Casing a Well
Posted by Heading Out on August 30, 2009 - 11:05am
Click here or on the "Tech Talk" tab at the top of the opening screen to view prior talks in this series. Recently, these have been running every Sunday.
There has been some concern (that among other things has led to the actions in the House to bring hydrofracing fluid under the Safe Drinking Water Act) about the use of different fluids in oil and gas wells and the risk that they can get into and contaminate surface ground waters that may be used as drinking water. So I thought that I would write a little about well casing today.
Not that well casing is the only thing in the local environment that has to be protected or designed for. Because the odds are that where you want to drill does not sit right next to a highway. That means that you are going to have to install some sort of a road to get to where you want to put the drill. That may sound fairly straightforward in somewhere like Texas, (though it got some folks upset in Wyoming), but it becomes a lot more complicated if your oil patch is in the middle of the North Slope of Alaska, or the Empty Quarter in Saudi Arabia.
In the North Slope, for example, they make the roads out to the sites out of ice. Because the ice must carry the weight of the units that haul the rig into place, the road has to be of a certain thickness, and it has to be at a certain level of coldness to give it strength, (which means winter which is also dark). This means that they can only move rigs at certain times of the year and that restricts the rate at which they can develop new fields and wells. As a result the season is only about four months long, I believe (though have not been up there at that time of year to check).
Having got to the site then it has to be prepared, among other things we need to have a way of getting the cuttings that come out of the hole separated from the drilling mud, and then having a place to put both them, and to store the mud until it can be drawn back into the pumps and circulated back into the hole. And we need to create an initial hole, or cellar, where we can start the drilling pipe into the ground. I will cover all the different things that go into the surface layout in another post, let’s for now concentrate on that hole, that is going to head down for up to several miles in order to get to the oil or gas.
This initial part of the well has to be fairly large, for reasons explained below. Let us begin the well with a fairly large sized drill bit, say 9-7/8 inches in diameter. So we thread this into the drill collar, lower it to the rock surface and start to rotate the string. As the bit advances we can monitor the rock that it drilling through by looking at the cuttings that come out of the hole. We have some idea of what rocks are down there from the surveys that convinced us to drill here in the first place, but it helps to have this confirmed. Plus we need to know if there are any unpleasant surprises down at the sharp end. As the hole gets deeper the time for these cuttings to reach the surface, and be cleaned and examined, the lag for return, gets longer, and so it gets a bit trickier to know what is happening at the bottom of the well.
This can lead to short-term problems. Bear in mind that the hole is being drilled as an open hole. In other words, once the drill goes beyond the conductor pipe, it is drilling in rock, with only the rock walls on either side of the well holding it open. This can be a problem in drilling through weak or jointed rock, since bits can fall into the hole behind the bit, and if enough of those fall they can jam the bit in place (since they fall on the bit above the cutting surfaces).
As the bit goes deeper we add additional lengths of drilling pipe to form the drill string, and the bit penetrates through rocks that are of different types and some of these will have fluid in them. Water, whether fresh, which might be the supply for a local community, or salt, is quite common. The hole cannot be left open any longer, because the water flowing from the surrounding rock into the well will dilute the mud, so that it no longer works as it was supposed to, plus, we might start losing some of the drilling fluid into the surrounding rock. Plus different layers of non-drinkable water can work back up the well into the drinking water aquifer.
To stop this from happening we have to stop drilling and seal off the rock on the sides of the well from the well itself. This is known as casing the well, and running casing will hopefully (but not always) be only needed once before we get to the bottom of the well.
So we pull all the drill string out of the hole, remove the drill and lower steel pipe into the well to encase the well, from the bottom of the conductor pipe down to where the bit has found (and hopefully drilled through) the rock that is giving us the problem. (Hence the name casing). Having this continuous length of casing in the hole will likely stop, say water, from getting in and diluting the drilling mud, but if this was all that we did, then it would still leave a problem, since the steel pipe does not completely fit up against the rock wall created by the drilling bit. In other words there will be a gap between the casing and the rock wall, that will allow fluids to travel up or down. This gap has to be filled, and the filler is normally a special form of cement.
