Passive Solar Design Overview: Part 3 – Thermal Storage Mass
Posted by nate hagens on January 26, 2009 - 9:23am

In Part 1 of this series, we looked at the three main architectural styles of passive solar design (Direct Gain, Indirect Gain, and Isolated Gain), as well as the first of the five design aspects, Aperture. In Part 2, we covered heat transfer, building heat gain and loss, and Absorbers. This article will present an over of the next design aspect, Thermal Mass, which is one of the main factors in avoiding passive solar overheating in the daytime and excessive cooling at night. Mornings are typically the coldest times for some passive solar homes, and this article aims to provide help to those who want to design their next home or renovate their existing one to provide moderation in heating, cooling, or both.
OverviewIf the sun shone steadily upon our home or office 24 hours per day, we could simply size the equatorial-facing windows to collect just the right amount of sun for winter heating and be done. However, as the effective sunlight available in winter can be short-lived, in order to keep a reasonably stable temperature before the sun comes back up again, the passive building design must account for storage of warm thermal energy in the form of mass storage. The location, materials, shape, and size are the important aspects of mass storage (though shape is an advanced topic beyond the scope of this overview, as are detailed calculations of heat re-release via radiation and convection). Thermal storage techniques can vary widely between regions that tend to be closer to the tropics vs. regions that are closer to the poles. It should be pointed out that virtually all buildings have incidental mass storage in the form of furniture, wallboard, wood or masonry flooring, and so forth. This is usually not anywhere near the amount of storage needed, though with a superinsulation design approach it can supply an appreciable amount.
As noted in Part 1, passive solar techniques can be combined with active solar techniques; for example, a thermal mass floor heated directly by the sun could also be integrated (during the design/construction phase) with a radiant floor system heated on cloudy days by stored hot water from an active solar heating system.
Location of Thermal MassTo review the 3 main styles of passive solar design, there is Direct Gain (sunlight enters through windows into the living space), Indirect Gain, and Isolated Gain.


Figure 7 - Indirect solar gain Figure 8 - Isolated Gain
There are also variants to these styles, with six examples below (many other variants exist);
- Interior wall mass storage: Interior walls, whether warmed directly by the sun part of the time or indirectly from reflections
- Standing walls: Similar to trombe walls, but are shorter and non-bearing, some providing a view out of the windows and easier access to insulating shades.
- External wall mass storage: Thick external masonry or log walls with little to no insulation that moderate swings in outside temperature in warmer climates where the average daily temperature is close to (or in) the 'comfort zone' (i.e., Southern California, Mediterranean, etc). Solar insolation on these external walls is also a factor, indeed a special case. Please note: in cool and cold climates, any thermal mass outside of the wall's insulation layer has little to no thermal storage effect in winter.
- Roof pond mass storage: A pond on the roof with thermal 'visibility' into the house, warmed during the day, covered with insulation at night [5]
- Earth mass storage: Partially (or fully) undeground house that uses the earth as thermal mass store.
- Annualized Geo Storage: An extension of simple earth mass storage (see figure 13). Hot air is collected year around and thermosiphoned down through a thermal mass wall in the winter (or via fan-driven bypass in the summer, making it active) and through the earth beneath a building [6].



Figure 9 - Interior wall mass storage Fig. 10 - Roof pond storage Figure 11 - Standing wall storage

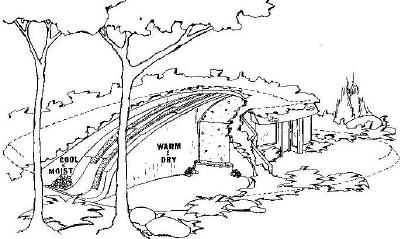
Figure 12 - Annualized Geo Storage Figure 13 - Use of the ground for insulation and thermal mass
Thermal Mass Materials
Beside structural and aesthetic considerations, the main thermal mass properties we are interested in are;
- specific heat (c): the amount of heat required to increase the temperature of a unit weight of material one degree. For example, it take 1 BTU to raise 1 pound of water 1 degree F.
- density (ρ): the mass per unit volume for a material. For example, water weighs 8.33 pounds per gallon (lb/gal) or 1 kg/litre.
- thermal conductivity (k): the rate at which heat travels through a material. For example, for each degree F difference between one side of a 1 foot concrete wall and another, heat travels through every square foot of that wall at 0.833 BTUs per hour (see value in Table 2).
