3: do you have to run a pressure pipe or will the casing handle the pressure?
(I'm kinda thinking you run a pipe, as part of sealing off separate parts of the well with packers to do multiple fracs).
Speaking of packers, I'd be interested in knowing more about them and how they're placed and removed.
sunny -- you always get a little sand recovery when you flow back but generally an inconsequential amount. The bigger problem is when you "screen out": no matter how much horsepower you apply you can't get the entire frac volume pumped into the rock.
Frac distance: always an educated guess. A big frac might go out a few hundred feet. Often a more critical question is frac height. But often it's very difficult to tell where the frac went. They have the prefrac model but I've seen that be very far from reality after the frac. And in many cases you can't confirm the goal you were attempting
Casing strength -- all casing have a pressure rating. If you need to pump at a very high pressure then you run the more expensive tubulars. But despite planning you can split casing at times.
Packers -- A great vaiety out there. Try googling oil field packers and you'll see a bunch of commercial sites with vaying degrees of info.