The way that the cement is placed is simple in principle, but a fair bit more difficult to do properly and effectively. Think of the long thin tube of casing, filled with a cement that acts something like toothpaste. This cement has to be pushed down the tube so that it squeezes out of the bottom and then flows back up between the casing and the rock wall, filling all the gaps as it is pushed back up to the top or surface. (Hence the name surface casing). Particularly when this casing is run, it is important that the gap is fully filled. This is because this is the casing that seals the well from local groundwater, used for domestic and industrial supply. Since the cement will move more easily thorough a larger passage, than a very narrow one, this gap has to be above a certain minimum size. Small centralizers will be attached at points down the steel casing to keep it in the middle of the hole, rather than pressing up against one of the walls (since this might leave an open channel up through the cement). There are also “scratchers” which are put on the casing so that when it is rotated in place it will scratch the walls of the borehole and remove any mud cake that might have formed, so as to give a better bond between the cement and the rock wall.
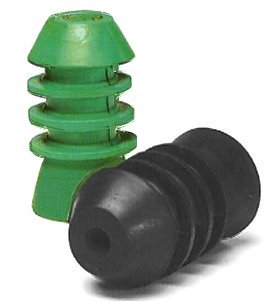
A small plastic plug (the bottom plug) is put into the casing ahead of the cement. This separates it from the mud that is already in the hole. It is fitted with wipers, that clean mud from the walls of the casing, and it is pushed down to the bottom of the casing by the cement that is pumped into the well behind it. There are some pictures of some of the tools and descriptions of the process here, here and here.
Once the bottom plug gets to the end of the casing, there are ports it passes that allow the cement to flow out of the casing and back up the outside. Once the cement has been pumped into the casing a second, top plug, also fitted with wipers, is put into the casing and this is then pushed down by the conventional drilling mud. As it is pumped down it forces the plug down, and the cement out and back up to the surface. Because of possible variations in hole size and other possible problems, perhaps about 50% more cement might be pumped into the well than the calculations might suggest. When the top plug hits the bottom plug, then there is a pressure spike at the pumping station, telling the operator that it is finished. The rig then waits on cement (WOC) until the cement is hardened. The drill pipe can then be put back in the hole and drilling can restart.
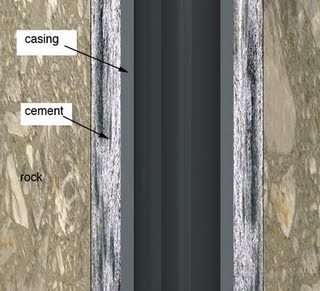
But whoops, the bit won't fit in the hole any longer! For the sake of discussion lets say we ran half-inch thick casing. And that we had an inch of cement behind it all around the casing. Then the hole we have available to get the drill through down to the bottom is now only 6-7/8th inches in diameter. So we now might use a 6-5/8th inch diameter bit to continue drilling (since we don't want it rubbing against the casing wall).
If we run into another layer of problem rock as we drill down to the bottom of the hole, then we are going to have to run another set of casing. This is known as intermediate casing, and the process is the same, and it leaves us with an even smaller hole through which to get a drill bit through.
So that, when you get toward the bottom of the well you may end up drilling with a bit that is only 3-3/4 inches in diameter. These drill with a smaller thrust than the larger bits, and so, although you may have a very powerful drilling platform, with thousands of horsepower available, you may end up, as you approach the pay zone where the oil is, using only a fraction of that power.
We'll discuss what happens when you hit oil next time, but perhaps by now you might begin to understand why, in drilling a well that might cost $1.25 million, the actual drilling part alone may be no more than a third of the cost.
As usual I welcome comments, questions or criticism. But to catch the obvious one - yes, after running casing, the first thing you have to drill through are the two plugs and the remaining cement in the bottom of the well, before you can reach and start drilling through the rock again.
Many thanks for this great series HO. Your descriptions are very systematic and clearly stated and make the various processes very understandable. Understanding these operations gives the reader a much better grasp of what is involved in oil exploration and production. A fine addition to TOD topics.