- thermal resistivity (r): the inverse of the conductivity.
- heat capacity (β): specific heat times density (cρ), which determines how much heat energy a material can hold
Because we are EROEI-aware here at TOD, we also want to know how much energy was involved in the production and handling of the materials, called embodied energy. The values shown are approximates, as material hauling energy varies widely. Note that some of these values are often listed in other units (e.g., conductivity as BTU·in/hr F ft2) and careful attention must be paid to calculating units correctly (such as inches, feet, meters, cm, temperature scales, etc).
Table 2 - Thermal Mass Properties and Embodied Energy of Common MaterialsMaterial | Specific Heat (c) BTU/(lb F) |
Density (ρ) lb/ft3 |
Thermal Conductivity (k) BTU/(hr F ft) |
Thermal Resistivity (r) (hr F ft)/BTU |
Heat Capacity (β) BTU/ft3/F |
Embodied Energy BTU/lb |
Water (still) | 1 | 64 | 0.351 | 2.941 | 64 | 0 (add energy to pump) |
Face Brick ASTM C 216 |
0.24 | 130 | 0.76 | 1.32 | 31.2 | ~10752 |
Building Brick ASTM C 62 |
0.22 | 120 | 0.47 | 2.13 | 26.4 | ~10752 |
Concrete (light) |
0.22 | 125 | 0.833 | 1.2 | 27.5 | ~4003 |
Concrete (heavy) |
0.24 | 150 | 1.33 | .75 | 36 | ~4003 |
Granite | 0.20 | 165 | 1 - 2.3 | 0.43 - 1 | 33 | (energy to extract and haul) |
Wallboard (gypsum) | 0.26 | 50 | 0.093 | 10.81 | 13 | 1935 |
Straw bale | 0.32 | 5.2 - 8.3 | ~0.057 | ~17.4 | 1.65 - 2.63 | 56 - 103 |
Fiberglass batts | 0.23 | 0.65 | 0.027 | 37.5 | 0.15 | 12,000 |
Cellulose batts | 0.46 | ~4.4 | ~0.0275 | ~37 | ~1.9 | ~200 |
Air (80F, dry) | 0.24 | 0.0624 | 0.0171 | 58.81 | 0.0149 | 0 |
- Any convection of the fluid within the storage media increases the rate of heat transfer
- The embodied energy of Green Brick is only 168 BTUs/lb, due to use of recycled materials (at factory shipping dock).
- The embodied energy of "Green Concrete" (slag concrete) is 50% lower (at factory shipping dock).
R-Value = rd, and
U-Value = k/d
d = thickness (in the same units as in density and area)
Example: The R-Value of a 4" typical cellulose batt is;
R-Value = 37 x 4/12 = 12.3
Note that the overall R-value of the non-window portion of a wall includes not only the insulation, but the framing (studs) as well. Framing can create a less resistive path for heat loss (or gain); this effect is referred to as thermal bridging. This reference derives realistic R-values for various wall types.
Phase Change MaterialsUp to this point, we have been looking at materials that stored sensible heat, that is, heat one can sense when raising the temperature of a substance by some number of degrees. But when materials change phase from solid to liquid, or liquid to gas (excluding triple point), a large amount of energy is expended just to realize the phase change; this is called latent heat of fusion (or melting). For example, remember that it takes 1 BTU to raise 1 lb of water 1 degree F. However, it takes 144 BTUs to melt 1 lb of ice at 32F to water at 32F.
There are commercially available phase change materials (PCM) that change from solid to liquid in the temperature ranges that are suitable for building applications. Due to the tremendously larger amount of BTUs that can be 'stored' via phase change, significant size reductions can be possible, though most such phase change materials have less latent heat capacity than water. The materials can be contained in tanks, embedded into other sensible thermal mass in a hybrid fashion, or incorporated into building materials, such as PCM impregnated wall board [7][8] and even insulation. The use of such building materials can greatly reduce (or eliminate completely) the need for other thermal mass storage.
Thermal Mass SizeOnce we know the heat capacity and conductivity of a material, the size of the thermal mass is the remaining factor that determines the number of hours or days the thermal mass continues to moderate the building temperature, whether providing warmth or coolth. At this point, the general readership may prefer to examine rules of thumb that some designers in the industry have followed, such as these from the Arizona Solar Center;
* masonry and concrete floors, walls and ceilings to be used for heat storage should be a minimum of 4 inches thick.