Heck HO...what are you trying to do...put the group into a comma? Just teasing. I appreciate your post and hope the rest of the folks absorb what they can. I've followed some of the legitimate concerns along with the absurd hysteria. You and I both know that accidents can happen when frac'ing but it's rare and even more rare when it damages potable water reservoirs. Folks, especially those in New England, should be far mor concerned with other industries which have regularly contaminbated water zones with injected waste. I don't recall the exact number but I read a story years ago about the thousands of abnadone disposal wells in New Jersey where there isn't evena record of what was pumped down hole.
As far as regs go all thos northern states need do is copy the regs in Texas. In addition to potentially wasting 100's of thousands of dollars on the process the reg fines and civil liabilites are more then sufficiaent to make operators do their but. But accidents still happen. But accidents don't stop us from driving cars or flying. Much of the hype I've seen is obviously politically motivated. It's evryne's responsibility to seperate fact from spin.
I for one was not "put into a comma." Sounds painful! ;)
Was reading OilFinder's latest missive over at peakoil.com: The Monterey Shale: A Bakken from Sunny California! Found it pretty amusing that ARCO only found the shale could be not only source rock but also a producer when they developed a leak in their casing at South Ellwood - later in that thread I posted a Search and Discovery page about the Monterey and a field in the San Joaquin that was also discovered "accidentally." You guys include anything in budget outlay for serendipity?
Sorry Dude. I was rushing out to see the terra cotta warriors from China and didn't bother with spellcheck.
Good accidents do happen. About 15 years ago they perf'ed an abandoned NG well in a shallow sand to make a water disposal well. The sand looked water wet but an unusual mineral (glauconite) in the reservoir hid the presence of the oil. When they tested the well it flowed oil instead of water. It had been penetrated by a number of other wells but they never caught on. The field ultimately produced 7 million BO. Not bad for a screw up, eh?
25 years ago, when I lived in NJ, one of the other problems with toxic waste was that the NYC mob-controlled disposal companies had been simply burying drums of stuff in the Jersey countryside at night. One of the fears when buying a house in a new development was that they would subsequently discover your house was built on top of such a site. Some of the sites had been discovered when the drums rusted through and stuff started leaking into the surface water.
Thanks HO
Credit Suisse has a report out last month discussing this issue and the proposed new frac regulations. Here is the first page:
Hi Nate,
Looking forward to reading your Campfire post this week on Natural and Human / Social capital.
I wanted to quickly address some of the standard industry positions in this Credit Suisse report.
First, under the 2005 act, frac'ing was specifically exempted from the existing Safe Drinking Water act, at the behest of Cheney and co. So the new legislation is closing a loophole rather than adding new regulation.
Second, I'm continually amazed how effective the "your gas bill might go up a dollar" argument is in stopping regulations, whereas the "your house might blow up, or you might have to pay for imported water forever, or the value of your property may plummet" is never mentioned.
Third, the greater threat to production is obviously price instability rather than added regulatory cost. The wild swings in NG prices over the last two years are far more damaging than regulatory costs. As Matt Simmons says, "too bad we destroyed the industry."
Fourth, requiring conclusive evidence before protecting the public good is rather backwards. The fact that there is no conclusive evidence that frac'ing doesn't lead to groundwater contamination, such as numerous cases in Colorado and New Mexico, should be the test case.
Fifth, we don't measure the downside, downstream costs of no effective federal regulation. In the Marcellus this includes potential contamination of reservoirs containing drinking water for New York City. This is not hype but rather legitimate concern.
Sixth, the casing is the typical argument for how drinking water is protected. As another poster has pointed out, there's the issue of disposal of extracted frac'ing fluids. In Pennsylvania, these are typically stored in open pits and ponds on site for some time. This doesn't also address fluids left in the hole, potential other pathways opened by frac'ing itself or the water inputs needed: 2-6M gal. per well.
Good Morning:
You write as though there is no regulation in place. In reality, as the testimony that was given on the Hill relative to the bill showed, this is already comprehensively addressed by State legislation, and state regulators enforce it. One of them pointed out to the Committee that after hearing of the rumors of contamination he made a point of contacting each State's water folk to get the details and found that the cases that were being used as examples did not exist.
All the fluids are typically drained from a well at the start of production, and state regulation mandates that they be properly disposed of - typically with a fluid balance being checked to ensure that all the fluids have been accounted for. (Not my words but from the testimony.)
Hi HO,
Thanks for the post and for the technical detail and for your experience in the field, for which I am grateful. I've read your posts before and found this experience most helpful.
I speak mostly from my research into the Marcellus NG play. I was taking my Permaculture certificate course in Hancock and Deposit, NY where the play was very much in evidence last spring.
The State DEC had made a point of promoting the play with the idea that existing environmental rules, which predate the technology, would be sufficient. The Governor, however, required the DEC to go back and revisit the rules. At the time there were a grand total of 19 DEC enforcement agents to oversee the hundreds of wells that were planned, now dormant due to the price crash.
So while there were rules in place they were clearly not specific to the technology, the regulatory body was insufficiently funded and was even actively promoting the idea that no new rules were needed. Fox guarding chickens.
Perhaps instead of contacting the State water people (again asking the Foxes- "no I haven't heard about any Chicken problems...") a little more digging would show many examples of methane in water in Colorado and New Mexico (although I believe these are shallow oil and coal methane plays), and disposal problems in Pennsylvania.
An EPA whistleblower in Colorado brought to light that many concerns within the EPA itself (more Foxes) were actively supressed when the EPA released its much-touted report saying there was no evidence of contamination threat with frac'ing.
And if existing regulations were sufficient why would the industry need special exemption from SWDA? The idea that frac'ing fluids should be protected and undisclosable as "trade secrets" is laughable.
It seems amazing to me that we could insert thousands of feet of pipe down a hole that is itself thousands of feet long. I can only imagine all the ways it might get stuck. Especially if you are trying to put in into or through a layer of unsatble rock that might breakup and obstruct the hole. I suspect these problems are why it took so many decades and billions of dollars to get as far as we have.
It is interesting that you have to plan how many casing stages you will need at the beginning of the process. Hit an unexpectedly nasty layer, and I can imagine you might have to abandon the hole, because it is then impossible to do just one more satge of smaller diameter pipe. I guess thats why the people making the decisions, based upon educated guesses get paid the big bucks.
How often is a $1,000,000+ invested in a dry well? And if dry wells are more common than producers then several million dollars may be invested per producing well. If each producing well requires the price of a large wind turbine then which is the better investment?
As for hydrofracing fluids causing pollution then we should first look at these fluids at ground level such as in handling spills and the handling of mud coming back to the top.
I don't know offhand the current success rate for oil wells in general - and it tends to vary quite a bit with the field, - even Aramco drills the occasional dry well, but there was a report for the Barnett shale in Texas that said, for gas wells, that it was costing about $5 million a well, and that 28% of them proved profitable . And that profit can be significant, even though it does not necessarily extend much beyond two years.
That's cheap!!
Offshore starts at around $50 million and runs up from there depending on TD, formation, and where you are in relation to the rest of the world.
The duster ratio is harder to gauge. Wildcatting the ratio is likely close to 10 to 1 but you need to take time into account. Locations we drilled and plugged 20 years ago are now moving toward production.
Hi HO, thanks for doing this tech talk series.
I have a couple of questions about casing. I have heard that some casing is recovered from the well and recycled. I assume that the surface casing cannot be recovered because it is protecting the groundwater from contamination. But what about the intermediate casing? Is that also cemented into place against the rock wall? And if so, how do they break it free? Or does none of the exterior casing get recovered, and it is only production tubing or such interior pipe that is being referred to as recycled?
I ask for two reasons, 1. there is a lot of energy embodied in the casing pipe and 2. it is a bit of a puzzle to me how you would break exterior concrete free along the length of a pipe. You can't get at it with drills, or hammers, or acid. I figure that if it is done, it must be clever.