* sunlight should be distributed over as much of the storage mass surface as possible by using translucent glazing.
* a number of small windows to admit sunlight in patches gives better control re: overheating.
* use light colored surfaces (non-thermal mass storage walls, ceilings, floors) to reflect sunlight to thermal storage mass elements.
* thermal storage mass elements (floors, walls, ceilings) should b dark in color.
* masonry floors used for thermal mass should not be covered with wall-to-wall carpeting.
* the most favorable storage occurs when each square foot of sunlight is spread (diffused) over a nine square foot area of storage surface.
* the most efficient way to increase heat storage capacity is to increase the storage surface area and the distribution of sunlight rather than the thickness of the storage mass, because masonry absorbs heat slowly, and intense sunlight on a small area will have a negative affect by increasing room temperature while not significantly increasing the rate heat is absorbed by the storage mass, while a system using dispersed, less intense radiation across a larger surface of thermal mass storage will moderate room temperature fluctuations and store most heat at the same time.
and these rules of thumb from GreenBuilder.com;
* A heat load analysis of the house should be conducted.
* Do not exceed 6 inches of thickness in thermal mass materials.
* For every square foot of south glass, use 150 pounds of masonry or 4 gallons of water for thermal mass.
* Fill the cavities of any concrete block used as thermal storage with concrete.
* Use thermal mass at less thickness throughout the living space rather than a concentrated area of thicker mass.
* The surface area of mass exposed to direct sunlight should be 9 times the area of the glazing.
* Sun tempering is the use of direct gain without added thermal mass. For most homes, multiply the house square footage by 0.08 to determine the amount of south facing glass for sun tempering.

Figure 14 - Effect of thermal mass size on interior temperature swings
While the rules of thumb above may be helpful, most designers and architects are driven to achieve a more exacting level of performance of the buildings they are designing. For those who prefer to delve a little further into the engineering side, the next important concept to understand is the thermal time constant (TTC), or the thermal inertia of the building taking into considertion the building's insulating properties. The greater the TTC, the lower the temperature swing, and the greater the time lag it takes to reach the maximum and minimum temperatures (see figure 14). The following sets of formulas might appear dizzying to some; fortunately, there are software applications available that calculate all of this for us by simply entering the specifics of the building materials and dimensions, so don't be put off by the math. For each exterior surface in the building, we can perform a simple estimation of the TTC per unit area (more detail can be added if desired [9][10]);
TTCA = Ros + QAR [11]
where:
QA = c*d*ρ
d = thickness (in the same units as in density and area)
R = d/k
Ros = resistance of outside still air film (neglible in a breeze or with superinsulation)
For a composite surface of multiple layers, starting from the outside layer as "1";
TTCA=QA1(Ros+ 0.5R1)+QA2(Ros+ R1 + 0.5R2)+ QA3(Ros + R1 + R2 +0.5R3) ... [13]
See an example of multi-layer TTC calculations that show how having thermal mass on the inside of insulation gives a much higher TTC than having thermal mass on the outside of insulation [12]. For those considering renovating a building with exterior masonry walls, this is an extremely important factor in determining your design approach.
To determine the TTC of a surface area;TTCs = As * TTCs [14]
where:
As = area of surface
TTCext. surfaces = ΣTTCs/Atotal [14][15]
To take into account any other interior thermal mass (e.g., partition walls, standing water walls, insulated masonry slab, etc), we can approximate the overall effective thermal mass;TTCtotal = TTCext. surfaces + ΣMiβi/kidi&rhoi
where:M = mass of individual interior objects i
The TTC can sometimes be empirically determined in a real world setting for existing buildings by starting off with a known interior temperature, then observing the temperature change over a number of hours (with a different outside temperature). Outside temperatures don't always stay the same, so more advanced calculations may be needed.
TTC = t/(1-[(Tt-Tstart)/ΔT]) [15]where:
t = time in hours
Tt = ending interior temperature
ΔT = difference between inside and outside temperatures
The diurnal heat constant (DHC) is very similar, though even more importantly tells us the building’s capacity to absorb solar energy coming into the interior of the space and release the heat to the interior for a given period P.