I also have a question about multiple stage fracture jobs. How do they keep the high pressure fluids from traveling to the prior fracture locations and just lifting those openings again, rather than forcing new openings? As I understand it (and could be in error) they perforate the casing pipe at each location starting at the end of the lateral. Then they put in a plug to block off the already fractured end of the well. But after your discussion on casing, I wonder if they must also seal the outside of the casing? So the high pressure fluids don't just run down the edge of the casing to find the weakest point along the whole well length and open a channel there? Is it concrete the whole casing length?
Thanks!
You've already stated the big problem with recovering casing. You might be confusing that casing recovery with the recovery of the risers, which are the pipes that carry the oil/gas from the seabed up to the surface. Those are recovered, but the casing is generally plugged and cut off at some depth below the sea bed. However if you drill deviated wells out from a common well you might be able to recover some of the internal casing - but in the cases I've heard of they cut that off with the outer casing and leave it.
I'll get around to how wells are conventionally completed, then horizontal wells etc in future posts.
Thanks! Looking forward to the next installments.
One problem with hydrofrac is that methane leaks into aquifers such as home wells or under houses. A build up of methane, not burners being on, is what causes gas explosions in houses.
Here's a story where a water well exploded when the submersible pump was switched on.
Now you can't drill a water well there.
So then those people must live on bottled water?
"Last year we permitted 8,000 wells, and this may be the only incident that occurred," said the DEP's Lobins. "You can't cover every possible scenario that you could encounter out there, so when the regulations are crafted it addresses the ones that will be most protective of 99.9 percent of the wells."
At the bottom of the hill on Carter Road, Richard Seymour runs a certified natural farm that ships produce across the state. His well is running red and turbid and bubbles with so much gas that he fears he'll lose that agricultural certification. If there's a technology, like cementing, that can protect his water, then shouldn't it be required in every case, he asks?
We feel pretty alone on this, pretty frustrated," Seymour said. "I assumed the DEP, EPA, the state -- the government -- would protect our land. We didn't know that as a landowner the burden was on us."
http://www.post-gazette.com/pg/09116/965379-109.stm
Also, in some places the legal casing requirements are very low or don't exist.
Casing is expensive and will the government have the resources to check where there is a legal requirement?
I read somewhere that casings and metal pipe leaks increase exponentially over time.
http://www.onepetro.org/mslib/servlet/onepetropreview?id=00017930&soc=SPE
I wonder if there is a difference between old technology and new. For example, is it possible that there are some very old wells, whose casing is rusting through? This could cause a problem, if it were true and there were fracking in the area. If newer pipe is made so it is much more rust resistant one wouldn't expect the same kinds of problem. I thought I heard something like this--but wasn't sure I really had it straight.
True Gail. All casing, even the high quality stainless, will rust through eventually. That's why the regs now require cement to be pumped inside the casing in the fresh water interval when abandoning a well to avoid this potential problem. Only a very foolish operator would frac too close to any existing well bore...abandoned or not. But there are still a few incompetents around.
maj -- the potential problem is real but seldom caused by frac'ing. In the early days the regs on cementing casing inplace were laxed and it wasn't unheard that methane would leak upwards between the casing and the original open hole as the well was produced. The main reason for cementing is to prevent this sort of cross flow. Thirty years ago we drilled a well in an area where there had not been any shallow NG to worry about. So they just hauled ass through the section and the well blew out and killed two hands. During the decades the deeper reservoirs produced methane and it had slowly leaked up the annulus (space between hole and casing where the cement usually prevents this). Since the bad old days regs have tightened considerably (at least in the Guld Coast).
The company rep reported that out of 8000 NEW Marcellus gas wells in Pennsylvania only ONE water well had blown up.
Sounds good except then I read that leaks increase exponentionally over time.
Rust creeps! And how many operators are using SS casings?!
I'm somewhat reassured(for what it's worth)that some/most of the gas industry are careful, professional and diligent in sealing gas wells but unless there's a government cop with some resources to at least throw some regs around I have to wonder.
Maybe it's just the whole wildcatting atmosphere and this poor guy who found out nobody (no EPA, no PA, etc.) was looking out for him but I think we need a system in place to develop this properly( call it Big Gummit Socialist Fascism if you must--'That which we call a rose, By any other word would smell as sweet;')
What companies usually do is they buy people(or local gummit) off to try to get away with whatever they can.
What I'd like to see is a complete plan of how to develop this resource.
We're all so relieved that the O&G biz found 600 Tcf of unconventional gas(allegedly) we're just about willing to let them do anything they want.
maj -- Between my experience with Fed regulators and those from the state of Texas I think the folks up there shouldn't expect much help from the feds. A strong state agency like we have here can do the job. It wasn't always so in Texas but it's watching over the interests of the citizens quite well these days IMO. But if the folks in New England just sit on the hands and wait for the industry to do a proper job without goods regs inplace they will be very sorry eventually IMO.
ROCKMAN,
I'm interested in gas well casings in part because I strongly support CO2 sequestration of large fossil fuel sources like power stations and refineries. The Gulf Coast area has lots of big CO2 sources and lots of depleted oil and gas fields. If cap and trade or better a carbon tax gets passed I can see a business opportunity even without EOR,EGR. I've heard that prices for sequestration at the site are ~$15 per ton not including the pipelines. Of course the amount of CO2 from an average coal power station(500MW) would be huge--10,000 tons per day by way of a 16" pipeline. It doesn't seem very profitable but the work would probably be very steady, regardless of the markets.
The concern as always is will the CO2 leak out. People are also frightened of the Lake Nyos event when 1700 people were asphyxiated. These type of lakes are very rare and the problem seems to be an accumulation of CO2 rather than a steady leak.
http://en.wikipedia.org/wiki/Lake_Nyos
http://en.wikipedia.org/wiki/Limnic_eruption
DOE says they can get a seal that will last for centuries. By law I think the injection well has to be 2000 feet down in approved reserviors. The pressure of supercritical CO2 is ~1500 psi while gas wells often operate well above +2000 psi.
I tend to believe DOE but I have no direct knowledge of the practical geology. I haven't heard of any leaks with CO2-EOR which I understand produces 5% of US domestic oil production.
I wonder if the O&G people would be interested in this.
http://fossil.energy.gov/programs/reserves/npr/CO2_EOR_Fact_Sheet.pdf
maj -- CO2 is one of the most corrosive elements dealt with in the oil patch. Even the best coated casing can fall. But the leakage of any gas from a reservoir to the surface is very rare (excluding a well blow out of course). But there have been many cases where injected gas have leaked into other reservoirs. About 15 years ago over 7 million gallons of propane leaked out of a salt cavern and I'm not sure they ever figured out where it went. But it didn't make it to the surface. But other then leaking up the annulus of some well there's almost no chance of any gas making its way back to the surface.
The ideal injection reservoir is a pressure depleted NG reservoir. Pressuring the CO2 is THE expensive part of the project. The lower the pressure of the targeted reservoir the less horsepower is needed. An even better source is a pressure depleted oil reservoir since the CO2 might increase ult reecovery.
A nice primer.
Re: water contamination:
The Oil and Gas Conservation Act in Alberta (http://www.ercb.ca/docs/requirements/actsregs/ogc_reg_151_71_ogcr.pdf) has some regulations about distance from other structures or sources and waste disposal but I can't seem to find anything about prior testing of water wells, although I would expect a smart lease operator to do so as part of due diligence.
Alberta law explicitly requires prior testing of water wells within 600 metres before drilling for coal-bed methane (http://www.elc.ab.ca/pages/Publications/PreviousIssue.aspx?id=309). This provides a baseline if any contamination is claimed.
Some stripper wells would have been abandoned because of low production but it is cheaper to run them than to spend the money shutting them in.
Nifty YouTube Vid: YouTube - Ground drilling Animation. Lots of interesting related clips there. Was watching one of a downhole camera - the geologic equivalent of invasive endoscopy.
Your comment about the need to build roads and the difficulty of building them reminded me of something else I have run into--"fly-in" sites. I was told that some of the in situ SAGD sites in Alberta are fly in. I understand that some of the early Ecuador Amazon sites (back in the 70s) were fly in sites. I am sure there are others.