DHCsurface = F1s [12]where: (checkmark is symbol for square root in simple html)
F1 = √ (cosh 2x - cos 2x)(cosh 2x + cos 2x)
x = d√πρc/Pk
s = √Pkρc/2π
P = period (24 hours)
The overall DHC of a building is the summation the DHC values of each surface in contact with the interior air;
DHCtotal = ΣDHCsurfaceAsurface [12]
Now we have come full circle since determining the daily heat gain at the beginning of Part 2, and can calculate the total variation in indoor temperature; ΔT (swing) = 0.61Qgain/DHCtotal [12]where:
ΔT (swing) = the difference between the minimum and maximum interior temperatures.
Qgain = the daily building energy gain calculated above.
We can iterate to find the size of the mass we need to stay within the desired maximum temperature swing. To design for a number of cloudy days, change the value of P (for example, to have sufficient thermal mass for 3 heavily cloudy days, P = 3). Spreadsheets make this much easier to "what if".
As we've seen above, the ordering of the insulation and mass layers greatly effects the temperature swing and time lag of the interior temperature. The TTC value is most important when considering heat loss/gain across wall/window surfaces with little to no solar gain and without summer night time "flushing" of cooler air through the house. Use of solar gain or summer night cool air flushing shifts our focus to the DHC value. Different approaches can be evaluated by the placement of insulation and thermal mass [12];
- High insulation, low thermal mass: Results in a low TTC and low DHC, so while the heat loss across highly insulated surfaces is low, there is still higher levels of heat loss through windows. The internal temperature is subject higher daily swings without thermal mass and such a building is a poor candidate for passive solar heating or cooling.
- External insulation, internal thermal mass: A high TTC and high DHC, providing a moderation of the indoor temperature during the winter and summer from winter solar gain and summer night time flushing.
- Internal insulation, external thermal mass: A low TTC and low DHC, providing very little temperature moderation. The internal temperature is subject higher daily swings and such a building is a poor candidate for passive solar heating or cooling.
- Internal and external insulation, encased thermal mass: Common with insulating concrete forms (ICF), provides a medium-high TTC, but a low DHC, so while it is somewhat effective for moderating temperatures generally, this approach does not store heat from passive solar insolation, nor does it cool off on summer nights with cool air flushing.
We have touched on many of the basic points concerning Thermal Mass, though there are still more details to cover to finalize a complete passive solar design in these areas. The good news is; design tools are available to automate the selection and calculation of formulas, as we will see in later articles. Continuing the series, Part 4 will complete the rest of the design aspects (Distribution and Controls), followed by several other articles in the series devoted to renovation, design tools, green building standards, case studies, and more.
References:
1. David Kent Ballast, Architect's Handbook of Formulas, Tables, and Mathematical Calculations, Prentice Hall, 1988
2. Kissock, J, Internal Heat Gains and Design Heating & Cooling Loads, University of Dayton Lecture
3. Michael J. Crosbie, The Passive Solar Design and Construction Handbook, John Wiley and Sons, 1998
4. John Little, Randall Thomas, Design with Energy: The Conservation and Use of Energy in Buildings, Cambridge University Press, 1984
5. Passive Solar Heating and Cooling, Arizona Solar Center
6. Jeff Vail, Annualized Geo-Solar, JeffVail.net
7. K. Darkwa *, J.-S. Kim, Dynamics of energy storage in phase change drywall systems, Wiley, 2005
8 Jo Darkwa, Mathematical Modelling and Simulation of Phase Change Drywalls for Heating Application in a Passive Solar Building, AIAA, 2005
9. Warszawski, Abraham, Industrialized and Automated Building Systems, Taylor & Francis, 1999
10. US Department of Defense, Passive Solar Buildings, Unified Facilities Criteria, UFC 3-440-03N, 2004
11. F. Bruckmeyer, The Equivalent Brick Wall, Gesunheitsingenieur, 63(6), 1942, pg 61-65
12. J. Douglas Balcomb, Passive Solar Buildings, MIT Press, 1988
13. M. Hoffman, M. Feldman, Calculation of the Thermal Responses of Buildings by the Total Time Constant Method, Building and Environment, Vol 16, No. 2, pg 71-85, 1981
14. Givoni, Baruch, Climate Considerations in Building and Urban Design, John Wiley and Sons, 1998 pg. 115-147
15. Høseggen, Rasmus, Dynamic use of the building structure - energy performance and thermal environment, Norwegian University of Science and Technology, 2008
16. Bruce Haglund, Kurt Rathmann, Thermal Mass in Solar and Energy-Conserving Buildings (.pdf), University of Idaho