It seems to me to have a fly in site you would need to transport by helicopter:
-A drilling rig.
-All of the casing for pipes, drilling mud, and equipment to monitor what is happening.
-Generator to power the various electrical equipment.
-Diesel fuel for the drilling rig and the electrical generator.
-All of the workers.
-A place for the workers to stay. (Tents?)
-Food and water for the workers.
All of this would be non-trivial to do. I know in Alberta, the pairs of wells I saw went 1,000 feet deep, then turned and went over 3000 feet horizontally. The second well in the pair had to be precisely aligned under the first well in the pair, to work properly. The particular location I looked at had something like 30 well pairs--with additional "phases", there would be more.
Without a lot of fairly powerful helicopters, it is difficult to see how this could be done.
That's where the Mi 26 comes in. We had one in Yellowknife the year the ice-road failed. A fuel tanker won't fit in a C-130 but it will fit in the Mi 26. Nothing else will carry haul-truck tires. And economical, too, at 3000 lph.
There is at least on on the Alberta drilling inventory at Airborne Energy Solutions
Heading Out -
Nicely done piece .... as usual.
Perhaps this question has already been covered in one of your previous tutorials, but I don't seem to recall it.
When one is drilling a really deep well, say something on the order of 10,000 ft., the drill string becomes physically just that: a very long, flexible string of metal with a length/diameter ratio akin to that of a long thin wire. As such, it probably has the torsional rigidity of an over-cooked piece of spaghetti.
Now, even though there is a layer of drilling fluid between the drill string and the casing, I would imagine that, due to its great length and flexibility, the outside diameter of the drill string must at many points come in direct contact with the inner diameter of the casing as it rotates and probably wobbles. When that happens, the friction must increase greatly. I am trying to picture an almost two-mile long length of pipe with metal-to-metal contact and many points and wondering why the drill drive mechanism at the surface doesn't just wind the pipe up like a big long torsional spring and cause it to eventually either jam or snap.
As an analogy, if you lay a long enough rope out along flat ground, you will eventually get to a length where there is so much frictional resistance just from the rope's own weight that you will not be able to drag the entire rope because the force needed to pull it exceeds the breaking strength of the rope. So here's the question: Is there such a point in drilling, and if so, how far away from it are some of these ultra-deep drilling efforts? In other words, is there some natural limit on depth whereby the frictional resistance becomes greater than the torsional strength of any practical drill string configuration?
I am going to do a separate post on drilling pipe and issues such as this in a short while (topics seem to be piling up) however the short answer is stabilizers . (I just picked one site that had a picture of one that you could see). These keep the pipe in the middle of the hole as you go down, and reduce your problem. There are other things that make life more difficult - the weight of the pipe itself for example - that I will also write about.
joule -- As OH says he'll provide details later. In the meantime a 10,000' well isn't considered deep in these parts. Last year I drilled out of a string of casing that was over 28,000' deep. One of the huge tech advances in the last decade has been the development of down hole drill motors. The drill pipe doesn't turn at all. Instead the mud is pumped down the drill string and runs through a turbin that the mud flow causes to spin. This then turns the drill bit. Thus no torque and friction on the drill pipe. It's simply lowered straight into the hole. That well eventually drilled below 34,000'...the second deepest hole in the western hemisphere.
But we still "part" drill strings from time to time. It can even happen in wells just a few thousand feet deep if you're not paying attention.
ROCKMAN -
Thanks for the explanation. I guess that down-hole drill motors solve the problem I envisioned.
Still, the act of drilling a five or six mile deep well boggles my mind. That drill string must get mighty heavy even with it being buoyed up by the dense drilling mud.
joule -- this may sound counterintuitive but typically extra heavy drill pipe (called collars) are placed at the bottom of the drilling assmble so more weight can be applied to the drill bit. Deep wells can often have mud weights exceeding 16 pounds per gallon. A normal pressured section requires around 9.5 pounds per gallon. Even when the drill string weighs more then 500,000 pounds in can stll "float" in such heavy muds. But torque (the earth "grabing" the drill string)is the real enemy. It can ruinb your day in a heart beat. Imagine twisting off (breaking the drill string) and loosing a hole you just spent $100 million to drill.
Right now there is an oil and gas leak off the West Australian coast.
http://www.news.com.au/perthnow/story/0,27574,26002483-2761,00.html
The drill hole at West Atlas rig blew out at about the 2,500 metre level I believe. There is talk that another rig will try to intersect the hole to divert the flow. Let's hope there will be no cyclones while this happens. Meanwhile the press shows pictures of baby whales that may or may not be at risk.
There was also a steam leak in a deep well in granite for a geothermal experiment in South Australia. The steam contains radon and should not be vented. When the granite eventually cools that casing will be abandoned, yet another thing that detracts from claims that this technology is sustainable.
Radon 222 has a half life of 3.82days. Unless the well is very close to a populated area, I don't think it should be considered a problem. The main radon problem is potentially increased levels in housing, as radon is continuously created by radioactive decay of uranium in the ground, and it can concentrate in areas such as basements. If you can simply delay the rate of diffusion of the radon to a few times 3.8days, it will decay before it can get to you. So I find that to be a surprising statement.
The company seems to be arguing that some radon release in testing is acceptable since coal ash releases more
http://www.geodynamics.com.au/IRM/Company/ShowPage.aspx?CPID=1271
However another geothermal company Petratherm is drilling an even 'hotter' granite within sight of a uranium in situ leaching project.
I guess it would be undesirable for a worker to directly inhale a puff of radon. I think the likely problems with granite geothermal are not to do with radioactivity but low steam temperatures, granite cooling, unpredictable fracking, remoteness from the grid and so on. Australia's redoubtable Minister for Energy claims it will be the power source of the future that will avoid the need for nuclear fission.
Nice summary HO.
The need for large diameter holes is self explanatory in your piece but often over looked by people.
When I was in south Texas in the early 2000's doing ag work lots of the water wells were 8 inch casings from the 1950's but leaking. They were being recased with 6 inch but that limited water flow significantly. We had a new water well drilled (in addition to our operating 8 inch well), to 465 feet if memory serves, and the top was a 12 inch bore before casing. The goal was to have a big enough hole so that if it needed to be recased in 50 years you would still have high flow, between 500-1000 gpm to irrigate.
The new well operated at 1000 gallons per minute, tested to 1400+ gpm, but you need a big hole to deliver that much volume.
And for people that question the numbers; one acre inch = 27,000 gallons of water. This means that to mimic a rain event of one inch on just one acre of land requires 27,000 gallons of water. When tying to irrigate a few hundred acres in a day with 1/2 inch you need A LOT of water. For that 1000 gpm well you could water approximately 1 acre of land every half hour with 1/2 inch of water, or 48 acres per day (running 24 hours) with 1/2 inch.
This puts the power of nature in perspective, since we don't even blink at a rainfall event of 1 inch over hundreds of square miles. Try to do that with irrigation and you understand why many people on this site are concerned about a future with scarce energy. That doesn't even get into the fear that the water will not be there to pump. Lesson learned for me. I now live where water falls from the sky to grow things rather than needing to be pumped from the ground.
They are bringing in a second rig to intersect the West Atlas blowout
http://www.news.com.au/perthnow/story/0,27574,26007825-2761,00.html
I presume the second hole has to get close to the defective casing on the first well. It would then draw oil and gas from a pocket so there would not be enough pressure to break the surface. Does that sound right?
That's about it Boof...more or less. But they don't have to be set too close to the other well. In fact, beyond saftey concerns, you need to be at a 1000' feet or more away to be able to turn the drill pipe from vertical to horizonal. When the new well bore gets close they use magnetic logging tools to detect the casing/drill pipe in the wild well. In can take days to drill the last 100' since you're trying to hit a target that's only inches wide. A relief well will typically pumped heavy mud or cement into the blowing wells to seal it off. I'd don't ever recall seeing a relief well produce...except by accident of course. A relief well can blow out if you're not careful